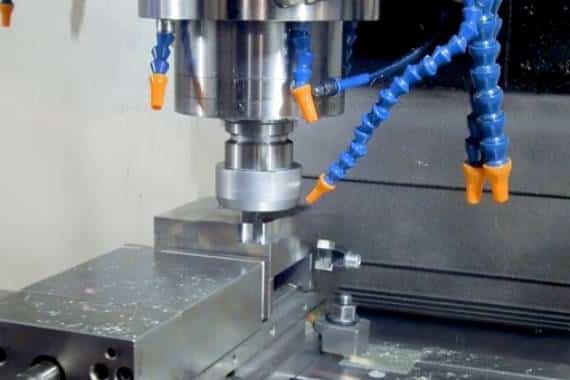
CNC machining, however, offers a reliable way to fabricate acrylic parts safely, with a high degree of accuracy and minimal waste of acrylic material. CNC machining results in very few errors, making it possible to create high-quality acrylic parts and prototypes such as headlamps, casings, jewelry, and more.
crylic (PMMA) is a highly desirable material due to its strength, toughness, and transparency. But relying on conventional machining processes to cut acrylic can be a complicated procedure: the material is highly fragile and any excess force can cause unwanted breakages.
Acrylic, with its excellent clarity and adaptability, poses an interesting material for CNC machining. Known scientifically as polymethyl methacrylate (PMMA), acrylic offers a unique combination of properties that make it both appealing and challenging to machine.
Its susceptibility to heat and proneness to scratches necessitate a meticulous approach to machining, yet its plasticity and resilience allow for a wide range of applications, from intricate models to durable components.
Material Properties of Acrylic (PMMA) for CNC Machining
Now that we know the advantages of Acrylic for CNC machining operations and projects, let’s get into more specific data on its material, physical and chemical properties:
Density: 1.18 g/cm³ – This influences the weight of the finished product and affects machining parameters like feed rate and speed.
Tensile Strength: 70 MPa (10,153 psi) – A measure of the maximum stress acrylic can withstand while being stretched or pulled before breaking.
Flexural Strength: 115 MPa (16,687 psi) – Indicates the amount of bending stress acrylic can endure without deformation.
Compressive Strength: Around 90 MPa (13,053 psi) – The capacity of acrylic to resist squeezing forces.
Modulus of Elasticity: 3,000 MPa (435,113 psi) – This elastic modulus indicates the stiffness of acrylic, impacting its flexibility under load.
Impact Resistance: Notched Izod impact test results are around 0.35-0.40 KJ/m² – Reflects acrylic’s ability to withstand sudden impacts, crucial for applications where durability is a concern.
Thermal Expansion Coefficient: 50-60 x 10⁻⁶ K⁻¹ – Acrylic expands with temperature increases, a vital consideration for parts intended for environments with temperature fluctuations.
Heat Deflection Temperature: 95°C (203°F) at 0.46 MPa (66.4 psi) – The temperature at which acrylic deforms under a specific load, important for applications near heat sources.
Light Transmission: Up to 92% for clear acrylic – Essential for applications requiring optical clarity.
Refractive Index: Approximately 1.49 – Influences the passage of light through acrylic, significant for optical and lens applications.
Water Absorption Rate: 0.3% – Acrylic can absorb minimal moisture, affecting its dimensions and properties in humid conditions.
Chemical Resistance: Acrylic is resistant to dilute acids and alkalis but can be damaged by strong solvents and cleaners – Knowledge of chemical resistance ensures the longevity of acrylic parts in various environments.
UV Resistance: Acrylic inherently resists UV light degradation, making it suitable for outdoor use without significant yellowing or weakening over time.
Hardness: Rockwell M scale 95 – Determines the surface wear and scratch resistance of acrylic materials.
Understanding these properties of acrylic is crucial for CNC machining, as they directly affect the choice of cutting tools, machining parameters, and the suitability of acrylic for specific applications.
Table of Contents
What are the steps to CNC machining Acrylic?
CNC machining acrylic is a process that transforms a simple acrylic sheet into a complex, precision part or product.
The CNC (Computer Numerical Control) machining process for acrylic involves several key steps, each important to achieving the desired outcome with the highest quality.
Here’s an overview of the stages involved:
Design and CAD Modeling: Initially, the concept is visualized and then designed using CAD (Computer-Aided Design) software. This digital model is the blueprint for the machining process.
Selecting the Acrylic Material: There’s a choice between cast and extruded acrylic, each with unique properties that affect the machining process and the final product.
Preparing the CNC Machine: This involves setting up the machine, including calibration and ensuring all components are functioning correctly.
Tool Selection: Selecting the right cutting tools is crucial to prevent damage to the acrylic and achieve a high-quality finish.
Securing the Acrylic: The material must be clamped securely to prevent movement during machining, which could lead to inaccuracies.
Setting Machining Parameters: Parameters such as spindle speed, feed rate, and depth of cut must be adjusted specifically for acrylic to ensure optimal machining conditions.
CAM Programming: The CAD model is translated into G-code, the machine language that controls the CNC machine’s movements.
Running a Test Cut (Optional): A preliminary test cut can help identify any potential issues before the final machining process begins.
Machining the Part: The machine follows the programmed path to cut the acrylic material into the desired shape and size.
What are the different CNC machining operations suitable for acrylic?
CNC machining operations tailored for acrylic leverage the material’s unique properties, such as its clarity, UV stability, and impact resistance. These operations are designed to maximize the potential of acrylic in various applications, ensuring that the end products meet the required precision and quality standards.
Acrylic’s versatility makes it an ideal candidate for a range of CNC machining processes, each chosen based on the specific needs of the project.
CNC Milling Acrylic
CNC milling is a highly adaptable operation suitable for acrylic machining, capable of producing intricate details and smooth finishes. This process involves the removal of acrylic material using a rotating cutting tool, allowing for the creation of complex three-dimensional shapes.
Technical Suitability for Acrylic: The non-contact nature of CNC milling minimizes the risk of cracking or melting the acrylic, which could occur with less precise machining methods. The control over the milling machine’s speed, feed rate, and depth of cut allows for adjustments to be made specifically for the acrylic’s properties, ensuring a high-quality surface finish and reducing the need for post-processing.
Applications: From prototype development to the production of finished parts, CNC milling serves a wide range of applications in industries such as automotive, aerospace, and medical devices. This versatility is particularly beneficial for creating components with tight tolerances or intricate designs, such as lenses for car lights, transparent covers for medical devices, and decorative items.
CNC Turning Acrylic
CNC turning of acrylic involves the use of a lathe where the acrylic material is rotated while a cutting tool is fed into it, producing cylindrical parts with precise dimensions and a smooth finish.
Technical Suitability for Acrylic: This operation is particularly effective for acrylic due to its ability to produce rounded components with high dimensional accuracy. The controlled environment of CNC turning minimizes material stress, preserving the acrylic’s optical properties and preventing warping or distortion.
Applications: CNC turning is commonly used to manufacture acrylic parts that require symmetrical shapes, such as tubes, rods, and circular components used in lighting fixtures, architectural elements, and consumer electronics. The process ensures uniformity and consistency, essential for components that must fit together precisely in assembly.
CNC Drilling Acrylic
CNC drilling is a precise method to create holes in acrylic materials, ranging from simple, straight-through holes to more complex, angled entrances and exits.
Technical Suitability for Acrylic: The precision of CNC drilling allows for the creation of clean, burr-free holes without causing cracks or other damages to the acrylic. By adjusting drilling parameters such as speed and feed rate, it’s possible to achieve optimal results while maintaining the integrity of the acrylic material.
Applications: This operation is crucial for parts that require mounting or assembly, including displays, fixtures, and enclosures in various industries. The ability to drill holes with high precision is vital for the assembly of complex acrylic structures, ensuring that components fit perfectly without additional modifications.
CNC Engraving Acrylic
CNC engraving on acrylic offers the ability to etch detailed graphics, text, and patterns into the surface of the material, adding aesthetic or functional features to the part.
Technical Suitability for Acrylic: Engraving on acrylic with CNC technology provides unparalleled control over depth and detail, allowing for intricate designs that are not feasible with manual processes. The process is gentle enough to avoid cracking the acrylic while being powerful enough to produce clear, visible markings.
Applications: CNC engraved acrylic is widely used in signage, award plaques, and decorative panels, where precision and clarity are paramount. The technique also finds applications in industrial labeling and branding, where durability and legibility of the engraved marks are critical.
CNC Cutting Acrylic
CNC cutting provides a precise and efficient method for shaping acrylic sheets into desired dimensions and forms. This process involves using a CNC router or mill to cut through the acrylic material, following a predefined path or design.
Technical Description and Suitability: The precision of CNC cutting allows for intricate designs and sharp, clean edges on acrylic parts. The non-contact nature of the cutting tools minimizes the risk of physical stress, reducing the likelihood of cracking or chipping the material. This operation is particularly suitable for acrylic due to its ability to produce smooth surfaces that require minimal post-processing. Applications range from creating complex shapes for architectural models to detailed parts for electronic devices.
CNC Laser Cutting Acrylic
CNC laser cutting stands out for its ability to deliver high precision and detail when working with acrylic materials. It uses a focused laser beam to melt, burn, or vaporize the acrylic, allowing for intricate cuts and engravings.
Technical Description and Suitability: Laser cutting is ideal for acrylic because of its clean, flame-polished edges, which eliminate the need for additional finishing processes. The method is highly accurate, enabling the creation of complex designs without physical contact with the material, thereby preventing mechanical stress and ensuring the acrylic’s integrity. It’s widely used in signage, decorative items, and components where precision and aesthetic quality are paramount.
CNC Laser Engraving Acrylic
CNC laser engraving offers a unique capability to etch detailed designs, text, or images onto the surface of acrylic materials. Unlike cutting, engraving focuses on modifying the surface appearance rather than cutting through the material.
Technical Description and Suitability: Laser engraving on acrylic produces a frosted, white appearance in the engraved areas, offering excellent contrast against the clear material. This process is suitable for acrylic due to its precision and the ability to achieve high detail without damaging the material’s surface. Applications include branding, decorative etching, and creating tactile interfaces on acrylic components.
What are different Surface Finishes for CNC Machined Acrylic?
After CNC machining, acrylic parts can undergo various surface finishing techniques to enhance their appearance, durability, or function. This overview introduces popular finishes that add value to CNC machined acrylic components.
Flame Polishing: This finishing method involves exposing the edges of acrylic parts to a flame to melt the surface slightly, resulting in a glossy, transparent finish. Flame polishing is effective for smoothing out machined edges, improving the aesthetic appeal of the part. It’s suitable for applications where a high-gloss finish is desired, such as in retail displays or decorative items.
Buffing and Polishing: Mechanical buffing and polishing processes use abrasive compounds and soft cloths to reduce surface roughness and achieve a mirror-like finish on acrylic parts. This method is essential for applications requiring maximum optical clarity and smoothness, including lenses, covers, and high-end decorative pieces.
Sanding – Sanding is a mechanical process that removes minor imperfections and smoothens the surface of acrylic parts. This method is critical for preparing the material for further finishing processes or for achieving a specific texture.Sanding is particularly effective for acrylic because it can gradually refine the surface, allowing for control over the smoothness without removing excessive material. It’s often the first step in a multi-stage finishing process.
Vapor Polishing – Vapor polishing is a technique that uses a chemical vapor to melt the surface of the acrylic slightly, resulting in a glass-like, transparent finish. This method is highly effective for improving the optical clarity of machined edges and surfaces. Suitable for acrylic due to its ability to achieve a clear, polished surface without mechanical contact. The process is particularly beneficial for parts with complex geometries that are difficult to polish manually.
Chemical Polishing – Chemical polishing involves immersing the acrylic part in a chemical solution that selectively dissolves the surface, smoothing out imperfections. This method provides a uniform finish without the need for physical abrasion. Acrylic responds well to chemical polishing, as the process enhances its natural clarity and gloss. It’s effective for parts that cannot be exposed to the heat of mechanical polishing methods.
Bead Blasting – Bead blasting employs fine beads propelled at high velocity to gently abrade the surface of the acrylic, resulting in a uniform, textured finish. This method is gentle enough to avoid damaging the acrylic while providing a consistent matte finish that can hide fingerprints and light scratches.
Painting and Coating – Painting and coating involve applying a layer of paint or protective coating to the surface of the acrylic, offering endless color options and additional surface properties such as enhanced UV resistance or hardness. Acrylic is an excellent candidate for painting and coating, as it adheres well to various types of coatings, providing durability and customization in terms of color and finish.
Laser Engraving – Laser engraving on acrylic creates precise, detailed markings by selectively removing material with a focused laser beam, resulting in a frosted appearance on the engraved areas. Acrylic is highly suitable for laser engraving due to its ability to produce clear, high-contrast markings without affecting the material’s integrity.
Dip Coating – Dip coating involves immersing the acrylic part in a liquid coating solution, then withdrawing it at a controlled rate, leaving a thin, uniform film on the surface. Acrylic parts benefit from dip coating as it provides a smooth, even coat without brush marks or drips, enhancing the appearance and adding a layer of protection.
What are the Types of Acrylic Suitable for CNC Machining?
Not all acrylic types behave the same way. The selection of the right type of acrylic is crucial for achieving the desired outcome in terms of quality, durability, and aesthetics. Let’s explore the types of acrylic suitable for CNC machining and their distinct characteristics.
Cast Acrylic
Cast acrylic is manufactured by pouring liquid acrylic into molds, which results in a homogeneous material with excellent optical properties. It is highly regarded for its clarity, making it ideal for applications requiring transparency, such as lenses and windows. Cast acrylic is preferable for CNC machining due to its lower internal stress compared to other types. It machines cleanly, producing a smooth surface that requires minimal post-processing.
Applications: Used in signage, displays, and light fixtures, where its optical clarity and resistance to UV light and weathering are beneficial.
Extruded Acrylic
Extruded acrylic is made by continuously pushing acrylic mass through a form to create lengths of acrylic sheet. The process results in a material with tighter thickness tolerances and lower cost, but with more internal stress. While it can be more prone to cracking during machining, extruded acrylic can still be used effectively with the proper settings. It’s suitable for projects where tight tolerances are essential.
Applications: Ideal for framing, shelving, and applications where uniform thickness is critical.
Continuous Cast Acrylic
Continuous cast acrylic strikes a balance between cast and extruded acrylic, offering properties similar to cast acrylic but with the efficiency of an extruded production process. This acrylic type combines the machinability and quality of cast acrylic with the economic benefits of extrusion, making it a versatile option for a wide range of applications.
Applications: Widely used in industrial applications, including machine guards and noise barriers, where both clarity and durability are required.
Modified Acrylic
Modified acrylic includes additives that enhance certain properties, such as impact resistance or flame retardancy. These modifications expand the application range of acrylic in more demanding environments. The additives can affect the machining process, but generally, modified acrylics can be machined effectively with adjustments to account for the altered properties.
Applications: Suitable for use in environments where standard acrylic might not perform well, such as in high-impact or fire-sensitive areas.
Acrylic Composites and Laminates
Acrylic composites and laminates consist of layers of acrylic and other materials, such as metals or other plastics, to achieve specific properties not possible with pure acrylic. Machining these materials requires careful planning and tool selection to accommodate the different layers’ properties. The results can offer unique aesthetic and functional benefits.
Applications: Used in decorative panels, architectural features, and anywhere a combination of materials is needed for design or functional reasons.
Frosted and Textured Acrylic
Frosted and textured acrylic provides a distinctive finish right from the manufacturing process, eliminating the need for extensive post-processing to achieve a matte or textured surface. These acrylic types machine well, though the focus may be more on preserving the texture or finish during the machining process.
Applications: Perfect for light diffusing applications, signage, and decorative elements where a non-glossy surface is desired.
What are the Advantages of Using Acrylic for CNC Machining?
Acrylic offers distinct advantages that make it a versatile choice across a broad spectrum of industries.
Optical Clarity and UV Stability
One of the hallmark properties of acrylic is its optical clarity. With a refractive index of 1.49, it allows up to 92% of visible light to pass through, outperforming glass and other plastic materials. This level of transparency, combined with excellent UV stability, ensures that acrylic components maintain their clarity without yellowing, even with prolonged exposure to sunlight.
High Strength and Durability
Acrylic exhibits a remarkable balance of strength and durability, characteristics that are often compared favorably to glass but with greater impact resistance. This makes it an ideal candidate for applications requiring a lightweight material that does not compromise on robustness.
Ease of Machining
CNC machining acrylic is straightforward, thanks to the material’s consistency and the absence of grain, allowing for precise and intricate detailing without the risk of splintering or chipping. This ease of machining makes acrylic suitable for complex and detailed projects.
Chemical Resistance
Acrylic demonstrates strong resistance to a wide array of chemicals, making it suitable for environments where exposure to solvents and other chemicals is common. This resistance helps in preserving the integrity and appearance of machined parts over time.
Temperature Resistance
The material’s ability to withstand varying temperatures without deforming or losing clarity is another advantage. Acrylic’s temperature resistance makes it adaptable to both indoor and outdoor applications, broadening its utility.
Surface Hardness
Despite its relatively soft surface, which makes it susceptible to scratches, acrylic can be easily polished back to its original clarity and shine. This surface hardness ensures longevity and maintainability of the machined parts.
Weather Resistance
Acrylic stands up well against environmental factors, including wind, rain, and prolonged sun exposure, making it an excellent choice for outdoor applications. Its weather resistance is attributed to its UV stability and inherent material properties.
Versatility
The versatility of acrylic lies in its ability to be dyed, molded, glued, and finished to meet specific requirements. This adaptability allows for a wide range of applications, from functional parts to decorative items.
Polishable Edges
The edges of acrylic parts can be polished to achieve a high-gloss finish, enhancing the overall aesthetics of the final product. This characteristic is particularly valuable in applications where visual appeal is paramount.
Bonding Capability
Acrylic can be bonded effectively with specialized adhesives, allowing for the fabrication of complex assemblies. This bonding capability, coupled with its other advantages, makes acrylic a preferred material in many engineering and design applications.
XTJ is a leading OEM Manufacturer that is dedicated to providing one-stop manufacturing solutions of Machining 6061 Aluminum from prototype to production. We are proud to be an ISO 9001 certified system quality management company and we are determined to create value in every customer relationship. We do that through collaboration, innovation, process improvements, and exceptional workmanship.lication: Automotive industry, Bicycle and motorcycle, Door and windows and furniture, Household appliance, Gas meter, Power tool,LED lighting, Medical instrument parts, ect.