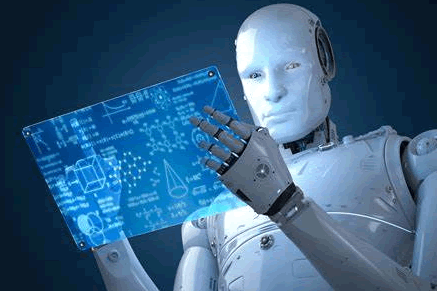
Industry Data is an invaluable commodity in the modern world. Manufacturing is going through a fourth industrial revolution (known as Industry 4.0), where companies are focusing heavily on the interconnectivity of devices, automation, artificial intelligence software, and real-time data processing. By leveraging key advancements such as internet connectivity equipment and machine learning, manufacturers are manipulating data to produce at faster, more efficient rates. However, these technologies are complex and require an understanding of many different aspects of computer science and manufacturing to correctly implement them. This article will explore how machine learning is used in a manufacturing setting and its benefit to the efficiency, productivity, and overall profitability of a company’s manufacturing capabilities.
For related information on this topic, visit our article about predictive analytics and machine learning in the supply chain.
Table of Contents
What is Machine Learning (ML), and How Does it Work?
Machine learning (ML, also known as predictive analytics) is an implementation of artificial intelligence (AI) that uses large datasets and computer algorithms to gradually improve its intended application over time. The history of ML methodology coincides with the advent of artificial intelligence in the 1960s by IBM and is increasingly more important in the field of data science.
Machine learning functions in much the same way humans learn a skill; a program is used to accomplish a task, and each successive completion of this task will inform how to better achieve the goal on the next go around. ML systems are different in that they can surpass human capabilities and can handle larger datasets than humans ever could alone.
ML uses statistical methods and algorithms (either “learned” by manual human input or by a generative process developed autonomously) to perform tasks within sets of data. Some ML programs take in an input of valid (aka “training” or “labeled”) data and use this set to make classifications/predictions in future datasets, while others discover these interesting patterns in raw (or “unlabeled”) datasets. Without getting too far into the computer science weeds, ML can be thought of as a means of handling massive datasets and leveraging them for user benefit. ML techniques can discover key insights within large quantities of seemingly random data, making it valuable in data mining projects where ML can ultimately help optimize the application at hand. Or, in classification/predictive roles, ML can be used to identify similarities in writing or visuals and can determine what future pieces of information should look like in new datasets.
It is important not to confuse ML with deep learning, another sub-field of AI that implements complex neural networks – that is, systems modeled after the human brain. Think of deep learning as a specific branch of the ML field; for brevity, this article will largely focus on classical ML systems and their use in the manufacturing space, and not deep learning programs (though they overlap in many cases).
Types of ML Training Methods
The graphics processing unit and chip manufacturer Nvidia defines four main types of ML training methods, all differentiated by how they function to solve problems. Note that this section is a simplification of ML functionality meant to provide a brief overview and that the inner workings of ML are much too rigorous to be fully understood in one sitting:
Supervised learning, as its name suggests, is when an ML program is trained via a pre-labeled dataset classified by the user (a human). Supervised learning is implemented when there is an ample supply of reference points with which to train the algorithm, and it is generally effective in continuous data and classification applications (think graphing x-y values or differentiating faces in an image). However, supervised learning can be time-consuming on the user’s part, or may be impossible to achieve due to the absence of reference points or “true” values.
Unsupervised learning is the opposite of supervised learning – a raw, unlabeled dataset is fed into an ML program and its algorithm identifies relationships without any user intervention. Best used for discovering unknown or hidden patterns within massive datasets, unsupervised ML techniques will cluster, detect anomalies, associate, and remove noise data to train an algorithm towards its intended application. Unsupervised learning is a great tool for users who do not have access to labeled data or are looking for patterns not seen by the human eye.
Semi-supervised learning is a blend of the two previous techniques. An ML program is fed a mix of labeled and unlabeled data to get the best out of both learning methods. Semi-supervised programs can use structured, labeled data to make independent conclusions about the unstructured data. This not only increases the program’s accuracy in comparison to unsupervised learning, but this method also reduces the time and cost of obtaining a fully labeled dataset needed for supervised learning.
Reinforcement learning is the newest addition to ML training techniques, where a reinforcement algorithm learns via trial and error and is “rewarded” or “punished” based on whether its conclusions help or hurt its main objective. Reinforcement learning is classified as a behavioral ML model, as it requires rounds of real-time feedback to become more accurate as time goes on. The famous IBM Watson system that won the 2011 Jeopardy challenge implemented reinforcement learning to determine when to attempt an answer, which category to choose, and how much to wager on its bets.
ML in Manufacturing
This section will detail how ML can be applied in a manufacturing setting to augment existing techniques and capabilities. Note that this section is not exhaustive and only provides some of the most notable advancements as of 2023
Predictive Maintenance
One of the largest benefits of ML in manufacturing is its use in predicting, detecting, and alerting users to potential problems in their factory equipment. Usually, equipment will simply fail and cause painful delays and unscheduled downtime in a company’s production capabilities – however, by utilizing time-series data from remote monitoring systems combined with predictive maintenance ML algorithms, users can visualize the status of their equipment and predict things such as Remaining Useful Life (RUL) as well as flag devices performing outside their normal system behavior before they break down. This implementation of ML pinpoints the weakest areas of a manufacturing line, reduces machine downtime, and provides a detailed schedule of the predicted maintenance of equipment for maintenance workers, ultimately eliminating unpleasant surprises.
For more information on remote monitoring, read our article on how to add remote monitoring to your production line.
Process-Driven Loss Reduction & Defect Detection
An ML system observing your factory can detect where losses in yield are coming from, as well as identify defects. Using a method known as root-cause analysis, algorithms will highlight the most inefficient parts of the production line. Improving upon these inefficiencies can lead to significant increases in yield, optimizing resource usage, and minimizing waste volume per unit produced. Visual sensors can also remotely inspect for products that deviate from the normal (though these systems may land in the camp of deep learning), increasing quality assurance across large production volumes without the lengthy process of human inspection. Process-driven loss reduction is attractive to manufacturers, as it will not only highlight areas of improvement within their supply chain but also lead to an increase in yields and to an overall larger profit margin.
Data-Enabled Resource & Asset Management
Having constant, automated oversight can lead to all kinds of optimizations, including resource and asset management. ML programs will analyze material/product inventory, inbound shipments, work-in-process, market trends, and other variables that would otherwise be shrouded in paperwork. ML programs can also choose the best possible set of machines for a given production run, as well as show how much product is being warehoused at a given time. For example, Tyson Foods, Inc. utilizes ML algorithms with cameras in a so-called smart inventory management system to track the exact quantity of chicken passing through their supply chain, giving them valuable metrics to further their bottom line.
Product Demand & Energy Consumption Forecasting
ML techniques are not just useful for what exists in the present – their ability to forecast demand using data-driven prediction models can fundamentally change the workflow of a factory. Tools like time-series analysis, feature engineering, and Natural Language Programming (NLP) techniques help ML programs forecast customer behavior patterns over time, allowing manufacturing to ebb and flow with ever-changing trends. Also, thanks to the advent of Industrial Internet of Things (IIoT) devices, users can collect historical data on equipment activity levels and energy use. Using this data, ML programs can predict future energy consumption and estimate energy bills as well as optimize energy usage to reduce these bills across large timespans.
Process Visualization & Transparency
The ability to visualize the full breadth of a production process is an invaluable thing to have, and ML programs in tandem with IIoT devices can provide this full picture for users. AI-based “digital twin” factories model a virtual representation of your physical plant using real-time data. With this simulation, users can fully understand the scope of their projects, perform generative-based design within short timeframes, and visualize key metrics for those not well acquainted with their systems. This level of end-to-end transparency also helps discover hidden connections between seemingly unrelated processes in the supply chain, furthering optimization efforts.
Summary
This article presented an understanding of what machine learning is and how it can be used in a manufacturing setting. Clearly, machine learning is a cutting-edge tool that is revolutionizing the way we do business and will only continue to expand its current capabilities as factories get smarter. We hope this brief investigation highlights the massive benefits machine learning can bring to manufacturers and how it is applied to real-world supply chains. For more information on related products, consult our other guides or visit XTJ Machining official Site.
XTJ is a leading OEM Manufacturer that is dedicated to providing one-stop manufacturing solutions  from prototype to production. We are proud to be an ISO 9001 certified system quality management company and we are determined to create value in every customer relationship. We do that through collaboration, innovation, process improvements, and exceptional workmanship.