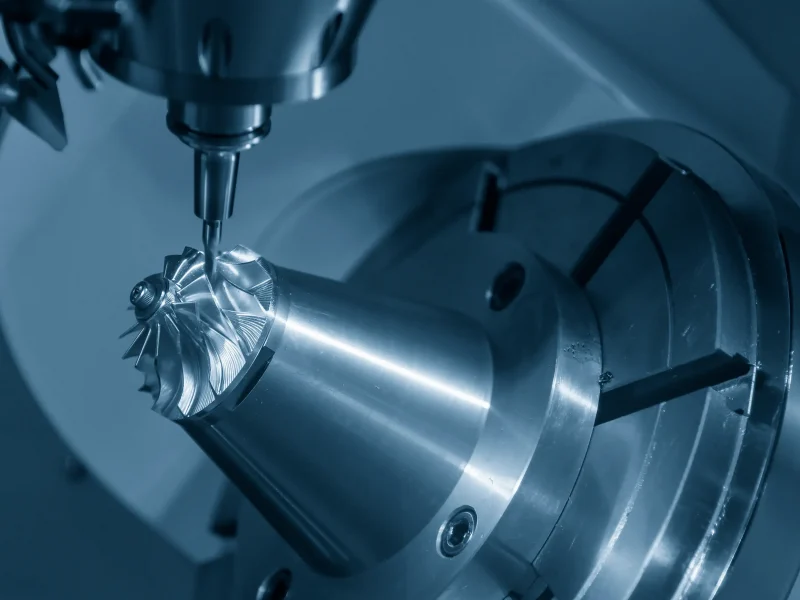
Although multiaxis machining has been the standard operating process for most manufacturers and industrial operations since at least the 50s and 60s, the addition of more simultaneous axes is still one of the most groundbreaking innovations in industry. The method itself of simultaneous and multiaxis milling and CNC machining is an engineering marvel, as it enabled many capabilities of the modern industry. However, the addition of other parts and components to industrial milling machines has enable the development of 5-axis advancements, making it one of the most commonly applied manufacturing process, marking the major developments of modern day manufacture.
Nowadays, multiaxis machining, notably 5 axis milling machines and CNC machines, are more common, as the addition of multiple axes is more or less the norm. These machines are used to manufacture parts and components for multiple industries, and are mostly associated with the production of metal parts (or of other materials) with complex shapes, precise measurement and extensive details. As of today, multiaxis machining is an industrial standard, and 5 axis CNC machines constitute the main addition for allowing machining and CNC milling along with more than the main 3 axes.
Table of Contents
What is 5 axis machining?
As a manufacturing and machining process, multiaxis machine, particularly 5 axis CNC machines are tools that enable the workpiece to be manipulated along multiple axes. These machines remove excess material from the workpiece during the milling process. In addition to the regular 3 axes (x, y, z), 5 axis machines can also move the substrate along the additional fourth and fifth axes, by rotating the spindle. 5 axis machines, as with most multiaxis CNC and milling machines, are defined by 3 main components.
The physical or machining capabilities usually refer to the spindle speed, torque and axis orientation. In CNC applications, the CNC drive system (positioning monitoring, ball screws and servomotors) and controller (data transfer and processing systems) are as significant.
Despite the clear advantage of multiaxis CNC machines, they are mostly useful for complex operations, parts and components with intricate designs and tight tolerances. These can however achieve levels of precision and customizability unattained with traditional procedures. With the ongoing advances in computer-aided manufacturing, the potential of 5 axis machining will only be compatible with more uses that are possible and enhance the process in terms of precision and required labor.
Varieties of 5 axis machines
5 axis CNC machines can vary in form, each adapted with specific applications. These several varieties can each achieve slightly different manipulation. They mostly differ in the main parameters of multiaxis machines, notably the number and orientation of rotary axes. 5-axis machining is quite similar to traditional 3-axis machining, with the main difference being the two extra rotational axes of the workpiece rotation, which offer a greater cutting flexibility. Depending on the specific configuration of a 5-axis machine, they can also perform a wider range of operations like milling and turning. Each of these varieties have specific benefits and common usages.
3+2 Axis Machines
As a subtype of 5-axis machines, this type of multiaxis machines can obtain most of the results achieved by regular 5-axis machines. This type of configuration can be obtained by attaching a tilting rotary table to a vertical machine. The main characteristic of 3+2 axis machines is that the workpiece remains stationary and fixed throughout the process, with the cutting tool instead enabled to move along two additional axes.
This process can indeed make cuts along the workpiece from all sides. This configuration can still adjust the orientation and positioning of the workpiece, but it still has to remain static when machine is operating; a method known as positional 5-axis machining. This process can often be cost-effective as it enables better substrate stability, and is compatible with several cutting tools. Yet, it is often less efficient for more complex designs.
4+1 Axis Machines
This is another configuration of 5-axis machining methods using stationary axes. In this method, only a single rotary axis holding the substrate is held in a fixed orientation. This configuration is essentially a simplification of regular 5-axis CNC machining, harnessing the dynamic movements of three translational axes and one rotary axis. This method can also be described as surface-independent machining, as the cutting angle is not necessarily determined by the surface angle. 4+1 axis machine can maintain a constant angle, increasing the stability of the workpiece, and minimizing the changes in speed that often characterize surface-dependent machining. Yet, this method is restricted to only a limited set of cylindrical shapes.
Simultaneous 5-Axis Machines
This refers to the regular 5 axis CNC machines. It is a surface dependent machining process in the sense that the cutting tool is always perpendicular to the substrate, and allows movement of the cutting tool along the three primary axes, and rotation of the workpiece along the three rotational axes as well. This configuration would enable the cutting or milling tool to remove material in areas that hard to reach with other 5-axis configurations. The current advances in multiaxis machining have made 5-axis machines easier to operate and their process more time-efficient. This method is particularly effective for complex parts.
Advantages and Disadvantages
There are many characteristics of 5 axis machines that have made them very sought after by manufacturers. The work of a 5 axis machine in unmistakable and their potential is only expanding with the use of multiple cutting tools and advances in technology and multiaxis machining. Nonetheless, there are still challenges facing its industrial applications.
The most prominent benefit of 5-axis machines is the increased accuracy and facilitated creation of complex geometries. The axes can attain hard to reach areas with precision, and create complex cutting angles, contours and undercuts that have otherwise been difficult and required processing with several machines.
Another main benefit is the centralized setup that multiaxis machines offer. In most 3 axis machines, the workpiece is processed with different pieces of equipment, and the transition can often cause a loss of alignment. The centralized single setup of 5-axis machines can be adapted to multiple uses which ensures a thorough processing of the substrate without the need to recheck parameters and measurements.
These machines can also decrease the time required to process components with complex shapes. In addition, the short cutting tool, often used with 5-axis CNC machines, has reduced vibrations when operating at high cutting rates, which can produce a significantly better surface texture.
Despite the observable advantages of 5-axis machines in terms of quality and efficiency, the challenges facing this method are mostly due to its cost and, at times, complexity of processes. Notably, the cost of a 5-axis machine is quite high. As most of its applications have implemented computer-aided processes, the required software can also add to the costs. In addition, maintenance of 5-axis machines is not only costly but also demanding in terms of worker skill.
Operating a 5 axis CNC machine requires intricate programming to manipulate the several axes and the cutting tool. The trajectory and movement of each component has to be calculated and monitored throughout the process to ensure precise cutting and avoid collisions and tool interference. Such a complex process requires different geometric operations and highly skilled labor. As such, it can significantly increase labor costs, as well as the risk of error.
Usage Of 5-Axis Machines
Most industrial appliances and components are produced from machining processes, however the more intricate designs, complex parts requiring very precise measurements are often the forte of 5-axis CNC machines and multiaxis machining in general. This makes 5-axis milling and machining perfect for industries like energy and aerospace. The latter in particular requires several components with complex shapes and requiring precise measurements. The spindles and highly customizable orientation of a 5 axis CNC machine can target specific areas an handle extreme cutting conditions and fine-tuned designs.
This method of multiaxis CNC machining has recently become the standard in manufacturing parts for the automotive industry. The induction of multiaxis machining revolutionized automobile manufacture by enabling the production of engines with more tight tolerances, and consequently more horsepower, and managed to make automobiles more reliable. Nowadays, a 5 axis CNC machine can be used to make gearboxes, drive axles as well as engine housings and rims.
With the recent growth of robotics and automated industrial machinery, 5 axis machines have become widely applied to produce customized robotics parts. These can include effectors, storage units and customized jigs. The possible usages of multiaxis machining is increasingly expanding. With the recent breakthroughs in industry and technology, this CNC method will enable more projects that were previously challenging and complex.
Conclusion
5-axis mills and CNC machines are now a staple of modern manufacture and industry. They can produce complex parts and geometries with precise measurements. They are optimal for components with tight tolerances and requiring high resistance, and can also significantly improve the process of most manufacturing operations. The single setup approach of 5-axis machines is now an optimum parameter for the vertical machining center. The precision and high accuracy attained with these machines will only become a standard in the near future. As multiaxis machining advances, it will significantly expand their potential.