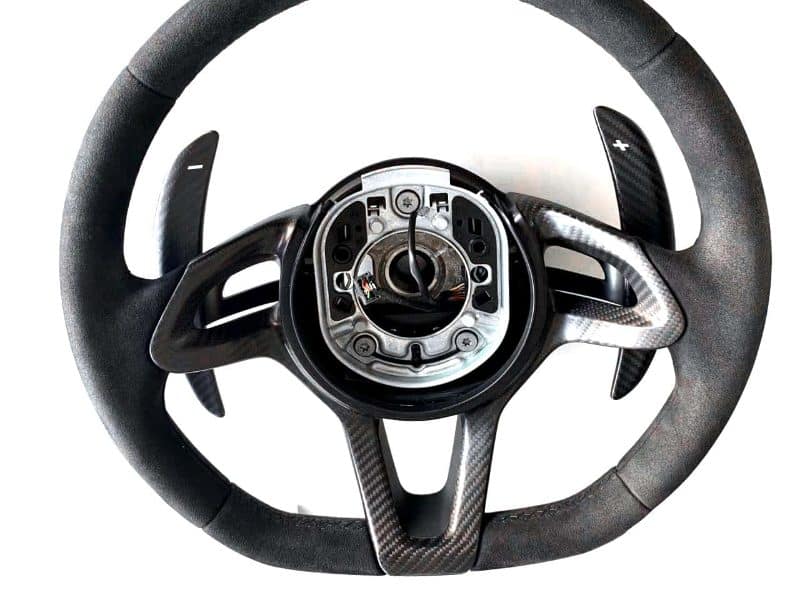
Table of Contents
What is Rapid Prototype Type,Applications and Solution?
Rapid prototypes are early-stage models that serve as the foundation of product development. These prototypes provide invaluable insights to manufacturers on the design and manufacturability of the products. They are cost-effective options to help minimize risks and accelerate product to market.
This article will take you through the various types of prototypes and how you can benefit from them. You will also learn the best practices for prototyping to help you stay ahead in the ever-evolving landscape of modern manufacturing.
What Are Rapid Prototypes?
Rapid prototypes are early, usually simplified versions of a product or system created to test and evaluate its design, functionality, and feasibility. They are early-stage physical or digital models that offer a sneak peek into form, function, and design of products.
They are crafted swiftly, utilizing advanced technologies like 3D printing, CNC machining, or computer-aided design (CAD). This accelerated pace allows designers and engineers to test ideas, identify flaws, and iterate on their designs at a faster speed.
Prototypes can be in various forms, depending on the nature of the project. They are typically developed quickly to expedite the design and development process. Rapid prototypes are not just about getting a first glimpse. The key is to provide a tangible representation that aids in visualization, feedback collection, and refining the product before full-scale production kicks in.
Benefits of Using Prototypes
Needle and carpool syringe for local anesthesia
There are several advantages of using prototypes, and they include:
Catch Design Flaws Early
Early detection of design flaws is critical in the development of medical devices. Prototypes allow designers and engineers to physically interact with the product and identify potential issues that might not be apparent through digital models or simulations.
By identifying and addressing these flaws early in the process, you can save both time and resources that would have been spent on making corrections in later stages of development or even after production has started.
Ensure Functionality
Prototypes enable thorough testing of the product’s functionality under real-world conditions. This includes assessing its performance, accuracy, reliability, and potential technical limitations. In medical devices, this means ensuring that the product operates safely and effectively in a clinical setting, meeting the specific requirements and standards for healthcare applications.
Reduce Costs
While creating prototypes does involve an initial investment, it ultimately leads to cost savings in the long run. By identifying and rectifying design flaws early, you can avoid expensive rework or recalls after mass production has commenced.
Additionally, prototypes can be used to conduct user testing and gather feedback, which helps refine the design before committing to large-scale production. This means you’re less likely to invest in producing many devices that may need expensive modifications or corrections later.
Other benefits are:
Risk Mitigation
Prototypes allow you to identify and mitigate potential risks early in development. This can include regulatory compliance issues, safety concerns, or unexpected technical challenges.
Market Validation
Prototypes can be used for market testing and validation. By presenting a physical representation of the product to potential customers or investors, you can gauge interest and gather valuable feedback before committing to full-scale production.
Streamlined Communication
Prototypes provide a common visual reference point for discussions among team members, stakeholders, and investors. This ensures that all involved in the project clearly and consistently understand the product’s design and functionality.
Improved Time-to-Market
Rapid prototypes, in particular, accelerate the design and development process. This can lead to a shorter time-to-market for the final product, which can be a significant competitive advantage.
Types of Prototypes
3D printer prints orange plastic model
While we’ve used the term ‘prototype’ frequently thus far, it’s worth noting that there are various types of prototypes, each of which can be used for different purposes or at different stages of development. In fact, you may end up using a variety of prototypes to successfully launch your product.
These are the different types of prototypes to achieve this goal:
Proof of Concept
A proof of concept model is often the first prototype to come out of the development process. These prototypes are used to confirm the viability of a project. They frequently have a crude appearance and design. A proof of concept’s primary objective is to test the idea underlying general assumptions and confirm that it can be implemented technically. This can be viewed as an examination of your design.
Visual Prototype
This is a prototype that shows what the finished product will look like. The final product’s size, shape, color, and texture are better illustrated by the visual/appearance prototype. Such a visual-touch component adopts the appearance and texture of the actual product. A visual prototype is similar to a realistic 3D rendering if a concept prototype is like an imprecise 3D sketch. The latter, which combines style and utility, frequently helps with product demonstration. It also displays the viability of the product before entering the market.
Working Prototype
A working prototype is a model or early example of a product that is created to test an idea or procedure so that it can be improved upon or shown to marketing firms and investors. It makes it possible to test the product’s usability and functionality, and it can assist in locating and resolving any potential design flaws. However, a functional prototype isn’t always a reliable indicator of a product’s viability in the marketplace.
Pre-production Prototype
Usually, this is the last test run before starting full-scale production. Pre-production prototypes and production samples can both assist you in identifying manufacturing problems and reducing potential risks. You can easily compare prices using this final prototype. The retailers and distributors who you are offering your new gadget want to see the real thing. Having a factory sample on hand eases your mind and facilitates your launch planning.
When to Use Prototypes
Different types of prototypes are suited for different stages of a project. Here’s a breakdown of when to use prototypes at different stages:
Conceptual Stage
Low-Fidelity Prototypes: Low-fidelity prototypes are helpful when the basic idea is being explored at the conceptual stage. These can be simple sketches, wireframes, or paper mockups that help visualize the overall concept and basic functionalities.
Design Stage
Medium-Fidelity Prototypes: As the design takes shape, medium-fidelity prototypes become valuable. These are more detailed and interactive than low-fidelity prototypes. They can be digital mockups or interactive simulations that give a clearer picture of how the product will function.
Development Stage
High-Fidelity Prototypes: In the development stage, high-fidelity prototypes are employed. These are very close representations of the final product, often built using actual materials and components. They can be used for rigorous testing to verify that all design aspects function correctly.
Testing and Validation Stage
Functional Prototypes: These prototypes closely mimic the final product’s form and function. They are used for thorough testing, validation, and user feedback.
Production and Manufacturing Stage
Pre-Production Prototypes: These are the final prototypes created just before mass production. They are used to verify that the CNC machining process can produce products that meet the desired specifications and quality standards.
Post-Production Stage
Pilot Production Prototypes: After the product has entered mass production, pilot production prototypes may be used to fine-tune the manufacturing process and address any unforeseen issues that arise during large-scale production.
It’s important to note that the choice of prototype type and stage of use may vary based on the specific industry and product being developed. Regulatory requirements and standards may also dictate when and how prototypes are used for precision manufacturing.
Production Pitfalls Prototypes Can Help Avoid
Robots model and 3D printer
You can face multiple pitfalls in production when you employ the rapid prototyping services. Some of them are:
Design Flaws
Early Detection: Prototypes provide a tangible representation of the product, allowing designers and engineers to interact with it physically. This hands-on experience often reveals design flaws that may need to be evident in digital models or drawings. For instance, it can uncover issues related to ergonomics, size, shape, or overall aesthetics.
Iterative Improvement: Identifying design flaws early in development allows for iterative improvements. Designers can make necessary adjustments and refinements to the prototype before moving forward, saving time and resources that would have been spent on correcting these issues after production has started.
Validation of Design Intent: Prototypes help ensure the final part aligns with the original design intent. They provide a concrete representation for stakeholders to review and approve, helping to avoid misunderstandings or misinterpretations of the design.
Technical Issues
Functional Testing: Prototypes allow for comprehensive testing of the product’s functionality. This includes assessing how well different components work together, whether electronic systems operate as intended, and if the product meets performance specifications. Any technical challenges or deficiencies can be identified and addressed before mass production.
Compatibility Verification: In complex systems or devices, prototypes can be used to verify compatibility with other equipment or systems with which the product may interact. This ensures seamless integration and operation in real-world environments.
Material and Manufacturing Considerations: Prototypes built with actual materials and manufacturing processes can reveal any issues related to material selection, assembly, and manufacturing techniques. This helps refine the production process to ensure consistent quality in the final product.
Usability Problems
User-Centered Evaluation: Prototypes are invaluable for user testing and gathering feedback on the product’s usability. This includes assessing how easily users can interact with the device, understand its functions, and achieve their intended goals. It helps in identifying potential barriers or challenges that users may face.
Addressing Accessibility: For medical devices, ensuring accessibility is crucial. Prototypes can be used to evaluate accessibility for individuals with disabilities, providing that a wide range of users can use the device safely and effectively.
Human Factors Engineering: Usability testing with prototypes aligns with human factors engineering principles, aiming to optimize human interaction and systems. It helps in designing products that are intuitive, efficient, and user-friendly.
What Are the Phases of Rapid Prototyping Cycle?
Sport car prototype
Here are the different phases in the rapid prototyping cycle:
Preparation of the 3D file, usually in an STL file, starting from a CAD model prepared by the designer or through reverse engineering, that is, creating a model starting from a piece already made, perhaps with a 3D scanner.
Management of the 3D model, with the repair of the mesh, the orientation of the piece, preparation of the printing plate (nesting), and printing layers (slicing).
Printing of the prototype layer by layer according to the different technology used.
The processing phase, i.e., the finishing of the piece by removing supports or excess material and improving the surfaces by sandblasting or dyeing to make the final product as similar as possible to the desired one.
What Are the Best Practices for Prototyping?
Prototyping is an essential step in the software product development process that can assist teams in producing better products. Teams can adhere to the following best practices to guarantee the efficacy and efficiency of the prototyping process:
Determine the problem and goals: Before you start prototyping, you should clearly understand the problem you want to solve and the goals you want to achieve. This will assist you in developing focused and effective prototypes.
Use the correct tools: There are numerous prototyping tools available, including UG, and HPM. It is important to select the appropriate tool for your prototype project based on your team’s skill set and the project’s requirements.
Start small: When creating your prototypes, it is essential to begin with simple designs and interactions. This lets you quickly iterate and refine your ideas without wasting time or resources.
Get feedback soon and often: It is essential to involve users in the prototyping process as early as possible and to collect feedback at each stage. This feedback can assist you in identifying potential problems and improving the final product.
Usability test: It is essential to test your prototypes for usability to ensure they are intuitive and simple. This can be accomplished through user testing, which involves observing how users interact with your prototype and gathering feedback on its usability.
Be flexible: Prototyping is an iterative process involving trial and error. Adaptability and willingness to make changes based on user and stakeholder feedback is critical.
Document the process: You can streamline your workflow and ensure you adhere to best practices by recording your CNC prototyping procedure. Notes on design choices, user comments, and prototype iterations can all be found in this paperwork.
Successful product development teams can produce successful prototypes by adhering to these best practices. Prototyping can result in a better final product and lower the risk of developing a product that does not meet market requirements or user needs.
Applications of Rapid Prototypes
3D prototype model by resin material
Prototypes find applications across various industries where precision machining is involved. In many of these sectors, there’s a constant demand for a functional prototype to demonstrate the functionality of the actual product. Here are some applications of prototypes in different industries:
Medical Industry
The field of medicine is progressing rapidly, prompting a demand for new equipment. Yet, in many cases, medical companies require a prototype to ensure the functionality of the intended product. Given the critical nature of healthcare, precision is paramount, and the prototype must closely mirror the final product. This holds true for various medical devices such as orthotic devices, medical implants, MRI machines, safe enclosures, research equipment, and more.
Automotive Industry
Similar to the medical sector, testing prototypes is crucial to ensuring their functionality and compatibility with the vehicle before mass production. Prototype machining plays a pivotal role in crafting automotive prototypes to precise specifications. Additionally, it extends its capabilities to manufacturing parts for various modes of transportation, including shipping vessels, transport trucks, and more.
Aerospace Industry
There is zero tolerance for errors in the aerospace industry, where even a small mistake could lead to drag or increased wear on components. Therefore, prototypes are crucial in this industry. Testing the functionality of parts before actual use in an aircraft is a standard practice. Common prototypes include parts of landing gear, manifolds, bushings, airfoils, and more.
Military Sector
The production of complex contraptions for ammunition and war vehicles necessitates the use of prototypes. In this context, rapid prototypes prove to be ideal candidates. Examples of devices crafted for this industry encompass plane parts, communication elements, transportation components, ammunition, and more.
Choose XTJ for Your Prototyping Services
We at XTJ recognize the value of efficient prototyping in creating prototypes. We offer superior rapid prototyping solutions through cutting-edge manufacturing techniques like 3D printing, CNC machining, and sheet metal fabrication. At XTJ, we deliver exceptional services covering the entire spectrum of manufacturing, from initial prototyping to full-scale production.
Our team of skilled professionals and advanced machinery guarantee that every detail of your prototype is meticulously crafted, meeting the highest standards of quality. We tailor our rapid prototyping services to suit the unique needs of your project, ensuring a customized and optimized experience.
Our commitment to excellence ensures top-tier quality and significantly lowers production costs and reduces time-to-market for your projects. Our cutting-edge rapid prototyping services are designed to bring efficiency, precision, and innovation to your product development journey. Get a quote today for your prototyping and production needs.
Conclusion
Rapid prototypes are essential parts of manufacturing innovation. They provide a quick, tangible glimpse into the product, streamlining development and minimizing risks. They bridge the gap between ideas and reality.
We have explored the various types of prototypes, uncovering how they cater to diverse industry needs. We have also touched upon the best practices for effective prototyping – a roadmap that guides manufacturers toward success.
However, you must work with a reliable manufacturing partner to ensure unmatched speed and efficiency with rapid prototyping. XTJ’s rapid prototyping services is your gateway for groundbreaking products.