Custom Sheet Metal Fabrication for Your Unique Needs
From one-off prototypes to high-volume production, we deliver precision parts with fast turnaround and competitive pricing.
Sheet Metal Fabrication and Prototyping Services
XTJ PrecisionMfg delivers high-quality sheet metal fabrication and prototype customization services, providing fast, cost-effective, and reliable solutions for your projects. Our capabilities include precision bending, punching, and cutting of standard-thickness metals, perfect for prototyping and small-batch production. We craft durable, end-use metal parts with a wide range of material options and surface finishes to meet your exact specifications. Serving industries such as automotive, medical devices, aerospace, electronics, energy, and robotics, we ensure tailored solutions that drive your success.
Why Choose XTJ for Sheet Metal Fabrication?
With over 15 years in precision manufacturing, XTJ Precision Mfg Ltd combines cutting-edge CNC machinery and skilled engineering to deliver sheet metal parts that meet the toughest industry standards—ISO 9001 certified and trusted by global leaders in aerospace, automotive, and beyond.
Unmatched Precision
Achieve tolerances as tight as ±0.05 mm with laser cutting and CNC bending—ideal for aerospace and medical applications.
Lightning-Fast Lead Times
Prototypes in 2-5 days, production in 1-3 weeks, beating industry averages by 20%.
Material Expertise
Work with 20+ metals, including aerospace-grade titanium and corrosion-resistant 316 stainless steel.
Full-Service Workflow
From DFM (Design for Manufacturability) analysis to post-processing like passivation, we reduce costs by up to 15%.
Scalability Without Compromise
Handle 1-off prototypes or 10,000-unit runs with consistent quality, backed by automated quality control.
Cost Efficiency
Leverage China’s manufacturing ecosystem for 30-40% savings compared to Western suppliers, without sacrificing quality.
Get your custom sheet metal parts today
The Core Process of Our Customized Sheet Metal Parts
Sheet metal fabrication is the manufacturing process of transforming metal sheets (typically ranging from 0.5mm to 6mm in thickness, such as steel, aluminum, stainless steel, etc.) into desired shapes and structures through a series of processes. Since thin metal sheets are more prone to deformation than thicker workpieces, various techniques can be employed for processing. Generally, the complete sheet metal fabrication process can be divided into three main categories.
Material Removal
We skillfully cut sheet metal into desired shapes using advanced techniques like laser cutting and punching, delivering clean edges and exact specifications for your projects.
Material Deformation
Through bending, forming, and rolling, we transform metal sheets into complex geometries with high accuracy, meeting your custom design needs effortlessly.
Material Assembly
Our assembly process joins components seamlessly with welding, riveting, or fastening, creating durable, ready-to-use products tailored to your requirements.
Removal Methods for Sheet Metal
Laser cutting offers a highly accurate and streamlined approach to sheet metal fabrication, utilizing a focused laser beam to create precise cuts with exceptional detail. Featuring a beam diameter as small as 0.001″ (0.025 mm), it achieves tight tolerances and clean edges, making it perfect for intricate designs. With adjustable focal lengths, it handles a variety of materials effectively, though it’s less ideal for extremely thick metals. Its standout benefits include superior precision, reduced post-processing, and wide material versatility.
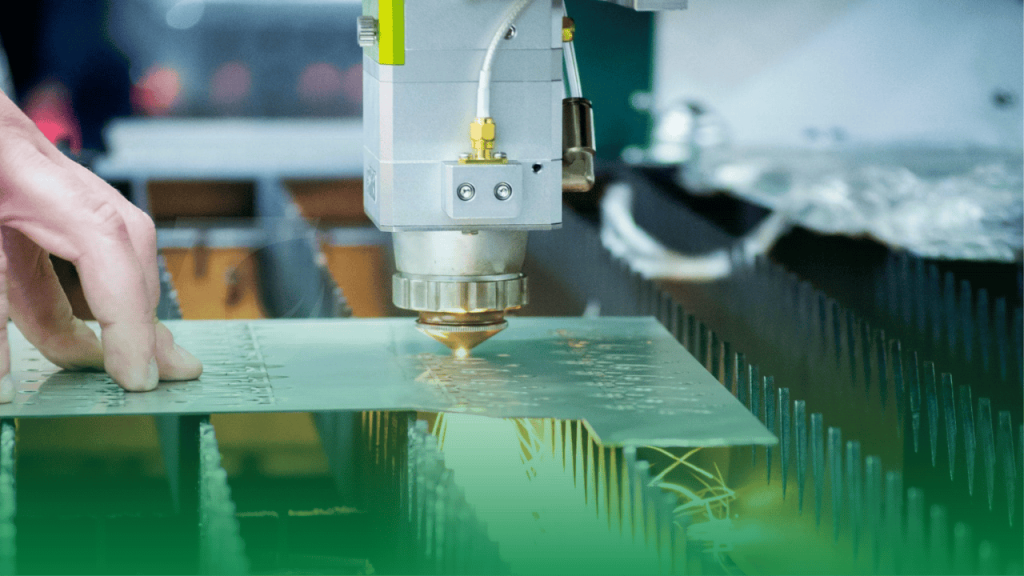
Plasma cutting is a powerful technique tailored for cutting thicker sheet metals, employing a heated plasma arc to slice through materials efficiently. This method delivers rapid results and can manage metals of significant thickness, with tolerances around ±0.01″ (0.25 mm). While it produces a slightly wider cut line, it’s highly effective for industrial applications and diverse metal types, though some edge finishing may be needed. Key advantages include speed, cost-efficiency, and robustness for heavy-duty tasks.
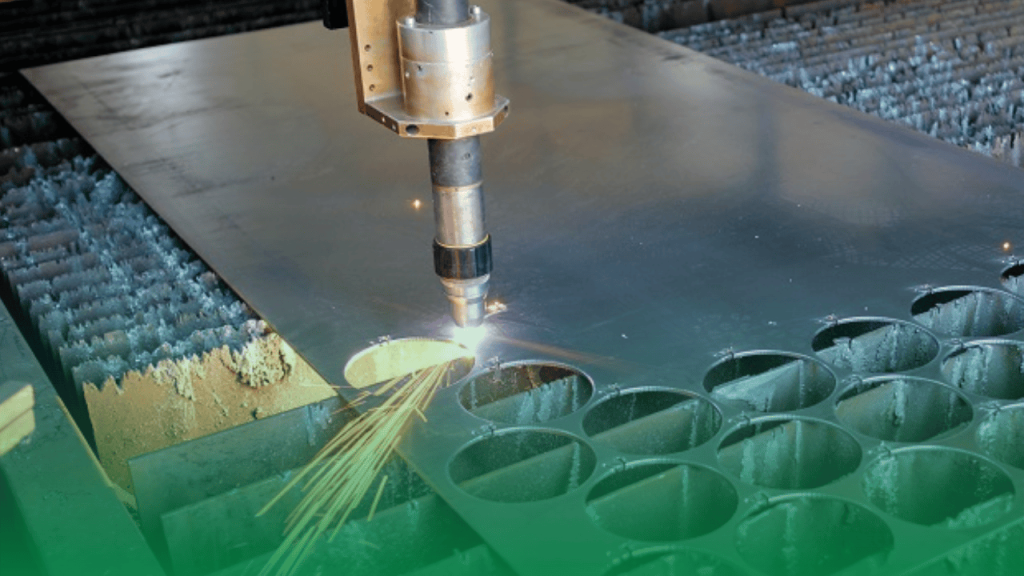
Waterjet cutting provides a flexible and precise solution, using a high-pressure water jet—often with abrasives—to shape sheet metal without heat impact. Achieving accuracy up to ±0.005″ (0.13 mm), it’s ideal for heat-sensitive materials like titanium or aluminum, supporting both thin and thick sheets with complex contours. This process ensures material integrity and minimal waste, making it a sustainable choice. Its primary strengths are adaptability, no thermal damage, and eco-friendly operation.
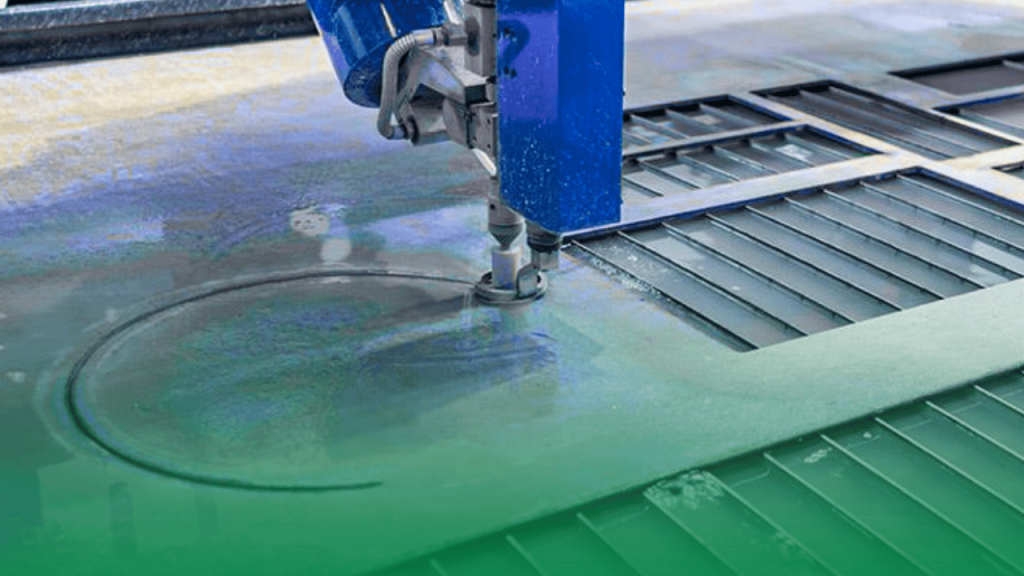
Shearing is a practical and efficient method that employs a mechanical shear to create straight cuts on sheet metal, optimized for basic shapes and high-volume production. With tolerances around ±0.01″ (0.25 mm), it works best with thinner metals and requires little setup time, offering a cost-effective solution. While it’s not suited for detailed patterns, its speed and simplicity stand out. Benefits include high throughput and reliable performance with standard metal types like steel and aluminum.
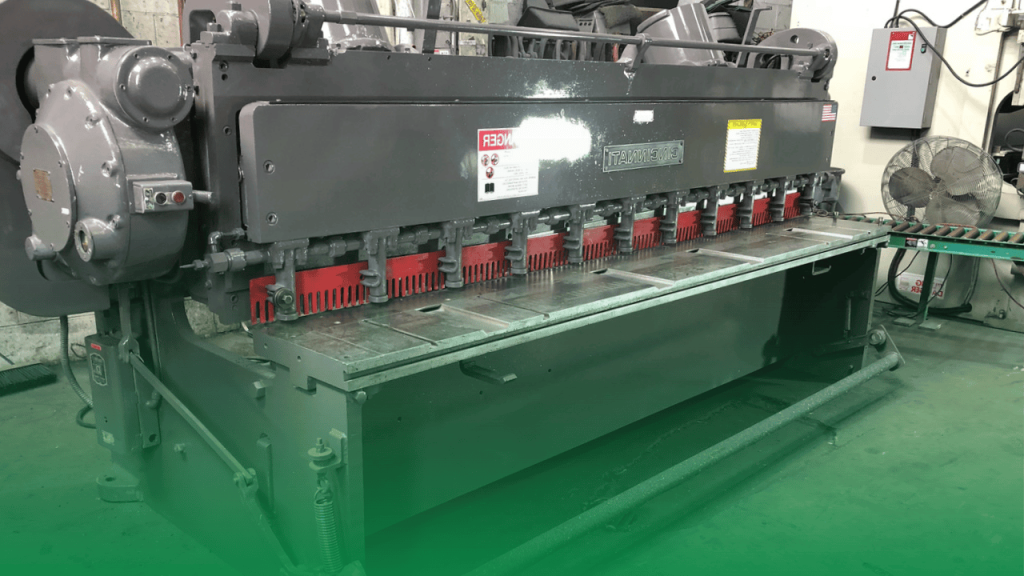
Deformation Methods for Sheet Metal
Bending is a key deformation process that uses a bending machine, such as a CNC press brake, to shape sheet metal into precise angles based on design requirements. This method ensures consistency and accuracy, making it ideal for creating components like brackets or enclosures. With adjustable settings, it accommodates various thicknesses and materials, delivering clean bends with minimal distortion. Its primary advantages include high repeatability, versatility, and suitability for both small batches and large-scale production.
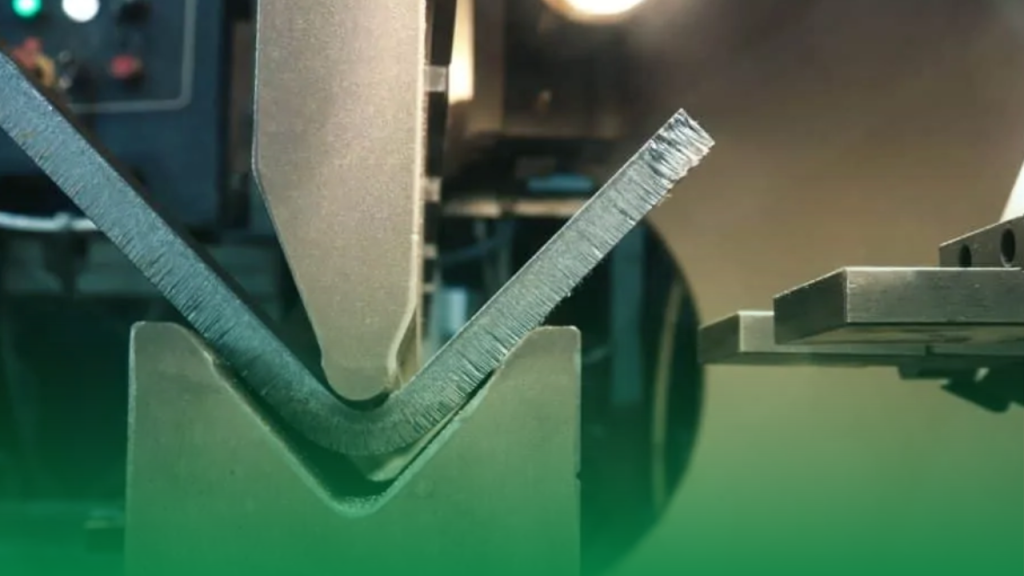
Stamping involves using dies to deform sheet metal by punching holes or forming intricate shapes with exceptional precision. This process is highly efficient for mass production, enabling the creation of detailed parts like panels or connectors. It works well with a range of metals and thicknesses, though it requires careful die design for optimal results. Key benefits include rapid production speeds, cost-effectiveness for high volumes, and the ability to achieve complex geometries.
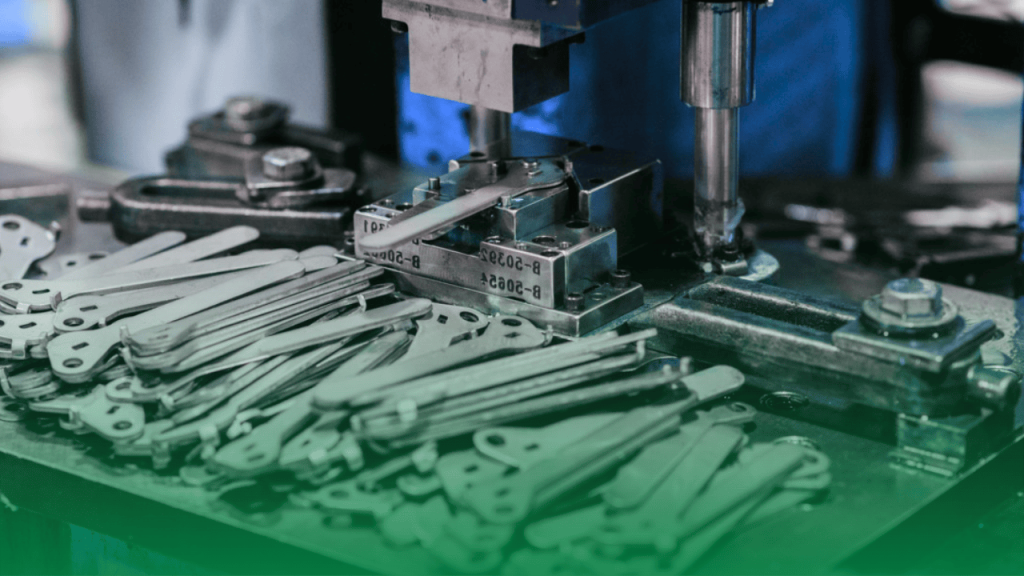
Stretching and deep drawing transform sheet metal into three-dimensional shapes, such as cans or housings, by stretching it over a die or drawing it into a cavity. This technique is perfect for producing seamless, deep-formed components with smooth surfaces. It excels with ductile materials like aluminum or steel, though it demands precise control to avoid thinning. Its standout features include the ability to create strong, uniform shapes and support for customized, intricate designs.
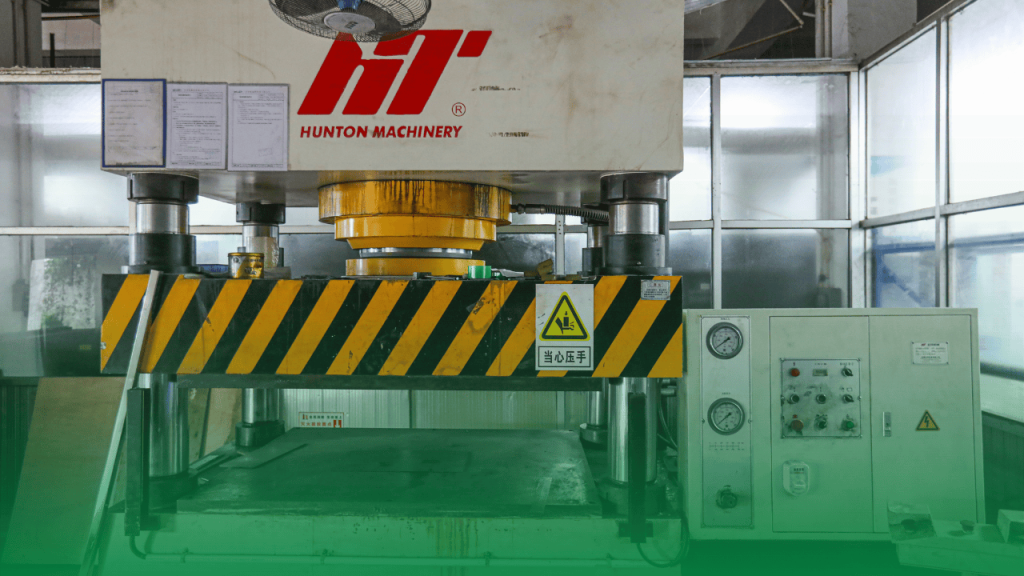
Assembly Methods for Sheet Metal
Assembly marks the concluding phase of sheet metal fabrication, where various parts are united to create a finished product. Components can be linked together using fasteners, welds, rivets, or other conventional joining techniques.
Welding is a robust joining technique that fuses metal parts together using methods such as MIG, TIG, or spot welding, forming a permanent and strong bond. This process is widely used in industries requiring high structural integrity, such as automotive or aerospace, and can handle a variety of metal thicknesses. With proper execution, it ensures durability and resistance to stress, though it may require skilled operators and post-weld finishing. Its key advantages include exceptional strength, airtight seals, and suitability for heavy-duty applications.
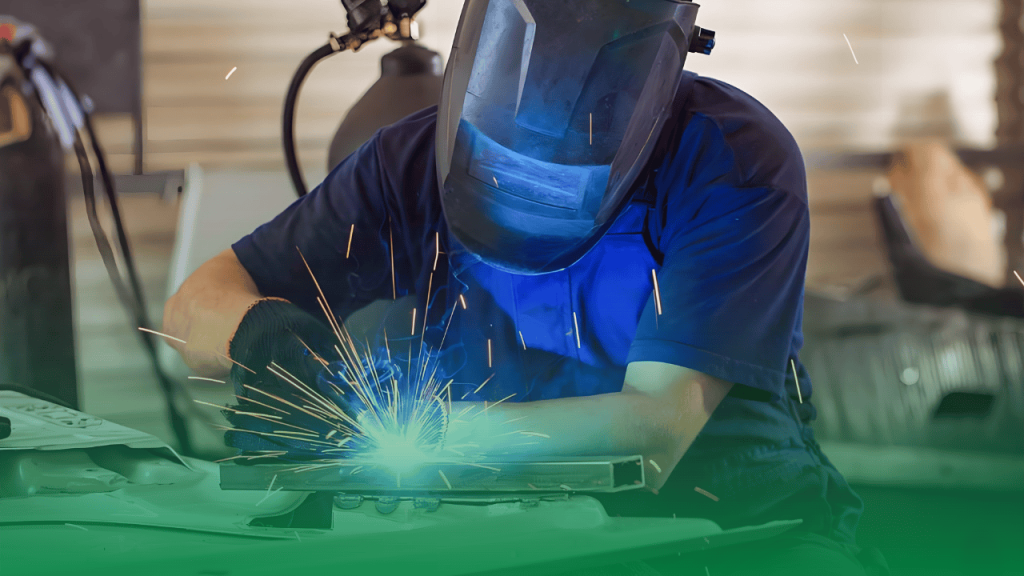
Riveting involves securing sheet metal components with rivets, providing a dependable and often temporary or lightweight connection. This method is popular in construction and aircraft manufacturing, where easy disassembly or weight reduction is needed. It offers good load distribution and doesn’t require heat, making it safer and more accessible for certain materials. Benefits include reliability, simplicity, and the ability to join dissimilar metals effectively.
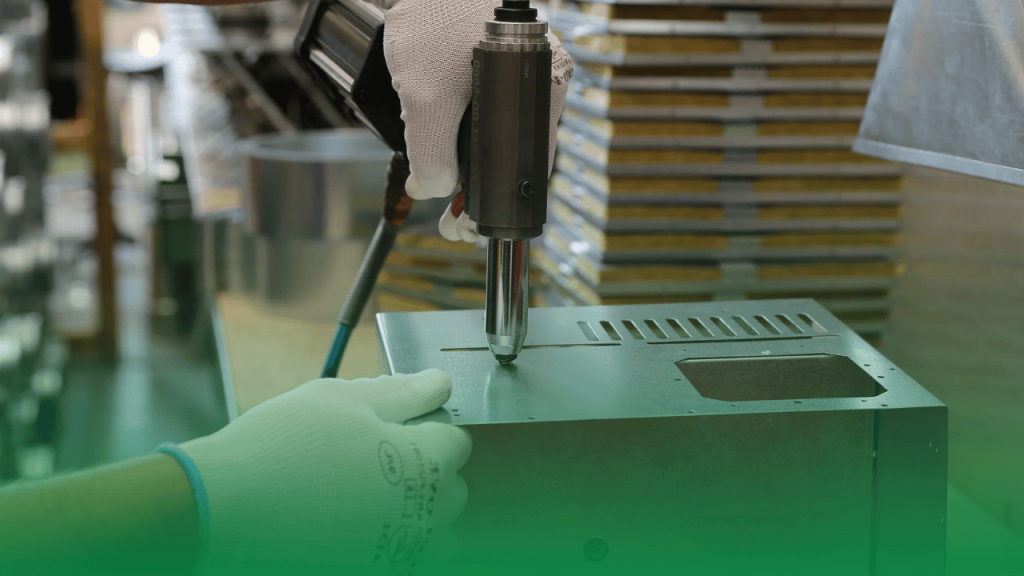
Bolting and nutting create a detachable joint by fastening sheet metal parts with bolts and nuts, making it an excellent choice for structures that require maintenance or modifications. This method allows for easy assembly and disassembly, ideal for machinery or modular designs, and supports a range of material thicknesses. While it may need periodic tightening, its flexibility and reusability stand out, offering a practical solution for adjustable or repairable assemblies.
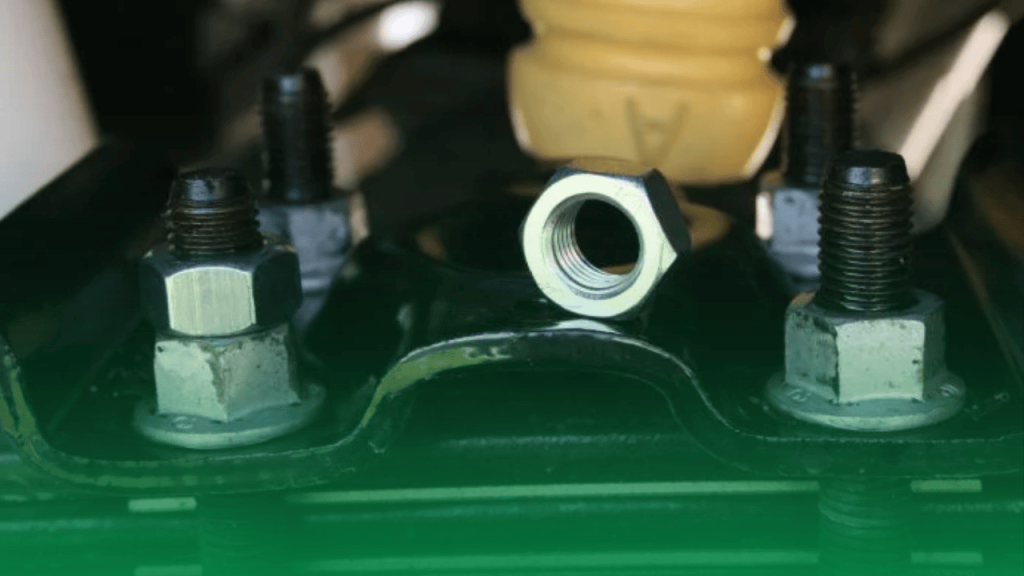
Adhesive bonding uses industrial adhesives to join sheet metal parts, catering to applications where aesthetics or compatibility with special materials is a priority. This technique is perfect for lightweight structures or parts where welding might damage heat-sensitive materials, providing a smooth, seamless finish. It requires careful surface preparation for maximum strength, but its versatility and ability to enhance visual appeal make it a valuable option for modern designs.
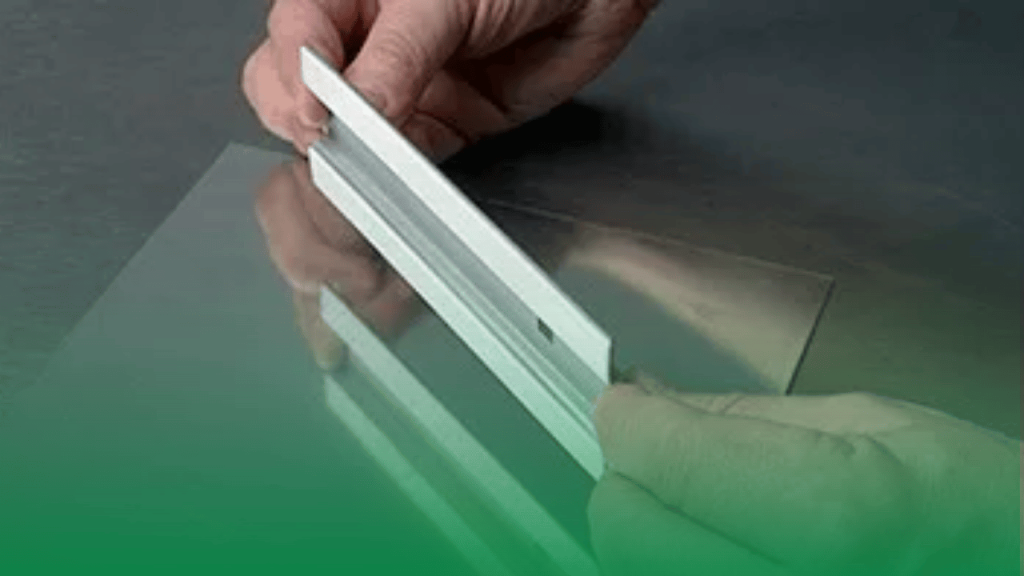
Selecting the optimal fabrication technique is essential for perfect part quality.
Unsure which method fits your project?
Tailored Solutions Across Industries
We align our processes with industry-specific requirements, delivering sheet metal solutions that meet MIL-SPEC, AS9100, and FDA standards where applicable.
Aerospace
Lightweight 6061 aluminum panels with ±0.02 mm tolerances for UAV frames.
Automotive
Stamped stainless steel brackets tested to 500,000-cycle fatigue standards.
Electronics
EMI-shielded copper chassis with 0.1 mm precision for telecom devices.
Industrial Machinery
Heavy-duty 10 mm steel weldments for robotic arms, load-tested to 5 tons.
Your Project, Streamlined: From Design to Delivery
Our proven 3-step process minimizes lead times and maximizes quality, supported by real-time tracking and dedicated project managers.
Materials Engineered for Performance
We stock over 20 metal grades, each selected for specific mechanical properties, sourced from certified suppliers like Baosteel and TISCO.
![]() | Aluminum (6061/5052) | Yield strength 276 MPa, lightweight (2.7 g/cm³), anodizable. |
![]() | Stainless Steel (304/316) | Tensile strength 515-690 MPa, corrosion-resistant (PREN 24+). |
![]() | Titanium (Grade 5) | 950 MPa strength, 4.43 g/cm³ density, aerospace-approved. |
![]() | Copper/Brass | Conductivity 100% IACS, decorative finishes available. |
The Backbone of Modern Manufacturing
Sheet metal fabrication drives innovation across industries, offering unmatched flexibility for complex geometries and robust assemblies. Our automated CNC processes reduce waste by 25% and improve repeatability to 99.8%, per industry benchmarks.
- Tolerances: ±0.03 mm with laser cutting, surpassing manual methods by 50%.
- Speed: 40% faster prototyping than traditional fabrication (2-5 days vs. 7-10 days).
- Applications: Over 70% of industrial enclosures rely on sheet metal
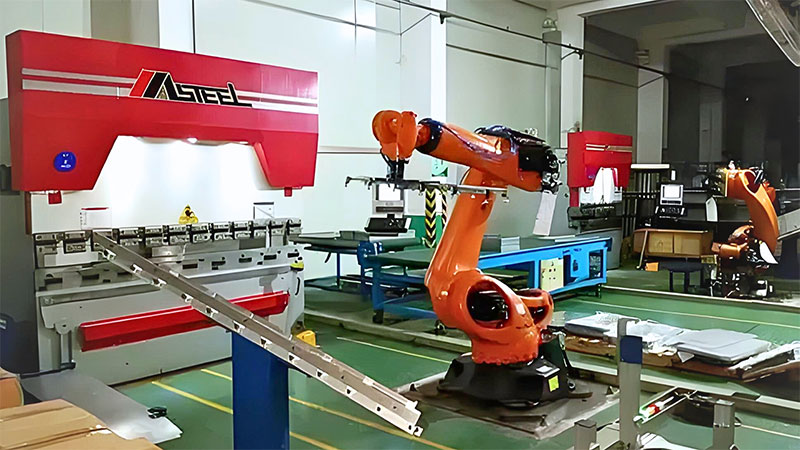
Proven Results for Real-World Challenges
Our clients trust us to solve their toughest fabrication needs—here’s how we’ve delivered.
Delivered 1,000 titanium brackets in 14 days, meeting AS9100 specs, saving 18% on costs.
- Aerospace Client
Produced 500 sterile-grade enclosures with zero defects, validated by FDA audit.
- Medical Device OEM
Precision Parts, On Time, Every Time
Ready to turn your designs into reality? Partner with XTJ Precision Mfg Ltd for world-class sheet metal fabrication.