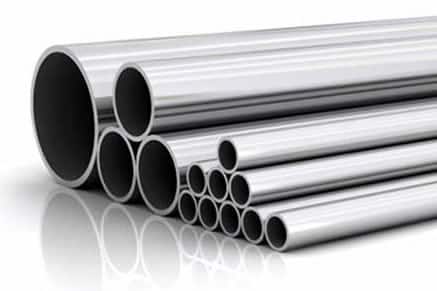
What is Standard Steels?
Standard Steel is the generic term for a large family of iron-carbon alloys that are malleable, within some temperature range, immediately after solidification from the molten state.
The principal raw materials used in steelmaking are iron ore, coal, and limestone. These materials are converted in a blast furnace into a product known as “pig iron,” which contains considerable amounts of carbon, manganese, sulfur, phosphorus, and silicon. Pig iron is hard, brittle, and unsuitable for direct processing into wrought forms. Steelmaking is the process of refining pig iron as well as iron and steel scrap by removing undesirable elements from the melt and then adding desirable elements in predetermined amounts. A primary reaction in most steelmaking is the combination of carbon with oxygen to form a gas. If dissolved oxygen is not removed from the melt prior to or during pouring, the gaseous products continue to evolve during solidification. If the steel is strongly deoxidized by the addition of deoxidizing elements, no gas is evolved, and the steel is called “killed” because it lies quietly in the molds. Increasing degrees of gas evolution (decreased deoxidation) characterize steels called “semikilled”, “capped,” or “rimmed.” The degree of deoxidation affects some of the properties of the steel. In addition to oxygen, liquid steel contains measurable amounts of dissolved hydrogen and nitrogen. For some critical steel applications, special deoxidation practices as well as vacuum treatments may be used to reduce and control dissolved gases.
The carbon content of common steel grades ranges from a few hundredths of a percent to about 1 percent. All steels also contain varying amounts of other elements, principally manganese, which acts as a deoxidizer and facilitates hot working. Silicon, phosphorus, and sulfur are also always present, if only in trace amounts. Other elements may be present, either as residuals that are not intentionally added but result from the raw materials or steel-making practice, or as alloying elements added to effect changes in the properties of the steel.
Steels can be cast to shape, or the cast ingot or strand can be reheated and hot worked by rolling, forging, extrusion, or other processes into a wrought mill shape. Wrought steels are the most widely used of engineering materials, offering a multitude of forms, finishes, strengths, and usable temperature ranges. No other material offers comparable versatility for product design.
Standard Steel Classification
Wrought steels may be classified systematically into groups based on some common characteristic, such as chemical composition, deoxidation practice, finishing method, or product form. Chemical composition is the most often used basis for identifying and assigning standard designations to wrought steels. Although carbon is the principal hardening and strengthening element in steel, no single element controls the steel’s characteristics. The combined effect of several elements influences response to heat treatment, hardness, strength, microstructure, corrosion resistance, and formability. The standard steels can be divided broadly into three main groups: carbon steels, alloy steels, and stainless steels.
Carbon Steels
A steel qualifies as a carbon steel when its manganese content is limited to 1.65 percent (max), silicon to 0.60 percent (max), and copper to 0.60 percent (max). With the exception of deoxidizers and boron when specified, no other alloying elements are added intentionally, but they may be present as residuals. If any of these incidental elements are considered detrimental for special applications, maximum acceptable limits may be specified. In contrast to most alloy steels, carbon steels are most often used without a final heat treatment; however, they may be annealed, normalized, case hardened, or quenched and tempered to enhance fabrication or mechanical properties. Carbon steels may be killed, semikilled, capped, or rimmed, and, when necessary, the method of deoxidation may be specified.
Alloy Steels
Alloy steels comprise not only those grades that exceed the element content limits for carbon steel, but also any grade to which different elements than those used for carbon steel are added, within specific ranges or specific minimums, to enhance mechanical properties, fabricating characteristics, or any other attribute of the steel. By this definition, alloy steels encompass all steels other than carbon steels; however, by convention, steels containing over 3.99 percent chromium are considered “special types” of alloy steel, which include the stainless steels and many of the tool steels.
In a technical sense, the term alloy steel is reserved for those steels that contain a modest amount of alloying elements (about 1-4 percent) and generally depend on thermal treatments to develop specific mechanical properties. Alloy steels are always killed, but special deoxidation or melting practices, including vacuum, may be specified for special critical applications. Alloy steels generally require additional care throughout their manufacture because they are more sensitive to thermal and mechanical operations.
Stainless Steels
Stainless steels are high-alloy steels and have superior corrosion resistance to the carbon and conventional low-alloy steels because they contain relatively large amounts of chromium. Although other elements may also increase corrosion resistance, their usefulness in this respect is limited.
Stainless steels generally contain at least 10 percent chromium, with or without other elements. It has been customary in the United States, however, to include in the stainless steel classification those steels that contain as little as 4 percent chromium. Together, these steels form a family known as the stainless and heat-resisting steels, some of which possess very high strength and oxidation resistance. Few, however, contain more than 30 percent chromium or less than 50 percent iron.
In the broadest sense, the standard stainless steels can be divided into three groups based on their structures: austenitic, ferritic, and martensitic. In each of the three groups, there is one composition that represents the basic, general-purpose alloy. All other compositions are derived from the basic alloy, with specific variations in composition being made to obtain very specific properties.
The austenitic grades are nonmagnetic in the annealed condition, although some may become slightly magnetic after cold working. They can be hardened only by cold working, and not by heat treatment, and combine outstanding corrosion and heat resistance with good mechanical properties over a wide temperature range. The austenitic grades are further classified into two subgroups: the chromium-nickel types and the less frequently used chromium-manganese-low-nickel types. The basic composition in the chromium-nickel group is widely known as 18-8 (Cr-Ni) and is the general-purpose austenitic grade. This grade is the basis for over 20 modifications that can be characterized as follows: the chromium-nickel ratio has been modified to change the forming characteristics; the carbon content has been decreased to prevent intergranular corrosion; the elements niobium or titanium have been added to stabilize the structure; or molybdenum has been added or the chromium and nickel contents have been increased to improve corrosion or oxidation resistance.
The standard ferritic grades are always magnetic and contain chromium but no nickel. They can be hardened to some extent by cold working, but not by heat treatment, and they combine corrosion and heat resistance with moderate mechanical properties and decorative appeal. The ferritic grades generally are restricted to a narrower range of corrosive conditions than the austenitic grades. The basic ferritic grade contains 17 percent chromium. In this series, there are free-machining modifications and grades with increased chromium content to improve scaling resistance. Also in this ferritic group is a 12 percent chromium steel (the basic composition of the martensitic group) with other elements, such as aluminum or titanium, added to prevent hardening.
The standard martensitic grades are magnetic and can be hardened by quenching and tempering. They contain chromium and, with two exceptions, no nickel. The basic martensitic grade normally contains 12 percent chromium. There are more than 10 standard compositions in the martensitic series; some are modified to improve machinability and others have small additions of nickel or other elements to improve the mechanical properties or their response to heat treatment. Still others have greatly increased carbon content, in the tool steel range, and are hardenable to the highest levels of all the stainless steels. The martensitic grades are excellent for service in mild environments such as the atmosphere, freshwater, steam, and weak acids, but are not resistant to severely corrosive solutions.
Numbering Systems for Metals and Alloys
Several different numbering systems have been developed for metals and alloys by various trade associations, professional engineering societies, standards organizations, and private industries for their own use. The numerical code used to identify the metal or alloy may or may not be related to a specification, which is a statement of the technical and commercial requirements that the product must meet. Numbering systems in use include those developed by the American Iron and Steel Institute (AISI), Society of Automotive Engineers (SAE), American Society for Testing and Materials (ASTM), American National Standards Institute (ANSI), Steel Founders Society of America, American Society of Mechanical Engineers (ASME), American Welding Society (AWS), Aluminum Association, Copper Development Association, U.S. Department of Defense (Military Specifications), and the General Accounting Office (Federal Specifications).
The Unified Numbering System (UNS) was developed through a joint effort of the ASTM and the SAE to provide a means of correlating the different numbering systems for metals and alloys that have a commercial standing. This system avoids the confusion caused when more than one identification number is used to specify the same material, or when the same number is assigned to two entirely different materials. It is important to understand that a UNS number is not a specification; it is an identification number for metals and alloys for which detailed specifications are provided elsewhere. UNS numbers are shown in Table 1; each number consists of a letter prefix followed by five digits. In some, the letter is suggestive of the family of metals identified by the series, such as A for aluminum and C for copper. Whenever possible, the numbers in the UNS groups contain numbering sequences taken directly from other systems to facilitate identification of the material; e.g., the corresponding UNS number for AISI 1020 steel is G10200. The UNS numbers corresponding to the commonly used AISI-SAE numbers that are used to identify plain carbon, alloy, and tool steels are given in Table 2.
Summary
This article described the principal types of standard steels.CNC Machining with standard steels,please Visit XTJ.
XTJ is a leading OEM Manufacturer that is dedicated to providing one-stop manufacturing all Type standard steels Parts solutions from prototype to production. We are proud to be an ISO 9001 certified system quality management company and we are determined to create value in every customer relationship. We do that through collaboration, innovation, process improvements, and exceptional workmanship.