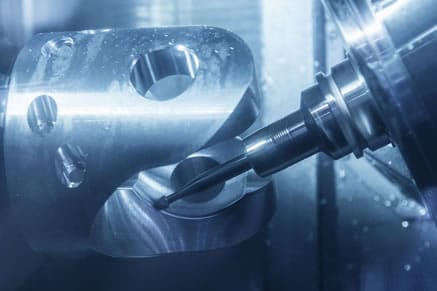
Table of Contents
How to Rapid Prototype for Metalwork
Introducing a new product to market involves a complex process of design, market research, and manufacturing. Rapid prototyping is one part of this process where component parts are made in order to develop a working model of the product—testing its functionality and limitations. These prototypes can be made from the same material as that of the final product, or an alternative material can be used for the purposes of the test case.
Some methods of metal prototyping include:
Investment casting
Fabricating the part directly from metal stock
Machining the part directly from metal stock
Rapid prototyping methods and applications
Each prototyping method has its advantages and disadvantages, as well as factors that make it best suited for certain projects.
3D printing is a relatively new process also known as additive manufacturing—the process of printing one layer of product at a time until a 3D component is built up by the many layers. Each layer can be about 100 microns thick. The printer is controlled by a computerized system, which takes a 3D design as input and creates the 3D product as output.
Technology has evolved over time, and a wide variety of materials have become available for printing. Plastics, nylons, resins, silver, titanium, steel, wax, photopolymers, and polycarbonates can all be used as 3D printing material.
A young woman looks at a 3D printer creating a ball-shaped prototype
3D printing is an innovative form of additive manufacturing—printing one layer of a product at a time until a 3D component is created
There are three main types of 3D printing machines:
Selective laser sintering (SLS) uses printing material supplied in powder form. Each layer of the part is created by melting the powder using a laser. Fresh powder is rolled over the top of the partially completed part and the process is started again until the entire part is built.
Fused deposition modeling (FDM) uses thermoplastic filament and melts it for extrusion. The extrusion is precisely controlled by the computer in accordance with the 3D design, printing each layer in succession.
XTJ is a leading OEM Manufacturer that is dedicated to providing one-stop manufacturing solutions from prototype to production. We are proud to be an ISO 9001 certified system quality management company and we are determined to create value in every customer relationship. We do that through collaboration, innovation, process improvements, and exceptional workmanship.
Stereolithography also uses a laser, but in this case, a liquid product is solidified one layer at a time by the laser action—it is controlled to match the design.
3D printing is popular for rapid prototyping because the process is very resource efficient. No tooling of production lines is required, labor requirements are minimal, and very little waste is generated. The disadvantage of 3D printing is that it can be time consuming—taking hours, and sometimes days, to build complex parts. The part size is limited by the printing area of the machine. In addition, it may not be possible to produce the part in the desired material due to the very high melting point of some metals.
Sand casting
In metal foundries, patterns are used to make the mold that will be used to cast the metal part. A prototype pattern is made in the simplest and most cost-effective way, so that the part can be tested and adjusted if necessary. For this reason, the pattern is often used to make a sand mold as this is the cheapest and quickest mold to produce. From start to finish, a prototype can be made in 2 to 4 weeks using a loose wooden pattern.
A loose wooden pattern is made from wood by a pattern maker using techniques such as turning, tool, die making, and fine wood working. The pattern is manufactured in accordance with the prototype design with some tolerances built in for shrinkage, which occurs as the metal cools. Where the prototype design requires parts with backdraft, these parts are made as loose pieces of the pattern held in place by pins.
Molding sand is specially constituted with the right blend of components so that it has the characteristics needed for metal casting. It must hold its shape, not release too much moisture, and give a good quality finish. Sand is packed around the loose wooden pattern to form a cast, which can then be used to make the metal prototype.
Casting a metal prototype is a standard foundry process where metal is melted, composition is controlled and molten metal is poured into the mold. Once cooled, the mold is broken off and the metal prototype is ready for finishing.
Metal casting of a rapid prototype with a loose wooden pattern is popular due to the low cost of production, and the relative ease of adjusting the pattern and recasting if necessary. It is also possible to make the prototype out of the same material as the final product, thus cutting out further steps of development down the line. Manufacturers often find that the process to develop a prototype often becomes the method for final production with minor modifications.
Investment castingInvestment casting is also a metal foundry process, but uses a different technique to make the pattern for creating the mold. The first step is the creation of a wax pattern that matches the design for the prototype. Historically, wax patterns have been made with injection molding machines or wax presses, but new materials and the development of 3D printing have created an opportunity for investment casting patterns to be made more easily and quickly.
Once the pattern has been made, it is cased in ceramic material which takes on the shape of the pattern as it sets. The mold is then heated until the wax melts and flows out of the casting mold—hence its alternative name, lost wax casting. Standard foundry casting processes follow, where molten metal is poured into the cast. When the metal has cooled and solidified, the ceramic cast is broken off, leaving the metal prototype ready for finishing.
The advantages of this method of rapid prototyping are similar to those of the loose wooden pattern—with the added benefit of finer tolerances and finishes.
Fabricating metal prototypes
Stock metal materials include sheets, rods, tubing, bars, and wire. Any of these can be used as the raw materials to fabricate a metal prototype as a downstream secondary step, rather than through primary manufacturing such as casting or 3D printing.
For sheet metal prototype manufacturing, many different processes can be employed to fabricate a prototype. For example, the physical model could be flattened and laid out on metal sheet to use it as a template, then lasers or torches could be used to cut outlines and openings, and to mark bends. Presses could be used to bend the metal at the marked boundaries, and specialized welding equipment can be used to join parts together.
Workers weld prototype automotive fabrications
Rapid prototyping by welding fabrications allows for minor adjustments to be made to samples without significant time and cost
Tubing can be used for prototyping by processing it through a number of diverse operations to create a prototype part that matches the design:
Flaring – widening the opening at the end of a tube into a funnel shape
Swaging – reducing or increasing the diameter of the tubing
Dimpling – small deformations on the metal surface
Bending – creating shapes through inserting bends at defined points in the tubing
Flattening – using a press to compress the tubing
Piercing – creating holes in the material
Expanding – using heat and tools to open the diameter of the tubing
The main advantage of fabricating a metal prototype from stock materials is the time efficiency. Patterns or molds are not needed, and the raw materials are available off the shelf. The disadvantage is that some prototype designs will be too complex for standard manufacturing processes and therefore cannot be made with this technique.
XTJ is a leading OEM Manufacturer that is dedicated to providing one-stop manufacturing solutions from prototype to production. We are proud to be an ISO 9001 certified system quality management company and we are determined to create value in every customer relationship. We do that through collaboration, innovation, process improvements, and exceptional workmanship.
Machining metal prototypes
End-mill machining tool is used to finish a metal prototype
Prototyping by investment casting can be successful, and further improvements can be enjoyed by finish machining
Machining is any process where a piece of raw material is cut into a desired final shape and size by a controlled material-removal process—also known as subtractive manufacturing. It can be used to manufacture various metal products, as well as materials such as wood, plastic, ceramic, and composites. In modern production, machining is carried out by computer numerical control (CNC).
CNC is the computerized control of machining equipment to make a part according to a 3D design. Machining equipment include lathes, mills, routers, drills, and grinders. The raw material for CNC machines are stock metal products like steel plates and bars.
A 3D design is converted to a computer program, which is then used by the control system to direct the machines. The raw material selected must be larger than the prototype being made because it is through the removal of metal by machining that the prototype is manufactured. Advanced CNC machines control operations on all 3 axes (x,y, and z) and can flip the part and switch machining tools automatically, resulting in a high quality finish and level of accuracy.
A computer numerical controlled (CNC) machine for rapid prototyping
A computer numerical control (CNC) machine allows for metal prototyping with a high degree of accuracy
The advantage of CNC machines over other fabrication techniques is the automated action based on a 3D design. Human intervention is limited and the prototype manufactured matches the design with a high degree of accuracy. More complex prototypes can be manufactured using CNC machines than through manual operations. A disadvantage of machining parts is that the part is made by removing metal from the raw material and this results in waste. Although the waste material can be recycled, there are cost implications and losses that will occur.
Case studies on rapid prototyping
Automotive industry
Research shows that the developments in 3D printing are making a dramatic impact on the ability of engineers to test their ideas and bring products to the market quickly. An automotive article highlights the fact that testing aerodynamics of certain automotive parts is critical to measure their impact on the car’s performance. As test results are obtained, minor adjustments can be made to design, and a new prototype is reprinted very quickly. For aerodynamic testing, it is not essential for the part to be made from the final material as it is the shape that is being tested, not the strength. 3D printing is helping automotive engineers to accelerate their development and improve their efficiency.
Different applications are suited to different manufacturing methods. In one example, a designer discovered this when manufacturing a 2-part ring assembly with a space for a micro SD card in the internal space. The first prototypes were made by Direct Metal Laser Sintering (DMLS), but lower quality surface finish and poor assembly led to an investigation of using a CNC machine with electrostatic discharge machining. The improved performance of the prototype highlighted the advantages of CNC in this specific application.
High-tech industry
Reducing costs of development is an economic imperative for many high-tech companies as they bring their new creations to the market place. When Icon Aircraft launched the project for their A5 recreational aircraft, they invested significant time and energy into finding the most cost effective and efficient way to build their components for prototyping and mass production. A case study indicates that Icon Aircraft gained 2 to 3 weeks on the production schedule, $2000, and two person-days per air ducting part by reducing the need for specialized tooling.
Aircraft industry
The American Foundry Society’s prize for 2017 casting of the year was awarded to a company that developed a new casting for an aircraft passenger seat frame. Historically, this structural component was made from a single billet, but a process of detailed design and engineering resulted in a lattice structure made from magnesium—a material that is lighter than aluminum, but cannot be 3D printed. The casting prototype yielded a product that has the required strength yet is much lighter than existing machined parts. Savings of $100k/year on a single passenger aircraft were calculated based on reduction in fuel costs due to the lighter seats, as well as associated emissions reductions.
Rapid prototyping and the road ahead
A growing number of methods for rapid prototype manufacturing are available to innovators and engineers. Each method has its own advantages and disadvantages. Casting processes are suited to applications where the prototype must be made in the same material as the finished product, especially for high melting point metals. 3D printing is suitable for smaller components made of specific printable materials—this technology is developing and improving continuously. Machining can be used to cut away metal from a stock product where the complexity is not too severe and standard processes such as milling and grinding can still be used.
XTJ is a leading OEM Manufacturer that is dedicated to providing one-stop manufacturing solutions from prototype to production. We are proud to be an ISO 9001 certified system quality management company and we are determined to create value in every customer relationship. We do that through collaboration, innovation, process improvements, and exceptional workmanship.