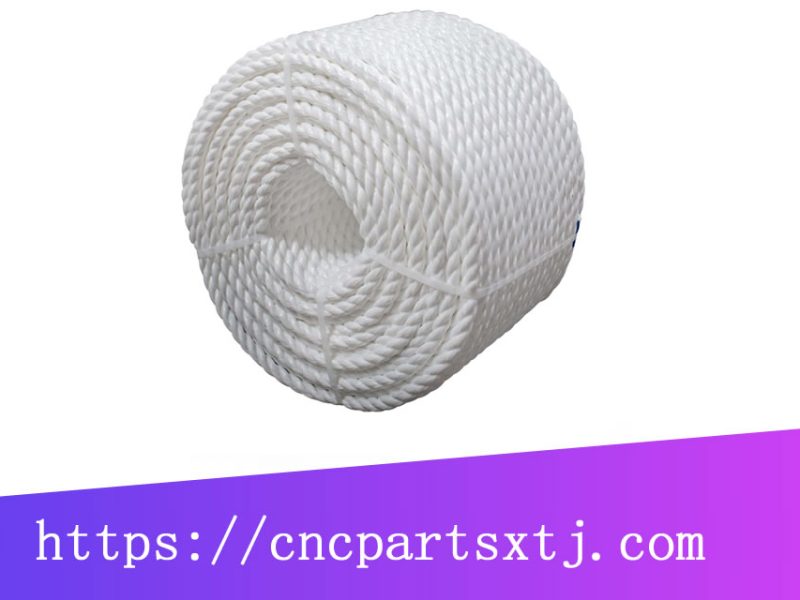
Polypropylene(PP) is a polymer made up of repeating propene monomer units. The polymer stands out against other polymers for its lightweight, chemical resistance, flexibility, and transparency. Polypropylene is a general-use polymer that is used in applications including packaging, automotive, textile, and medical industries. The impact of polypropylene is that there is a lightweight and cost-efficient material whose properties can be manipulated to suit a wide range of applications.
This article will discuss polypropylene, its properties, applications, composition, and impact.
Table of Contents
What Is Polypropylene (PP)?
Polypropylene is a low-density and heat-resistant thermoplastic polymer, which is slightly harder than polyethylene. The chemical structure of polypropylene can be manipulated to create a polymer that is either hard or soft, light or heavy, opaque or transparent, and insulative or conductive. Polypropylene melts rather than burns and becomes soft at a raised temperature and hard when cooled, these are two key properties of polypropylene.
What Material Composes a Polypropylene?
Polypropylene is a thermoplastic with a crystalline structure. It is composed of a propene monomer which is connected in a polymer chain in either a homopolymer or copolymer chain.
What Are the Properties of Polypropylene?
The properties of polypropylene are:
High chemical resistance
Fatigue resistant
Heat resistant
Tough
Semi-rigid
Translucent
What Is the Purpose of Polypropylene?
The purpose of polypropylene is to provide a lightweight, high-strength, cost-effective material for the packaging, automotive, medical, and textile industries. Polypropylene is a polyolefin that is harder than polyethylene which makes it a useful substitute for polyethylene.
What Is the Use of Polypropylene?
Polypropylene is used for applications that require chemical resistance, light weight, low cost, and transparency. Such applications include: drinks bottles, bottle caps, medical syringes, interior vehicle trim, plastic bags, and protective helmets.
How Is Polypropylene Different From Other Plastics?
Although polypropylene is similar to other plastics in many ways, it does have some different characteristics that make it stand out. The first is that it is very lightweight. Because of polypropylene’s low weight, it is used to make ultra-low-density foam. It is more transparent than other plastics, making it a good choice for packaging applications. Polypropylene is also more easily degradable and takes less energy to produce, making it more sustainable for the environment.
What Are the Different Types of Polypropylene?
7 different types of polypropylene are used for different purposes. These different polypropylene types are listed below:
Homopolymer: This is the most common, general-purpose, polypropylene. This form has one propylene monomer and is used in healthcare, packaging, pipes, healthcare, automotive, and electrical applications.
Copolymer: Polypropylene copolymer is produced through the polymerization of propene and ethane. Ethane contents of 6% by weight and ordered randomly in the polymer chain create a polypropylene random copolymer, which is transparent and flexible. Ethane contents of 5–15% ordered in a regular pattern within the polymer chain create a tougher and less brittle polypropylene referred to as polypropylene block copolymer. This is used in high-strength applications.
Impact Copolymer: Is polypropylene with an ethane content of 45–65%. This increases its impact resistance and is used mainly for packaging, houseware, and piping applications.
Expanded: Expanded polypropylene creates an ultra-low-density foam with a high strength-to-weight ratio, thermal insulation, chemical resistance, and impact resistance. Expanded polypropylene is used in construction, packaging, and the automotive industry.
Terpolymer: A polypropylene terpolymer uses ethylene and butane to connect propylene segments. The ethylene and butane are more transparent than polypropylene and are in the chain in random order. Polypropylene terpolymer is best used for sealing film applications.
High Melt Strength: High melt strength polypropylene is a long chain branched polymer with a wide range of good mechanical properties, high heat stability, and high chemical resistance. This form of polypropylene is used to make soft, low-density foams for packaging.
Bio-based: Bio-based polypropylene gets its title because it uses a renewable feedstock to create its monomer for anywhere between 30–100% of its content by weight.
What Are the Most Common Uses of Polypropylene in Everyday Products?
Polypropylene is used in many products which people use every day. The most common are in packaging, automotive parts, and fabrics. Polypropylene can be used in packaging for food, cosmetics, medical products, and laboratory items. The automotive industry uses polypropylene for instrument panels, bumpers, door trim, and other interior plastics. Polypropylene is used for tape, continuous filament, strapping, and raffia in the fabric industry.
What Industry Usually Uses Polypropylene?
Since polypropylene is a general-purpose plastic, it is used in many industries including: packaging, automotive, textile, medical, and electrical cable industries. Each industry makes use of polypropylene for different reasons. However, some recurring reasons are its chemical resistance, low cost, high strength, and low density.
Can Polypropylene Be Used in Food Packaging?
Yes, food packaging is one of polypropylene’s most common uses. The FDA has approved its use as a food container and, currently, there is no evidence to suggest that the material is cancer-causing. Polypropylene is safe to use as a single-use plastic for food containers and is also safe for use as microwavable containers.
To learn more, see our article on Types of Packaging Materials.
Can Polypropylene Be Used in High-Temperature Applications?
No, polypropylene is not suited for hot-temperature applications. The maximum recommended operating temperature for polypropylene is 82 °C. At temperatures above this, the polymer will begin to lose its mechanical properties. For many applications 82 °C is considered to be a low operating temperature.
What Are the Environmental Impacts of Producing and Disposing of Polypropylene?
Producing and disposing of polypropylene is considered more environmentally friendly than using other materials such as PET. Polypropylene produces only 1.95–3.5 kg of CO2 for every 1 kg of polypropylene produced. Polypropylene takes 20 to 30 years to degrade. The material produces less solid waste by weight than PET, PS, or PVC and can be recycled with little waste. While the production and disposal of polypropylene does have a negative environmental impact, it is one of the less impactful plastics that is produced. This impact could be further reduced, as currently only 1% of polypropylene produced is recycled.
What ISO Standards Are Applicable to the Manufacturing and Quality Control of Polypropylene?
ISO 19069-1:2015 is a standard for the molding and extrusion of polypropylene. This standard is used to identify and designate the different types of polypropylene. The types of polypropylene are classified based on their tensile modulus, impact strength, and melt flow rate as well as other important parameters including processing method, fillers, and reinforcing materials. ISO 5677:2023 is another standard for the testing and characterization of mechanically recycled polypropylene.
What Is the Advantage of Using Polypropylene?
There are many advantages to the use of polypropylene, which is why it is one of the most used general-purpose plastics. These advantages are listed below:
Can carry 4,000 psi, which is high when compared to other plastics.
Due to polypropylene’s structure, it is non-reactive with acids which makes it an ideal container for cleaning chemicals.
Does not absorb water, it will only absorb 0.01% of its weight when submerged in water, which makes it waterproof. This is an ideal property for waterproofing.
Flexibility allows polypropylene to be melted and formed into any shape required, when at a lower temperature the polymer retains its flexibility which means it can be used as a hinge for bottle lids.
Is used for protecting cables as it is a very good insulator.
What Is the Disadvantage of Using Polypropylene?
The use of polypropylene does have its disadvantages. The disadvantages below need to be considered before using polypropylene for any application:
Is not suitable for use at high altitudes or in applications with persistent exposure to direct sunlight. The UV rays will degrade the bonds of the polymer chain making the plastic brittle and susceptible to water absorption.
As polypropylene is heated it will expand and change shape at a higher rate than other plastics which is not desirable.
Polypropylene’s material properties worsen as the polymer is heated over 82 °C.
The poor bonding properties of polypropylene make it hard to paint or apply any surface coatings.
Has a low melting point as well as a low flash point which makes it more susceptible to ignition.
Is Polypropylene a Safe Plastic To Use?
Yes, polypropylene is safe to use, it is a non-toxic material that is approved for use in food packaging. Polypropylene is also approved for use in medical implants which makes it one of the safer plastics in use today. There is no evidence that polypropylene is a cancer-causing material and it has no BFAs (Bisphenol A) which are a growing concern for human health.
What Is the Difference Between Polypropylene and Polyethylene?
The difference between polypropylene and polyethylene is that polypropylene is much lighter, chemically resistant, and abrasion-resistant. Polyethylene is used over polypropylene because it is more flexible. The polypropylene chain is made up of repeating propene monomers whereas polyethylene is made up of repeating ethylene monomers.
XTJ is a leading OEM Manufacturer that is dedicated to providing one-stop manufacturing solutions from prototype to production. We are proud to be an ISO 9001 certified system quality management company and we are determined to create value in every customer relationship. We do that through collaboration, innovation, process improvements, and exceptional workmanship.