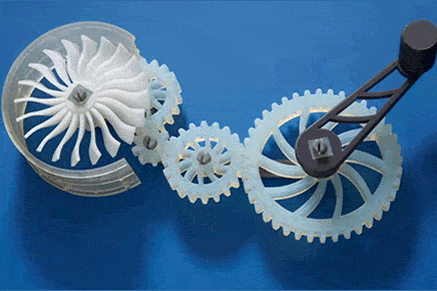
The most common FDM 3D printing materials are ABS, PLA, and their various blends. More advanced FDM printers can also print with other specialized materials that offer properties like higher heat resistance, impact resistance, chemical resistance, and rigidity.
MATERIAL | FEATURES | APPLICATIONS |
---|---|---|
ABS (acrylonitrile butadiene styrene) | Tough and durable Heat and impact resistant Requires a heated bed to print Requires ventilation |
Functional prototypes |
PLA (polylactic acid) | The easiest FDM materials to print Rigid, strong, but brittle Less resistant to heat and chemicals Biodegradable Odorless |
Concept models Looks-like prototypes |
PETG (polyethylene terephthalate glycol) | Compatible with lower printing temperatures for faster production Humidity and chemical resistant High transparency Can be food safe |
Waterproof applications Snap-fit components |
Nylon | Strong, durable, and lightweight Tough and partially flexible Heat and impact resistant Very complex to print on FDM |
Functional prototypes Wear resistant parts |
TPU (thermoplastic polyurethane) | Flexible and stretchable Impact resistant Excellent vibration dampening |
Flexible prototypes |
PVA (polyvinyl alcohol) | Soluble support material Dissolves in water |
Support material |
HIPS (high impact polystyrene) | Soluble support material most commonly used with ABS Dissolves in chemical limonene |
Support material |
Composites (carbon fiber, kevlar, fiberglass) | Rigid, strong, or extremely tough Compatibility limited to some expensive industrial FDM 3D printers |
Functional prototypes Jigs, fixtures, and tooling |
Table of Contents
Filament types
PLA
The most widespread 3D-printing material, polylactic acid (PLA), is a biodegradable plastic made from renewable sources like corn starch. PLA has many benefits, such as a low melting point ideal for lightweight and consumer use. It’s also strong, doesn’t expand as much as other materials when heated, and has good adhesion to other materials.
It’s such a versatile manufacturing material that you might not realize there’s PLA all throughout your home and workplace in disposable cutlery, appliance and electronics parts, “scrunchable” plastic like food packaging, fishing line, diapers, feminine hygiene products, and more.
ABS
Acrylonitrile butadiene styrene (ABS) is suited to applications that need strength alongside flexibility—think Lego bricks. It’s durable, cheap, lightweight, and extrudes through a 3D printhead easily.
Because it’s as tough and rigid as it is cheap, ABS has better impact resistance and shock absorption than many polymers, which makes it great for products like bike helmets and golf-club heads.
It can also be so it suits slightly more outlandish shapes—think of musical instruments with complex inner structures, like clarinets or oboes; car bumper bars; and binoculars.
PETG
As the name suggests, this plastic is related to the polyethylene terephthalate of water and soda bottles but modified with glycol, hence the added “G.” It has high strength and flexibility, and when compared to the more widely used PLA, it has good temperature resistance.
PETG is ideally suited to applications that need to be sturdy and smooth and aren’t prone to excessive shrinkage. It has great adhesive properties, but because it’s “stickier” than most, clumping at the extruder nozzle can cause more problems than other polymers.
And because it can be sterilized, it’s considered the perfect plastic for food packaging.
Resin types
Although there are many types, resin 3D printing refers to any process where liquid from a small tank is sent to the extruder to be heated or cured to dry, also called “vat polymerization.” Liquid resin is a photopolymer, which means it reacts/solidifies when exposed to light, and there are a couple of varieties.
Clear
Clear resins are used for small objects needing highly detailed surfaces or finishes. Colorless, see-through, light, smooth, and water resistant, they’re perfect for products that will be sanded or painted in post processing.
Water washable
Most resin 3D-printed parts need some sort of clean-up to remove errant edges or excess deposits, a process usually done with alcohol solutions. Washable resins don’t need such chemical treatments—you can post-process them with water for a smooth finish.
Flexible
Used when your final product needs to come back to its original shape after bending or compression, these rubbery resins are perfect for prototypes of handles, shock absorbers, or parts that need to withstand sustained twisting or flexing.
Resin methods
Resins are best suited to aesthetic parts and nonfunctional prototypes, and there are three major types of photopolymerization that create them.
Stereolithography
Mirrors are used to direct one or several laser beams across the resin as it’s laid down on the bed of the printer, curing the object as each new layer is applied.
Digital light processing (DLP)
A flash of light cures or sets an entire layer in one go, directed to the build surface by a network of tiny mirrors.
Masked Stereolithography (MSLA)
Just like in stereolithography, except that a light source shines through an LCD screen that contains a mask of the single layer so the light can cure only that layer in each step.