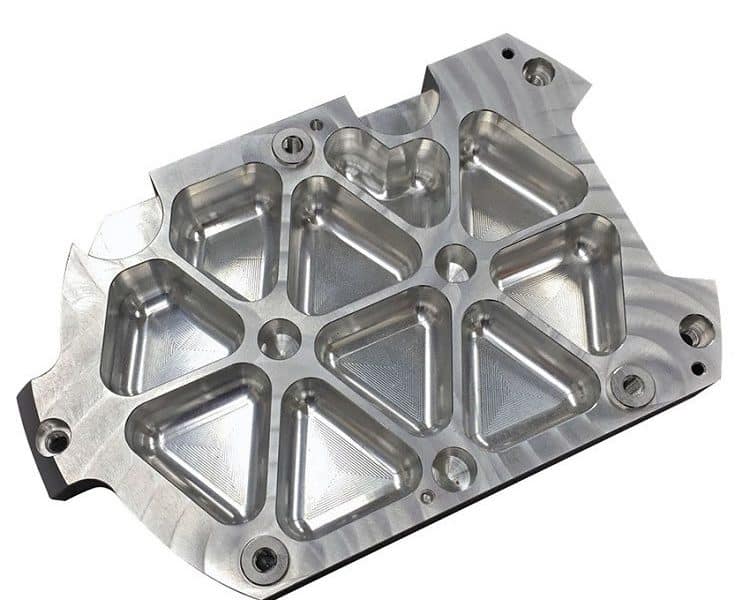
Nylon 11 and Nylon 12 are polyamides that we offer in our broad selection of materials here at XTJ. While both polyamides are nylon materials, they are developed differently. PA12 is derived mostly from petroleum sources. On the other hand, PA11 is entirely derived from vegetable oil, making it one of the rare bio-based thermoplastics available.
Nylon 12 is developed to replace most of the functions of Nylon 11, so most of its properties are consistent. Both PA11 and PA12 are commonly used in powder bed fusion processes like selective laser sintering (SLS) and multi-jet fusion (MJF) — both of which are some of the fastest 3D printing technologies. They offer strong resistance to chemicals including fuels, bases, and salts, have excellent resolution, and have the ability to recycle around 70% of unfused powder after a build.
Chemically speaking, PA11 and PA12 are very similar polymers, differing only by one carbon in the polymer backbone. However, that single carbon atom makes a tremendous difference in how the polymer arranges itself to form three-dimensional objects.
The stronger, more flexible alternative
While both Nylon 11 and Nylon 12 have uses in both prototyping and end-use applications, Nylon PA11 has the edge over PA12 in flexibility, strength, and impact resistance. These qualities make it the preferred material for more demanding applications.
PA11 nylon printed prosthetics image by adobestock
Impact Resistance – Nylon 11 is more flexible and generally stronger than Nylon 12. The combination of its strength and high elongation at break makes it the most impact-resistant nylon 3D printing plastic material available at XTJ.
Mechanical Properties – With its excellent mechanical properties, Nylon PA11 is a popular choice within the consumer goods markets for cases and containers as well as within the sports and automotive industry. It has been found to be particularly useful within the medical sector, an ideal choice for prosthetics, insoles, snap fits and living hinges due to its durability and flexibility.
Environmental Impact – As PA11 is entirely derived from vegetable oil, it consumes less non-renewable resources to be produced and overall leaves a lower environmental impact.
The stiffer, more constant alternative
Nylon PA12 has superior UV and heat resistance and an excellent ability to stay constant despite drastic temperature changes. The material is characterized by high strength, stiffness, strong resistance to cracking under stress, and an excellent long-term constant behavior.
PA12 nylon prototype
Heat and UV Resistance – Nylon PA12 has a heat deflection temperature of 182 degrees Celsius (at 0.42MPa). At elevated temperatures and increased radiation levels, PA12 maintains excellent dimensional stability and resists degradation of the polymer matrix. As such, it is often found in functional components, where resistance is more important than durability. Fats, oils, and solvents are examples of environments in which a part’s resistance is critical.
Operating Temperatures – Apart from high temperatures, PA12 can withstand drastic temperature drops and have strong resistance to cracking under stress. It can stay exceptionally strong even when temperature dip below freezing.
Processability and Cost – Though less eco-friendly, Nylon PA12 prints more reliably than PA11, is compatible with more surface finishing options, and is a cheaper material to manufacture, making it favoured for rapid prototyping.
One less carbon atom can make a huge difference
Both of these polyamides are excellent materials and can be used to fulfil a vast range of prototyping and end-use application goals. Although they share many similarities, there are distinct differences that make each material better suited for different applications.
PA11 is more flexible, less brittle, and better for printing thin walls and lattice structures. It is ideal for making mechanically loaded functional parts and also a great choice if you want to make quality products without leaving a carbon footprint on the environment. In comparison, PA12 is stiff, cheaper, has better heat resistance, and has excellent long-term-constant behavior. It is preferred for making components exposed to drastic temperature changes and for day-to-day rapid prototyping.
XTJ is a leading OEM Manufacturer that is dedicated to providing one-stop manufacturing solutions of Aluminum 7075 Parts from prototype to production. We are proud to be an ISO 9001 certified system quality management company and we are determined to create value in every customer relationship. We do that through collaboration, innovation, process improvements, and exceptional workmanship.