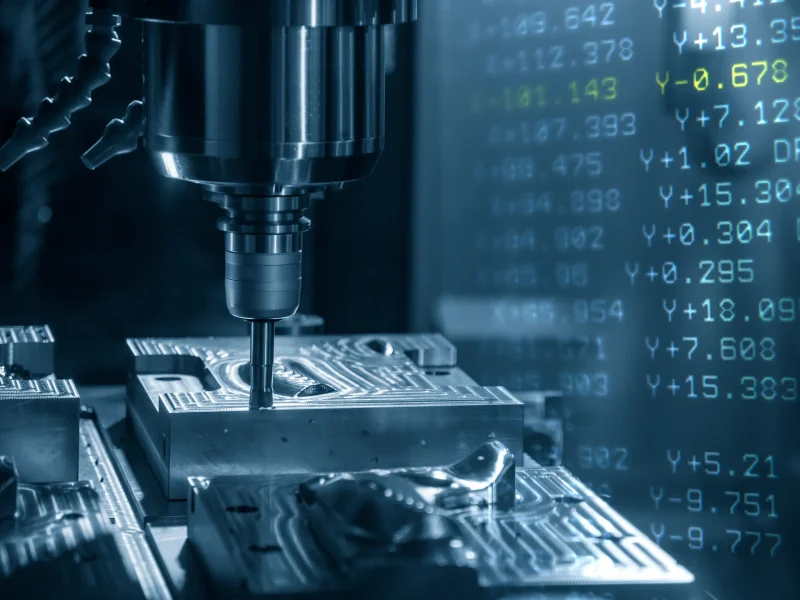
One of the most remarkable features of multiaxis CNC machining processes and tools is the consistent addition of axes. This essentially describes the developing aspect of this manufacturing method. Over the last few decades, multiaxis CNC machines have consistently developed, expanding the reach of manufacture and industry, and created new possibilities and usages for machining processes. From a technical standpoint, the principles of multiaxis machining are a marvel of modern engineering, and enabling more possible axes has quickly become a defined objective.
With the advent of the 7 axis CNC machine, multiaxis machining had seemingly attained the optimum of this technical capability. In terms of geometries, this multiaxis configuration can seemingly produce any complex shape. Yet, complexity and precision are one of the hallmarks of most multiaxis machining configurations, the defining feature of 7 axis CNC machines is the speed, repeatability consistency of its output, coupled with accuracy and convenience. This is what makes 7 axis CNC machines, as well as most configurations with a high number of axes, optimal for high volume usage and mass productions.
Table of Contents
What Is 7 Axis CNC Machining
A simple definition is a CNC machine that can operate over 7 axes (3 translational axes for the movement of the cutting tool, 3 rotary axes holding the workpiece, and an additional axis enabling the rotation of the arm holding the tool head). This configuration relates to a wider paradigm of multiaxis that was built upon. 7 axis CNC machines can essentially perform all the tasks of their predecessor configurations with more precision in less time and have additional improved capabilities.
The number of axes in each configuration refers to the number of vectors along, which the machine can either turn the spindle or remove material (milling). Likewise, 7 axis CNC machining defines two slightly different configurations, which can both attain the same effect. There are CNC machining centers, which can use either a 5 axis or a 6 axis milling machine but adapt their process for 7 axis capabilities, and then there are CNC machines with built-in 7 axis capability, usually robots. Both configurations can perform the same tasks, with slightly different results. In general, 7 axis CNC machining is mainly improved over other configurations with the additional capabilities of its single setup, speed, and accuracy.
Types Of 7 Axis CNC Machining
There are generally two types or configurations of 7 axis CNC machines. The first type, which is possibly the most commonly adopted, is the machining center with 7 axis capabilities. This refers to a CNC machining, mostly equipped with 5 axis or 6 axis machines, adapted to perform 7 axis functions. These centers can usually use equipment made by different manufacturers and are capable of both turning and milling operations. Although this configuration can produce complex geometries with the same level of accuracy and is capable of multitasking, it differs from the robot arm 7 axis CNC machine.
The robot arm configuration in industrial usage has mostly been used for automating processes like welding and handling. However, largely due to the recent advances in technology and manufacture, the use of industrial robot arms has expanded to include CNC machining as well and has several advantages over CNC machining centers. The 7 axis robot arm is structured differently than regular multiaxis CNC machines. The axes are built in the movement capabilities of the robot arm. These industrial robot arms are usually mounted on top of a rail or a rotating to facilitate movement to different areas of large workpieces.
The difference between the machining center and the industrial robot arm lies also in the materials supported by each configuration. The 7 axis CNC machining center is compatible with hard and rigid materials like most metals, cast iron, and aluminum, whereas industrial robot arms are used for brittle materials like marble, resin or plastic.
Difference With Other Multiaxis Machines
7 axis CNC machining from other configurations is that it describes a capability in the manufacture and not necessarily a specific type of machine. As mentioned above, 7 axis CNC machining is mostly performed by machining centers, with equipment and CNC machines adapted for 7 axis capabilities. This overall method is significantly better than other configurations for some metrics. For example, accuracy and precision, especially with large or complex parts and components with tight tolerances, is one of the main advantages of 7 axis CNC centers. Although 3 axis or 5 axis CNC machines are perfectly capable of producing many complex shapes, 7 axis CNC centers can produce them at a higher rate, making them more optimal for operations with high demand.
As one of the great capabilities of modern industry, yet a costly investment, 7 axis CNC machining can produce great results, it is however mostly used for very complex pieces. 7 axis CNC centers can differ in terms of the size of workpieces. Many centers can work mostly average-sized pieces, but there are also specialized centers with more capabilities.
Compatible Materials
As with most multiaxis machining configurations, 7 axis CNC machining is compatible with many materials depending on the particular configuration. Although multiaxis machining is used for rigid materials, mostly metals or cast iron, the process can also be adapted for other brittle materials like plastic or wood. For example, CNC routers are still used with wood and some types of stone and polyurethane foam.
This is different for 7 axis CNC machining. Depending on the configuration, the process can be adapted to either be compatible exclusively either with hard or brittle materials. The CNC machining center with 7 axis capability works mostly with hard materials (metals, iron, and aluminum). Unlike the 7 axis robot arm configuration, which is mainly used with brittle materials like resin, plastic, wood, or polyurethane foam.
Applications Of 7 Axis CNC Machining
With the increased capabilities, 7 axis CNC machining is now widely used in a variety of industries with a high demand for complex and solid pieces with tight tolerances. For example, in the automotive industry, many of the required parts and components can be produced either with the help of a 5 axis or 6-axis CNC machine. However, specialized CNC machining centers with 7 axis capabilities are now increasingly more relied upon, as they can produce at a higher volume. Industrial robot arms with 7 axis capabilities can create a full prototype of automobiles, in exceptional time.
The aerospace industry is also reliant on 7 axis CNC machining. As aircraft require many large or complex parts, 7 axis CNC centers can produce pieces with the required parameters. Specialized 7 axis CNC machining centers can even produce components of exceptionally large size, like airplane wings and jet engines, with high efficiency.
Advantages And Limitations
In terms of output, both configurations of 7 axis CNC machining (CNC centers and industrial robot arms) are highly capable of efficiently producing very complex geometries, which is its main advantage over other multiaxis configurations. The speed and compatibility with a cutting tool or other tool head parameters is another remarkable feature of 7 axis CNC machining, as well as the single setup it provides. Most CNC machining centers with 7 axis capabilities are adapted to perform several tasks like turning and milling which avoids moving the object or halting the process. In addition, the very precise and measured workspace of these centers ensures better precision over several stocks of manufactured pieces.
As with most multiaxis CNC machines, the only limitation is the cost. 7-axis CNC machining is different in the sense that it requires a complete structuring of the chain to function properly. Inherently, it consists mostly of re-adapting the CNC machines to perform with 7 axis capabilities. This can often be a costly investment. The same is true for 7 axis industrial robot arms. The increased costs of 7 axis CNC are also related to the skill level required to properly operate a 7 axis CNC center.
Conclusion
As of today, 7 axis CNC machining is still one of the latest developments in industry and manufacturing. The potential of this method is still currently developing. This paradigm of multiaxis machining has indeed been one of the most impactful breakthroughs in manufacture, and with the constantly developing features and capabilities, the output of manufacturers will significantly improve, as well the quality standards and reliability of most appliances and technical equipment.
7 axis CNC machining is by far one of the most advanced configurations of multiaxis machining. It is seemingly capable of achieving in sort of complex geometry with precise measurements in a short time with high efficiency. Although it is a very costly piece of technology, and for many manufacturing operations, it remains largely inaccessible; it’s very likely for this change, as the technology itself develops in the future.