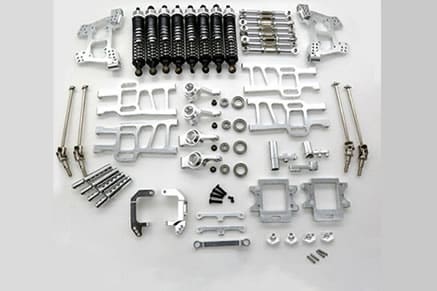
Table of Contents
What is Mold Making?
Mold making is the process of designing and creating molds that serve as the blueprint for producing identical copies of a particular object or part.
These molds, crafted with high precision and attention to detail, are used in various manufacturing processes to replicate products in materials ranging from metals and plastics to ceramics and composites.
The essence of mold making lies in its ability to produce high volumes of parts with uniformity, efficiency, and intricate detail, making it a cornerstone in the manufacturing sector.
What is the History of Mold Making?
Delving into the history of mold making takes you on a journey back to the Bronze Age, where the first instances of this craft were applied to create weapons, jewelry, and artifacts of significant cultural importance.
This ancient technique, which has evolved through the centuries, forms the bedrock of modern manufacturing processes. From the rudimentary use of stone and clay molds to the sophisticated application of steel and silicone molds in today’s industries, mold making has been quintessential in shaping human progress and innovation.
The art of mold making has been pivotal in various civilizations, with the Egyptians and Sumerians advancing the craft by creating molds for bricks, pottery, and metal objects.
The progression from sand casting in ancient times to the development of lost-wax casting during the Middle Ages further demonstrates the evolution of mold making techniques.
The Industrial Revolution marked a significant turning point, introducing mechanization into mold making and laying the groundwork for modern processes like injection molding and CNC machining.
In recent times, the advent of 3D printing has revolutionized mold making, offering unprecedented flexibility and precision.
This technology allows for the rapid prototyping of molds, significantly reducing the time and cost associated with traditional mold making methods. Today, mold making stands as a testament to human ingenuity, bridging the past and the future of manufacturing.
How Does Mold Making Work?
Understanding how mold making works illuminates the intricate process behind the creation of countless products you interact with daily.
At its core, mold making involves the creation of a negative space or cavity that perfectly mirrors the desired object’s shape.
This cavity then serves as a template to produce multiple copies of the object, whether it be in plastic, metal, or any other material.
The process is meticulously planned and executed, ensuring the highest quality and precision in the final products.
The main stages involved in mold making include:
Design and Conceptualization: The process begins with a detailed design phase, where engineers and designers collaborate to create a 3D model of the part to be produced. This model serves as the blueprint for the mold, incorporating all necessary features such as cavities, cores, and ejector systems, while also considering the thermal and mechanical stresses the mold will undergo.
Material Selection: Choosing the right material for the mold is crucial. Factors such as the intended use of the mold, the material of the final product, and the production volume play significant roles in this decision. Common materials include steel for high-volume production molds, aluminum for quicker heat dissipation, and silicone or rubber for flexible mold parts.
Machining and Fabrication: Once the design is finalized and materials selected, the physical creation of the mold begins. Techniques such as CNC machining, EDM (Electrical Discharge Machining), and 3D printing are employed to fabricate the mold. This step requires precision to ensure that the mold accurately reflects the design specifications.
Surface Finishing and Polishing: After machining, the mold undergoes surface finishing to enhance its quality and functionality. Polishing is essential for achieving the desired surface finish on the final product, especially for molds used in injection molding, where the smoothness of the part is critical.
Assembly and Testing: The individual components of the mold are assembled into a complete mold tool. This assembly must be precise to ensure that the mold operates correctly and safely. The assembled mold is then tested to verify that it fills correctly, cools appropriately, and ejects the part without issues.
Trial Runs and Adjustments: Before going into full production, trial runs are conducted to identify any potential problems with the mold or the molding process. This stage allows for the fine-tuning of the mold, adjusting temperatures, pressures, and cycle times as necessary to ensure optimal performance.
Final Inspection and Approval: The last step involves a thorough inspection of the mold and the trial parts produced to ensure they meet all specifications and quality standards. Once the mold passes this final inspection, it is approved for full-scale production.
The seamless integration of these stages results in the efficient production of high-quality molds, capable of creating precise and consistent copies of virtually any object. The versatility and adaptability of mold making underscore its indispensable role in today’s manufacturing landscape, catering to industries ranging from automotive to healthcare, consumer goods, and beyond.
What is the Required Equipment and Machines for Mold Making?
Whether you’re creating a simple silicone mold for a bespoke piece or intricate injection molds for mass production, understanding the machinery and tools essential for mold making is crucial.
This foundation ensures that your mold making endeavors are successful, efficient, and capable of producing high-quality molds that meet specific manufacturing requirements.
CNC Milling Machines: The backbone of mold making, CNC milling machines are used to carve, drill, and shape molds out of metal blocks. They offer unmatched precision and control, making them indispensable for creating complex molds with tight tolerances.
EDM Machines (Electrical Discharge Machining): EDM is crucial for creating intricate details and achieving precise dimensions within molds, especially for hard metals that are difficult to machine with traditional methods. This process uses electrical discharges to erode material in a controlled manner.
3D Printers: Revolutionizing prototype mold making, 3D printers allow for the direct fabrication of mold components from digital models. They’re particularly useful for creating complex geometries that are challenging to achieve with traditional machining.
Lathe Machines: Used for producing symmetrical mold components, lathe machines cut, sand, drill, and deform the material, offering versatility in mold making processes, especially for cylindrical parts.
Grinding Machines: These machines provide the finishing touches to molds, ensuring smooth surfaces and precise dimensions. They’re used to grind, polish, and finish metal mold components.
CAD/CAM Software: Computer-Aided Design (CAD) and Computer-Aided Manufacturing (CAM) software are critical in the modern mold making process. They allow for the precise design and programming of machining operations, ensuring the molds are made to exact specifications.
Tool and Die Making Equipment: These specialized tools are used for cutting, shaping, and finishing molds and include everything from hand tools to die sets. They’re essential for adding fine details and for the hands-on finishing work on molds.
Mold Assembly Tools: Once individual mold components are machined or printed, assembly tools are needed to accurately put together the final mold. This includes clamps, presses, and screws, which ensure that molds are assembled securely and accurately.
Heat Treatment and Tempering Equipment: Heat treatment and tempering are processes used to increase the strength and durability of metal molds. This equipment is vital for prolonging the life of molds that will be used in high-pressure injection molding.
Polishing and Finishing Tools: For achieving the perfect surface finish on molds, polishing and finishing tools are used. These can range from simple hand tools for manual polishing to sophisticated automated systems for high-gloss finishes.
Inspection and Measurement Tools: Precision is key in mold making. Tools such as micrometers, calipers, and coordinate measuring machines (CMM) are used to inspect and measure mold components, ensuring they meet all specified dimensions and tolerances.
Safety Equipment: Safety cannot be overlooked. Protective gear, including gloves, goggles, and respirators, is essential to protect mold makers from the hazards associated with machining, chemicals, and heat used in the mold making process.
What are the Supported Materials for Mold Making?
Mold making, a foundational process in manufacturing, leverages a wide range of materials to meet diverse production needs. Each material offers unique properties that make it suitable for specific types of molds and casting processes. Understanding the characteristics and applications of these materials is crucial for choosing the right one for your mold making project.
Metals
Steel (including tool steel and stainless steel): Known for its durability and resistance to wear and tear. Steel molds are predominantly used in high-volume production settings, especially for injection molding and metal casting processes. They are capable of withstanding high temperatures and pressures, making them ideal for producing metal, plastic, and rubber parts.
Aluminum: Offers a good balance between cost and performance, with excellent thermal conductivity and lighter weight compared to steel. Aluminum molds are often used for injection molding and blow molding, suitable for lower volume production where faster cooling times are beneficial.
Beryllium Copper: Valued for its superior thermal conductivity and strength, beryllium copper is often used in areas of molds that require precise temperature control. This material is commonly found in injection molds to improve cooling times and reduce cycle times.
Plastics and Polymers
Epoxy Resins: Epoxy molds are used for low-volume production and prototypes due to their ease of use and versatility. They are suitable for casting plastics, metals, and concrete, providing a good surface finish and detail.
Polyurethane Resins: Offer flexibility in hardness and are used for making molds that require a certain degree of elasticity. Polyurethane molds are commonly used for casting concrete, plaster, and some metals.
Silicone Rubber: Highly flexible and resistant to extreme temperatures, silicone molds are perfect for detailed and complex shapes. They are widely used in the food industry, special effects, and for casting resins, waxes, and metals.
Ceramics
Refractory Ceramics: These materials can withstand very high temperatures, making them suitable for metal casting molds, especially in foundry applications. They are used to create molds for casting steel, iron, and non-ferrous metals.
Composites
Fiberglass: Provides strength and durability, used for larger molds that need to be lightweight. Fiberglass molds are often used in automotive, marine, and aerospace industries for producing large panels and structural components.
Carbon Fiber: Offers exceptional strength and stiffness with minimal weight. Carbon fiber molds are used in high-performance applications where precision and durability are critical.
Others
Graphite: Utilized for high-temperature applications in metal casting, especially for precious metals. Graphite molds offer excellent surface finish and detail.
Plaster of Paris: A cost-effective material for temporary molds, suitable for casting ceramics and some metals. Plaster molds are used for prototypes and art projects.
Wax: Primarily used in lost-wax casting processes for creating detailed and complex shapes, especially in jewelry making and precision metal casting.
Additive Manufacturing Materials (for 3D Printed Molds)
Photopolymer Resins (for SLA/DLP printing): Ideal for detailed prototypes and complex designs. Photopolymer molds are used for small production runs and custom parts.
Thermoplastic Filaments (for FDM printing): Offers versatility and ease of use for creating prototype molds or low-strength parts.
Metal Powders (for SLS/SLM/DMLS): Enables the direct 3D printing of metal molds for small-batch production and complex geometries.
What is the Best Material for Mold Making?
Silicone rubber stands out for its versatility, excellent thermal stability, and non-stick properties, making it suitable for a wide range of applications, from intricate jewelry to food-grade containers. Its ability to replicate fine details and withstand repeated use without degrading makes silicone molds a top choice for professionals and hobbyists alike. Howver, the best material for mold making largely depends on the specific requirements of the project, including the type of product being cast, the desired finish, and the production volume.
What is the Cheapest Material to Make a Mold?
Plaster of Paris is often considered the cheapest material for making molds due to its low cost, accessibility, and ease of use. While not as durable as other materials, it is ideal for low-volume casting or prototyping where fine details are not crucial. Plaster molds are commonly used in art, education, and for casting decorative items, making it an economical option for projects where cost is a primary concern.
What are Various Manufacturing Processes That Utilize Mold Making?
There are many manufacturing processes that significantly benefit from mold making, demonstrating its versatility and indispensability in modern manufacturing.
Injection Molding: A paramount process where molten material, often plastic, is injected into a mold cavity to create parts with complex shapes. Injection molding is vital for producing a vast range of consumer and industrial products, from automotive components to household items.
Blow Molding: Employed to manufacture hollow plastic parts, such as bottles and containers. In blow molding, air is blown into a heated plastic tube, expanding it into the mold’s cavity to assume its shape. This process is crucial for the packaging industry.
Thermoforming: Involves heating a plastic sheet until it’s pliable, then stretching it over a mold and cooling it to form the desired shape. Thermoforming is widely used for making disposable cups, containers, and clamshell packaging.
Rotational Molding (Rotomolding): Used for creating large, hollow items like tanks, kayaks, and playground equipment. The material is heated inside a closed mold, which is rotated to distribute the material evenly and form the part.
Compression Molding: A method where material is placed into a heated mold cavity and then compressed to shape. It’s often used with thermosetting plastics and composites, suitable for making large, intricate parts such as automotive panels and electrical insulators.
Transfer Molding: Similar to compression molding but allows for more complex parts by transferring the material from a chamber into the mold under pressure. It’s especially beneficial for encapsulating parts or creating components with tight tolerances.
Casting: Encompasses a variety of techniques where a liquid material is poured into a mold and solidifies. Metal casting, including sand casting and investment casting, is essential for producing metal parts with intricate details for industries like automotive, aerospace, and construction.
Resin Casting: Involves pouring a liquid resin into a mold, where it hardens into a solid plastic part. Resin casting is ideal for small-batch production, prototypes, and artistic creations due to its detail and versatility.
Vacuum Forming: A simplified version of thermoforming, where a heated plastic sheet is sucked down onto a mold using vacuum pressure. This process is used for making lightweight, cost-effective parts such as product packaging and trays.
Die Casting: Metal casting that uses high pressure to force molten metal into steel molds. It’s particularly suited for producing high-volume metal parts with excellent surface finish and dimensional accuracy, commonly used in the automotive and consumer electronics sectors.
How Much Does Mold Making Typically Cost?
Mold making costs can vary widely based on the complexity of the design, the material used, and the manufacturing process selected.
At a glance, mold costs can range from a few hundred dollars for simple silicone or plaster molds to tens of thousands for intricate, high-volume injection molds made of steel or aluminum.
Here are the 5 most important factors that influence the end price:
Material Selection: The choice of material affects the overall cost, with metals like steel and aluminum being more expensive than silicone or plaster.
Mold Complexity: Complex molds with intricate details, undercuts, or multiple cavities require more time and precision to create, increasing the cost.
Production Method: Techniques like CNC machining or 3D printing may have higher upfront costs compared to traditional handcrafting methods.
Size and Volume: Larger molds or those intended for high-volume production are more costly due to the increased material usage and the time required for machining and finishing.
Finish and Tolerance Requirements: High-precision molds with tight tolerances and smooth finishes require additional processing, contributing to higher costs.
For example, a small, simple silicone mold might cost as little as $100-$200, whereas a complex metal mold for injection molding could easily exceed $10,000 or more, depending on the specifications.
How Long Does Mold Making Typically Take?
On average, producing a simple mold might take a few days to a week, while more complex molds, especially those requiring precision machining or intricate details, can take several weeks to several months to complete.
The timeframe for mold making can vary significantly because of these 4 factors:
Design Complexity: More detailed and complex designs take longer to develop and manufacture.
Manufacturing Process: Some processes, like 3D printing, can produce molds faster than traditional machining or handcrafting.
Material Curing and Setting Times: Materials like silicone or resin may require significant curing time, adding to the project timeline.
Revisions and Prototyping: The need for design adjustments or prototyping can extend the timeline, especially if multiple iterations are needed to achieve the desired outcome.
What Are the Design Considerations for Making a Mold?
When designing a mold, several crucial considerations ensure the final product meets all requirements for functionality, quality, and manufacturability. Here are practical tips and design considerations for creating an effective mold:
Material Selection: Choose a mold material that suits the production volume, the material being molded, and the required surface finish. For high-volume production, durable materials like steel or aluminum are preferred.
Part Design Compatibility: The design of the part must be compatible with molding processes, considering factors like draft angles, wall thickness uniformity, and the presence of undercuts.
Mold Flow Analysis: Utilizing software for mold flow analysis can predict potential issues with material flow, helping to optimize gate location and minimize defects.
Cooling System Design: A well-designed cooling system is vital to control the mold temperature, reduce cycle times, and ensure uniform part cooling.
Ejection System Placement: Proper placement of ejector pins or other ejection mechanisms is necessary to prevent damage to the part during removal from the mold.
Surface Finish Requirements: The desired surface finish of the final product affects the mold design, including the choice of mold material and any coatings or treatments needed.
What are Some Common Problems in Mold Making?
Mold making can encounter several problems that affect the quality of the final product. Here are some main issues and their solutions:
Air Traps: Air trapped in the mold can cause voids in the final part. A solution is to design the mold with proper venting or vacuum systems to allow air to escape.
Warping: Differential cooling can lead to warping or deformation. Optimize the cooling system and consider the material’s shrinkage properties during the mold design phase.
Surface Imperfections: Defects such as sink marks or surface blemishes can occur. To prevent this, you can adjust mold temperature, pressure, and cooling times and ensure uniform wall thickness in the part design.
Mold Misalignment: This can lead to parting line defects or flash. Always ensure high precision in mold manufacturing and assembly to maintain alignment.
XTJ is a leading OEM Manufacturer that is dedicated to providing one-stop manufacturing solutions from prototype to production. We are proud to be an ISO 9001 certified system quality management company and we are determined to create value in every customer relationship. We do that through collaboration, innovation, process improvements, and exceptional workmanship.