CNC Milling is a high-precision industrial technology used to fabricate parts from a variety of materials, from metal to plastic. The computer numerical control milling machines are equipped with programs for automated cutting and computer-controlled servo systems that guide the machine to cut a workpiece at the exact desired location in a smooth and precise manner. The automotive, aerospace, medical and more industries have all been revolutionized by the high precision and consistent results that this type of machining provides.
In order to perform CNC milling, a variety of tools are required, including a CNC milling machine, computer software, and raw materials. The following article will provide you with an in-depth guide to the CNC milling process.
What is CNC Milling and How Does it Work?
CNC milling is a computer-controlled machining process that uses a rotating cutting tool to remove material from a workpiece. The cutting tool is usually mounted on a spindle and moves in a linear or circular motion while the workpiece is mounted on a table and is fed into the cutting tool.
CNC machines are operated by computer programs that tell the machine what to do. The programs are written in CNC languages, which are similar to regular programming languages but with a few differences. The most common one is G-code. These programs tell the machine how fast to move, what direction to move in, and when to stop. Most machines will have many more options than just these simple ones. Some machines have a touch screen that shows the program on the screen instead of writing it down and is used to edit the program if mistakes are made.
CNC milling machines can perform a variety of milling operations, including end milling, face milling, and slot milling. End milling is a versatile and powerful process, capable of cutting slots, shoulders, flats, and complex 3D shapes. Face milling on the other hand is used to produce a wide variety of flat surfaces on workpieces with large diameters. While slot milling can be used to create grooves and pockets in workpieces for mating components and other purposes. We’ll discuss these types of CNC milling operations in more detail in the following paragraphs.
The Different CNC Milling Operations
There are a variety of different CNC milling processes, each of which can be used for different applications. Here is an overview of the most common CNC milling processes.
Turn Milling
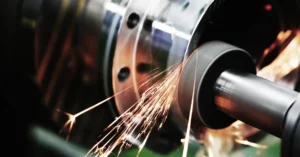
Turn-milling is a versatile machining operation in which a workpiece is held in a chuck and rotated while a milling cutter is fed into it as it proceeds by removing material. The amount of material removed can be controlled by the feed and speed rate of the milling cutter.
This type of CNC turning operation consists of two steps that can be repeated multiple times on the same part while using different tooling in each one of them. The first step is to turn the workpiece on a lathe which creates the cylindrical shape, and the second is the milling of the piece and creating the desired product.
The rotation during the turn-milling process creates a helical path which makes the shape of the cutting edge of the cutting tool best suited to the respective milling operation. It is used to create threads, grooves, and other internal features on a workpiece.
Chamfer Milling
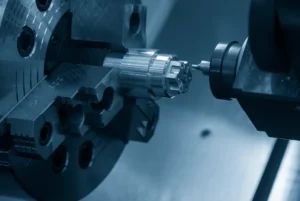
Also referred to as chamfering, it is the process of a small angled cut of material from the edge of a workpiece to achieve a gentle surface called a chamfer. As a result, the two-dimensional chamfer develops a series of angles creating a smooth surface which is generally used to prepare the edges of a workpiece for welding or brazing.
This type of CNC milling process is useful in a wide array of applications and industries. Chamfer milling tools give boards and other materials a smooth, curved edge – perfect for any architectural, engineering, or carpentry project. The medics and electronic engineers are also on hand to create safe and smooth angled edges on the components.
There exist various types of chamfer milling, some of the most common are Square Corner Milling, Outside Corner Milling, Inside Corner Milling, Flat Bottom Milling, and Chamfer Face Milling.
Slot Milling
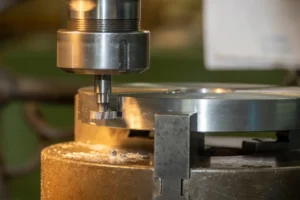
Slot milling is a type of CNC milling operation where a rotating cutting tool is used to remove material from a workpiece by moving it in and out of a slot. It is specifically used to create keyways, slots, or pockets.
What differentiates it from the other types of CNC milling operations is its ability to cut deeper slots or pockets than what can be achieved with end milling for example. In addition to that, this CNC milling process often results in a cleaner and better surface finish.
Slot milling cutting tools are incredibly versatile. With multiple teeth mounted in a circular pattern on a spindle, they can machine solid-jaw mandrels, guide bars, and flat parts from metal stock. Not only that but they can also cut grooves and recesses, score and cut, drill holes, make round holes, form rectangular, square, and hexagonal slots and pocket openings, and mill the faces of pins and dowels.
Profile Milling process
Profile milling is a CNC machining process used to create intricate three-dimensional surfaces on a workpiece. This tool can be used to create features such as slots, pockets, and contours. The milling operation is generally performed by a multi-axis milling machine that has a milling cutter rotating around the workpiece. The cutter carves through the material, following the tool path as it moves.
Profile milling can be used for three main types of operations:
Roughing
Roughing operations are intended to downsize the thickness of stock in large enough sections to remove excess material from inside or outside of the part. The holes on the face of the workpiece require an end mill that cuts on the periphery or the side of the cutter. The mill that is commonly used in this type of operation is the “peripheral end mill.”
Semi-finishing
Center-cutting tools are used on semi-finishing machines to cut around the holes where they will be located. This allows for more precise placement of the holes before the semi-finishing tools cut the parts.
Finishing
It is the process of reducing the amount of material removed in roughing, making way for the finishing operations. And it is usually performed using a small finishing end mill. Different machines should be used for roughing and finishing, and an optimized cutting tool should be used for each operation to achieve more precise results.
Face Milling
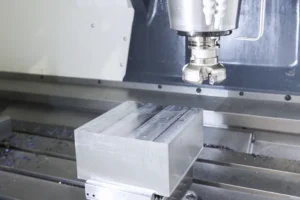
Face milling is the process of machining flat surfaces on a workpiece. A face mill cuts flat surfaces on the workpiece by feeding the workpiece against a rotating cutter with many cutting edges. This is different from drilling, where only one hole is created at a time.
Face milling consists of four steps:
- Before you can start face milling, you need to prepare and set up your material on a vertical milling machine. The workpiece must be secured firmly to the table of the machine to ensure a precise and successful operation.
- Next, you need to position the spindle of the machine in such a way that it is perpendicular to the surface of the workpiece.
- After properly positioning the cut, you will then adjust the feed. The pace of the headstock is also adjusted to perform a proper cut. The feed can be adjusted by the external spindle handles.
- You can then finally process by machining. In order to produce the desired form and shape of the workpiece, it is necessary to make multiple passes with the cutter. The final product will be cut along the bottom of the pattern that you drew. You will produce multiple cuts before achieving the desired result.
Shoulder Milling
Shoulder milling is a type of CNC milling operation in which the cutter is mounted on a spindle and cuts along the perimeter of the workpiece. The cutter is usually stationary and the cut is completed by tilting the tool spindle along a straight vertical axis. The most common shoulder angle is 90 degrees, but other angles may be used depending on the application.
The purpose of a shoulder CNC milling machine is to produce flat, angular surfaces on the workpiece. What makes a shoulder mill cutter ideal for this job is the need for constant access to the workpiece surface and cutting tools. In contrast to chucking, the milling process cuts in a zigzag pattern rather than in a straight line.
Other CNC Milling Operations
In addition to the ones stated above, there are a number of other CNC milling operations that can be performed. These include:
Plain Milling
It is also sometimes called surface milling or slab milling. Plain milling is defined as milling flat surfaces with the cutter axis parallel to the surface being milled. Normally, plain milling is done with the workpiece surface mounted parallel to the surface of the machine table and the milling cutter mounted on a standard CNC machine arbor.
Form Milling
Form milling is the process of machining special contours composed of curves and straight lines, or entirely of curves, at a single depth of cut. The usual cutter has multiple teeth and rotates on an arbor, held in a spindle that is driven by the main spindle of the machine. The cutter teeth engage the workpiece and form chips that are removed by fluting (grooves) between the teeth.
Angular Milling
Angular milling is a type of milling operation in which the workpiece is fed at an angle relative to the cutter axis. The cutting action of the milling cutter produces chip shapes that are not perpendicular to the workpiece surface, which can create many different types of features on the workpiece. Angular milling can be used to create features such as slots, shoulders, and grooves.
The Different CNC Milling Machines
While all CNC milling machines share some basic features, there are also a number of unique features that make each machine ideal for specific applications.
Bed-type Milling Machines
A bed-type milling machine is a large, heavy-duty CNC milling machine used in metalworking and machining applications. This type of milling machine has a large, flat table that is moved in the X, Y, and Z directions to mill heavy-duty parts. These machines are typically used to mill large, heavy parts that cannot be milled on a smaller, lighter-duty machine. Bed-type milling machines are very accurate and have a very high tolerance for milling large, Irregular shapes.
The bed-type milling machine is a large, expensive piece of equipment that is generally used only in industrial settings. However, there are some advantages to using it over others. One advantage is that bed-type milling machines are more rigid than other types of milling machines, so they can handle heavy cuts and produce high-quality results. Also, bed-type milling machines have more “instantaneous” torque to allow for a higher cutting speed, making them ideal for projects that have repetitive cuts with small-time gaps.
A bed-type milling machine is one in which the spindle is mounted on a movable table that can slide back and forth in a horizontal direction, as well as move up and down. The table can also be rotated to allow for milling at different angles. These machines are typically used for larger milling jobs than those that can be done with a hand-held milling machine.
Knee-type Milling Machines
A knee-type milling machine is a type of CNC milling machine that has a vertically adjustable worktable that rests on a knee-like projection at the front of the machine. The worktable can be raised or lowered to accommodate different workpiece heights, and the quill (the part of the machine that holds the cutting tool) can be moved up and down to allow for different depths of cut.
Knee-type milling machines are one of the most versatile milling machines available. They can be used to perform a wide variety of operations, including slotting, angle milling, and drilling. However, they are not as accurate as some of the other types. This is because the table on a knee-type milling machine is not as rigid as on a vertical milling machine. This means that when the table is raised and lowered, some of the cuts made on the workpiece might not be exact enough.
Vertical Milling Machines
A vertical milling machine is a type of CNC milling machine where the spindle is oriented vertically. Milling cutters are held in the spindle and rotate on its axis. Typically the spindle can be extended, or the table raised or lowered to produce the same effect, allowing for plunge cuts and drilling. The vertical milling machine is well suited for smaller jobs, such as milling parts for prototypes or short production runs.
The vertical CNC milling machine has many advantages compared to alternative machining equipment. Some of which we mention:
- They take up less space in a shop because of their tall and thin shape.
- They can perform more than one operation at a time, such as drilling and milling.
- They are relatively inexpensive compared to their other CNC milling counterparts.
- Vertical CNC mills are easy to learn and operate.
However, compared to the horizontal milling machine, vertical mills are quite limiting and can only be used for certain applications. One disadvantage is that they tend to be slower because the cutters are spinning in a vertical orientation. This means that more time is needed to remove the same amount of material.
Horizontal Milling Machines

A horizontal milling machine is a type of milling machine that has its spindle aligned in a horizontal orientation. The spindle is parallel to the table and the machine has a cutting tool that is mounted on an arbor. The cutting tool and the table can both be moved in different directions. The machine can also be fitted with different attachments such as a rotary table or a dividing head.
This CNC milling machine is designed to remove material from a workpiece, and it can do so very efficiently. The horizontal milling machine can be used to create very precise and intricate parts. It is often used in the aerospace industry and other industries where extremely precise parts are required.
However, there are some potential drawbacks to using this type of machine. One downside is that horizontal CNC milling machines can be expensive to purchase and maintain. Additionally, these machines can be large and bulky, making them difficult to move around or transport. Another potential drawback is that horizontal CNC milling machines can generate a lot of noise and vibration, which can negatively impact the environment and neighboring properties.
Xin Tian Jian: Your one-stop custom CNC machining services
Xin Tian Jian is a leading custom manufacturing service provider. We offer a wide range of services, from CNC milling to surface finishing, so you can find the perfect fit for your needs. We have been ISO 90001-2015 certified and our quality management system has been assessed as meeting the requirements of the International Standard.
XTJ machining will provide your business with all kinds of CNC machining services. We specialize in high-precision CNC milling and can handle both challenging shapes and small, intricate parts. With up-to-date CNC machines and skilled engineers and technicians, we can help you produce customized products that are difficult for others to make for you.
In order to provide you with the best quality service, we offer free consultation services before you make your purchase. Our team of highly-skilled professionals will work closely with you to ensure that your specifications are met and your requirements are satisfied.
Request an online quotation in just a few minutes – all you need is to fill out the form on our website and our team will get back to you within 24 hours (usually much sooner!). You can also inquire about your quote by sending us an email.
FAQ
What is the difference between the CNC horizontal milling machine and the CNC lathe machine?
CNC horizontal milling machines are used to create parts with complex shapes and features, while CNC lathe machines are used to create parts with symmetrical features.
Is a CNC milling machine the same thing as a CNC routing machine?
No, a CNC milling machine is not the same thing as a CNC routing machine. While both machines are computer-controlled, a CNC milling machine uses rotating cutting tools to remove material from a workpiece, while a CNC routing machine uses a router bit to cut material.
What is the difference between CNC milling and CNC turning?
CNC milling is a process where a material is cut using a rotating cutting tool, whereas CNC turning is a process where a material is cut using a rotating workpiece. Both processes can be used to create parts with a variety of shapes and sizes.
How many spindles are there in a CNC milling machine?
There are typically three to five spindles in a CNC milling machine. These spindles can be positioned around the workpiece to mill features from multiple sides at the same time.
