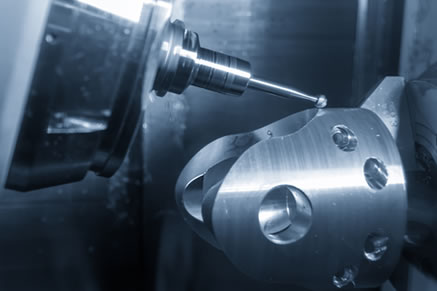
When it comes to machining lightweight metals, two popular options come to mind: titanium and aluminum. Both of these metals are widely used in a variety of industries due to their strength-to-weight ratio, corrosion resistance, and manufacturing capabilities.
Engineers may have questions about these materials in relation to their applications, such as “Is titanium lighter than aluminum?” or “Is titanium stronger than aluminum?” In order to help you decide which metal is best for your next machining project, here’s an overview of the advantages and disadvantages of both materials.
Overview of Machining Titanium vs. Aluminum
CNC Machining has become an essential process in the fabrication and production of components ranging from screws and bolts to medical implants and more. Titanium and aluminum are two popular materials that are commonly used due to their unique properties relative to other metals.
XTJ is a leading OEM Manufacturer that is dedicated to providing one-stop manufacturing solutions of Machining 6061 Aluminum from prototype to production. We are proud to be an ISO 9001 certified system quality management company and we are determined to create value in every customer relationship. We do that through collaboration, innovation, process improvements, and exceptional workmanship.lication: Automotive industry, Bicycle and motorcycle, Door and windows and furniture, Household appliance, Gas meter, Power tool,LED lighting, Medical instrument parts, ect.
The combination of strength and light weight of these two metals makes them attractive for projects ranging from aerospace engineering to everyday mechanical applications. When selecting between titanium or aluminum as the material of choice, it’s important to consider factors such as cost to machine, corrosion resistance, tensile strength, and thermal conductivity, among others.
Machining Titanium
CNC machining titanium implants
Titanium can be machined for a wide range of possible applications, from medical implants to aircraft components and beyond. As a durable, lightweight material with excellent corrosion resistance, titanium is ideal for use in parts that require strength and resilience.
Machining the metal properly requires an understanding of the best techniques for cutting and forming titanium components, as it is more challenging than working with other metals due to its extreme hardness. A skilled machinist can employ specialist tools and gear to effectively craft titanium parts for any application with precision and accuracy. Thanks to new technologies, machining titanium has never been easier or more efficient.
Advantages
Titanium is renowned for its high strength-to-weight ratio, making it ideal for engineering applications such as aerospace components. Further, titanium has a superior corrosion resistance property that makes it desirable in marine environments or even industrial settings with exposure to harsh chemicals. Additionally, titanium has a wide range of uses in various industries, including automotive manufacturing, medical equipment production, chemical engineering, and more.
Disadvantages
The biggest disadvantage associated with titanium is its cost factor–it’s usually much more expensive than aluminum or other metals on the market today. Furthermore, the difficulty involved in manufacturing titanium components means that it can be time-consuming and difficult to achieve desired results.
Machining Aluminum
CNC machine drilling aluminum block
Aluminum is one of the most versatile materials in machining applications due to its low density and strength-to-weight ratio. As a result, aluminum is widely used for metalworking projects ranging from constructing complex machinery to producing aesthetic components like those used in electronics and architectural designs.
Its malleability makes it easier to cut into shapes or carve, while its relatively lower temperatures required to process the material make it ideal for modifying components quickly with minimal waste. Additionally, aluminum’s corrosion-resistant properties make it desirable for many industries, making it an outstanding choice for machining applications.
Advantages
Unlike titanium, aluminum offers a significantly lower price point which makes it a popular choice among engineers who want to stick within budget constraints. Plus, there are a wide variety of heat-treating capabilities available with aluminum which allows manufacturers to fine-tune the metal’s ductility, hardness, or other mechanical properties based on their specific needs.
Disadvantages
While durable and lightweight compared to steel or other heavy metals commonly used in machining projects, aluminum lacks the strength-to-weight ratio offered by titanium–meaning that while cheaper than titanium, products may not offer the same longevity over time, depending on the application.
Which is Better for my Project?
Engineer working on cad
Determining which type of metal is the most suitable for a machining project requires a bit of research. Consideration must be given to the working environment, the complexity of the project, and the desired characteristics upon completion. Titanium projects tend to require specialized equipment and tooling due to its relative hardness. If a project requires intricate details with exceptional precision, titanium may be ideal due to its robust strength.
Ultimately, each case needs to be carefully considered by taking into account multiple factors. It’s important to weigh the capabilities and disadvantages before deciding on either titanium or aluminum for your machining project.
XTJ is a leading OEM Manufacturer that is dedicated to providing one-stop manufacturing solutions of Machining 6061 Aluminum from prototype to production. We are proud to be an ISO 9001 certified system quality management company and we are determined to create value in every customer relationship. We do that through collaboration, innovation, process improvements, and exceptional workmanship.lication: Automotive industry, Bicycle and motorcycle, Door and windows and furniture, Household appliance, Gas meter, Power tool,LED lighting, Medical instrument parts, ect.