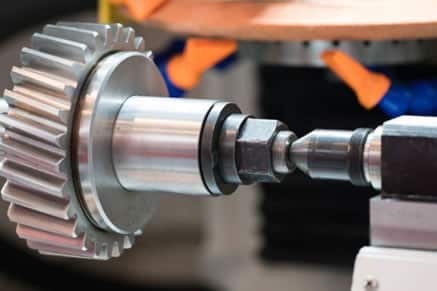
The CNC machining process offers many advantages because it is automated and uses computer-controlled machine tools to fabricate parts from raw materials. The process can produce many different parts with varying levels of complexity. CNC machining is often used in the aerospace, automotive, and medical industries, where specific parts must meet stringent specifications and tolerances in manufacturing processes.
CNC machining has made it possible to create objects a hundred times faster than a few decades ago.
y
Table of Contents
what is CNC machining and how does it work?
This article explores all you need to know about CNC machining, what it is, how it is done, different types and the benefits of the process.
What is CNC Machining?
CNC machining is a type of automated machining process that uses computer numeral control technology to shape an object or a part by removing material from a workpiece until the desired shape is achieved.
CNC stands for Computer Numerical Control. It means utilizing computerized software to control how a machine moves and operates.
It works by converting a digital model of a part into a sequence of computer instructions that control the actions of the machining tools to achieve the desired output
CNC machining equipment works on a variety of parts, such as metals, metal alloys, wood, stone, and more. The size of machine tools can vary based on the specific part that requires manufacturing.
Since it is computer-controlled, CNC machining can deliver superior levels of versatility, efficiency, and precision relative to other common manufacturing methods. This makes it a popular manufacturing choice for a vast range of industries and applications.
Who Invented CNC Machining?
Removing material using milling tools to shape an object has been an ongoing practice since ancient times. When it comes to the modern history of CNC machining though, the process of controlling machine tools through numerical control was invented in 1949 by John Parsons at MIT.
Development of CNC Machining
In 1949, MIT conducted a research project for the US air force to use motorized methods for creating helicopter blades and aircraft engines and frames. This is what gave rise to CNC technology.
Richard Kegg, in 1952, further improved the numerical control machining process, which led to CNC milling machines.
Due to the absence of computers, the automated nature of early CNC machining processes was made possible with the help of punched tape. With the advent of digital computing in the 1960s, the punched tape was replaced with computerized controls.
How Does CNC Machining Work?
CNC machining relies on computer programs to create the layout of the process in which the machine tool should function. Since users cannot directly communicate with the machine tools, Computer-Aided Design (CAD) software is used.
CAD software creates the 2-dimensional and 3-dimensional models for the required CNC machined parts. With this design, the machine knows what the final part looks like.
The computerized controls do the calculation required for removing material, so the workpiece looks like the final part created in the CAD software.
Let us go through the breakdown of various processes that occur during CNC machining.
The Four Stages of CNC Machining
CNC machining occurs in four stages:
Stage 1: Creating the CAD Model
Before CNC machining begins, the 2D or 3D model of the final design is required. This model is created in CAD software. There are many CAD software programs available online, free and paid.
Creating CAD models is not difficult and can easily be learned. However, some complex parts might require more experience with CAD, for which expert designers can be hired.
Stage 2: Converting CAD Model to CNC File
No CNC machine understands CAD language directly. CNC machines only recognize movement based on coordinates. Therefore, the CAD model must be converted to a CNC understandable file called G code.
Many CAD software programs can write the output file directly in G code by using the particular setting before saving the file.
In other cases, converting the CAD design to G code will require dedicated software called Computer Aided Manufacturing (CAM). CAM software is a very functional tool when it comes to the automation of machine processes.
Besides using CAM software, many simple free tools can convert simple CAD designs to G code with the click of a button. However, they don’t have the vast suite of features that CAM software offers.
Stage 3: Configuring the CNC Machine
Before starting manufacturing processes, the CNC machine must be set up the right way.
Think of this as configuring the printer before you print something. You need to feed the printer with pages and check specific settings. CNC machines operate similarly.
Before machining begins, there are many setup processes to complete. For instance, you must ensure the workpiece is properly positioned on the machine. The dies must also be set correctly, and other position settings.
Stage 4: machining operation execution
Once the configuration stage is complete, the machine operation can begin. For this, you can execute the program on the display panel of the CNC machine.
Depending on what you design, you might have to go through various program prompts to choose different types of settings and options.
Once the CNC program is executed, the machine keeps going till the end of the program. It only stops if switched off by the operator or in the case of an unexpected error or power disruption.
Main Terminologies in CNC Machining
It is crucial to be familiar with CNC machining terminology in this field. Some common CNC-related terms include:
Computer-Aided Design (CAD)
Computer-Aided Design is the software that creates the graphic representation of the required final part in 2D or 3D. Generally, complex parts are produced by breaking them into small parts, each having its own CAD model.
AutoCAD and FreeCAD are two of the most popular CAD applications, with the latter being completely free.
Computer-Aided Manufacturing (CAM)
Computer Aided Manufacturing (CAM) software generates CNC programs that a machine can understand. These programs help automate different types of machines, including CNC machines.
CAM software works together with CAD programs to execute operations using a CNC machine. Most quality CNC machines come with complementary CAM software.
Distributed Numerical Control (DNC)
In a Distributed Numerical Control (DNC) setup, multiple machine tools can be connected to a central server. The central server processes the design files and sends commands to each machine tool separately.
DNC is utilized when the individual CNC machine memory is too small to process the software. It can also be used where multiple numerical control machines require synchronized working for faster operational capabilities.
Manufacturing Data Collection (MDC)
Manufacturing Data Collection (MDC) is what it sounds like. Manufacturing Data Collection software collects data from machines and operators about the different manufacturing information generated in real time.
This information helps manufacturers to improvise on the existing production line. It also points out the causes of any delays and loss in production.
What are G-code and M-code?
G-code and M-code are files that a CNC machine requires to operate. Each of these has its own importance, which we will go through one by one:
G-code
The ‘G’ in G-code refers to Geometry, making G-code a Geometric code. G-code is an alphanumeric command that tells the CNC machine how to move.
The X, Y, and Z references in G-code refer to the axes of movement, and the number pertains to the value in that particular axis. N refers to the line number.
Some particular codes refer to specific operational capabilities of the machine, such as adjusting the spindle speed or turning the spindle on and off.
M-Code
M-codes are miscellaneous machine codes that perform the non-cutting actions of the CNC machine. These include starting and stopping different programs, controlling the coolant flow, or adjusting the behavior of machining tools.
What are the Different Types of CNC Machining Processes?
A CNC machine is not one specific machine, as it is a group of different types of CNC machines working on various machining processes. Some of the most popular CNC machining operations include:
CNC Milling
CNC milling is one of the most popular types of CNC machining processes. In fact, many professional machine shops often use a CNC machining and CNC milling process interchangeably. Face milling and peripheral milling are two of the most frequently used CNC mill applications.
In a CNC milling machine, rotating cutting tools move relative to the workpiece to remove material.
The cutting tool (also called a milling tool) is fixed on a spindle that can rotate. The rotation and movement of the spindle give CNC milling machines the ability to perform three or more axes milling operations.
CNC Drilling
The CNC drilling process is a lot simpler than using milling tools or the turning process. In CNC drilling, the workpiece is held stationary while a drill bit moves over the workpiece and creates holes.
The purpose of drilling holes might be to add screw bolts, aesthetic requirements, or any other use.
CNC Grinding
CNC grinding machines use a rotating flat abrasive wheel for removing material from rough workpiece surfaces. This machine process is usually applied to create a smooth-finished part. The grinding wheel rotates at a very high speed.
CNC Routing
CNC routers are very similar to CNC milling machines. The main difference is that in a CNC router, the workpiece is always stationary, and the cutting tool moves in X, Y, and Z dimensions. CNC routers create faster cuts than milling machines without compromising accuracy and design complexity.
Types of CNC Machines
Besides the various types mentioned above, there are other CNC processes too. Some independent fabrication machines are integrated with a CNC for automatic movement. Some of these additional CNC machines are:
Broaching
Broaching utilizes a toothed cutting head to create niche shapes on a workpiece. Broaching cuts are very consistent and highly accurate. These machines can be linear or rotary (with a rotating toothed cutting tool).
Sawing
Sawing utilizes a toothed blade for creating straight, linear cuts. The cuts are created by the removal of material due to friction with the saw blade. When operated with a CNC, this process is usually applied for the automated cutting of materials.
Honing
Honing is similar to grinding in that it is generally used for the secondary finishing of a material. In the honing process, an abrasive stone or wheel is used for controlled grinding of the workpiece, creating the desired shape, size, or finishing.
Lapping
Lapping is also similar to grinding. But, lapping uses an abrasive paste, powder, or mixture instead of a grinding wheel to create a smooth surface finish. The abrasive mixture is inserted between two materials (one of which is the workpiece) and then rubbed against each other.
CNC lathes
CNC lathes are primary shaping tools used for machining metal or wood. In a lathe machine, the workpiece is rotated around a central axis, and the machining head moves linearly along the surface. CNC lathes can perform various functions, such as cutting, drilling, sanding, knurling, facing, and more. CNC lathes perform much better than manual lathes.
Plasma Cutters
Plasma cutters are an evolved form of cutting technology, using a high-temperature plasma jet to cut material. The plasma is created by an electrical arc, so this method applies to conductive materials only.
Laser Cutters
Laser cutters use a laser beam to cut through a material. Unlike plasma cutting, laser cutting is not limited to the cutting of electrically conductive materials. Laser beams can cut through anything by adjusting the laser parameters.
Flame Cutters
Flame cutting uses an Oxy-acetylene (also known as Oxy-fuel) gaseous mixture to cut through metals. When the Oxy-fuel stream is narrowed and ignited, it creates an ultra-high temperature flame that can easily cut through metal.
Press Brakes
The purpose of Press Brakes is to bend metal plates and sheets. The material is placed between a V-shape or a U-shape die. Then the die is pressed, resulting in the bend as required.
Electric Discharge Machines (EDM)
Electrical Discharge Machines (EDMs) are used for cutting conductive materials. In EDM, electrical pulses are emitted by a cutting head near the material, which creates an electrical arc. This arc melts and removes the material at the required position resulting in a cut.
Water Jet Cutters
Waterjet cutters utilize ultra high-pressure water for the cutting action. These cutters can cut through anything: metal, alloy, wood, stone, or glass. The water jet stream is controlled by CNC and moved according to the software.
Selecting the right CNC machine for the job
When making CNC machined parts, it is important to figure out which type of machine is most suitable for the parts in question.
Every machine has its pros and cons, but it is difficult to find every kind of CNC machine in one place — except maybe at a machine trade show, or in a CNC shop willing to invest lots of money.
If the most suitable machine is not available, you need to find a way to make the parts with the machines that are available. Here are some explanations of vertical vs horizontal milling and turning machines.
Figuring out the best way to load the workpieces
When you have chosen the CNC machine to make your parts, the next step — before programing — is to find the best way to load your workpieces in order to gain the best machined result. I believe this stage is more important than making the tool paths, but in my experience, most machinists have a difficult time with it, and it prevents them from moving forward smoothly.
As a prototype machining company, we try to hire people who have an open mind and are able to find solutions in this area, since we come across different CNC parts every day. (Of course, some people quit the job within two weeks!) Check out the different CNC workholding methods.
XTJ is a leading OEM Manufacturer that is dedicated to providing one-stop manufacturing solutions from prototype to production. We are proud to be an ISO 9001 certified system quality management company and we are determined to create value in every customer relationship. We do that through collaboration, innovation, process improvements, and exceptional workmanship.
Knowing what type of cutting tool to use
After choosing the machines and deciding on the best way to make the parts, selecting the right cutting tools will help to achieve a tighter tolerance and better surface finish. In short, suitable cutting tools result in better components.
Here’s an example: milling ribs with draft might take hours using normal sphere cutting tools, but would require just a few minutes with a taper cutter.
So imagine how much time you could save when milling 10 pieces or more. Find out the differences between types of CNC cutting and machining tools.
What are the Advantages of CNC Machining?
CNC machining technologies have revolutionized the manufacturing industry by minimizing manual work and allowing for unparalleled levels of consistency and accuracy. It is often considered a modern boon due to its numerous advantages.
As a product designer, it is vitally important to know whether to stick with CNC machining or to design the parts for another manufacturing process.
Here is a brief overview of some of the key benefits:
Production Speed
Production speed is one of the primary reasons which led to the vast and rapid spread of CNC machining. With CNC machining, it is possible to speed up production exponentially since it removes the limitations of human labor.
Consistency
Computer Numerical Control machining ensures that all the parts created look and work the same. There is no possibility of human error. This leads to the fabrication of precision parts that serve their purpose as intended.
Reduction of Rejections
In conventional manufacturing processes using manual labor, there was a lot of human error, which resulted in rejections during quality control. This wasted a lot of time and resources. With CNC machining, the whole process is automated, which leads to fewer rejections.
Cost Saving
Labor costs include the salary paid to the labor, downtime during breaks, and the added benefits payments.
The accuracy, speed, efficiency, and automation of CNC machining reduce manufacturing costs by minimizing production times and labor hours. These savings can be passed along to customers, creating a competitive advantage and providing an opportunity for business reinvestment.
However, other factors affect CNC machining costs, like quantity, material selection, and geometry.
Material Versatility
CNC machining can be performed on practically any material with sufficient hardness.
Manufacturing Data Tracking
A CNC machine feeds manufacturing data that allows manufacturers to track the entire process for every part. They can learn about the exact machines every part went through during manufacturing. In case of a fault, the exact cause can be tracked immediately.
Accuracy
With CNC machining, it is possible to achieve accuracy on a micro level. Manufacturers can even push that limit with appropriate tools. Such a level of accuracy is not possible with manual operations.
XTJ is a leading OEM Manufacturer that is dedicated to providing one-stop manufacturing solutions from prototype to production. We are proud to be an ISO 9001 certified system quality management company and we are determined to create value in every customer relationship. We do that through collaboration, innovation, process improvements, and exceptional workmanship.
What Materials Can Be Processed By CNC Machines?
CNC machining enables working on a wide range of materials. In fact, you do not need various machines for CNC machining materials that are different. Most types of CNC machines support multiple materials allowing them to switch between producing different machine parts with a slight change of tooling.
Metals
Metal is one of the most common materials that undergo the CNC machining process. Its hardness makes using manually controlled machining long, arduous, and less precise. CNC machines provide the best and fastest way to work on metal parts.
Some of the metals that are used to manufacture parts with CNC machines are:
Aluminum: Aluminum is not just the most abundant metal on earth but also the most commonly used in CNC machining. Its high strength-to-weight ratio makes it ideal for lightweight parts that require decent strength.
Magnesium: Magnesium is most commonly utilized for creating the outer body of electronics. This is because Magnesium is 33% lighter than Aluminum, making it perfect for reducing the weight of electronics like laptops.
Titanium: Titanium is one of the toughest materials out there. It undergoes CNC machining for applications in aerospace, the military, and for any other high-grade requirement.
Cast Iron: CNC machining parts from cast iron is very useful as you can produce parts at twice the speed of producing parts using steel, with less wear resistance on tools.
Alloys
CNC machines can work on metal alloys just as well as metals. Here are the common alloys that go through CNC machining:
Stainless Steel: Stainless Steel is one of the more popular varieties of steel. Due to its hardness and other physical properties, it is always shaped by the CNC machining process.
Carbon Steel: Carbon steel is the most widely used alloy in the world. It is cheaper than stainless steel and has higher strength. CNC machines can shape carbon steel with high accuracy.
Brass: Brass is soft and corrosion-resistant. There are numerous varieties of brass with varying proportions of zinc and copper. All these varieties can be CNC machined.
Plastic
Many people are unaware of it, but CNC machining can also be used to shape plastic parts. Common plastics used in modern manufacturing include:
Nylon: Nylon is strong, flexible, and fire-resistant. Nylon CNC machined parts are sometimes used to replace some metal parts since Nylon also has good lubrication properties.
ABS: ABS plastics are often used for applications like injection molding due to their thermoplastic nature. However, for making prototypes, CNC machining ABS is the better way to go.
PMAA: PMAA Acrylic is strong, transparent plastic. Therefore, PMAA is used for replacing glass in items like optical equipment or food containers.
PEEK: PEEK is one of the most expensive plastics with exceptional temperature resistance and physical properties. CNC machining of PEEK finds applications in the aerospace and medical industries.
Wood
Wood is another common material used in CNC machining. Not only that, it is actually quite easy to machine due to its soft nature. The most common application is for making furniture.
What are the Applications of CNC Machining?
CNC machining has applications in every industry, from the creation of tools to the final end product.
Here’s an overview of some of the use cases of the CNC machining process:
Vehicles: CNC machining is utilized for making the frames, engines, and other small components of all types of transport vehicles, including cars, trains, and airplanes.
Metal Fabrication: The metal fabrication industry relies on CNC tools for all types of projects.
Electronics: The electronics industry also uses CNC machining for making appliance frames.
Research and Development: Since CNC machining can create anything based on a 2D or 3D digital model, it is the go-to method for making prototypes.
Defense: High-end CNC machines are used for heavy-duty defense operations, such as creating weapons, aircraft, and more.
Architecture: CNC machining is also used for creating art and decor pieces. For instance, the intricate stonework you see in kitchens is made using CNC-controlled waterjet cutting tools.
Robotics/automation: CNC machining allows for rapid prototyping with the ability to make quick and frequent modifications and sophisticated robotic parts, which are essential for success in the fast-growing and innovative robotics field.
Medical: CNC machining benefits the fast-paced medical device sector by enabling rapid prototyping for product testing and validation. It also delivers high-quality end-use components that are utilized in everything from orthotic devices to MRI machines.
XTJ is a leading OEM Manufacturer that is dedicated to providing one-stop manufacturing solutions from prototype to production. We are proud to be an ISO 9001 certified system quality management company and we are determined to create value in every customer relationship. We do that through collaboration, innovation, process improvements, and exceptional workmanship.