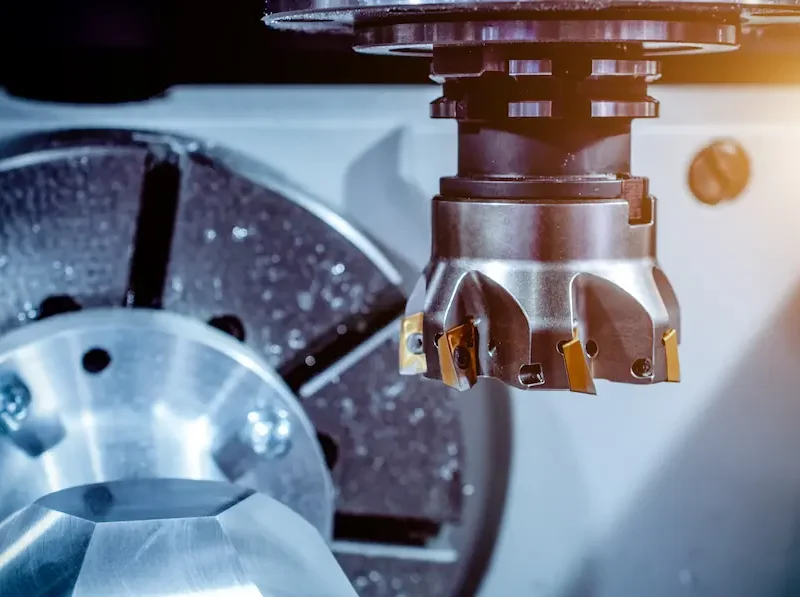
Face milling is a process that is used to create smooth, flat surfaces on materials like wood, metal, and plastic. While it is typically performed using a CNC machine, it can also be done manually. When done correctly, face milling can produce outstanding results. However, there are a few things you need to keep in mind to optimize your process. Here are some tips to help you get the most out of your face milling operations.
Table of Contents
A General Overview of the Face Milling Process
Face milling is the technique of machining flat surfaces on a workpiece. The face mill is mounted on a spindle that rotates in a horizontal plane. The cutting edge of face milling cutters is a set of teeth that are arranged in a helical pattern. The teeth provide the cutting action on the face mill, which removes material from the workpiece. Face milling cutters can also be used to create rabbets, chamfers, and other features on the face of a workpiece.
The face milling process involves four steps:
- Preparing the workpiece
Before beginning the face milling operation, you need to set up your material on a vertical milling machine. The workpiece must be secured firmly to the table of the machine.
- Spindle positioning
Next, you need to position the spindle of the machine in such a way that it is perpendicular to the surface of the workpiece.
- Adjusting the feed and the speed of the headstock
You will adjust the feed in order to properly position the cut. The pace of the headstock is also adjusted to perform a proper cut. The feed can be adjusted by the external spindle handles.
- Machining.
In order to produce the desired form and shape of the workpiece, it is necessary to make multiple passes with the cutter. The final product will be cut along the bottom of the pattern that you drew. You will produce multiple cuts before achieving the desired result.
Different Types of Face Milling Cutters
There is a wide range of tools that can be used for face milling, depending on the desired surface finish. End mills, fly cutters, and shell mills are some of the most commonly used face mills.
End Mills
An end mill is a cutting tool that has multiple flutes and can be used to cut in different directions. It is often used for face milling operations to create intricate patterns and designs. End mills can be found in a variety of sizes, from very small to very large.
Fly-Cutters
Fly cutters are generally used to face mill. This is done by holding the fly cutter at a slight angle to the workpiece and moving it across the surface of the workpiece in a sweeping motion. Fly cutters consist of a body that holds – (generally) one- or more inserts. The fly cutter is held in the chuck of a milling machine and rotated at high speed as the operator guides the tool along the surface of the workpiece.
Shell Mills
A shell mills is a type of milling cutter that is commonly used for face milling. Shell mills have large, circular cutting edges that are located on a shell-shaped body. The advantage of using shell mills is that they are very versatile and can be used on a variety of materials. Other joint uses for shell mills include shoulder milling, and high-feed milling.
Face milling tools are an important part of the machining process, and the right tool choice can make a big difference in the quality of the finished product. There are a variety of face milling tools available on the market, and the best tool for the job will depend on the specific application. When choosing a mill, it is important to consider the material to be machined, the desired finish, and the speed and feed rate required.
How to Optimize Your Face Milling Operations
When face milling, it is important to use the correct tooling and set up to ensure that the cutting process is efficient and accurate. There are a few things to keep in mind when face milling to optimize the process:
- Many times, face milling takes place after the part has been machined with a drill or press. Be sure to set up your part before milling so that your finish is already ready.
- Use a dedicated setup for face milling. This will allow you to reduce your cycle time and increase the accuracy of the part.
- Choose the correct material for the work piece. The right material depends on the type of cut to be performed.
- Use the correct feed and speed rate for the workpiece. A slow and steady avoids chatter and ensure a smooth finish.
- Use the right finish. As most finishing mills can be used for a wide variety of machining operations, it is important to understand the different finishes that the milling machine can produce to ensure proper machining.
- Check the tooling. Tooling can be expensive, so check your milling machine to ensure that it is capable of machining the workpiece at the required finish before buying it.
- It is important to use a sharp cutter. A dull edge cutter will result in a poor finish and can cause tool breakage.
- Support the workpiece properly to avoid vibration and ensure an accurate cut.
The Takeaway
Face milling is a process that is used to create smooth, flat surfaces on materials like wood, metal, and plastic. It can either be performed using a CNC machine or manually. While most face mills can be used for a wide variety of machining operations, it is important to understand the different finishes that the milling machine can produce to ensure proper machining. The article discusses the ins and out of face milling and provides some tips to help you get the most out of your machining project.