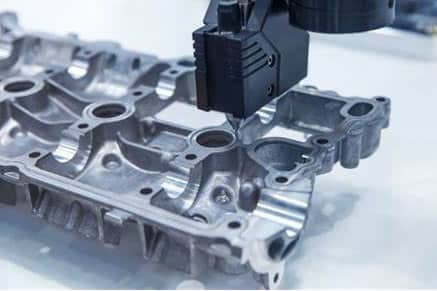
Precision molding is the latest technology in the world of plastic injection molding. Precision molding is a type of plastics molding that is the most expensive and sophisticated process of mold design in the market.
precision molding
precision mold
The process of precision molding is never used in the development of the entire product by the plastic injection molding companies. It is only used in the manufacturing process in small and infrequent occasions when product development calls for an unusually precise form of plastic injection molding.
Table of Contents
About Precision Molding
As mentioned above, precision injection molding is a highly technical process and requires the use of precision molds and precision machines. The process of precision molding differs from conventional injection molding techniques. The process is required for the development of precise plastic parts with complex geometries that can replace high precision metal parts for various industrial applications.
Download Application Bodybuilding Without Material – Torrent parabolan bodybuilding room in bondoufle, bodybuilding room – (essonne).
The precision of a part is largely dependent on the precision injection mold and its suitability to meet the design engineering requirements.
XTJ is a leading OEM Manufacturer that is dedicated to providing one-stop manufacturing solutions  from prototype to production. We are proud to be an ISO 9001 certified system quality management company and we are determined to create value in every customer relationship. We do that through collaboration, innovation, process improvements, and exceptional workmanship.
Precision Injection Mold
The precision of the mold is a result of various factors including:
Precision of the mold cavity size
Accurate position of the cavity
Precision of parting surface
Choice of materials
Dimensional tolerance of general precision moulds
Number of cavities in the mold design
The thickness of the bottom plate, supporting plate and cavity wall
Runner size
The material of precision mould (preferably steel aloys with high mechanical strength)
Design engineering
How Does Precision Molding Work?
The process of molding plastic by CNC machining into an exceptional price and calculated shapes is known as polymer optics.
As the technology grows in precision and sophistication, the world needs more and more sophisticated processes for industries served to mold plastic into specific shapes that are used in specialized industries such as automotive, pharmaceutical, medical devices, information technology, and other industries served.
Following are some additional pointers about precision molding by molding consultants:
This process is advantageous because it is economically more viable.
The process is also a new and far enhanced solution to the optic issues that occur in the contract manufacturing of technical products and scientific molding.
The custom injection molding process is not the appropriate method of developing optical parts that are needed in various high precision products. The precision injection moulding process allows the producer to customize the process to meet the needs of the molding product.
The resulting research and development lead to Precision Injection Molding (PIM) technology that will allow the development of plastic equipment by the mold manufacturer at reasonable prices but with very high-quality control and precision.
The polymer optic in the precision injection moulding is the key to developing a highprecision molds and gives the development process of plastics injection various unique edges.
They are ideal for large production of products at a low cost by the molding company. Before PIM, these products had to be developed manually by molding experts and molding consultants. Now, these products are developed on a large scale and are highly precise.
Integrated optical and mechanical functionality is a unique feature of the product that gives it precedence over the other custom injection molding processes.
Low weight designing is the main feature of the custom injection product. A low weight optical polymer has half the density of glass and it allows for the development of low weight designing. A low weight optical polymer will stay from 5-30 euros per kg and is much cheaper than its alternative.
The process does not require any additional steps and will always complete in one straightforward step. It means that the product is developed in lesser time and more accurately through contract manufacturing.
XTJ is a leading OEM Manufacturer that is dedicated to providing one-stop manufacturing solutions  from prototype to production. We are proud to be an ISO 9001 certified system quality management company and we are determined to create value in every customer relationship. We do that through collaboration, innovation, process improvements, and exceptional workmanship.
The cycle time of the process is lower than its counterparts. Thus the process becomes more suitable for mass production of molding materials.
The process also allows for production in any design or shape in the injection molder without any extra charges or costs.
Glass optics and precision optics through polymer are sometimes combined to enhance the precision building of the product as they allow for the development of high image quality control within reasonable costs.
Automation Potential
The process is highly celebrated for its potential for automation processes. The entire process is automated and is conducted through computers in every aspect through automation handling systems. The advanced process allows for fluid and customizable manufacturing cells.
The process of precision mold & design engineering is conducted through cells that can also perform plastic injection molding, coating, testing and even packaging through the computer programing.
The mechanical functionality of the process is highly customizable where mechanical mounts such as lens mounts, snappers, and various other fixtures can be easily installed or removed as required.
Surface Specifications
There are certain limitations to the utility of precision molding because of the manufacturing technology.
The polymer optical components allow for a diameter of the lens from 1mm to 100 mm and the lens thickness has to remain between 1 to 30 mm. The diameter to thickness ratio will remain between 1:1 to 5:1.
Tips and Tricks:
If you are opting for the precision molding process as a way to develop your product, then there are a few facts you should thoroughly understand and keep in mind.
Areas of Precision:
1. Tolerance Issues:
As stated earlier, precision molding is not done on the entire structure of the product but only the parts where scientific molding is required.
Precision molding is used when a product requires tight tolerance. Tight tolerance means that the requirements of the product have to be followed precisely and accurately otherwise the product may break in the injection molder.
If a part of the machinery breaks while the CNC machining is still moving then it could be dangerous. The parts that are the focus of this kind of pressure are developed through precision scientific molding.
These tolerances are, alternatively, achieved through injection molding, but precision custom injection molding is a better solution when developing these products.
Precision molding will only be applied to the parts that are connected with other parts so that they are fixed in the correct form. This means that you need to make sure that you understand the precision requirements of the product or you will end up wasting money on the wrong segment.
The development of the entire product in an injection molder through precision molding is too expensive and will be a waste of money in another sense. The best solution is to enquire which parts of the product require precision molding and then conduct precision molding accordingly.
Usually, the product is developed through insert molding and upon complete development of the product, the parts that require precision molding are molded accordingly.
The required tolerance is achieved through precision molding.
2. Materials:
The molding materials that is used for precision moulding is different from other materials.
The process of precision molding can cause shrinkage in the plastic. If the molding materials have a high shrinkage capacity than the material will shrink while undergoing the process and the entire product will be ruined.
A common plastic polymer, polyethylene, has a high shrinkage range of +/- .014″ to +/- .022. This is a commonly used polymer in plastic product manufacturing.
In precision molding, using this plastic resin will certainly affect the quality control of the developed product. A decent replacement for polyethylene is Acrylonitrile Butadiene Styrene (ABS).
plastic injection molding
ABS is a thermoplastic polymer, which means it is can retain its elasticity through high temperatures. It has a reduced shrinkage of =/-.006. It is still considered not appropriate for precision molding, which usually requires a shrinkage of +/-002.
This shrinkage capacity is usually achieved through the addition of glass or another resin that is mixed with the plastic. The external material keeps the plastic in its place and absorbs the excessive heat, thereby reducing shrinkage.
It should be noted that the induction of this material into the product does not ensure that the product will not shrink. The resulting product will shrink in parallel to the induced resin.
Now that the product has more structure, shrinkage can be taken into account and a product development plan can be developed that will keep the product straight.
3. Technique:
The process of precision molding requires that every piece of the product is developed identically and will be attached in an identical manner.
If a product is not identical to the mold design then the precision product will also not be accurate. A precise mold is the only way to ensure that there is no change in the design in any way.
When you are in need of a precision-molded product, make sure that the manufacturer understands this aspect of development.
Precision molding is a slow and steady process that requires time and focus. Do not choose injection molding companies who specializes in rapid tooling, as they are not too familiar with the precision molding process. The rapid tooling process finishes the mold design quickly.
This is the main idea of precision tooling and we hope to have covered all the basics.
There is not much information on the process available online so we decided to present the process through our experience.
If you ever require a precision modeling process for your products, it is best to truly understand the mechanics of the process as best as you can.
If the manufacturer can see that you know what you are talking about, they will be more motivated to deliver the product that you asked for.
Selecting Precision machines
Precision molding machines should preferably be high pressure. This helps improve the quality and the overall precision of the plastic parts.
An injection pressure of around 392 MPa reduces the shrinkage factor to zero. Additionally, the mechanical strength of the part increases significantly when the injection pressure is kept around 392MPa.
Further, the efficiency of the injection rate improves when maximum injection pressure is increased.
precision molding
Following are the main structural features of precision molding machines:
Stiffness of clamping system- the moving and fixed templates are controlled in between 0.05 to 0.08mm
Dimensional tolerance of parts
Die speed (open and closed)
Plasticizing parts- these include the screw, the screw head, material barrel, the check ring, etc.
Additionally, precision moulding machines should be able to manage the repeatability and accuracy of a product.
Other Important Considerations
When planning to create a precision molded product, it is important to consider the following key criteria:
Selecting the areas within a mold that require precision
As mentioned earlier in the article, precision molding is way more sophisticated and expensive than conventional plastics molding. This is the reason why it is important to understand the different aspects of your custom plastic parts and determine the ones requiring high tolerances.
It is also important to understand whether those tolerances can be managed through conventional injection moulding techniques. A plastic part may be created using both- conventional plastic injection molding process as well as precision moulding. An electronic part, may, for example, require precision works only for a small section of the piece and not the entire part.
Hence, understanding and determining the precision requirements will ensure a cost-effective solution that will meet your needs. Additionally, it will also help ensure that your parts are prepared with high quality and meet the production deadlines.
Selecting the right plastic material
Selecting the right plastic resins is an important factor for creating the right precision molded parts. The selection of material is one of the biggest determining factors in determining whether the plastic molded products will come out as desired.
Within the plastic material, shrinkage range is one of the most important criteria for creating parts with high precision. Narrow shrinkage ranges offer better chances of reaching tight tolerances.
Again, the requirement of shrinkage depends on the product being created. While a wider range of shrinkage is not preferable since it makes it hard to hit the right tolerance levels, it can still be used to create products that do not need to be of an exact size.
Polypropylene has a wider shrinkage range of +/- .014″ to +/- .022″. Acrylonitrile butadiene styrene (ABS) on the other hand has a narrower range but is still not in the category that fits the need for precision molding.
Usually, the shrinkage ranges required for molding a precision part is around +/- .001″ or +/- .002″
Choosing a plastic resin that offers low shrinkage is hence an easy way to get your materials right for precision moulding.
However, this may not always be a cost-effective option due to the high cost of the desired resins.
Various molders hence prefer to reach the high tolerance level by adding filler materials to the plastic resins. These include glass fibers, mica and other filler materials. The addition of fillers narrows down the shrinkage range and hence provides a better structure to the parts.
Selecting the best mold manufacturer
Choosing the right precision molding company is another important factor in creating quality molded products. The key requirements for creating precision molded plastic parts that have tight tolerances and are produced as exact replicas of each other is to have high precision molds and tools.
plastic injection molding
It is hence important to select a precision molding manufacturer who specializes in high precision tooling with a thorough understanding of the process. The availability of technology to create precise molds that produce identical parts is a very important criterion for manufacturing precision molded products.
Applications of Precision Molding
Precision moulding is used in the development of a wide variety of products as stated earlier. But the technology truly revolutionized the development of lenses in various applications as it allowed for the contract manufacturing of glass free lenses that were cheaper and much stronger.
XTJ is a leading OEM Manufacturer that is dedicated to providing one-stop manufacturing solutions  from prototype to production. We are proud to be an ISO 9001 certified system quality management company and we are determined to create value in every customer relationship. We do that through collaboration, innovation, process improvements, and exceptional workmanship.