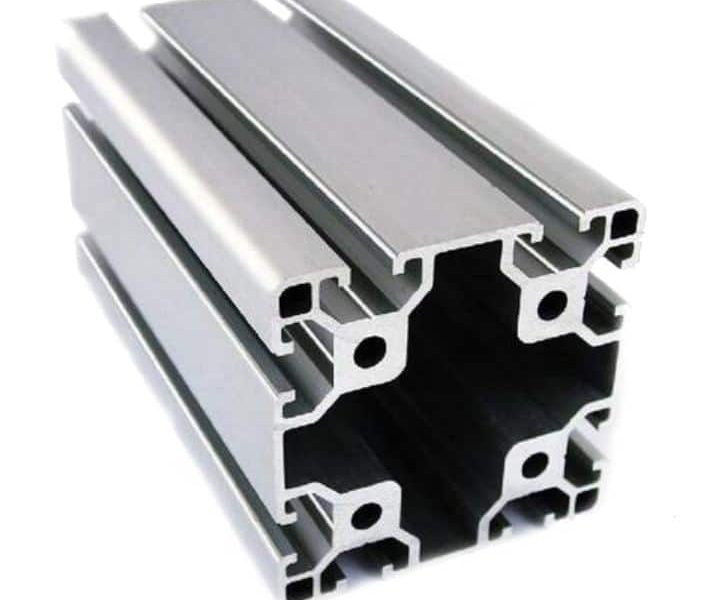
Table of Contents
How to Reduce the Cost of Sheet Metal Fabrication For CNC Machining Combining Parts?
Sheet metal rapid prototyping, among other techniques, as a way to save costs when designing parts. The versatility of sheet metal has made it a low-cost alternative in the custom manufacturing or rapid prototyping, where manufacturers purchase only the needed amount of material.
The Best efforts are aimed at the material itself, the manufacturing process used, design modifications, and finishing choices. Here we explain the various ways prototype manufacturers can use to save the cost of sheet metal fabrication.
Sheets With Standard Gauges And Sizes
Standard gauge and size sheets are less costly and more effective for low-cost rapid prototyping compared to special gauge sheets. Common gauge rapid prototyping designs use thinner materials that can be easily bent and cut to fit the intended shapes and geometric conformations.
Comparatively, using sheets with variable gauges and sizes may not only be costly but also increase the costs of resources used by prototype manufacturers during fabrication. For instance, standard stainless and standard-type magnetic stainless are both inexpensive sheet alternatives that offer high strength and corrosion resistance properties to the rapid prototype manufacturer. Depending on the standard sheet metal properties, the prototype manufacturer can effectively decide which parts to manufacture with each sheet metal type. Similarly, standard gauge materials such as aluminum 6061-T6 and steel CRS1008 are commonly stocked compared to specialized gauge materials. In turn, they attract no additional specialized acquisition fees to purchase.
Simpler Angle Bends
Complicated prototype designs are more expensive. Simpler and cost-effective prototypes can be achieved by reducing angle bends. Bends may distort the part because they stretch the sheet metal. The 4T convention requires that a bend is four times the thickness of the material used. Also, employing simpler but effective designs helps reduce the number of welds, cuts, and bends that are linked to high costs.
More cost-effective prototype designs employ consistent bend radius throughout the part while avoiding non-essential features like a blind hole and machined pockets. These pockets can be avoided by using press brakes that create a bend via linear punch. This approach can help reduce setup during machining and enforce rapid prototyping. Simpler and smaller bends are also linked with prototyping service accuracy.
Further, simpler geometrical conformations require and support the use of standard tooling. Most tooling warehouses make tools with specifications that support internal bend radii of between 0.30 inches and the thickness of the material. On the other hand, using specialized tools to achieve specific bend radii geometry may be costlier.
Collectively, maintaining simpler angles and bends during sheet metal fabrication ensures reduced material and manufacturing costs,
while guaranteeing rapid prototype manufacturing through reduced lead times.
Combining two or more parts can save the number of sheets used in fabrication. Parts can be combined through bends and joints to form a single and equally effective prototype. Other than the number of sheets used in fabrication, less time is spent on the fabrication of individual parts, ensuring rapid prototyping services.
Effective consolidation of several pieces to form a single part is an essential step in enforcing rapid prototyping. The step reduces the need for screws and fasteners while reducing costs associated with fabrication and quality control. Similarly, with parts consolidation less time may be spent during fabrication, thereby speeding up the process. For instance, recent developments in the aerospace parts industry have seen prototype manufacturers combine more than 20 pieces to form a single fuel nozzle, reducing its weight and related costs by 25%.
On the other hand, it is important to consider how combining sheet metals to achieve certain material thicknesses may affect the tolerance and performance of the prototype.
Reducing Tight Tolerances
Sheet metal fabrications involving tight tolerance may require the prototype manufacturer to use expensive materials and techniques. Additionally, tight tolerances are linked with more radii, holes, and distances, which are likely to inflate the fabrication costs.
During rapid prototyping services, it is commended that tight tolerances are only assigned to mission-critical parts. In aircraft manufacturing, for instance, all parts that are strictly regulated and essential for the optimal functioning of the plane are considered mission-critical. Considering the distribution of tolerances between mission critical and standard parts can save costs off the fabrication process.
The flexibility of tolerance is important in helping prevent delays in the prototyping services and standardization of costs. Tight tolerances can be minimized by using standard tolerances in all other non-critical parts of the prototype without significantly affecting the performance of the prototype or part.
Finishing Options That Minimize Costs
Sheet metal fabrication costs can be minimized by using low-cost finishing options following the rapid prototyping services. These services are meant to achieve the desired color and texture of the parts at reduced costs. Without appropriate finishing, the parts may be damaged and operate less efficiently than intended. It is essential that prototype manufacturers consider and weigh the cost of various finishing options. In prototyping, the appearance of the item may not be a priority, therefore it is commended that the manufacturer delays finishing techniques such as silk screening to minimize the fabrication costs.
Plating options can be used to prevent metal sheet erosion and maintain the part’s value and functioning. Passivation prevents the corrosion of stainless steel elements of the prototype and part. Prototype manufacturers can use powder coating to achieve texture and multicolor finishing and ensure the durability of the part. Silk screening helps with customized or complex design finishing. Where necessary, comparing and considering the various finishing options can help save overall cost of fabrication.
Conclusion
Overall, saving costs of sheet metal fabrication during parts design requires that the prototype manufacturer considers the type of material they use, modifications of prototype design, and prototyping and finishing techniques. Using standard gauge and size and simple designs offers a low-cost alternative for rapid prototyping services. From a design perspective, combining pieces to form a single part reduces the number of materials used. More importantly, working with an expert fabricator may help identify effective low cost approaches to the use of sheet metal fabrication in prototype manufacturing services.