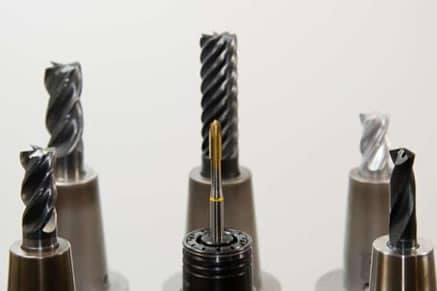
Table of Contents
What is Thread Milling?
Thread milling is a metalworking process to cut threads at different sizes through the circular ramping movement of a rotating tool, the thread pitch is created by the lateral movement in one revolution. Different from tapping, thread milling is primarily applied to large workpieces. However, solid carbide thread mills can also produce small threaded holes. The same machine can be used for both left and right-hand threads, different thread tolerance, various materials, and hole diameters, producing threads with high accuracy and great surface finish. Although not as widely used as thread turning, thread milling can achieve high productivity in some applications.
Advantages of Thread Milling
– Thread milling can cut threads on materials that are difficult to machine.
– It’s a safe machining operation and easier to do on the machine tool.
– The process can reduce machining time and save energy.
– The tool is flexible, either right or left-handed threads can be produced with the same tooling.
– The thread milling allows for maximum threads in a very short distance in the machining of very shallow blind threads in thin materials.
– It can achieve high thread quality and without burrs.
– Less wear on the machine spindle.
– Available on a lathe with live tools.
– Correct thread diameter right away.
– Using a tool smaller than the threads to ensure the thread be properly machined with the clearance needed to evacuate the chip.
– It’s necessary to have a hole right in size.
Thread Milling Tools
Thread milling cutters are tools designed to cut threads by milling. Varying thread milling tool or cutters enables the production of threads from internal to external, medium to large sizes. The thread mills can be used on CNC machining centers that have simultaneous, triaxle control, and helical interpolation functions. Thread milling using either solid carbide thread mills or steel holders with indexable inserts.
Solid carbide thread mill: useful for smaller hole sizes, more expensive than indexable tools, but can be cost-effective depending on the quality needed.
Indexable insert thread mill: not fit in holes that are 0.625 inches or less in diameter. Once the thread mill body is ready, the cost to produce threads is only in changing inserts.
How Does a Thread Mill Work?
The thread milling process can use helical-interpolation tool paths to replace tapping and the thread mill looks similar to taps, but the effect is different. Insert the thread mill into the hole along axis of the spindle, until deep enough to produce desired full thread depth, the controller moves the thread mill to the position of hole diameter and cut threads into the hole sidewall, then moves in a 360°circle, it returns to start position. When the thread mill does the circular motion, it needs to move towards the top of hole or move one thread pitch along the Z-axis of machines, for producing a thread. The depth of thread is usually no more than one and a half times the diameter of the hole, to minimize the deflection.
When to Use Thread Milling – Thread Milling Applications
Thread milling is a right machining process in the following applications or requirements:
– Thin-walled parts
– Asymmetric/non-rotating components
– Machining materials generate high cutting force and easy to cause chip evacuation problems
– Requiring to reduce tool inventory
– Unstable component setups
– As an alternative to tapping
– Adjust the tolerance of the thread
– Cut numerous odd thread sizes with a single tool
– Back chamfer the hole
Thread Milling vs Tapping – What’s the Difference Between Thread Milling and Tapping
Compared with tapping, which process should you choose?
– Tapping is usually used to make threads in small holes after drilling, while thread milling tends to produce threads in larger holes.
– Tapping uses a tool of the same size as the thread, forcing the chip through the thread to evacuate, while thread milling uses a tool with a smaller size than the thread, so thread milling achieves a better thread quality than tapping.
– Tapping can be performed either by hand or machine. Thread milling usually requires CNC machine tools with at least three axes for helical interpolation.
– Thread milling requires lower cutting forces than tapping.
– It is not necessary to have the correct hole size in the thread milling process, a single tool can be used in thread milling to make a wide range of hole sizes. While for tapping, a different size tap is required for each size hole that needs to be threaded.
– Thread milling produces pipe threads easily without creating the troublesome stringy chips produced in the tapping process.
– Thread milling can achieve a better thread quality and smoother surface than tapping
– Thread milling gives the user the ability to design custom threads, while the custom taps can be very expensive and require long lead times.
– Tapping does not allow for adjusting the thread fit. Once the hole is tapped, the size and position of the thread are fixed. While the thread milling can control the fit. The machine operator has the ability to adjust thread size using a strategy similar to using an end mill, rather than a drill bit to make a hole.
Thread Milling Guide & Tips
1. Choose a proper quality tool
High-quality and suitable thread milling tool is essential to avoid failure and problems during the process, you can select some qualified tooling manufacturers and compare their advantages and disadvantages, and choose the one closest to your request. Before that, you need to master the types of thread mills (Helical flute thread mills, Straight flute thread mills, Single profile thread mills, Indexable insert thread mills, Solid carbide thread mills, etc.) and specifications of those thread milling cutters (Single form, Tri-form, and Multi-form), like diameters.
2. Apply several radial passes
Separate the thread milling operation into several radial passes can achieve higher quality, improve the thread tolerance, ensure safety and avoid tool breakage in difficult-to-machine materials, as well as make it suit in difficult applications, like long overhangs and unstable conditions.
3. Opt for chip breakage and removal strategy
Apply proper tool or strategy to break and evacuate chips timely, cutting fluid and lubricant can be considered, avoid chip recutting, save time and guarantee the tolerance of thread.
4. Determine tool path
Left or right-hand threads are depending on the selected tool path. Which one is more suitable for you? Choose the more efficient one according to your experience.
5. Depth of the thread
– Generally, the depth of the thread should be no more than one and a half times the diameter of the hole. Because the longer the milling tool, the more chance it can experience deflection, which can create inaccuracies in the thread.
XTJ is a leading OEM Manufacturer that is dedicated to providing one-stop manufacturing solutions  from prototype to production. We are proud to be an ISO 9001 certified system quality management company and we are determined to create value in every customer relationship. We do that through collaboration, innovation, process improvements, and exceptional workmanship.