Nylon 66 (PA66), known for its excellent toughness, strength, and wear resistance, is widely used in mechanical manufacturing. However, burrs often pose a challenge during CNC machining of small grooves, frustrating engineers. Burrs not only affect the product’s appearance and assembly precision but can also reduce its service life. This article provides professional and practical deburring solutions, covering process optimization, tool selection, post-processing techniques, and design prevention, ensuring smooth, high-quality surfaces for CNC-machined Nylon 66 grooves.
At XTJ Precision Mfg, we have extensive experience in CNC plastic machining, specializing in high-quality plastic components tailored to specific application needs using techniques like CNC turning and milling to produce custom nylon parts.
1. Burr Formation Analysis: Why Do Small Grooves in CNC Nylon Machining Generate Burrs?
The material properties of Nylon 66 make it prone to burr formation when machining narrow or deep grooves. Key reasons include:
- High Toughness: The material resists complete cutting, leading to stretching, tearing, or curling during machining, resulting in burrs, especially at groove entrances, exits, and corners.
- Thermal Softening and Tool Sticking: Heat from cutting friction softens or even melts the material locally, causing it to adhere to the tool’s cutting edge, forming irregular burrs or built-up edges.
- Tool Extrusion: Dull tools or improper cutting parameters cause the material to be extruded rather than cut, leading to flanging burrs.
- Core Principle: Prevention first, treatment second. Optimizing machining processes and design minimizes burr formation from the outset.
2. Process Optimization: Controlling Burrs at the Source
Effective deburring starts with precise control during machining. Below are key considerations for tools, parameters, cooling, and toolpaths:
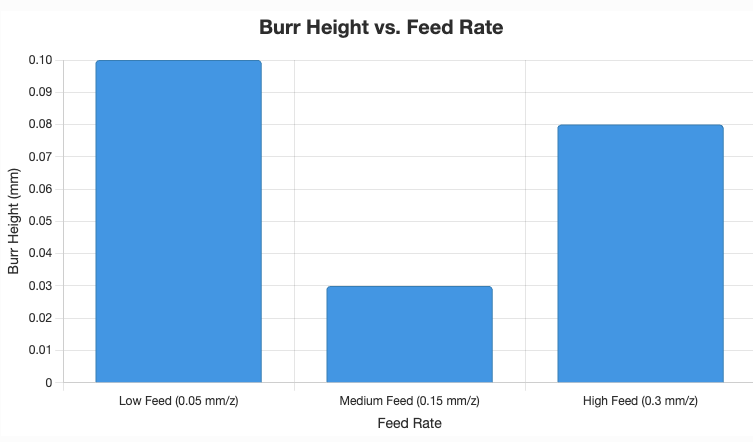
2.1 Tool Selection: Sharpness is Key
- Preferred Choice: Diamond-coated tools, with their ultra-low friction coefficient and high wear resistance, maintain sharp edges for extended periods, reducing material sticking and burr formation. Alternatively, high-performance uncoated carbide tools are viable.
- Tool Geometry: Use a large positive rake angle and sharp cutting edge to avoid edge dulling (negative land), ensuring smooth cutting.
- Size Matching: The milling cutter diameter should match the groove width to avoid excessive radial cutting depth, which causes extrusion. Multi-flute end mills (3-4 flutes) enhance cutting stability.
- Tool Management: Nylon 66 is sensitive to tool wear. Implement strict tool life management and regular replacement to maintain edge sharpness.
2.2 Cutting Parameters: Finding the Optimal Balance
- Avoid Low Feed Rates: Excessively low feed per tooth increases friction heat, softening the material and causing sticking and burrs.
- Avoid High Feed Rates: Overly high feed rates generate excessive cutting forces, tearing the material instead of cutting it, leading to burrs.
- High Spindle Speed: Moderately increase spindle speed to improve chip formation, reduce heat buildup, and minimize material adhesion.
- Finishing Strategy: Use small cutting depths with multiple passes or a dedicated finishing toolpath instead of single-pass machining. Control radial cutting depth (stepover) to reduce burr risk.
2.3 Cooling and Lubrication: Balancing Temperature and Friction
-
- Purpose: Remove cutting heat to prevent material softening, clear chips to avoid secondary scratches, and reduce cutting forces to minimize burrs.
- Recommended Solutions:
- Water-Soluble Coolant: Highly effective for cooling, suitable for most scenarios. Avoid oil-based coolants, which may cause material swelling.
- Cold Air or Mist Cooling: Ideal for applications where liquid residue is undesirable.
- Precise Application: Ensure coolant is directed at the cutting zone for maximum effectiveness.
2.4 Toolpath Strategy: Path Determines Outcome
- Prefer Climb Milling: Cutting forces press the workpiece downward, with chips thinning from thick to thin, improving surface quality and reducing exit burrs.
- Optimize Exit Points: Set tool exit points on non-critical surfaces or scrap areas to hide potential burrs.
3. Post-Processing Techniques: Efficiently Removing Residual Burrs
Even with optimized processes, some burrs may persist. Below are post-processing methods for different scenarios:
3.1 Manual Deburring (Suitable for Small Batches, Simple Structures)
Tools: Plastic-specific deburring knives, fine files, scalpel blades, or sandpaper/cloth (preferably wrapped around a stick).
Key Points: Use light, smooth motions to avoid excessive force, which can tear the material or create new burrs. Protect the workpiece body.
3.2 Cryogenic Deburring (Recommended: Efficient, Ideal for Complex Structures and Large Batches)
- Principle: Liquid nitrogen (-320°F) embrittles Nylon 66, and high-speed blasting with media (e.g., plastic beads) shatters and removes burrs.
- Advantages: Efficiently handles complex cavities and small, deep grooves with uniform deburring and minimal workpiece stress.
- Note: Requires specialized equipment with high initial investment. Precise control of blasting parameters is essential to avoid workpiece damage.
3.3 Thermal Deburring (High-Precision Scenarios, Use with Caution)
Principle: In a sealed chamber, a combustible gas mixture is ignited, creating instantaneous high temperatures to burn off burrs (which combust faster due to their high surface area) while minimally affecting the workpiece body.
Advantages: Thorough deburring, suitable for complex workpieces.
Disadvantages: High equipment costs, and instantaneous high temperatures may cause surface melting, discoloration, or material degradation in Nylon 66. Rigorous process validation is required.
3.4 Other Methods (Use with Caution)
Chemical Polishing: Brief immersion in specific solvents (e.g., formic acid) dissolves burrs but carries high risks of over-etching or material degradation. Not recommended for routine use.
High-Pressure Water/Sandblasting: Requires precise parameter control; otherwise, it may damage groove surfaces or be ineffective for small, deep grooves.
4. Design and Material Optimization: Preventing Burrs Proactively
4.1 Design Optimization: Paving the Way for Deburring
Chamfers/Fillets: Incorporate small chamfers (C-edge) or fillets (R-edge) at groove edges to provide a “ramp” for tool exit, significantly reducing exit burrs and facilitating post-processing. This is the most cost-effective preventive measure.
Avoid Fragile Edges: Ensure groove walls are not too thin or tall to prevent deformation-induced burrs.
Clear Standards: Specify burr control requirements in drawings (e.g., burr height ≤0.002 in, sharp edges dulled).
4.2 Material Optimization: Dryness First
Thorough Drying: Wet Nylon 66 is tougher and more prone to burrs. Ensure the material is fully dried before machining.
Batch Consistency: Monitor material batch stability to avoid performance variations affecting machining outcomes.
5. Practical Recommendations: A Multi-Pronged Approach for Perfect Deburring
Prevention as the Core:
- Invest in diamond-coated tools to ensure edge sharpness.
- Equip a robust cooling system, prioritizing water-soluble coolant.
- Optimize feed rates to avoid extremes, finding the “sweet spot.”
Post-Processing Strategy:
- Small Batches/Simple Structures: Manual deburring with precise operations.
- Large Batches/Complex Grooves: Cryogenic deburring for efficiency and reliability.
- High-Precision Requirements: Thermal deburring, but validate processes rigorously to avoid material damage.
- Chemical Polishing: Too risky, best avoided.
Design Support: Chamfers/fillets at groove edges are a “game-changer” for burr prevention—strongly recommended.
Diagnose First: Analyze burr shape and location to identify root causes (e.g., tool wear, insufficient cooling, or improper feed), then optimize processes accordingly.
Small-Batch Testing: Validate tools and parameters through trial machining, refining the approach iteratively.
6. cnc nylon machining factory suggestion
Burr issues in CNC machining of small Nylon grooves can be addressed through process optimization (sharp tools, reasonable parameters, effective cooling, climb milling), efficient post-processing (cryogenic deburring prioritized), and proactive design (chamfers/fillets). Focus on preventing burrs at the source, combined with appropriate post-processing for the specific scenario, to achieve both machining efficiency and product quality.
XTJ Precision Mfg specializes in machining nylon and other plastics, delivering high dimensional accuracy and surface finish. Our custom CNC machining services meet diverse application needs, providing tailored solutions for industries requiring high-quality plastic components. Contact us today to explore how our expertise can meet your specific requirements.