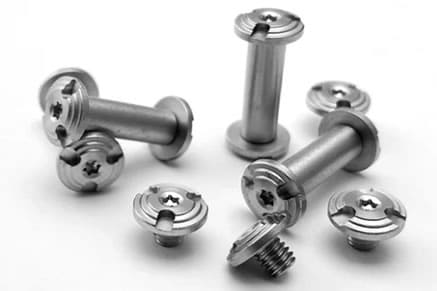
How to make CNC Rivet Holes
Rivet Holes come in various materials, such as aluminum, stainless steel, and copper. Likewise, they are essential in multiple sectors, such as bridge construction, skyscrapers, ships, airplanes, cars, and buildings. The process of joining materials with rivets is known as riveting.
Although riveting is not as common today, it remains widely utilized. Given its significance, it’s crucial to understand everything about rivets and riveting. This guide offers comprehensive insights into CNC rivet holes, providing tips for perfect rivet holes, techniques for CNC hole drilling, precise machining of rivet holes, and fabrication tips.
Close up view of CNC machine creating perfectly machined rivet holes
Importance Of Precision In Riveting
Precision in riveting, especially concerning CNC rivet holes, is essential for the structural integrity, endurance, and safety of assembled structures. When CNC hole pattern design and rivet hole dimensions are not accurately executed, it can lead to a range of issues, compromising the final product’s quality and functionality. Here are some key reasons why rivet hole accuracy and precision in riveting, guided by CNC hole machining tools and precision drilling techniques, are crucial:
Structural Integrity:
Rivets, especially in aerospace, automotive, and construction, are the backbone of structures. Accurate rivet hole dimensions and CNC hole pattern design are vital. Any discrepancies or misalignment due to imprecise riveting can weaken the structure, posing potential failures and safety hazards.
Leak Prevention:
In critical applications such as aircraft fuselages or hydraulic systems, rivet hole tolerances and precise CNC hole machining tools ensure a tight and secure seal. Any deviations in rivet hole dimensions or surface finish could lead to leaks, causing performance issues or system failures.
Aesthetics and Finish:
CNC hole machining tools and precision drilling techniques contribute significantly to the appearance of the final product. Properly aligned rivet holes with precise dimensions and surface finish enhance the overall aesthetic, especially in industries like automotive manufacturing or architectural design.
Efficiency and Cost-Effectiveness:
Accurate CNC hole programming and precision in riveting reduce the need for rework or repairs, saving time and costs in production. CNC hole machining tools ensure efficient material use, minimizing waste and optimizing production processes.
Factors Affecting Rivet Hole Quality
The quality of CNC rivet holes is super important for the strength, reliability, and safety of assembled structures. These CNC rivet holes are like the starting point for rivets to hold materials together really tight. They must be suitable to make sure the final thing is solid. Lots of stuff affects how good these holes turn out, and that impacts how well the riveting works.
Finished riveting process showcasing perfectly aligned rivet holes
Material Stuff:
The kind of material being drilled plays a significant role in how well the CNC rivet holes turn out. Metals, plastics, or composites each have their things to consider. If the material is hard or soft, it decides what drill bits and CNC hole tools to use, which can affect how the holes look.
Tools and Equipment:
Good-quality drill bits and CNC hole tools, following CNC Hole Drilling Techniques, are crucial to making precise and accurate rivet holes. Tools that are sharp and in good shape give cleaner holes, but if they’re old or not in good shape, the holes might not be so good.
Drilling Speed:
How fast the drill bit spins (drilling speed) and how fast it moves into the material (feed rate), following Precision Rivet Hole Machining, really matters. The proper speeds and feeds help prevent the material from getting too hot, changing shape, or making rough holes.
Using Coolant or Lubrication:
Having the proper coolant or oil is essential to cool things down when drilling, reducing friction and making the tools last longer. If there’s not enough oil or coolant, things can heat up too much, tools can wear out, and the holes might not look so good.
Shape of the Drill Bit:
The shape of the drill bit, following riveting hole perfection, like how sharp the point is, the design of the flutes, and how the cutting edge is made, all affect the holes. If the drill bit isn’t the proper shape, it might wander off course, make holes in the wrong place, or leave chips behind.
Rivet Hole Specifications
Rivet hole specifications play a pivotal role in the success of any riveting operation, ensuring that the drilled holes meet the required standards for size, depth, and accuracy. These specifications are carefully defined based on the type of materials being joined, the size and type of rivets to be used, and the structural requirements of the assembly. Here are the key aspects to consider when defining rivet hole specifications:
Size and Diameter:
The diameter of the CNC rivet holes is a critical factor, directly impacting the fit and effectiveness of the rivets. Specifications for hole size are typically determined based on the diameter of the rivet shaft or shank. It is essential to achieve the precise diameter to ensure a secure and snug fit for the rivet.
Depth:
The depth of the rivet hole is another crucial specification that affects the strength and integrity of the joint. It is determined by factors such as the material thickness being joined and the length of the rivet. Ensuring the correct depth allows for sufficient penetration of the rivet, creating a strong and durable connection between the materials.
Hole Pattern and Layout:
In applications requiring multiple CNC rivet holes, the pattern and layout are specified to ensure proper distribution of the load and even stress distribution across the joint. This includes considerations for the spacing between holes, the arrangement of rows or groups of holes, and any specific geometric patterns required for the assembly.
Tolerances:
Rivet hole tolerances define the acceptable range of variation in hole dimensions while still maintaining the desired fit and functionality of the rivet. Tight tolerances are crucial for precision assemblies, ensuring consistent and reliable results. Factors such as material properties, drilling techniques, and tooling capabilities influence the specified tolerances.
Surface Finish:
Rivet hole surface finish specifications ensure that the drilled holes have the required smoothness and cleanliness for proper rivet insertion and bonding. Smoother surfaces reduce the risk of stress concentrations and improve the overall integrity of the joint. Factors such as deburring, cleaning, and coating processes are considered when defining surface finish specifications.
Material Considerations:
The type of material being drilled also influences Rivet hole specifications. Variations in material hardness, brittleness, and thermal conductivity impact the drilling process and the final dimensions of the holes. Specifications must account for these material properties to achieve accurate and reliable results.
CNC Riveting Process
The CNC riveting process is a modern and efficient method for securely joining materials in industries such as aerospace, automotive, and manufacturing. This process relies on computerized precision and automation to achieve accurate and reliable results. Here’s a step-by-step overview of the CNC riveting process:
Design and Planning:
Engineers begin by creating detailed plans for the assembly, specifying the types of rivets, their placement, and the dimensions of the CNC rivet holes. CNC hole pattern design is crucial for defining the precise layout of the rivet holes on the materials.
Material Preparation:
Before CNC riveting begins, materials are prepared by cutting, shaping, and cleaning to ensure proper fitment and alignment of the CNC rivet holes. Rivet hole specifications are closely followed to meet the correct dimensions and specifications for each hole.
CNC Programming:
The CNC machine operator programs the equipment based on the design plans, inputting coordinates, depths, and patterns for the CNC rivet holes. CNC hole programming tips are utilized to optimize tool paths, speeds, feeds, and other parameters for efficient and precise drilling.
Tool Selection:
Selecting the right drill bits or cutting tools is crucial, depending on the material and specifications of the CNC Rivet Holes. CNC hole machining tools are chosen to match the material properties and dimensions required for the rivet holes.
CNC Drilling:
With the CNC machine programmed and tools ready, drilling begins as the equipment precisely moves the drill bits to create the CNC rivet holes according to the programmed instructions. Precision drilling techniques ensure accurate hole depths, diameters, and alignment for each rivet.
Rivet Placement:
Once drilling is complete, the rivets are inserted into the freshly machined CNC Rivet Holes. The CNC machine may automate this process. The CNC hole placement guide ensures the rivets are positioned accurately for a secure and reliable joint.
Riveting Process:
Riveting begins with the rivets in place, using methods such as pneumatic or hydraulic machines. The CNC machine controls the force applied during riveting to ensure consistent and optimal results.
Quality Inspection:
After riveting, a thorough inspection is conducted to check the quality of the joints, verifying rivet positions, dimensions, and overall integrity. Any deviations from the specifications or defects are identified and addressed to meet the required standards.
Finishing Touches:
Additional steps, such as surface finishing or sealing, may be performed to enhance durability and aesthetics. The rivet hole surface finish is carefully considered to ensure proper bonding and sealing of the rivets.
Advanced Techniques for CNC Rivet Holes
Advanced techniques for CNC rivet holes take drilling to the next level, offering precise, efficient, and versatile solutions for all kinds of jobs. These methods, driven by CNC programming and top-notch technology, guarantee top-notch quality, accuracy, and consistency when riveting. Here’s a rundown of these advanced techniques:
High-Speed Machining (HSM)
HSM techniques mean faster cutting speeds and feed rates, slashing down machining times without losing accuracy. This is particularly beneficial for large-scale production runs where efficiency is crucial. With HSM, you also get smoother finishes and longer tool life, making CNC rivet holes look and perform their best.
Gun Drilling
Gun drilling is a unique technique for making deep, exact holes. It uses a long, thin drill bit with coolant flowing through to flush out chips. CNC machines set up for gun drilling can make long, precise CNC rivet holes, often used in industries like aerospace and medicine.
Custom Tooling
Tailoring tools for specific jobs can seriously boost CNC riveting. Custom drill bits, reamers, countersinks, you name it—all made to fit the job perfectly. With custom tools, you get better efficiency, accuracy, and overall top-quality CNC rivet holes.
Laser Drilling
Laser tech for drilling CNC rivet holes gives unmatched precision and speed. It’s all non-contact, meaning you can make tiny, super-precise holes with ease. It is often used in industries like aerospace, medicine, or electronics for delicate hole patterns and micro-machining.
Tips for Optimal Hole Size and Depth
Understanding Material Properties
When working with different materials like metals such as aluminum or steel, it’s crucial to consider their hardness and density. This knowledge helps in selecting appropriate cutting speeds and feeds to achieve the desired hole size and depth. For softer materials like plastics or composites, a different approach is often necessary to prevent deformations or rough edges around the holes.
Selecting the Right Drill Bit
The choice of drill bit geometry and size is fundamental for achieving precise hole dimensions. Drill bits must align with the material being drilled to ensure clean cuts and accurate depths. Factors such as flute design, point angle, and cutting-edge geometry play a significant role in matching the drill bit to the material’s properties. Utilizing CNC hole machining tools tailored for specific materials further enhances accuracy and minimizes errors.
Employing Precision Drilling Techniques
Implementing precise drilling techniques is essential for controlling both the size and depth of the holes. Maintaining consistent pressure and feed rates throughout the drilling process ensures uniform results. Techniques such as peck drilling, where the drill bit is intermittently retracted to clear chips, can significantly improve hole quality and prevent overheating, especially in deep-hole drilling applications.
Optimizing CNC Hole Programming
Effective CNC hole programming is vital to ensure the machine drills precisely as required. Programming the CNC machine with accurate tool paths, depths, and speeds is essential for achieving the desired hole dimensions. Scrutiny of the program helps avoid errors in hole size or depth during the drilling operation.
Implementing Quality Control Measures
Regularly checking hole sizes and depths during drilling operations is critical for maintaining accuracy. Measuring tools such as calipers or micrometers are invaluable for verifying dimensions periodically. In-process inspection tools, such as laser measurement systems or probing devices, offer real-time feedback on hole quality, enabling immediate adjustments if deviations are detected.
Conducting Test Drilling for Verification
Before proceeding with drilling final components, conducting test drilling on scrap materials is advisable to ensure proper setup. This allows for adjustments to be made without impacting the actual parts. Precise measurement of the test holes using precision tools ensures they meet the required specifications. Once the drilling parameters are confirmed, proceed to drill the final components, periodically verifying hole sizes and depths to maintain quality assurance.
Here’s a table summarizing the finishing and quality control of CNC Rivet Holes:
Aspect Description
Inspecting Rivet Holes -Regular inspection of hole dimensions using callipers or micrometres- In-process inspection tools like laser measurement systems for real-time feedback- Ensuring hole sizes and depths meet specified Rivet Hole Specifications
Ensuring Longevity and Durability – Proper surface finishing techniques, such as deburring for smooth and clean holes- Applying protective coatings or treatments to prevent corrosion and increase durability.- Conducting thorough quality checks post-riveting to ensure the integrity of joints- Use of appropriate materials for longevity, considering factors like strength and wear resistance
Conclusion
This comprehensive guide serves as your best resource for achieving perfect CNC rivet holes. By employing precise CNC hole drilling techniques, adhering to rivet hole specifications, and implementing precision drilling techniques, you can ensure accuracy and consistency in your riveting operations.