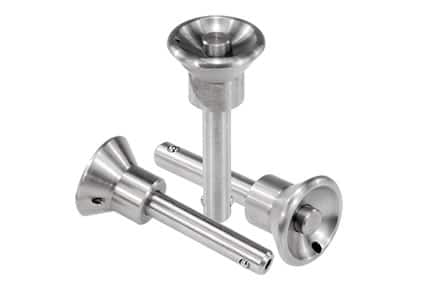
While the process offers significant benefits, unlike 3D printing and CNC machining, it demands a high level of commitment. There are a number of factors to consider before committing to an injection molding process, cost is definitely one of them. So, how much can you expect the process to cost? The plastic injection molding process can cost anywhere from $10,000 or less to $100,000. The total cost of injection molding quote is essentially made up of two parts: mould cost + part cost.
Table of Contents
How much does an injection mold cost?
The injection mold cost is also known as the tooling cost. Tooling refers to the design and manufacturing of the mold used to create injection-molded parts and is often the most expensive component of an injection molding project. Simple molds are typically in the $3,000 and $6,000 range while the price for larger, more complex, higher-production / steel moulds, or multi-cavity moulds can cost from $7,000 and up.
Plastic injection moulding requires a lot of expertise
Factors that determine injection molding tooling costs:
Mold design: The cost of mold design depends on the complexity of the part being produced, the number of cavities in the mold, and the level of precision required.
Materials: The most common materials used to make molds are steel and aluminum, with steel being more expensive but longer lasting.
Machining: High-precision machining is required for mold creation. The longer the machining time, the higher the costs. Larger and more complex molds will involve higher machining times.
Textures: Achieving specific textures or finishes by applying an SPI or VDI finish on the molded part may necessitate additional steps in the mold-making process.
Tooling maintenance costs: Molds require regular maintenance to ensure they are able to produce high-quality parts. The cost of mold maintenance will depend on the frequency of maintenance and the level of necessary repairs.
How much is the cost per part?
Once the initial costs of the molds are covered, the cost per unit during manufacturing is relatively low. You can expect the cost per part to typically range from $0.5 to $10 per piece or higher.
Factors that determine injection molding part unit costs:
Material: Plastic pellet resins used in injection molding can range from $1 per kg to $10 per kg or higher, depending on the type of material. Specialty materials, such as glass-filled polymers or elastomers used to achieve specific properties, will typically incur higher costs. Additionally, larger parts will require more material, hence costing more.
Operator costs: Injection molding requires skilled machine operators, and their expertise significantly influences the efficiency and quality of the production process.
Secondary Operations: Additional processes such as assembly, post-molding treatments, or finishing can increase unit costs.
Cycle time: More intricate designs, parts with complex features or larger parts may slow down the time it takes to remove the part from the mold, increasing overall cycle time and costs.
Production volume: Higher production numbers will lower the final per-piece cost of each part, as economies of scale and efficient utilisation of resources come into play.
Other costs: having quality control procedures in place will impact the overall cost. Energy consumption and the costs of the equipment will also contribute to the unit cost.
How do I reduce injection molding cost?
There are several things you can do to help control and lower costs when it comes to injection molding. Some of the more common items are:
Design Optimization: Simplify Part Geometry: Reduce the complexity of your part design where possible. Simpler designs often result in shorter cycle times and less expensive tooling.
Choose Cost-Effective Materials: Select materials that meet the required specifications but are cost-effective for your application. Consider standard resins over specialty materials unless specific properties are essential.
Minimize Finishing Requiements: Minimize Finishing Requirements: Design parts with finishes in mind to minimize additional post-processing steps, such as painting or polishing.
Work with Experienced Suppliers: Collaborate with experienced injection molding suppliers who can provide guidance on cost-saving measures, mould tool optimization and cycle time optimization.
How much will my injection molding project cost?
Estimate the cost of your injection molding project with us. XTJ has over 20 years of experience in medical device injection molding, automotive injection molding, consumer products injection molding, and many other industries.
Simply submit your 3D drawings and project details on our site submission form, or contact us at [email protected] to get a free injection moulding quote or to speak with an expert from our team.
XTJ is a leading OEM Manufacturer that is dedicated to providing one-stop manufacturing solutions of Aluminum 7075 Parts from prototype to production. We are proud to be an ISO 9001 certified system quality management company and we are determined to create value in every customer relationship. We do that through collaboration, innovation, process improvements, and exceptional workmanship.