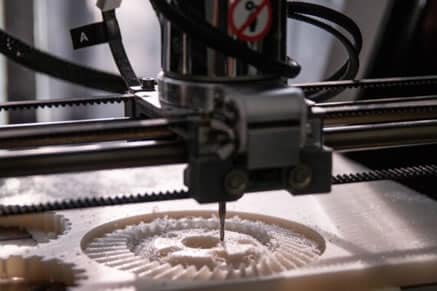
Table of Contents
What is a First Article Inspection?
A First Article Inspection is a type of production validation process. It involves testing and inspecting the first part or parts produced in a batch (or sample parts from the first batch) in order to confirm that it matches up to the engineering drawings.
The number of units assessed in a First Article Inspection report depends on the order size. For production orders, a typical FAI will cover 3–5 units, chosen at random. For a very small batch or a run of prototypes it may only cover the first unit.
A range of metrology equipment can be used during a First Article Inspection. Many inspections will demand the use of a Coordinate Measuring Machine (CMM), while others may require calipers, gauges, etc. Material testing and other validation procedures may also form part of the FAI: for example, an alloy may be tested for hardness and any potential defects. The results of the inspection are written up in a report, which is sent to the buyer.
First Article Inspection is particularly important for new orders, i.e. when a part is being made using a certain manufacturing process for the first time. It may be less critical for repeat orders where the process has already been validated.
A First Article Inspection Report (FAIR) will indicate success or failure. If successful, production can continue as expected; if not, corrective action is taken and the product returns to the pre-production stage.
Who performs a First Article Inspection?
In most cases, a First Article Inspection can be carried out by the part supplier. This is usually agreed upon in the purchase order, as it provides a level of quality assurance. However, in some cases the supplier does not have the in-house facilities for FAI. In these cases, the inspection may be outsourced to a metrology laboratory, which will then complete the report.
As long as the First Article Inspection is conducted by an authorized person, there should be no major difference between whether it is performed by the supplier or by a contractor.
When do you need a First Article Inspection?
While a First Article Inspection would seem to apply to the first attempt to manufacture a part, it may actually be requested in various circumstances, including:
When a part is manufactured for the first time
When a part’s design is updated
When the manufacturing process changes in some way (e.g. if a 3-axis CNC machine is replaced by a multi-axis machine)
When the manufacturer changes location
When a significant period of time has elapsed between orders
First Article Inspections are widely carried out in industries where parts have strict performance requirements. Such industries include defense, aerospace, automotive, and medical. They are not always required for simple consumer goods, apparel, and other low-risk areas, or for prototypes and small batches where there is minimal financial risk.
Aerospace and aviation are industries where First Article Inspection takes place for most parts. As such, standards organization SAE has published a standard for aerospace FAI. This is called the AS9102 standard.
What goes on a First Article Inspection Report?
A First Article Inspection Report (FAIR) contains a detailed breakdown of the inspection, showing what was tested, how it was tested, and the relevant results. An overview of information provided in an FAIR can be found below.
Part Identification
Part number
Revision level
Serial number
Drawing number
Supplier Information
Name and address of the supplier or manufacturer
Contact information
Product Characteristics
Dimensions
Tolerances
Material specifications
Surface finish requirements
Materials and Processes
Specifications for raw materials
Details on manufacturing processes
Inspection Details
List of measuring tools and equipment used during the inspection
Description of the sampling plan used for inspection
Date of inspection
Inspection Results
Actual measurements and data collected during the inspection
Conformance or non-conformance to specified requirements
Results of any required tests or validations
Certifications and Documentation
Certificates of compliance
Material test reports
Inspection and testing records
Non-Conformance Reports (if applicable)
Details on any deviations from the specified requirements
Corrective actions taken or planned
Other
Signatures and dates of approval from relevant parties, such as quality assurance personnel or engineers
Any additional comments or notes relevant to the inspection.
XTJ is a leading OEM Manufacturer that is dedicated to providing one-stop manufacturing solutions from prototype to production. We are proud to be an ISO 9001 certified system quality management company and we are determined to create value in every customer relationship. We do that through collaboration, innovation, process improvements, and exceptional workmanship.