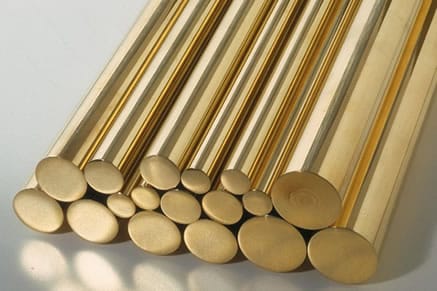
If you’ve got questions about aluminum bronze, or if you just want to get more familiar with it, this guide is for you. Here we’re diving into the basics of this family of metals, including makeup, properties, and applications.
Table of Contents
What is Aluminum Bronze?
Aluminum bronze is made up of 6-12% aluminum, replacing the tin traditionally used in other types of bronze. The rest is copper, although other elements such as iron, silicon, or nickel can be added to strengthen certain properties of the metal. This material is best known for its strength and corrosion resistance, which has led to its use in the marine, chemical, and energy industries. Aluminum bronzes are divided into groups of alloys depending on the percentage of aluminum and other elements present in the metal, which is covered in more detail below.
Aluminum Bronze Properties
The most standout features of aluminum bronze are its strength and corrosion resistance, but its properties vary with the form and alloy of the metal.
Aluminum bronze’s strength, which is on par with low alloy steels, changes with the form of the metal.
The table below contains information from the Copper Development Association on the tensile and yield strengths of general aluminum bronze in ksi (kilopounds per square inch) and MPa (megapascals) as well as hardness according to the Rockwell Hardness Test B scale.
Aluminum bronze’s other most major property is its corrosion resistance, which is higher than that of stainless steel, especially in seawater. On top of that the metal is resistant to oxidation, tarnish, fatigue, and creep, while remaining ductile and non-sparking. It also has low magnetic susceptibility and works well at high temperatures for sustained periods of time. This type of bronze has good properties for manufacturing as well. It’s easy to cast and fabricate, and can be machined, metallic arc welded, and brazed with special fluxes.
Apart from its general characteristics, each of the four basic groups of aluminum bronzes has its own specific traits:
Low alloy single-phase alpha aluminum bronzes. These have less than 8% aluminum. This type of aluminum bronze is best for cold working and remains ductile through both hot and cold temperatures.
High alloyed, two-phase aluminum bronzes. These have 8-11% aluminum, often with iron or nickel added to increase their strength. The increase of aluminum in the mix makes these metals better for hot casting and working. Alloys with 10% or more aluminum have the most strength and hardness, and are mostly used for specialized cases where wear resistance is crucial. The addition of iron increases the metal’s tensile strength, whereas nickel and manganese stabilize the structure. Nickel also improves the metal’s corrosion resistance and yield stress.
Silicon-aluminum bronzes. These are strong, ductile, shock load resistant, and have low magnetic susceptibility. Aluminum bronzes with up to 2% silicon and 6% aluminum are known as aluminum-silicon bronzes, and are stronger as well as easier to hot work and cast.
Manganese-aluminum bronzes. These metals have 13% manganese with 8-9% aluminum. Developed originally for propellers, these metals are good for casting and welding, as well as cavitation and impingement resistance. Their drawback is that they aren’t as strong as other aluminum bronzes.
Aluminum Bronze Uses
Thanks to its strength, non-sparking traits, and resistance to corrosion and magnetic force, aluminum bronze has become popular in the marine, water, chemical, electrical, and industrial markets. The material has become a popular choice in situations where other metals would be more expensive or wear faster, such as in welding and paper machine parts, tools, gears and worm wheels, dies, and non-magnetic marine chain and anchors. Chemical plants, oil refineries, and desalinization plants use alloys with less than 8% aluminum for pressure vessels and heat exchangers, while the strongest materials with 10% or more aluminum, or that include nickel, are cast into products like ship propellers or turbine compressor blades. The material is also a common choice for power generation, aircraft, automotive, construction, and manufacturing of iron, steel, and electrical products.
Conclusion
Now that we’ve summarized the nature, properties, and applications of aluminum bronze, we hope you will be able to source and work with this metal with greater familiarity. Aluminum bronze is only one of several types of bronze, including phosphor, manganese, and bismuth bronze. To learn more about the different types of bronzes and their applications, you can find out more in our bronze buying guide. Or, if you’re ready to procure aluminum bronze, you can search Thomas’ database of North American companies, which includes information on over 150 aluminum bronze suppliers.
XTJ is a leading OEM Manufacturer that is dedicated to providing one-stop manufacturing solutions from prototype to production. We are proud to be an ISO 9001 certified system quality management company and we are determined to create value in every customer relationship. We do that through collaboration, innovation, process improvements, and exceptional workmanship.