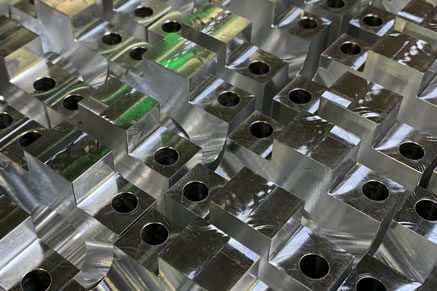
Table of Contents
What is Conversion Coating:Types and Application?
Conversion coatings are a significant factor in improving the performance and longevity of metal surfaces. These coatings are tightly adherent, protective layers of non-soluble compounds produced on the surfaces of materials through chemical or electrochemical reactions. These coatings are usually applied to protect a metal substrate from corrosion, but they may also serve as a base layer for additional coating layers, enhance surface lubrication, or be applied to achieve a desired appearance.
The four most common conversion coatings include chromate, phosphate, black oxide, and bluing. Black oxide and bluing apply only to steels. They enhance appearance but offer little corrosion protection.
This article will discuss the significance of conversion coatings in surface treatment and metal protection by exploring their functions, workings, and types.
What Is Conversion Coating?
“Conversion coating” is a comprehensive term describing coatings formed through chemical or electrochemical treatment of metallic surfaces, resulting in a superficial layer containing a metal compound. This procedure extends the life and functionality of metal materials by improving qualities like lubrication and corrosion resistance. They can also improve the adhesion of subsequently applied coating layers.
Is Conversion Coating the Same as Barrier Coating?
No. Chemical conversion coatings, or conversion coatings, are a type of surface passivation used to modify the surface of a metal, creating a protective metal oxide layer against corrosion and wear. On the other hand, barrier coatings serve as effective moisture or physical barriers, often applied on metals and ceramics to withstand harsh conditions. While conversion coatings enhance metal surfaces, barrier coatings provide a protective layer against environmental factors, sometimes applied over conversion coatings for added protection.
Is Conversion Coating the Same as Anodizing?
No, anodizing is a specific type of conversion coating. Conversion coating refers to various processes in which a metal surface undergoes a chemical reaction to enhance its properties. One particular technique in this category is anodizing, which involves the electrolytic oxidation of metals, usually aluminum, to produce a layer that is resistant to corrosion.
What Is the Purpose of Conversion Coating?
The purpose of a conversion coating is to create a protective layer on a metal substrate that contributes to the overall durability and performance of the metal. It provides a more suitable surface for painting and bondings.
How Is Conversion Coating Used in Manufacturing?
Conversion coatings are used by manufacturers of metal products requiring protection from environmental degradation to increase their corrosion resistance, and therefore their durability. Conversion-coated products are immersed in or sprayed with a coating solution appropriate to the alloy, which reacts with the metal to produce a layer that inhibits corrosion and aids in the adhesion of additional coating layers, such as paint. This treated surface is essential in several industries. In automotive applications, conversion coatings are used on car bodies and parts to protect against rust and corrosion, prolonging the lifespan of vehicles. In aerospace, conversion coatings are essential for aircraft components to withstand harsh environmental conditions and maintain structural integrity.
How Do Conversion Coatings Work?
Conversion coatings work by chemically reacting with the metal surface to create a protective layer. This process varies among the different coating types, which include: phosphates, chromates, and black oxide coatings. The specific chemical reactions for each type contribute to enhanced corrosion resistance, improved adhesion for subsequent coatings, and increased overall durability in diverse industrial applications.
How Does Conversion Coating Differ From Other Types of Coating?
Conversion coatings differ from other types of coating primarily because they chemically react with the metal surface, forming a protective layer. In contrast, physical coatings like paints merely create a barrier between the metal and the environment. Protective coatings can be categorized into barrier coatings, inhibitive coatings, sacrificial coatings, and combinations thereof. While non-metallic coatings often utilize polymers, epoxies, and polyurethanes, metallic coatings commonly employ zinc, aluminum, and chromium for corrosion protection. Conversion coatings provide unique chemical modification of the metal surface, enhancing its resistance to corrosion and improving adhesion for subsequent coatings.
What Are the Different Types of Conversion Coatings?
The different types of conversion coatings include:
1. Chromate Conversion Coating
Chromate conversion coating, also known as alodine coating, can produce versatile protective layers on metals such as: steel, aluminum, zinc, and others. This coating, applied by immersion or spraying, is produced by a chemical reaction that occurs on the metal surface. The spray or bath contains chromates and dichromates. The resulting gel forms a thin, corrosion-resistant layer that not only inhibits rust but also enhances paint and adhesive adherence. Commonly applied to items hardware, such as screws, hinges, brackets, and washers, chromate conversion coatings often impart a distinct, easily recognizable greenish-yellow hue to metal surfaces. Figure 1 is an example of a chromate conversion coating on a part:
conversion coating
Chromate conversion coating. Image Credit: Shutterstock.com/KPixMining
2. Molybdate
Molybdate conversion coatings provide corrosion protection for aluminum and its alloys, magnesium and its alloys, as well as zinc and zinc-nickel alloys. They are considered a less harmful alternative to chromate coatings, possessing similar anti-corrosion qualities without the associated environmental risks.
3. Phosphate Conversion Coating
Phosphate conversion coating, a common chemical treatment for steel parts, enhances corrosion resistance and provides a foundation for subsequent coatings. The process involves applying a solution of phosphoric acid and soluble salts such as zinc, iron, and manganese phosphate by sponging or spraying it onto the metal surface. These salts increase corrosion resistance by reacting with the metal surface to create a protective coating. The temperature and bath concentration are two examples of parameters that affect coating characteristics in different ways. Greater corrosion protection can be achieved by thicker coatings produced by higher bath concentrations. The speed of chemical reactions is another way that temperature influences coating adherence and thickness. In industrial applications, optimal management of these parameters ensures.
4. Titanate
AZ31 magnesium alloys are coated with titanate to provide protection. Organotitanates, such as tetra isopropyl titanate (TIPT) and tetra butyl titanate (TNBT), are commonly used for this purpose due to their reactivity. This coating creates a thin barrier that prevents corrosion and other forms of wear and tear. The formation process involves the precipitation of silicon hydroxide, titanium hydroxide, magnesium hydroxide, and fluoride, resulting in a porous layer that enhances corrosion resistance.
5. Anodizing
Anodizing, an electrolytic passivation process widely applied to aluminum alloys, titanium, and a couple of other metals, works by passing a direct current through an electrolytic solution, forming an oxide layer on the metal surface. Anodized coatings enhance resistance to corrosion and wear, and provide better adhesion for paint primers and glues. This process finds diverse applications in consumer products like smartphones and kitchen appliances, as well as in aerospace components like aircraft parts.
6. Stannate
Stannate conversion coatings offer a chromate-free way to prevent corrosion of magnesium alloys. A stannate conversion coating consists primarily of a layer of magnesium tin oxide developed by submerging the magnesium alloy workpiece in a dilute stannate solution. Such a coating functions as a barrier against corrosive agents, lowering corrosion rates, (displaying self-healing qualities, meaning it can repair minor damage to the coating over time).
7. Black Oxide
Black oxide serves as a conversion coating applied to a range of materials such as: ferrous metals or iron-based alloys, copper, zinc, and more. The oxide formed in the materials may be black but they are not all the same compound. The primary objectives of black oxide include: providing mild corrosion resistance, enhancing appearance, and reducing light reflection. For iron-based alloys, this process consists of placing the metal to be coated submerged in a hot (typically 141 °C) bath containing sodium hydroxide, nitrates, or nitrites of metals such as sodium. The compounds in the bath react to form a layer of magnetite (Fe3O4) on the material’s surface.
Hot, mid-temperature and cold black oxide processes offer specific advantages. Hot black oxide offers a deep, uniform black finish, enhances corrosion resistance, and improves lubricity. Mid-temperature black oxide balances cost and performance, suitable for moderate corrosion protection. Cold black oxide requires less energy, ideal for delicate components, providing corrosion protection while maintaining dimensional stability. After the blackening process is complete, oil, wax, or lacquer is applied to the material to improve corrosion resistance.
In contrast to iron-based alloys, copper (Cu) and zinc (Zn) require a different procedure for the application of black oxide coating. The procedure for these metals entails submersion in a chemical solution that contains particular oxidizing agents that are chosen based on the metal’s makeup. The ensuing oxide layer changes the metal’s look and offers corrosion resistance, although the compounds that form can differ. Furthermore, unlike iron-based alloys, these metals can need different temperatures, chemical compositions, and post-treatment methods when applying black oxide.
8. Zirconate
Zirconate coatings provide strong, long-lasting finishes. The surface preparation required for applying Zirconate coatings involves thorough cleaning and degreasing of the metal surface to remove any contaminants, such as oil, grease, or dirt to ensure a long-lasting bond with the metal. Better paint adherence, corrosion protection, and phosphate-free pre-treatment are some advantages of zirconate coatings. These coatings, which work on steel, zinc, and aluminum, have both financial and environmental benefits. They cut waste and emissions and require less upkeep and repair. Advantages of the process include reliability in quality and compatibility with current production lines.
9. Bluing
Bluing, like black oxide conversion coatings, results in a tightly adherent Fe3O4 coating on the surface of an iron-based alloy. The coating developed by bluing is much thinner than the coatings termed “black oxide” coatings. Bluing offers only partial protection against rust because it is so thin. Bluing can be accomplished by several different processes, including cold, hot, rust, and fume bluing. Cold bluing, utilizing selenium dioxide-based compounds, is suitable for small touch-ups, while hot bluing involves alkali salt solutions and is commonly used in large-scale gun bluing. Rust bluing provides excellent rust and corrosion resistance, and fume bluing mimics rust bluing using mixed acid fumes. The application of bluing is prevalent in the firearms industry for cosmetic enhancement, corrosion resistance, and glare reduction, with varying degrees of effectiveness depending on the process used.
10. Plasma Electrolysis
Plasma electrolysis or plasma electrolytic oxidation (PEO) forms a ceramic layer on the surface of light metals through a unique process involving a high-voltage electrolyte bath. PEO coatings offer corrosion and wear resistance, and are up to four times harder than low carbon steel. The process involves three steps: substrate preparation, substrate oxidation, and plasma modification. The ability to control and adjust each step provides flexibility, allowing for coatings with diverse properties to meet various industrial needs. PEO coatings find utility in automotive and aerospace industries due to their low stiffness and resistance to edge cracks. Additionally, PEO’s eco-friendly method utilizes safe aqueous solutions.
How To Choose a Conversion Coating
Choosing the right conversion coating involves considering several factors, including: the type of metal substrate, the intended application, environmental conditions, and regulatory requirements. Here are some steps you can take to help you select the appropriate conversion coating:
Determine the type of metal you are working with, as different metals may require different types of conversion coatings. For example, aluminum and steel often use different conversion coatings.
Understand the purpose of the conversion coating. Are you primarily seeking corrosion protection, paint adhesion, or other specific properties? The desired outcome will influence your choice.
Evaluate the environmental conditions the coated metal will encounter, such as humidity, temperature extremes, and exposure to chemicals. Choose a conversion coating that demonstrates resistance to these specific conditions, ensuring optimal performance over time.
Investigate industry and local regulations governing conversion coatings. Make sure that you will be able to comply with the environmental standards, safety guidelines, and hazardous chemical restrictions that cover your potential conversion coating candidates.
Consider the expected service life of the coated metal in its intended environment. Select a conversion coating that offers the necessary durability against wear, corrosion, and other potential challenges to meet or exceed the anticipated lifespan.
Is Passivation a Conversion Coating?
Yes, passivation is a type of conversion coating. It involves the formation of an outer layer of shield material through either a chemical reaction with the base material or spontaneous oxidation in the air. Passivation coatings can develop naturally on certain alloys, providing enhanced corrosion resistance and surface protection.
What Are the Applications of Conversion Coating?
Many industries utilize conversion coatings. One prominent application is the “black oxide coating for steel.” This treatment offers better paint adhesion, increased visual appeal, and resistance against corrosion. Black oxide-treated steel components are appropriate for industrial, automotive, or architectural applications in which both practicality and aesthetics are important.
What Is the Quality of Conversion Coated Product?
The quality of a conversion-coated product is determined by several important characteristics including:
Corrosion Resistance: Conversion coatings provide a protective barrier against corrosion, extending the lifespan of the substrate material. The corrosion resistance is often evaluated through standardized salt spray testing or electrochemical impedance spectroscopy.
Adhesion: The adhesion of the conversion coating to the substrate material is crucial for long-term durability. Adhesion tests, such as cross-hatch adhesion tests or pull-off tests, assess the strength of the bond between the coating and the substrate.
How Thick Is Conversion Coating?
Conversion coatings add a thin layer of protective material to a metal surface. For example, aluminum chromate coatings usually range in thickness from 0.00001 to 0.00004 inches.
How Long Do Conversion Coatings Last?
The longevity of a conversion coating is influenced by factors such as environmental conditions and maintenance. With proper care, these coatings can endure for several years, providing effective corrosion protection and other benefits to the treated metal surfaces.
What Are the Benefits of Conversion Coating?
Conversion coating offers various benefits, including:
One of its functions is to shield metal surfaces from corrosion, extending the lifespan of components.
Conversion coating improves bonding for paints and coatings, ensuring a more durable and lasting finish.
It provides an aesthetically pleasing surface finish.
A conversion coating prepares a surface for various subsequent treatments or applications, such as paint, primer, adhesive bonding, or other surface finishes.
It can enhance electrical conductivity or insulation, depending on the type of conversion coating.
What Are the Downsides of Conversion Coating?
Conversion coatings come with certain downsides, including:
Some conversion coatings may involve chemicals that pose environmental risks during manufacturing or application.
Certain chemicals used in conversion coatings may present health risks to those involved in the application process.
Compliance with environmental and safety regulations can be complex and demanding.
Depending on the type, conversion coatings may have limited durability, requiring periodic maintenance.
The application process can be complex, requiring careful control and expertise.
Initial and maintenance expenses can be a factor in the overall cost-effectiveness compared to the long-term benefits or total lifecycle costs of the product or service.
Is Conversion Coating Expensive?
Conversion coating processes can vary in cost depending on factors such as the type of metal being treated, the desired properties of the coating, and the scale of production. While conversion coating can offer significant benefits in terms of corrosion resistance and paint adhesion, it may not always be the most cost-effective solution.