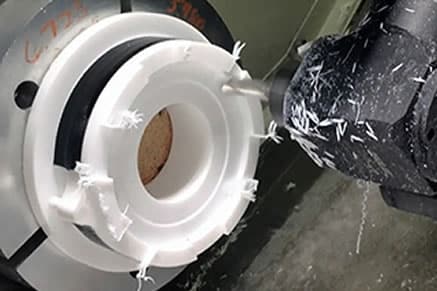
ABS plastic is a versatile material with vast applications in different industries, especially for machined prototypes and structural components. Here are some of the typical uses of machine ABS plastic parts:
Automotive
CNC-machined ABS parts are used extensively in the automotive industry due to their low cost, rigidity, low weight, and shock absorbance characteristics. Typical ABS automotive parts include driveline spares, wheel covers, protective bumpers, steering, vehicle dashboards, and suspension components.
Electronics and Electrical
Manufacturers in the electronics industry often use ABS plastic for various applications, including computer keyboards, enclosures, power plugs, insulators, power-tool housings, and power plugs.
Medical
CNC-machined ABS components have different uses in the medical sector. Typical medical ABS parts include drug delivery systems, compressors, lab equipment housing, pharmaceutical packaging, and ultrasound equipment.
Defense
Manufacturers in the defense industry CNC machine ABS plastic for different parts and components because of its remarkable toughness and high-impact resistance. Typical uses of ABS plastics in safety and defense field include hard hats, protective headgear, defense pads, and hard hats.
Food Processing
The food processing industry utilizes various ABS parts because of the material’s good heat resistance and chemical resistance properties. CNC-machined ABS plastics are commonly used in food dryers, refrigerator liners, ovens, food processors, and juice presses.
Expert Tips For Effective ABS CNC Machining
abs cnc machined part
ABS CNC Machined Part
Despite ABS’ excellent balance of materials, several pitfalls are associated with machining acrylonitrile butadiene styrene. In this section, we will explore the helpful tips for efficient ABS CNC machining:
Use Machine-Grade ABS Plastic
Generally, ABS plastics are of different grades, each with distinct formulations optimized for machining, extrusion, or casting. Hence, consider using machine-grade ABS plastics when drilling, milling, or turning to ensure better chip formation and excellent surface finish.
Adjust Your Cutting Parameters
Adapting your cutting parameters is essential to achieve the best results in ABS plastic machining. Making extremely deep or shallow cuts in a single pass can lead to machining chatter or deform your machined ABS parts. Besides, incompatible feed rates or cutting speeds can result in excessive heat build-up that affects your ABS products.
Although you need an experienced expert to find suitable cutting parameters for your parts, significant quality improvements compensate for optimizing this aspect of the machining process. However, ensure the ABS workpiece is firmly held in the CNC machine without being over-compressed to avoid distortion in the final part.
Consider Annealing the ABS Plastic
Unannealed plastic parts may have large internal stresses not usually visible in the stock material. These internal stresses could distort finished products if the ABS material is heated during machining or use, warping its dimensions outside tolerance limits.
However, machining experts recommend putting ABS plastic in a heat treatment oven before machining. Heat the material slowly, maintaining the annealing temperature, then cool it slowly to relieve internal stresses.
Use Suitable Cutting Fluid
cnc milled abs part
CNC Milled ABS Part
Overheating and deformation can occur when machining ABS plastic. Use an appropriate coolant to mitigate heat build-up and prevent the workpiece from machining complications or defects. Although ABS plastic exhibits good overall chemical resistance performance, machining it with coolants designed for ceramics or metals can lead to contamination.
Experts recommend using a non-aromatic, water-soluble coolant for plastic machining when fabricating ABS parts. Depending on the machined part’s design and preferred coolant, you can apply plastic coolant as a continuous mist, a jet of pressurized gas, or a flowing liquid.
Use Appropriate Cutting Tools
The machine tools suitable for CNC milling titanium alloys or high-strength steel are unsuitable for ABS plastics. Experts recommend using the cutting tools designed for plastic in CNC machining ABS parts, such as carbide end mills or router bits. Moreover, it is crucial to ensure these CNC tools have sharp edges to prevent damaging the surface of the plastic parts, especially when machining thin or intricate parts that can be easily distorted.
Acrylonitrile butadiene styrene (ABS) plastic is a common thermoplastic with good mechanical properties and manufacturability for low-volume production and custom parts. CNC-machined ABS parts are widely used in different industries due to this cost-effective material’s excellent impact strength, rigidity, and toughness characteristics. However, understanding the basics of ABS CNC machining is critical to ensuring the desired outcome and preventing complications.
XTJ is a leading OEM Manufacturer that is dedicated to providing one-stop manufacturing solutions of Machining 6061 Aluminum from prototype to production. We are proud to be an ISO 9001 certified system quality management company and we are determined to create value in every customer relationship. We do that through collaboration, innovation, process improvements, and exceptional workmanship.lication: Automotive industry, Bicycle and motorcycle, Door and windows and furniture, Household appliance, Gas meter, Power tool,LED lighting, Medical instrument parts, ect.