Aluminum 7075-T6
Stronger aluminum alloy with superior strength-to-weight ratio after heat treatment, ideal for CNC machined parts requiring high strength.
Chemical Composition Of Aluminum 7075-T6
7075 aluminium alloy (AA7075) is an aluminium alloy with zinc as the primary alloying element. It boasts excellent mechanical properties, showcasing flexibility, high strength, toughness, and fatigue resistance. However, microsegregation makes it more susceptible to embrittlement than many other aluminium alloys.
XTJ also offers significantly better corrosion resistance than the 2000 series alloys. This alloy is one of the most commonly used aluminium alloys for highly stressed structural applications and has been extensively utilized in aircraft structural parts.
Chemical Composition | Proportions | Role of Each Element |
---|---|---|
Aluminum (Al) | 87.1% – 91.4% | The base metal that gives the alloy its lightweight properties. |
Zinc | 5.1% – 6.1% | A primary alloying element that increases strength through precipitation hardening. Also improves corrosion resistance. |
Magnesium | 2.1% – 2.9% | A key alloying element that increases strength through solid solution strengthening. |
Copper | 1.2% – 2.0% | Another major alloying element that increases strength through precipitation hardening. |
Iron | Max 0.5% | An impurity that decreases ductility and fracture toughness. Kept to a minimum. |
Silicon | Max 0.4% | A natural impurity that increases fluidity during casting. Restricted to limit its negative effect on corrosion resistance. |
Manganese | Max 0.3% | Added to control the grain structure during solidification. Improves strength without reducing ductility. |
Chromium | 0.18% – 0.28% | Added for improved stress corrosion cracking resistance. Also contributes to strength. |
Titanium | Max 0.2% | Added to refine the grain size, which increases toughness and ductility. |
Zirconium | 0.08% – 0.15% | Improves grain structure control and recrystallization resistance when added with chromium. |
The T6 heat treatment involves solution heat treating, quenching, and aging to achieve optimal strength.
General Characteristics Of Aluminum 7075-T6
Aluminum 7075-T6 offers high strength, lightweight, corrosion resistance, and machinability, ideal for aerospace components demanding precision and durability.
Expert CNC Machining: We Know Materials Inside Out.
Physical properties
Density | 2.81 g/cm3 |
Corrosion resistance | Moderate |
Melting Point | 475°C (887°F) |
Magnetism | Non-magnetic |
Coefficient of Thermal Expansion | 23.5 x 10-6 m/m-K |
Thermal Conductivity | Approximately 130 W/m-K |
Electrical properties | Approximately 21% IACS |
Mechanical properties
Ultimate Tensile Strength (UTS) | 510–540 MPa (74,000–78,000 psi) |
Yield Strength (0.2% Offset) | At least 430–480 MPa (63,000–69,000 psi) |
Elongation at break | 6%-11% |
Modulus of Elasticity (Elastic Modulus) | 71.7 GPa (10.4 x 106 psi) |
Fatigue Strength | 159 MPa (23 ksi) |
Brinell Hardness | around 150 HB |
Vickers hardness | About 140-150 HV |
Available Surface Finishing
Anodizing | Type II (Sulfuric Acid Anodizing): Provides a thin oxide layer, which can be dyed in various colors. Type III (Hard Anodizing): Produces a thicker, wear-resistant layer. |
Powder Coating | Electrostatically applied and cured under heat to form a hard protective or decorative layer. |
Electroplating | Deposition of metals like chrome or nickel onto the aluminum surface to provide a reflective finish or added corrosion resistance. |
Chromate Conversion Coatings | Provides good corrosion resistance and an excellent primer layer for paint or other coatings. |
Note: The properties of Aluminum 7075-T6 can exhibit minor variations depending on the supplier.
Types Of CNC Machining Aluminum Process
The variety of aluminum machining services at XTJ ,We can produce a wide range of products in different shapes and sizes.
These include CNC Milling, CNC Turning, Swiss Machining, EDM, and Grinding. Utilizing a combination of these processes is often necessary to meet the expectations for quality and accuracy set by CNC -Machining and our customers.
Our team of experienced engineers can tailor the production process depending on the needs of each project, creating efficient solutions with a commitment to exceptional quality in each finishing process.
Common Applications Of Aluminum 7075-T6
Aluminum 7075-T6, known for its strength and durability, is widely used in Aerospace, Automotive, and Defense, from aircraft structures to automotive wheels and armor plates.
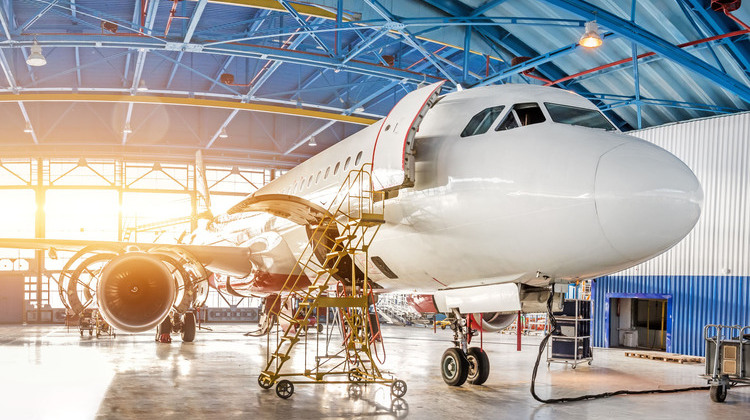
Aerospace
7075-T6 is widely used in aircraft and aerospace for structurally critical CNC machined components like fuselage frames, bulkheads, and engine parts where high strength-to-weight ratios are crucial. Its fatigue resistance and corrosion resistance make it well-suited for the aerospace environment.
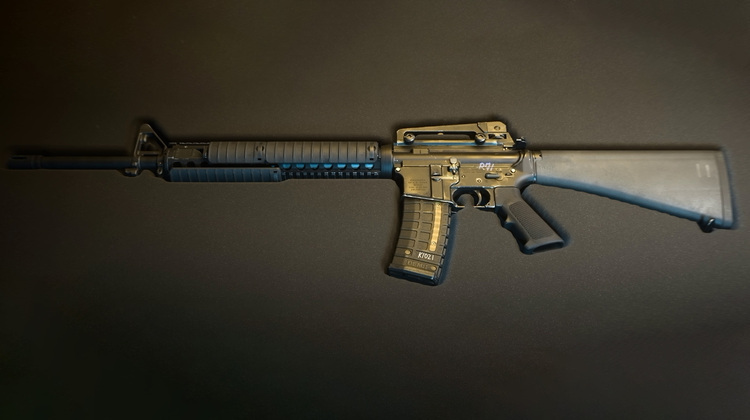
Defense
7075-T6’s hardness provides good ballistic protection for CNC machined military vehicle armor and plates, while its low density helps reduce weight. The alloy is commonly CNC machined into brackets, gears, casings, and other high-strength defense components.
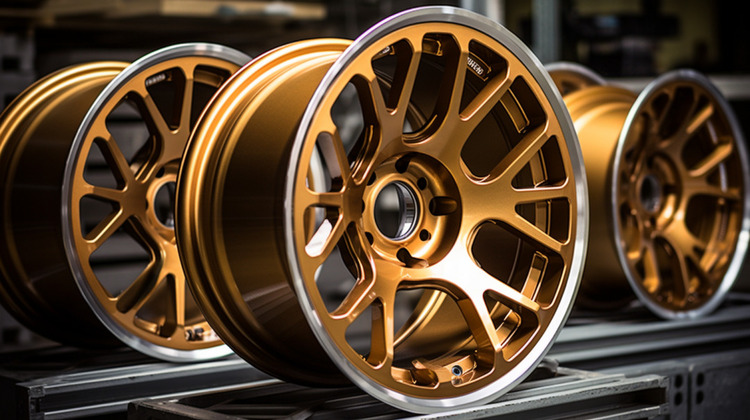
Automotive
7075-T6’s strength, light weight and machinability make it useful for CNC machined automotive parts like wheels, transmission casings, and roll cages. Reducing component weight through high-strength, lightweight 7075-T6 improves vehicle fuel efficiency.
Aluminum 7075-T6
The “T6” in Aluminum 7075-T6 indicates a heat treatment process. This temper involves solution heat-treating and artificial aging, enhancing the alloy’s strength and hardness. In this state, 7075 aluminum achieves peak mechanical properties, including a tensile strength of 510–540 MPa and a yield strength of 430–480 MPa.
7075-T6 is one of the strongest aluminum alloys, especially when compared to the 6000 series, making it suitable for applications that require high strength.
7075-T6 aluminum has superior corrosion resistance but is prone to stress-corrosion cracking. Its resistance can be enhanced through treatments like Anodizing, Chromate Conversion, Powder Coating, Plating, and Passivation.
Aluminum 7075 is available in various tempers, each with distinct properties:
- 7075-O: Annealed, offering high ductility but lower strength.
- 7075-T7 & T73: Solution heat-treated and overaged for improved stress-corrosion resistance.
- 7075-T651 & T7351: Heat-treated, artificially aged, and stress-relieved, balancing strength and corrosion resistance.
- 7075-T7651: Heat-treated, stretched, and overaged for a mix of strength and stress-corrosion resistance.
XTJ is a leading OEM Manufacturer that is dedicated to providing one-stop manufacturing solutions of Machining 6061 Aluminum from prototype to production. We are proud to be an ISO 9001 certified system quality management company and we are determined to create value in every customer relationship. We do that through collaboration, innovation, process improvements, and exceptional workmanship.lication: Automotive industry, Bicycle and motorcycle, Door and windows and furniture, Household appliance, Gas meter, Power tool,LED lighting, Medical instrument parts, ect.