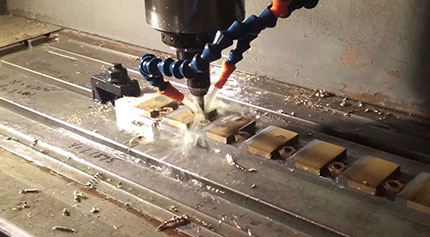
CNC machining, also known as Computer Numerical Control machining, is a subtractive manufacturing process in which material is precisely removed from a workpiece using computer-controlled machines to achieve the desired final shape. It includes CNC milling, CNC turning, and so on. This technology is critical to modern manufacturing because it allows for the production of complex and high-precision parts in a variety of industries. As the world prioritizes sustainability, the demand for renewable energy sources such as wind and solar power is increasing rapidly. To meet this demand, efficient and dependable manufacturing processes are required. This article investigates how CNC machining benefits the green energy industry by examining its key benefits and the wide range of applications it serves in producing the components that power renewable energy solutions.
Advantages of CNC Machining for Green Energy
Advantage 1: Precision and Accuracy
Computer-controlled Accuracy: Unlike traditional machining methods, which rely on manual operation, CNC machining uses computer programs to control every aspect of the cutting process. This translates to extremely precise movements of the cutting tools, ensuring that parts are machined to exact specifications with minimal deviation.
Repeatability and Consistency: CNC programs can be replicated flawlessly, ensuring consistent part dimensions and tolerances throughout production runs. This consistency is critical for green energy systems, where components such as wind turbine blades or solar panel frames must work flawlessly together under extreme conditions.
Advantage 2: Material Versatility
Metals for Durability and Strength: CNC machining excels at processing metals such as steel, aluminum, and titanium. These materials are required for the construction of durable and long-lasting components in wind turbines (gearboxes, shafts), solar power plants (frames, heat exchangers), and hydropower stations (turbine runners, control gates).
Plastics for Lightweight Efficiency: CNC machining can precisely machine plastics suitable for green energy applications. For example, lightweight but strong composites can be machined into wind turbine blades, reducing weight and improving energy capture. Specific plastics can also be used for solar panel components due to their insulating properties.
Advantage 3: Rapid Prototyping
Swift Iteration and Testing: CNC machining enables the rapid development of prototypes based on new designs. Compared to traditional methods, CNC machining significantly reduces lead times, allowing engineers to test and refine their ideas much faster. This rapid iteration cycle accelerates the development of innovative green energy components.
Design Optimization Through Physical Testing: CNC machined prototypes offer a physical representation of a new design concept. Unlike simulations, physical prototypes enable real-world testing under simulated operating conditions. This enables the early detection of potential design flaws or areas for improvement, resulting in more efficient and optimized green energy solutions.
CNC machining machine
Advantage 4: Complex Component Manufacturing
Unmatched Precision for Intricate Features: CNC machining provides unrivaled precision, allowing for the creation of parts with intricate features and tight tolerances. This is critical for components such as turbine nozzles, where complex flow channels play an important role in energy conversion efficiency. Traditional manufacturing methods may struggle to provide the required level of detail and precision for these features.
Multi-Axis Machining for Geometric Freedom: CNC machining, unlike traditional methods that are limited to specific tool movements, makes use of multiple axes. This allows the cutting tool to move along multiple axes at the same time, making it possible to create complex three-dimensional shapes. This is critical for components such as solar panel heat exchangers, which have intricate internal channels for efficient heat transfer.
Advantage 5: Cost-Effectiveness
Reduced Material Waste: CNC machining employs computer-controlled toolpaths, which reduce material waste during the manufacturing process. This is especially useful for expensive materials commonly used in green energy components, such as high-grade steel or carbon fiber composites. Reduced waste means lower overall production costs.
Scalability for Production Needs: CNC machining is fundamentally scalable. The same program can be used to create a single prototype or hundreds of identical parts for mass production. This eliminates the need for large investments in additional equipment or tooling to meet increased production demands, making it a cost-effective solution for both scenarios.
CNC-Machining-Steel-Parts
XTJ is a leading OEM Manufacturer that is dedicated to providing one-stop manufacturing solutions of Machining 6061 Aluminum from prototype to production. We are proud to be an ISO 9001 certified system quality management company and we are determined to create value in every customer relationship. We do that through collaboration, innovation, process improvements, and exceptional workmanship.lication: Automotive industry, Bicycle and motorcycle, Door and windows and furniture, Household appliance, Gas meter, Power tool,LED lighting, Medical instrument parts, ect.
Applications of CNC Machining in Green Energy
Wind Power
Wind turbines are the workhorses of wind energy generation, and CNC machining is essential in creating various components that ensure their efficient operation. Below are some specific examples:
Wind Turbine Blades: Wind turbine blades, which are perhaps the most recognizable component, benefit greatly from CNC machining. These massive structures necessitate complex aerodynamic profiles to maximize wind capture and energy conversion. CNC machining’s ability to handle large workpieces while maintaining precise blade geometry is critical.
Gear Housings: Wind turbines use a complex gearbox system to increase the rotational speed of the turbine shaft, generating electricity. CNC machining is used to create the strong gear housings that enclose these gearboxes. Precision machining ensures perfect alignment of gears and shafts, reducing friction and increasing power transmission efficiency.
These are just a few examples, and CNC machining is used to manufacture a wide range of other wind turbine parts, including electrical components and fasteners. Its precision, versatility, and ability to handle various materials make it an essential tool in the wind energy industry.
Solar Power
Solar energy is an important part of the green energy landscape, and CNC machining contributes significantly to the production of various components in solar power systems. Here’s how this technology promotes solar energy generation:
Photovoltaic (PV) Cell Frames: These frames house the solar panels, shielding the sensitive photovoltaic cells from environmental damage. CNC machining enables the creation of these frames from lightweight yet strong materials such as aluminum. The precise machining ensures that the panels fit perfectly within the frame and allows for efficient heat dissipation, resulting in maximum solar cell performance.
Heat Exchangers: Heat management is critical for achieving peak solar cell efficiency. CNC machining enables the manufacture of intricate heat exchangers for solar thermal power plants. These exchangers have complex internal channels that maximize heat transfer from the solar collectors to the working fluid, resulting in an efficient conversion of solar thermal energy to electricity.
Tracking System Components: Many solar panel arrays use tracking systems to optimize sun exposure throughout the day. CNC machining is used to manufacture various components for these tracking systems, including gearboxes, shafts, and mounting brackets. The precise machining ensures that the tracking system runs smoothly, allowing the panels to precisely follow the path of the sun for maximum energy capture.
These are just a few examples; CNC machining is used in a variety of other solar energy components. Its ability to handle a wide range of materials, create complex geometries, and ensure precise dimensions makes it an invaluable tool for increasing efficiency and reliability in solar power systems.
Hydropower
Hydropower continues to be a significant contributor to renewable energy generation, and CNC machining is critical in creating various components for efficient water utilization in hydropower plants. Here’s an overview of some key applications:
Turbine Housings: These sturdy structures house turbines that harness the power of flowing water to generate electricity. CNC machining enables the manufacture of these housings from high-strength materials such as steel or stainless steel. Precision machining ensures that water flows smoothly through the turbine, reducing energy losses and increasing power generation efficiency.
Shafts and Runners: The turbine’s rotating shafts transfer energy from the water to the generator. CNC machining enables the manufacture of these shafts with tight tolerances and high surface finishes. This reduces friction losses and ensures smooth rotation, resulting in maximum power output.
Guide Vanes and Stay Rings: These components are essential for efficiently directing water flow toward the turbine runner. CNC machining allows for the creation of components with precise geometries and smooth surfaces. This optimizes water flow through the turbine, reducing turbulence and increasing power generation efficiency.
Here are some of the ways CNC machining benefits the hydropower industry. Its ability to handle tough materials, achieve tight tolerances, and create intricate geometries makes it an indispensable tool for ensuring efficient and dependable hydropower generation.
CNC machining parts
Conclusion
Precise components are essential for efficient green energy systems. CNC machining ensures consistent and precise part creation, thereby improving the performance of wind turbines, solar panels, and hydropower components. The ability to handle a wide range of materials, from strong metals to lightweight composites, allows engineers to select the best material for each component, resulting in efficient and functional green energy systems. Intricate components are frequently required for green energy systems. CNC machining addresses this challenge by creating complex shapes and features, allowing for the production of these critical parts.
XTJ is a leading OEM Manufacturer that is dedicated to providing one-stop manufacturing solutions of Machining 6061 Aluminum from prototype to production. We are proud to be an ISO 9001 certified system quality management company and we are determined to create value in every customer relationship. We do that through collaboration, innovation, process improvements, and exceptional workmanship.lication: Automotive industry, Bicycle and motorcycle, Door and windows and furniture, Household appliance, Gas meter, Power tool,LED lighting, Medical instrument parts, ect.