Choosing the right sheet metal bending technique shapes your project’s cost, quality, and speed. Imagine you need a precise part—should you focus on material, complexity, or production volume first? Material costs for metals like mild steel or aluminum can range from $0.70 to $5.00 per pound. Simple bends cost less than complex shapes, and high-volume runs can cut your per-part cost by over half. XTJ Precision Mfg helps you match your needs to the best process.
Key Takeaways
- Choosing the right bending technique affects your project’s cost, quality, and speed significantly.
- Air bending offers flexibility and low tooling costs, ideal for prototypes and small batches but less precise.
- Bottom bending provides higher accuracy and repeatability, suitable for medium to high production volumes.
- Coining delivers the highest precision with minimal springback, best for high-volume, exact parts but requires costly tooling.
- Consider material type, thickness, and production volume when selecting a bending method to avoid defects and extra costs.
- Proper part design, including bend radius and grain direction, helps prevent cracks and ensures strong, accurate bends.
- Automation and skilled operators reduce errors, speed up production, and improve consistency in bending processes.
- Consult experts like XTJ Precision Mfg for complex projects or tight tolerances to choose the best technique and avoid costly mistakes.
Why Choice MattersCost and Quality
You make a big impact on your project’s cost and quality when you choose a bending technique. Each method uses different tools, machines, and labor. Some techniques need expensive tooling or skilled operators, while others work well with automation. If you pick the right method, you can save money and improve quality.
Aspect | Evidence Summary |
---|---|
Cost Impact | Integrated strategies like Lean and Six Sigma have cut costs by 7% to 17% in real-world cases. Some projects saved from $50,000 up to $50 million. |
Quality Impact | Most projects saw better quality, such as fewer mistakes, shorter wait times, and higher satisfaction. |
Implementation Themes | Success depends on clear plans, good leadership, and skilled teams. |
Barriers | Problems often come from poor training, weak data, or not enough support. |
Conclusion | The right strategy, like the right bending technique, leads to better cost and quality results. |
XTJ Precision Mfg helps you weigh these factors. Their team reviews your needs and recommends the best process for your goals.
Lead Time
Lead time means how long it takes to finish your parts. You want to avoid delays and keep your project on track. The bending technique you choose affects how fast you can move from design to finished product.
- Accurate lead time calculations help you estimate costs for materials, labor, and energy.
- Knowing lead times lets you plan for inspections and avoid defects.
- Good planning prevents bottlenecks and keeps your workflow smooth.
- Reliable lead time predictions help you deliver on time and keep customers happy.
XTJ Precision Mfg uses advanced planning tools. They help you pick a method that fits your schedule and keeps your project moving.
Common Mistakes
Mistakes in bending can waste time and money. You can avoid many problems by choosing the right technique and working with experts.
- Automation reduces human error and speeds up repetitive tasks.
- Regular maintenance and clear communication prevent breakdowns.
- Automated panel benders in the auto industry cut production time and labor costs.
- CNC machines improve accuracy and reduce errors in complex bends.
- Poor design, like holes too close to bends, causes distortion.
- Scratched surfaces come from bad handling or worn tools.
- Programming errors in CNC machines lead to delays and bad parts.
- Inaccurate measurements and poor planning increase scrap and rework.
- Skilled workers and good training lower mistakes and boost efficiency.
XTJ Precision Mfg trains their team and uses the latest technology. They help you avoid these common pitfalls and get the best results.
Sheet Metal Bending Techniques
Air Bending
Process
You use air bending when you want flexibility in your bends. In this method, you place the sheet metal on a V-shaped die and press it with a punch. The punch does not force the metal all the way into the die. Instead, the depth of the punch controls the angle of the bend. This technique works with many materials and thicknesses.
Pros and Cons
-
- Pros:
- You need less force than other methods, which means less wear on your tools.
- You can adjust the bend angle easily by changing the punch depth.
- Tooling costs stay low because you do not need a separate die for each angle.
- This method works well for prototypes and small batches.
- Cons:
- Springback can cause the metal to return slightly toward its original shape, so you must compensate for this.
- You get less precision compared to other methods, especially for tight tolerances.
- The bend angle can vary if the material thickness or properties change.
- Anisotropy in the metal, or differences in strength along different directions, can affect bend quality. Thinner sheets show more of this effect.
- Pros:
Tip: Air bending helps you test how different materials behave. You can spot differences in bendability along the rolling and transverse directions.
Best Uses
- General sheet metal fabrication
- Projects that need flexible angles or quick setup
- Prototyping and low-volume production
Limitations
- Not ideal for parts that need very high precision
- You must watch for springback and adjust your process
- Material thickness and direction can change results
Bending Technique | Key Characteristics | Advantages | Typical Tolerances | Applications |
---|---|---|---|---|
Air Bending | Uses a punch and V-die; bend angle controlled by punch depth and die opening | Low tooling cost; flexible angle adjustments; reduced die wear; low tonnage | N/A | Versatile, general sheet metal fabrication |
Bottom Bending
Process
In bottom bending, you press the sheet metal all the way into the bottom of the V-die. The punch forces the metal to match the die angle exactly. You need more force than air bending, but you get a more accurate bend.
Pros and Cons
- Pros:
- You achieve higher precision and repeatability because the die sets the angle.
- Springback is much less than in air bending, so you get more reliable results.
- This method works well for parts that need tight tolerances.
- Cons:
- You need more force, which can increase machine wear.
- Setup takes longer, and you need a separate die for each angle.
- Tooling costs are higher than air bending.
- Bottom bending achieves precise bends by fully pressing material into the die, reducing springback.
- Key machine parameters like bending force, bending length, and die gap settings affect quality.
- Skilled operators and good procedures help you get the best results.
Best Uses
- High-accuracy parts
- Projects that need consistent, repeatable bends
- Medium to high production volumes
Limitations
- Not as flexible for changing angles
- Higher tooling and setup costs
- Requires careful die selection and setup
Bending Technique | Setup Time | Force Requirements | Precision and Repeatability | Springback Effect | Applications |
---|---|---|---|---|---|
Bottom Bending | Longer, less flexible | Moderate force to fully press material | Higher precision; consistent angles and tighter tolerances | Significantly minimized; angles more accurate and reliable | Ideal for high accuracy and repeatability needs |
Coining
Process
Coining uses very high force to press the sheet metal completely into the die. The punch and die squeeze the metal so hard that it takes the exact shape of the die cavity. This process causes the metal to harden in the bend area.
Pros and Cons
- Pros:
- You get the highest precision and repeatability, with tolerances as tight as ±0.1°.
- Springback is almost zero because the metal is fully deformed.
- The bend area becomes stronger due to work hardening.
- You can create complex shapes and embossed features.
- Cons:
- You need special machines and strong tooling to handle the high force.
- Tooling costs are higher than other methods.
- Not all materials are suitable for coining, especially very thick or hard metals.
Coining gives you unmatched accuracy and eliminates springback. However, you must invest in strong equipment and tooling.
Best Uses
- Precision parts that need exact angles
- Embossed or detailed features
- High-volume production where accuracy matters most
Limitations
- High force requirements limit material and thickness choices
- Tooling and equipment costs are significant
- Not practical for low-volume or prototype work
Bending Technique | Key Characteristics | Advantages | Typical Tolerances | Applications |
---|---|---|---|---|
Coining | High force plastically deforms metal into die cavity | High accuracy (±0.1°); minimal springback; work hardening; complex forms | ±0.1° | Precision parts, embossed features |
V-Bending
Process
You use V-bending when you want to create sharp angles in sheet metal. In this process, you place the metal sheet over a V-shaped die. A punch presses the sheet into the die, forming the desired angle. You can adjust the angle by changing the depth of the punch. V-bending works well for many materials and thicknesses.
Pros and Cons
- Pros:
- You can achieve a wide range of angles with one set of tools.
- Tooling costs stay low because you do not need a special die for each angle.
- The process is simple and quick to set up.
- You can use V-bending for both small and large production runs.
- Cons:
- Springback can affect the final angle, especially with thinner materials.
- You may see some variation in bend angles if material thickness changes.
- Surface scratches can occur if you do not use clean or well-maintained tools.
Recent studies show that V-bending gives you reliable results when you control key factors like punch depth and material type. Experiments and computer models confirm that you can predict and reduce springback by adjusting these parameters. For example, using optimized settings for materials like aluminum or mild steel improves accuracy and reduces errors to less than 1°. Incremental bending methods also help you achieve tighter tolerances and better efficiency.
Best Uses
- Making brackets, enclosures, and panels
- Projects that need different angles without changing tools
- Both prototypes and mass production
Limitations
- Not ideal for parts that require extremely tight tolerances
- Springback requires careful compensation, especially for thin sheets
- Surface finish may suffer if tools are worn or dirty
Tip: Always check your material thickness and punch depth before starting V-bending. This helps you get the angle you want and reduces springback.
Folding
Process
Folding uses a different approach from other bending methods. You place the sheet metal on a flat surface, and a clamping beam holds it in place. A folding beam then lifts or lowers the edge of the sheet to create the bend. You can fold up or down, which makes this method flexible for many shapes.
Pros and Cons
- Pros:
- You can bend large panels and long parts with ease.
- The process does not scratch or mark the surface as much as other methods.
- You can make complex shapes, including hems and closed profiles.
- Folding works well for thin and delicate materials.
- Cons:
- The machines can be expensive and take up more space.
- Folding is slower than press brake methods for high-volume runs.
- You may need skilled operators for complex folds.
Folding gives you smooth bends and protects the surface finish. You can use it for architectural panels, doors, and cabinets where appearance matters.
Best Uses
- Large sheet metal panels
- Parts that need a clean, scratch-free surface
- Architectural and decorative applications
Limitations
- Not suitable for very thick or hard materials
- Slower for high-volume production
- Machine size limits the maximum part length
Note: Use folding when you want to avoid surface scratches and need to bend long or delicate sheets.
Roll Bending
Process
Roll bending shapes sheet metal into curves or cylinders. You feed the sheet between three rollers. The rollers move and bend the metal as it passes through, creating a smooth, continuous curve. You can adjust the rollers to change the radius of the bend.
Pros and Cons
- Pros:
- You can create large, smooth curves and cylinders.
- Roll bending handles long sheets and thick materials well.
- The process works for both simple and complex profiles.
- You can use it for high-strength steels and advanced alloys.
- Cons:
- Springback increases with stronger materials and larger bend radii.
- You need more passes for ultra-high strength steels, which takes more time.
- Achieving tight tolerances on large radii can be difficult.
- The process requires careful setup and maintenance.
Industry data shows that roll bending can achieve a minimum bend radius as small as the thickness of the sheet for some steels. For mild steel, springback ranges from 1° to 3°, but for ultra-high strength steels, it can reach 10° to 30°. You need about 50% more passes for these tougher materials. Using the right tooling, lubrication, and maintenance helps you get better results. Roll bending also lets you make complex shapes, such as automotive roof rails, which improve strength and reduce weight.
Parameter / Aspect | Details / Statistics |
---|---|
Minimum Bend Radius (r/t) | As small as 1T for roll bending; 3T for air bending |
Springback Influence | 1-3° for mild steel; up to 30° for ultra-high strength steels |
Number of Passes | 50% more for ultra-high strength steels |
Application Examples | Automotive A-pillars, roof rails, complex profiles |
Limitations | Tight tolerances on large radii are difficult; higher loads needed for strong steels |
- Minimum bending radius depends on the method, wall thickness, and steel strength.
- Roll bending works best for round shapes and long curves.
- Always check with your bender to confirm achievable radii for your project.
Best Uses
- Cylinders, pipes, and curved panels
- Automotive parts like roof rails and structural tubes
- Large architectural features
Limitations
- Not ideal for tight angles or small, precise bends
- High springback with strong materials
- Needs skilled setup and regular maintenance
Tip: Use roll bending for large, smooth curves and when you need to form high-strength materials into complex shapes.
Wipe Bending
Process
Wipe bending uses a punch and a wiping die to create a bend along the edge of a sheet. You place the sheet on the die. The punch presses down, forcing the sheet against the edge of the die. The die holds the main part of the sheet flat while the punch bends the free edge upward. This method forms a sharp, consistent angle along the length of the sheet.
Tip: Wipe bending works best when you need a straight, uniform bend close to the edge of your part.
Pros and Cons
- Pros:
- You get fast, repeatable bends for high-volume production.
- The process works well for making flanges and hems.
- You can use wipe bending for both thin and medium-thickness metals.
- The setup is simple for standard bends.
- Cons:
- The process can cause surface scratches or marks, especially if you do not use proper die materials or lubrication.
- Springback is common, so you must adjust the punch angle to get the correct final shape.
- You cannot use wipe bending for very thick or hard materials.
- The method limits you to bends near the edge of the sheet.
Aspect | Advantages | Disadvantages |
---|---|---|
Speed | Fast for high-volume runs | Less flexible for custom shapes |
Surface Finish | Good with proper die/lubrication | Risk of scratches without precautions |
Precision | Consistent for simple bends | Springback affects accuracy |
Material Range | Thin to medium sheets | Not for thick/hard metals |
Best Uses
You should choose wipe bending when you need to make:
- Flanges along the edge of panels
- Simple hems for reinforcement
- Enclosures and boxes with straight edges
- Automotive parts like brackets and mounting tabs
Wipe bending is common in industries that need many parts with the same bend, such as appliance manufacturing and automotive assembly.
Limitations
Wipe bending has some important limits:
- You cannot use it for bends far from the edge of the sheet.
- The process does not work well for complex or deep profiles.
- Surface finish may suffer if you do not maintain your tools.
- Springback can make it hard to achieve tight tolerances.
- You need to avoid very thick or high-strength metals.
Note: Always check your material and design before choosing wipe bending. This helps you avoid costly mistakes and ensures you get the results you want.
Comparison Table
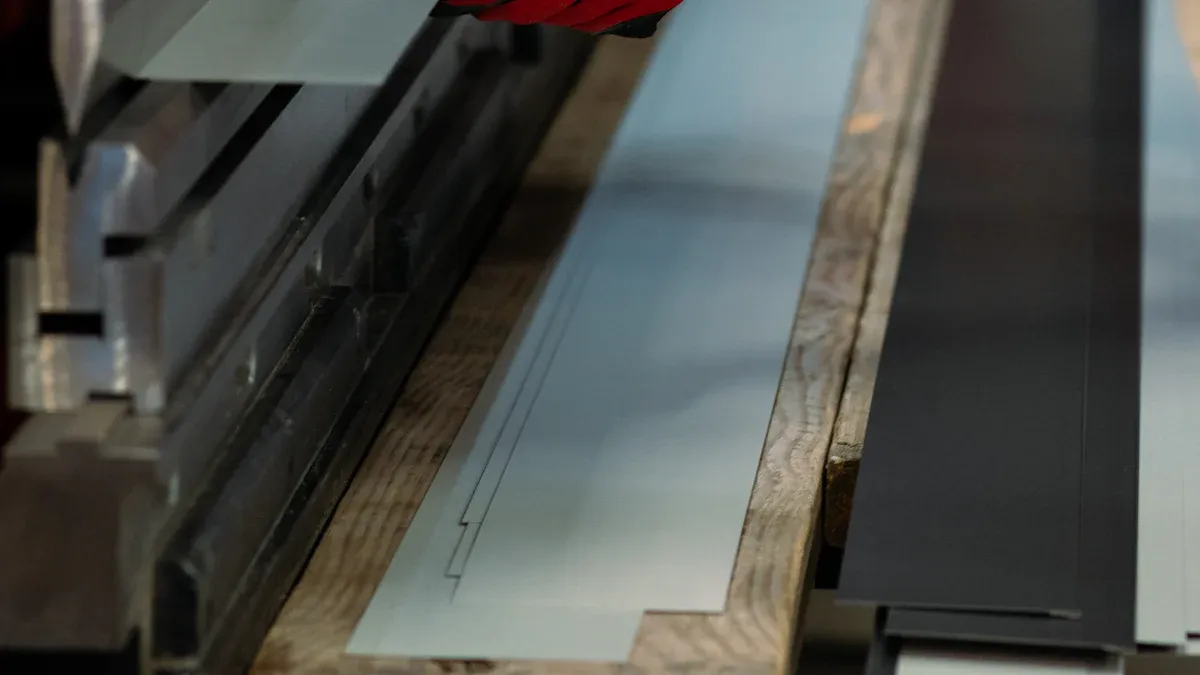
Pros and Cons
You want to choose the right bending technique for your project. Each method has unique strengths and weaknesses. The table below helps you compare the main pros and cons at a glance. This makes it easier for you to decide which process fits your needs.
Technique | Main Pros | Main Cons |
---|---|---|
Air Bending | Flexible angles, low tooling cost, quick setup | Springback, less precision, angle variation |
Bottom Bending | High accuracy, repeatable, less springback | Higher force, longer setup, more tooling needed |
Coining | Highest precision, minimal springback, strong bends | Expensive tooling, high force, not for thick metals |
V-Bending | Versatile, simple setup, works for many materials | Springback, surface scratches, angle variation |
Folding | Great for large panels, protects surface, complex shapes | Slower for high volume, costly machines, size limits |
Roll Bending | Smooth curves, handles long/thick sheets, good for strong metals | Hard to get tight tolerances, high springback, needs skill |
Wipe Bending | Fast for edges, repeatable, good for flanges | Surface marks, springback, only near edges |
Tip: Always match your technique to your part’s shape, size, and finish needs. This helps you avoid costly mistakes.
Quick Reference
You can use the next table as a quick reference when you need to compare key features. This table shows you the advantages, precision, tooling, and best uses for each method. It helps you make fast, informed decisions.
Technique | Key Advantages | Precision Level | Tooling Requirements | Typical Applications | Notes |
---|---|---|---|---|---|
Air Bending | Flexible, low cost | Moderate | Simple punch and die | Prototyping, small to medium runs | Some springback expected |
Bottom Bending | Accurate, repeatable | High | Specific die for each angle | High-accuracy, repeatable parts | Less flexible for angle changes |
Coining | Very precise, strong bends | Very High | Complex, expensive tooling | High-volume, precision parts | Needs high tonnage, not for thick metals |
V-Bending | Versatile, common method | Moderate-High | Standard V-die | Wide range of parts | Good for many materials |
Folding | Large, complex panels | High | Folding beam and clamp | Architectural, decorative, large sheets | Protects surface, short flanges |
Roll Bending | Smooth curves, long parts | Moderate | Three rollers | Cylinders, pipes, automotive parts | Needs skill, more passes for hard metals |
Wipe Bending | Fast, repeatable for edges | Moderate | Wiping die | Flanges, hems, edge bends | Only for bends near sheet edge |
If you need to bend large panels without surface marks, folding works best. For high precision and minimal springback, coining is your top choice. When you want fast, repeatable bends along the edge, wipe bending gives you the best results.
You can use these tables to compare methods quickly. This helps you save time and choose the best process for your project. When you understand the differences, you make better decisions and avoid common problems in sheet metal bending.
Key Factors
Material and Thickness
You need to consider both material type and thickness before choosing a bending technique. Different metals bend in unique ways. Aluminum and copper bend easily, while high-strength steel needs more force. Thicker sheets require stronger machines and special tools. If you use the wrong method, you risk cracks or poor bends.
A table can help you compare how each method handles different materials and thicknesses:
Factor | Air Bending | Bottoming | Coining |
---|---|---|---|
Material Type | Most metals, soft and ductile | Medium to high strength steels | High-strength, springy metals |
Thickness | Best for thin sheets | Medium thickness | Thick materials, high force needed |
Production Volume | Low to medium | Moderate | High |
Tooling Cost | Low | Medium | High |
Precision (Angle) | ±0.5° | ±0.3° | ±0.1° |
Required Tonnage | Low | Moderate | High |
Material composition and thickness also affect cutting and bending quality. For example, aluminum’s high thermal conductivity changes how it bends. Stainless steel can form heat-affected zones. Thicker sheets need more power and special equipment. If you choose the right method, you get better results and avoid costly mistakes.
Research shows that thickness changes bending performance. In one study, thicker fabrics and higher yarn density increased bending damage. Another test found that thicker resin samples had higher bending resistance. These findings prove that thickness matters for strength and quality.
XTJ Precision Mfg reviews your material and thickness before recommending a process. Their team checks if your metal and sheet size match the best bending method.
Precision Needs
Precision matters most when your parts have tight tolerances or complex shapes. Some projects need angles accurate to within a fraction of a degree. If you use a low-precision method, your parts may not fit or function as needed.
Statistical tools like Measurement Systems Analysis and error propagation help you measure and control precision. These tools identify where errors come from and help you improve accuracy. Advanced measurement systems can even detect tiny features smaller than a pixel. This technology is important for small, complex parts.
In large projects, like wind towers, you must keep deviations within a few millimeters. Manual measurements often lead to errors. High-precision machines and careful calibration ensure your parts meet strict standards.
XTJ Precision Mfg uses advanced measurement and calibration tools. They help you choose a bending method that matches your accuracy needs.
Tip: If your design has tight tolerances, always ask for a high-precision bending method.
Volume and Speed
Production volume and speed affect which bending method works best for you. If you need thousands of parts, you want a fast, repeatable process. For small batches or prototypes, flexible methods with low setup costs save you money.
Short run charts track how bending angles change over time. These charts show that some methods have more variation and need more checks. High-volume production benefits from automated machines and stable processes. Low-volume runs can use manual or flexible setups.
- High-volume: Coining and automated bending give you speed and consistency.
- Low-volume: Air bending and folding offer flexibility and lower costs.
- Medium-volume: Bottom bending balances speed and accuracy.
XTJ Precision Mfg asks about your production goals. They help you pick a method that fits your timeline and budget.
If you need fast turnaround, tell your supplier your volume and speed needs up front.
Part Design
You need to think carefully about your part design before you choose a bending technique. The way you design your part affects how well it can be made and how it will perform. If you ignore key design rules, you may face problems like cracks, misalignment, or costly rework.
Accurate setback calculations are essential. Setback is the distance you allow for the bend, and it depends on bend radius, material thickness, and properties like tensile strength and ductility. For example, aluminum needs a larger setback because it springs back more than steel. If you do not account for springback, your parts may not fit together as planned.
You should also consider the minimum bend radius. Most metals need a bend radius at least as large as the material thickness. Bending across the grain of the metal helps reduce the risk of cracking. If you bend along the grain, the part may break or lose strength. Always check the grain direction before you start.
Tolerances play a big role in part design. Tight tolerances make it harder to bend the part correctly. If your design has many bends close together, you must manage tolerance stack-up. This means small errors in each bend can add up and cause the final part to be out of shape. Working with your fabricator early helps you set realistic tolerances and avoid problems.
Tool clearance and bend sequencing also matter. You need enough space for the tools to reach each bend. If bends are too close, the tools may not fit, or the part may get damaged. Planning the order of bends can prevent collisions and make the process smoother.
Material choice affects how your part bends. High-strength steels and aluminum need larger bend radii and careful compensation for springback. If you use the wrong technique, you may see defects or poor quality.
XTJ Precision Mfg reviews your part design and checks all these factors. Their team uses Design for Manufacturing (DFM) principles to help you align your design with the best sheet metal bending method. Early collaboration ensures your parts are accurate, strong, and easy to assemble.
Tip: Always share your part drawings and material specs with your fabricator. This helps them suggest the best bending technique and avoid costly mistakes.
Decision Guide
Checklist
You can make better decisions by following a clear checklist. This helps you match your project needs to the right sheet metal bending technique. Use the table below to guide your process:
Aspect | Guideline / Data | Purpose / Benefit |
---|---|---|
Design for Manufacturability | Keep wall thickness uniform, use self-locating features, minimize fasteners | Simplifies fabrication, reduces waste and costs |
Bend Radii Standardization | Use bend radii proportional to material thickness (e.g., 1x for aluminum) | Prevents cracking, improves tooling efficiency |
Grain Direction | Bend perpendicular to grain when possible | Reduces risk of cracking, improves strength |
K-Factor Values | Use correct K-factor for thickness (e.g., 0.4 for 0.5 mm, 0.5 for 2 mm) | Ensures accurate flat patterns |
Tolerances | Keep bends within +/- 0.010 inches; radius tolerance +/- 1.0 | Ensures parts fit, reduces rework |
Software Tools | Use CAD with bend checks, unfolding, and simulation | Improves accuracy, reduces errors |
Assembly Design | Minimize part count, standardize fasteners, use pilot holes | Reduces assembly time, improves manufacturing ease |
Documentation | Record standard bend radii, K-factors, grain direction | Provides clear instructions, reduces mistakes |
Tip: Always review your checklist before starting production. This step saves time and prevents costly errors.
Example Scenarios
You can learn from real-world scenarios to choose the best technique for your needs. The table below shows how different approaches lead to better outcomes:
Scenario Context | Production Focus | Techniques Used | Outcomes / Benefits |
---|---|---|---|
New Product Launch | Assess feasibility and risks | Scenario analysis | Helps plan resources, adjust budgets, and reduce risk |
Manufacturing Project Management | Optimize resource allocation | Scenario analysis, ROI comparison | Supports decisions on project timing, outsourcing, or hiring based on simulated results |
Strategic Planning | Prioritize under constraints | Scenario simulation | Guides facility expansion or upgrades based on demand and regulations |
- Monte Carlo simulation helps you predict possible outcomes and manage risks.
- Cross impact analysis shows how one change affects other parts of your project.
- Decision trees help you see the results of each choice step by step.
- Scenario storytelling makes it easier for everyone to understand the impact of decisions.
- Scenario matrices let you compare options quickly using two key factors.
Statistical tools like Six Sigma and process control also help you improve quality and reduce waste in sheet metal bending projects.
When to Consult XTJ Precision Mfg
You should reach out to XTJ Precision Mfg when you face complex decisions or need expert support. Here are some reasons to consult their team:
- XTJ Precision Mfg holds ISO 9001 certification and focuses on quality, innovation, and process improvement.
- You can get help at any stage, from prototype to full production, because XTJ offers complete manufacturing solutions.
- Their experts help you select the right materials, tools, and machine settings for your project.
- You benefit from their experience with advanced software, CNC programming, and process optimization.
- XTJ provides guidance on documentation, assembly design, and quality control to ensure your parts meet all requirements.
Note: If you have a new design, tight tolerances, or need to optimize production, XTJ Precision Mfg can help you choose the best sheet metal bending technique for your goals.
Choosing the right bending technique shapes your project’s success. You improve results when you match your method to your material, design, and production needs.
- Guided decision processes use pattern recognition and automated planning. These methods save time, reduce tooling costs, and improve efficiency compared to manual trial-and-error.
- The decision guide and comparison table help you plan with confidence.
XTJ Precision Mfg supports you with expert advice. The right choice saves time, lowers costs, and ensures quality.
FAQ
What is the most cost-effective sheet metal bending technique?
You often find air bending the most cost-effective. It uses less force and simple tooling. You can adjust angles easily. This method works well for prototypes and small batches.
How do I reduce springback in my bends?
You can reduce springback by choosing coining or bottom bending. These methods use higher force and set the angle more precisely. Adjusting punch depth and using the right material also helps.
Which technique should I use for high-precision parts?
You should use coining for high-precision parts. This method gives you tight tolerances and almost no springback. It works best for large production runs where accuracy matters most.
Can I bend thick or high-strength metals?
You can bend thick or high-strength metals with roll bending or bottom bending. These methods handle more force. Always check your machine’s capacity before starting.
What is the best way to avoid surface scratches?
You should use folding or well-maintained tools to avoid surface scratches. Clean dies and proper lubrication also help. Protecting the sheet during handling keeps the finish smooth.
How do I choose the right bending technique for my project?
Start by listing your material, thickness, part design, and volume needs. Use the comparison table above. If you feel unsure, consult an expert like XTJ Precision Mfg for guidance.