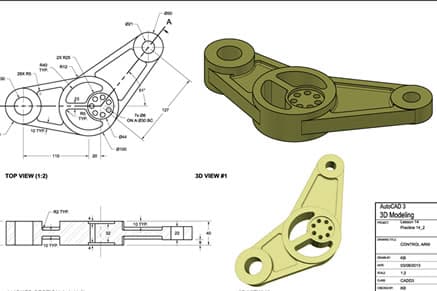
As medical technology rapidly advances, surgical robots have become integral to modern healthcare, revolutionizing surgical procedures with unparalleled accuracy and reliability. At the core of these cutting-edge mechanical systems lies precision manufacturing technology, notably computer numerical control (CNC) processing. CNC machining enhances production efficiency and guarantees component consistency and quality, essential for achieving peak performance in surgical robots.
This article aims to offer a comprehensive introduction to the manufacturing process of surgical robot parts, encompassing the application of CNC machine tools, material selection, and strategies to enhance manufacturing precision.

Table of Contents
Surgical Robots Overview
- Definition
A surgical robot is high-tech medical equipment controlled by professional doctors through a console or computer system to perform various surgical operations. Comprising a robotic arm, camera, and surgical tools, it provides precise control and feedback through specialized software. - Working Principle
The working principle of handled robots is based on precision kinematics and advanced vision systems. Situated in front of a console, the doctor operates control levers or buttons, allowing the robotic arm to perform precise operations inside the patient’s body. Simultaneously, the camera transmits high-definition images, enabling clear observation of the surgical area and assisting in precise control. Every subtle movement is controlled by precise procedures, ensuring that surgical operations are more precise and controllable. This precision, combined with instant information feedback, enables surgical robots to perform operations with higher accuracy and safety compared to traditional methods.
CNC Machining of Surgical Robots
Part manufacturing for surgical robots typically involves multi-axis CNC machining of precision components, micro-scale laser cutting and welding, and 3D printing of metals and various non-metallic materials. These parts require high precision and strict quality control, so CNC machining is widely used in the manufacturing of surgical robot parts.
CNC Machining of Surgical Robot Parts
In the manufacturing of surgical robot parts, the specific applications of the CNC machining technique mainly include the following aspects:

Manufacturing of Body Implants
Implant surgeries such as knee implants and hip replacements require a high level of precision and accuracy. This can be accomplished by CNC machines that achieve tolerances as small as 4μm.

Production of Surgical Tools
Complex surgical procedures require high-precision, professional tools, such as scalpels, scissors, complex robotic arms for minimally invasive surgeries, etc.

Manufacturing of Electronic Medical Devices
Many medical devices, such as MRI scanners, heart rate monitors, and X-ray machines, feature thousands of CNC-machined electronic components.

Manufacturing of Custom Prostheses
Through 3D scanning and CAD modeling, CNC machines can produce prostheses with intricate details. This process ensures high-precision dimensions, optimizing functionality and comfort for the patient.
Advantages of CNC Machining Technology for Surgical Robot Manufacturing
High precision | CNC machining technology can achieve micron-level machining accuracy. |
High complexity | CNC machining technology is capable of producing intricate shapes and structures. This includes straight lines, curves, and complex curved surfaces, all achieved through precise programming. |
High consistency | CNC machining technology can achieve mass production, and each part can maintain a high degree of dimensional consistency. |
Flexibility | CNC machining technology can adjust processing parameters and programs as necessary at any time. |
Automation | CNC machining technology can realize fully automatic production, which improves production efficiency as well as reduces labor costs. |
Challenges of CNC Machining in Surgical Robot Parts Manufacturing
CNC machining of surgical robot parts needs to deal with challenges such as special material processing thermal management, micron-level precision control, difficulty in processing complex structures, cost-effectiveness optimization, and rapid technology iteration.
Material characteristics | Surgical robot components are typically manufactured from specialized materials such as PEEK and titanium. However, these materials tend to generate excessive heat during processing, which restricts the use of coolants due to contamination concerns. |
High precision requirement | The parts of surgical robots usually require micron-level precision, and any small deviation may make a difference in the effect of surgery. |
Complexity | The parts of surgical robots often have complex structures and shapes, which poses a great challenge to CNC machining. |
Cost control | While ensuring product quality, it is necessary to reduce production costs as much as possible due to the relatively high price of surgical robots. |
Rapid technological updates | CNC processing requires continuous learning and mastering of new technologies to adapt to market changes. |
Materials Used in Surgical Robots
In the manufacturing and processing of robotic surgical equipment, the following materials are typically utilized:

Titanium Alloy
Manufacturers often use titanium alloy to fabricate the shell and structural components of surgical robots for its excellent biocompatibility and corrosion resistance.

Stainless Steel
A common material offering good strength and corrosion resistance, stainless steel is utilized in the production of surgical tools and some structural components of robots.

Aluminum Alloy
Manufacturers use stainless steel, known for its strength and corrosion resistance, to make surgical tools and robot components.

Plastic Materials
Occasionally, manufacturers use high-strength engineering plastics to produce the shells, protective covers, or connectors of surgical robots.

Carbon Fiber Composite Materials
They often enhance mechanical performance and reduce the weight of components in surgical robots for their strength and lightweight properties.
The Specific Steps for the Application of CNC Machining in the Manufacturing of Robotic Surgical Components
·Part design:
First, engineers or designers design corresponding parts according to the needs of the surgical robot, and then they use CAD/CAM software to create 3D models of the parts.
·Develop a processing plant
The processing plan includes selecting suitable processing methods, setting processing parameters, choosing appropriate tools and equipment, etc.
·Programming:
Programmers use specific programming languages like G-code to write CNC programs.
·Trial cutting:
One can perform trial cutting, which validates the accuracy of the CNC program, using simulation software or an actual device.
·Formal processing:
The CNC equipment will automatically cut, drill, grind, and perform other operations according to the preset program until it manufactures the parts.
·Inspection and quality control:
Finally, quality inspectors will use various measuring tools and methods to check the size, shape, and surface quality of the parts.
How to Improve the Accuracy of Surgical Robot Parts Manufacturing?
Optimize the design and manufacturing process | Accurate design and simulation can be carried out through CAD or CAM software, and possible errors can be predicted and adjusted. |
Use high-precision equipment and tools | High-precision CNC machine tools, measuring instruments, and cutting tools can be used. |
Improve processing technology | Such as laser cutting, EDM, ultrasonic processing, etc. |
Strengthen quality control | We can conduct regular quality inspections to detect and correct problems promptly. |
Improve personnel skills | Improved skills and knowledge enable personnel to better comprehend and master processing technology and equipment, resulting in enhanced accuracy of part processing. |
Use new materials | Such as some high-performance plastics and metal alloys. |
Adopt new manufacturing technologies | Such as 3D printing, which can achieve precise manufacturing of complex-shaped parts, thereby improving the processing accuracy of parts. |
How to Choose the Right CNC Manufacturer for Your Surgical Robot Project?
Technical capabilities | Make sure the CNC manufacturer you choose has advanced technology and equipment that can meet the high precision and complexity requirements of surgical robots. |
Experience | Seek manufacturers with extensive experience, as they may have dealt with similar projects and possess the know-how to address potential issues. |
Quality Assurance | Understand the manufacturer’s quality control system and whether there are strict quality inspection and testing procedures to ensure the quality and reliability of parts. |
Service and support | Consider the after-sales service and support, including technical support and parts supply, which will help ensure a smooth project. |
Technical capabilities | Make sure the CNC manufacturer you choose has advanced technology and equipment that can meet the high precision and complexity requirements of surgical robots. |
Conclusion
CNC machining technology is instrumental in the production of surgical robot components, safeguarding the stability and safety of these devices through high-precision, high-efficiency processing techniques. As science and technology progress, the ongoing innovation in CNC processing will further propel the advancement of the surgical robot industry, making significant contributions to human health.
If you are seeking superior-quality infrared thermography imaging equipment and services Renowned for high-grade products, robust technical expertise, customization capabilities, exceptional after-sales support, and continuous innovation in both surgical robots and CNC technology, Runsom Precision is dedicated to providing diversified solutions.
XTJ is a leading OEM Manufacturer that is dedicated to providing one-stop manufacturing solutions of Machining 6061 Aluminum from prototype to production. We are proud to be an ISO 9001 certified system quality management company and we are determined to create value in every customer relationship. We do that through collaboration, innovation, process improvements, and exceptional workmanship.lication: Automotive industry, Bicycle and motorcycle, Door and windows and furniture, Household appliance, Gas meter, Power tool,LED lighting, Medical instrument parts, ect.