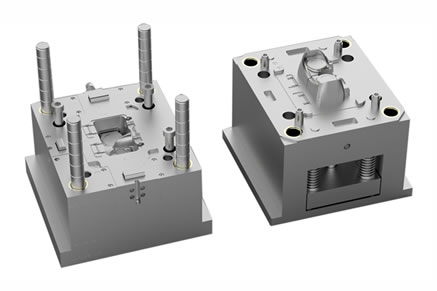
Custom plastic injection molding is a manufacturing process that involves the creation of a three-dimensional object by injecting molten plastic into a mold. This technique produces plastic parts with high precision and consistency, making it a popular choice in various industries such as automotive, medical, and consumer goods. With custom plastic molding, companies can create unique products that meet their specific requirements and design needs. The process begins with the design of a mold, which is then filled with melted plastic under high pressure. Once the plastic cools and solidifies, you open the mold, removing the finished product. Custom plastic injection molding offers a cost-effective way to produce large quantities of plastic parts quickly and efficiently, making it an ideal choice for mass production.
How to make custom plastic molds
Custom plastic molds are an essential tool for manufacturing plastic parts. They allow for the production of high-quality, consistent parts at scale. If you’re interested in creating custom injection molds, there are a few things to remember. The first step is to design your mold using computer-aided design (CAD) software. This will allow you to create a precise 3D model of your mold, which you can use to create a physical prototype using 3D printing or other rapid prototyping techniques. Once you’ve finalized your design, you can begin the mold-making process. This typically involves CNC machining or electrical discharge machining (EDM) to create mold cavities and other features. After the mold is complete, it’s important to test it thoroughly to ensure that it produces high-quality parts. This may involve adjusting the mold design or making other modifications as needed.
Choosing plastic injection molding materials
When making custom plastic molds, it’s also important to consider the material you’ll use for your parts. The type of plastic you choose can significantly impact the final product’s quality, strength, and durability. It’s important to select a material that is well-suited to the specific application that you have in mind. You should also consider factors such as cost and ease of processing when selecting a plastic material. Once you’ve chosen a material, you must determine the appropriate injection molding parameters, such as temperature, pressure, and cooling time. You can create high-quality parts that meet your specifications by carefully selecting your materials and optimizing your injection molding process.
custom injection mold
How much does custom plastic molding cost
The cost of custom plastic molding can vary widely depending on various factors. Some key factors that can affect the cost of custom plastic molding include the complexity of the part design, the quantity of parts you produce, the type of plastic material you use, and the specific injection molding process you use. Generally, custom plastic molding costs can range from a few hundred dollars for a simple part to tens of thousands of dollars or more for a complex part with high-volume production requirements.
Work with an injection molding company
To get an accurate estimate of the cost of custom plastic molding for your specific needs, it’s important to work with a reputable injection molding company that can provide you with a detailed quote based on your specific design and production requirements. This will typically involve providing the company with a detailed 3D CAD model of your part design, as well as information about the required quantities, material specifications, and other key details. By working with an experienced injection molding provider, you can ensure that you get a high-quality part at a fair and competitive price.
Different types of custom plastic injection molds
Custom plastic injection molds are a versatile tool that you use to produce a wide range of plastic parts with high accuracy and consistency. There are several different types of custom plastic injection molds, each with its own unique advantages and disadvantages. One of the most common custom plastic injection molds is the two-plate mold. This mold consists of two plates that are used to form the part cavity and the runner system. Two-plate molds are simple and easy to use, making them popular for low to medium-volume production runs.
What are three-plate injection molds
Another type of custom plastic injection mold is the three-plate mold. As the name suggests, this mold has an additional plate that separates the runner system from the part cavity. This allows for greater flexibility in the injection molding process, as it allows for more complex part designs and multiple materials. However, three-plate molds are more complex and expensive than two-plate molds, making them more suitable for high-volume production runs. Other custom plastic injection molds include hot runner molds, cold runner molds, and family molds, each with unique features and benefits.
XTJ is a leading OEM Manufacturer that is dedicated to providing one-stop manufacturing solutions from prototype to production. We are proud to be an ISO 9001 certified system quality management company and we are determined to create value in every customer relationship. We do that through collaboration, innovation, process improvements, and exceptional workmanship.