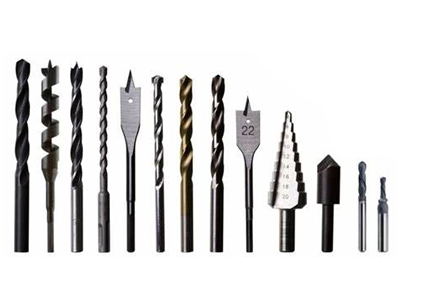
Table of Contents
What is Drilling ?
Drilling is a process that is used to create a cylindrical hole or bore in a solid piece of material, often as a precursor to tapping or to prepare the material for insertion of a fastener such as a bolt or a screw. The cutting tool used for drilling is called a drill bit, twist drill, or sometimes just a drill, but the latter may also refer to the entire tool as opposed to just the cutting bit itself.
Drill bits are some of the most common and versatile parts of any machine shop or home tool shed. They can drill into metals, solid wood furniture, porcelain, and even glass, and with a variety of different drill bits available, one can find an appropriate bit for almost any situation. One major aspect of drill bit selection is the material makeup of the drill bit itself. Not all twist bits will work on all applications. It is important to match the material of the bit to the material of the workpiece to produce the best results.
This article will present information on drill bits and the common materials from which they are manufactured to assist in the selection process for a particular application.
Best Material for Drill Bits
The best materials for drill bits are carbon tool steel, high-speed steel, and carbon high-speed steel. Standard twist drills are fabricated using steel whose mechanical properties allow the drill bit to maintain its toughness, exhibit good abrasion resistance, and resist changes in harness as a result of the heat that is generated during the drilling process. Generally, the selection of the drill bit for a particular application should be made by giving consideration to the amount of heat that will be generated.
Carbon Tool Steels
Carbon tool steels are used for applications where little heat is going to be generated. Both low and high carbon steels are both used for drill bits, but for different purposes. Soft low carbon steel cannot cut hard metals due to their poor tempers, but it can cut softwoods and plastics. They require sharpening to extend their lifespan. The primary bonus of low carbon steel is its relative inexpensiveness, especially when compared to some more exotic drill bit materials.
High carbon steels have better tempers than low carbon steels, so they require less maintenance, such as sharpening, and hold their form and effectiveness longer. They can cut both woods and metals, and if available, are preferred to low carbon steels when cutting extremely hard woods.
High-Speed Steel
High-Speed Steel (HSS) is a preferred material for use in drill bits since it has a higher red hardness and improved wear resistance. These properties allow for drilling at higher operating speeds and into harder materials. The friction created by high-speed turning can raise temperatures dramatically, but HSS is designed to operate at these higher speeds. HSS can function at normal temperatures, as well, but only at a level equal to standard carbon steel. HSS can also take coatings, such as titanium nitride, which give the drill bit better lubricity, decreasing friction and helping to extend the bit’s life.
Cobalt High-Speed Steel
Cobalt High-Speed Steel (HSS) drill bits have added Cobalt which gives the material a higher red hardness than standard HSS. This additional hardness permits these drill bits to be used for drilling materials that have a hardness of Rockwell 38C or greater such as treated stainless steel, cast iron, or titanium. They are also capable of being utilized at higher cutting speeds than conventional HSS and exhibit superior abrasion resistance.
Tungsten Carbide
Tungsten carbide is an extremely hard and wear-resistant material. Drill bits with tungsten carbide tips are effective for drilling into hard materials such as concrete, masonry, and some metals. Solid carbide drill bits are suitable for high-speed drilling applications.
Carbide Tipped
Carbide-tipped drill bits combine the toughness of steel with the hardness of tungsten carbide inserts. These bits are effective for drilling into hard materials and are commonly used in masonry and woodworking.
Diamond-Coated
Diamond-coated drill bits are designed for drilling into extremely hard materials like glass, ceramics, and tiles. The diamond coating provides excellent hardness and wear resistance.
Black Oxide-Coated
Black oxide-coated drill bits have a coating that enhances their durability and provides some corrosion resistance. They are suitable for general-purpose drilling in various materials.
Titanium-Coated
Titanium-coated drill bits have a layer of titanium nitride that increases their hardness and reduces friction. These bits are suitable for drilling into metal, wood, and plastic.
What is the Strongest Drill Bit Material?
Tungsten carbide is one of the strongest materials used for drill bits. Tungsten carbide is a composite material made from tungsten and carbon atoms, resulting in an exceptionally hard and wear-resistant substance.
Drill Bit Terminology
American National Standard B94.11M-1993 covers the relevant information relating to drill bits, including sizes, tolerances, nomenclature, and definitions. Below is a summary of some of the key terminology relating to drill bits.
Axis – refers to a centerline running down the middle of the drill bit longitudinally from the point of the drill bit to the end of the body.
Back taper – is a reduction in the drill bit’s diameter that occurs from the point of the drill bit to the end of the drill bit body. Most drill bits are machined with a small back taper to prevent the bit from binding in the workpiece when the drill bit becomes worn.
Body – refers to the portion of the drill bit that extends from the neck to the outer edges of the cutting lips and which contains the flutes.
Drill Diameter – the overall diameter of the drill bit measured at the point of the drill up to the margins.
Flutes – are the grooves that are formed in the drill bit which serve to allow the removal of chips from the hole being cut and to allow cutting fluid to reach the cutting lips of the bit. Flutes are usually helically shaped or straight cut.
Lips – the cutting surfaces of the drill bit.
Neck – a small section of the drill bit which has a reduced diameter that sites between the shank of the bit and the body.
Overall length – is the distance measured from the extreme end of the shank to the outer corners of the cutting lips. Note that this measurement excludes the conical shank end and the conical cutting point at the tip of the drill bit.
Point angle – the angle that is formed between the lips when a projection is made onto a planar surface that runs parallel to the axis of the drill bit and to the cutting lips.
Shank – the portion of the drill bit by which it is held in place and driven, i.e. the portion that does not contain flutes.
Types of Drill Bits
The classification of drill bits can be done in several ways –
By the type of shank
By the number of flutes
By the hand of cut
Common types of drill bits include:
Straight-shank drill bits
Taper-shank drill bits
Two-flute drill bits
Three-flute drill bits
Four-flute drill bits
Right-hand cut drill bits
Left-hand cut drill bits
Teat drill bits
Straight-shank drill bits have a cylindrically shaped shank that may or may not be the same diameter as that of the drill body.
Taper-shank drill bits are ones with a conically shaped shank that permits the drill bit to fit into tapered holes in machine spindles, driving sleeves, or sockets. Taper-shank drill bits will usually have a tang at the end of the shank which will fit into a driving slot in the socket.
Two-flute drill bits are the typical style of drill bit that is used to create new holes in a workpiece.
Three-flute drill bits and Four-flute drill bits are used to enlarge or finish pre-existing holes that have been drilled, cast, or punched in a material, but they are not used to create new holes.
Right-hand cut drill bits are ones that are designed to rotate in a counterclockwise direction as viewed from the cutting point end of the drill bit.
Left-hand cut drill bits are ones that are designed to rotate in a clockwise direction as viewed from the cutting point end of the drill bit.
Teat drill bits are ones in which the cutting edges are at a 90o angle relative to the axis line of the drill bit and are used to square off the bottoms of holes that have been drilled using standard drill bits. They also possess a small triangular-shaped extension at the tip of the drill which serves to lead and center the drill bit so that it holds its position during the drilling process.
For even more drill bits, shop from thousands of options on Xometry.com, the industry’s leading on-demand manufacturing platform.
Coatings and Treatments
Titanium
Titanium is a corrosion-resistant metal, and in the form of titanium nitride, is used as a coating applied to HSS drill bits to give them very high levels of surface hardness. This characteristic allows titanium-coated drill bits to be used to drill tough materials and last up to 6 times longer than standard HSS bits. This longevity makes it attractive for use in repetitive, large runs. It is a very versatile drill bit coating, and it can cut a broad variety of surfaces, including many types of steel and iron, as well as softer materials including wood, drywall, and plastic. The addition of titanium nitride also reduces friction between the bit and the workpiece, significantly reducing heat and therefore wear.
Black oxide
Black oxide is not a coating but rather a heat treatment process that is applied to HSS which reduces friction and increases the life of the drill bit by some 50% over that of standard HSS. They are created by heating HSS to 950 degrees F to add corrosion and rust resistance. These bits can be used for carbon steels, alloy steels, as well as softer materials such as wood, plastics, PVC, drywall as well as softer metals such as copper and aluminum.
Zirconium Coating
While not a primary material for drill bits, zirconium-coated metals function very well for drill bits. The zirconium nitride coating can increase strength for hard but brittle materials, like steel. The makeup of the zirconium also decreases friction for improved precision drilling.
Diamond
Some steel bits are embedded with diamond dust; these are available as either hollow core bits or as smaller blunt nose bits with no open space in the middle. The diamond enables them to cut through materials like glass, gemstones, ceramic, bone, and stone. However, they should not be used on ferrous metals.
Specialty Drill Bits
Beyond the typical drill bit types mentioned earlier, there are specialty drill bits that are sold for specific applications.
Plug cutter drill bits are used to cut a round plug from a piece of wooden stock material that can then be used to plug a counterbored hole for the purpose of concealing the hole.
Glass and tile drill bits feature carbide tips and a straight shank. These drill bits are used to drill holes in non-tempered glass or tile, such as when installing anti-slip safety bars in a tub or shower enclosure.
Masonry drill bits are used to drill into concrete, brick, using a hammer drill that provides a percussion action at the same time as the drill rotates.
Auger drill bits are used to cut larger holes in wood or similar materials and feature extra-large flutes to enable the cut chips to be removed from the hole. Similarly, spade drill bits (also known as paddle bits) have a flat wide blade that can be used to cut larger holes in wood. Traditionally, these are employed by plumbers and electricians to cut holes in wall studs and floor plates to allow wiring or plumbing pipes to be routed.
Forstner drill bits are used to provide more precise square bottomed holes in wood and are used, for example, to create a hole for countersinking concealed hinges that are traditionally part of kitchen cabinets.
XTJ is a leading OEM Manufacturer that is dedicated to providing one-stop manufacturing solutions from prototype to production. We are proud to be an ISO 9001 certified system quality management company and we are determined to create value in every customer relationship. We do that through collaboration, innovation, process improvements, and exceptional workmanship.