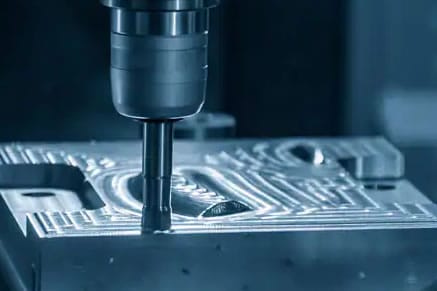
What is CNC Programming?
CNC programming is the process of creating a set of coded instructions, called a CNC machining program, that controls the operation of a CNC machine. These instructions are input into the CNC system and guide the machine’s movements to produce a desired part.
The CNC machining program consists of various function words and follows specific formats, such as ISO and EIA standards. CNC programmers must have a deep understanding of CNC machining principles, coordinate systems, program structure, and common CNC instructions.
Key Elements of CNC Programming
CNC machining program: A set of coded instructions that control the CNC machine’s movements.
CNC system: The hardware and software that interpret and execute the CNC machining program.
Function words: Words that define machine functions, such as movement, tool changes, and program loops.
Standards: ISO and EIA standards that ensure compatibility and consistency in CNC programming.
Machining principles: Understanding how CNC machines cut, shape, and form parts.
Coordinate systems: Coordinating the machine’s movements in relation to the workpiece.
Program structure: Organizing the CNC program to ensure efficient and accurate execution.
CNC instructions: Commands that control specific machine functions, such as speed, feed rate, and tool selection.
By mastering CNC programming, individuals can leverage the power of CNC machines to create complex and precise parts for various applications.
How to process CNC Programming?
CNC programming is a vital aspect of the CNC machining process. It involves using the G-code language to describe the shape, process, parameters, and auxiliary information of a part. The CNC programmer writes the program using specific function instruction codes and block formats.
Once the program is created, it is input into the CNC system for further processing. The program undergoes numerical calculation, tool motion trajectory calculation, and post-processing to generate a part processing program list. This list contains all the instructions necessary for the CNC machine to produce the desired part.
CNC programming can be done manually or automatically, depending on the complexity of the part. Manual programming requires the programmer to have in-depth knowledge of the G-code language and the ability to input the instructions accurately. Automatic programming methods, on the other hand, rely on advanced software that can generate CNC machining programs automatically. These methods are particularly efficient and reliable for parts with complex shapes.
Manual CNC Programming
In manual CNC programming, the programmer manually writes the program using the G-code language. They analyze the part requirements, determine the processing route, select the appropriate process parameters, and calculate the tool position data. The programmer must have a thorough understanding of the CNC machining principles, coordinate systems, program structure, and common CNC instructions.
Automatic CNC Programming
Automatic CNC programming utilizes computer software to generate CNC machining programs automatically. The software takes into account the part design, material, and specific machining requirements to create an optimized program. This method is highly efficient and reliable, especially for parts with intricate geometries and non-circular curve profiles.
How Many Types of CNC Programming?
When it comes to CNC programming, there are two main types: manual programming and automatic programming. Let’s take a closer look at each method and understand their differences.
1. Manual Programming
Manual programming involves completing the CNC process manually, without the use of advanced computer software. In this method, the programmer carefully analyzes part drawings, determines the processing route, selects process parameters, and calculates tool position data. Manual programming is suitable for simple parts and point processing operations, where the programming requirements are less complex.
2. Automatic Programming
On the other hand, automatic programming utilizes advanced computer software to generate CNC machining programs automatically. This method is highly efficient and reliable, especially for complex parts with intricate geometries and non-circular curve profiles. Automatic programming software takes input from the programmer and uses algorithms to generate the necessary CNC program, reducing the time and effort required.
With automatic programming, CNC programmers can streamline the programming process and handle complex part geometries more easily. However, it is important to note that manual programming still plays a crucial role, particularly for simpler parts and specific point processing operations where human decision-making is essential.
It’s important for CNC programmers to have a good understanding of both manual and automatic programming methods, as they provide different approaches to programming and cater to different machining requirements. Ultimately, the choice between manual and automatic programming depends on the complexity of the part and the desired level of automation.
Now that we’ve explored the two main types of CNC programming, let’s move on to the role of a CNC programmer and how they work in the next section.
What is a CNC Programmer?
A CNC programmer is a skilled individual responsible for preparing CNC machining programs that meet the specific requirements of a part. These professionals work in manufacturing companies and specialize in programming complex and challenging parts. CNC programmers play a critical role in the production process, ensuring that the machines operate efficiently and accurately.
The Role of a CNC Programmer
A CNC programmer possesses a range of skills and knowledge that enable them to excel in their role. These skills include:
A strong understanding of 3D space: CNC programmers must be able to visualize parts and understand their spatial relationships in order to program the machines correctly.
Visualization abilities: CNC programmers need to interpret and analyze part drawings to determine the best machining strategy and tool paths.
Normal vision: Clear and accurate vision is essential for CNC programmers to identify and inspect small details and dimensions on part drawings and finished products.
Flexible limbs: CNC programmers may need to physically access and operate CNC machines, requiring flexibility and dexterity.
Strong computing skills: CNC programmers work extensively with computer software and programming languages to write and edit CNC machining programs.
Read Achieving Precision: 6 Key Skills for Intermediate CNC Machinists
In addition to these skills, CNC programmers are responsible for selecting the appropriate tools, fixtures, and processing equipment for each job. They write and edit CNC machining programs, ensuring that the instructions are accurate and efficient. CNC programmers also analyze and control the machining quality of the parts, making adjustments as necessary to achieve the desired outcome.
CNC Programming Skills
To excel as a CNC programmer, individuals must have a solid foundation in CNC programming skills. These skills include:
Proficiency in G-code language: CNC programmers must be fluent in the G-code language, which is used to describe the part’s shape, process, parameters, and other necessary information.
Expertise in program structure: CNC programmers must understand the structure and format of CNC machining programs, ensuring that their programs are well-organized and error-free.
Knowledge of CNC machining principles: A deep understanding of CNC machining principles, such as coordinate systems and common CNC instructions, is crucial for CNC programmers.
Problem-solving abilities: CNC programmers must be able to identify and resolve programming issues and errors, ensuring that the CNC machines operate smoothly.
Attention to detail: Precision and accuracy are essential for CNC programmers to program the machines correctly and achieve the desired machining results.
With these skills and knowledge, CNC programmers contribute to the efficient and accurate production of parts in various industries.
How Do CNC Programmers Work Step by Step ?
CNC programmers play a critical role in the CNC machining process. They are responsible for creating the CNC machining programs that control the movements of the CNC machine and ensure the production of accurate and precise parts. Let’s take a closer look at the step-by-step process that CNC programmers follow:
1. Analyzing Part Diagrams
CNC programmers start by analyzing the part diagrams, which provide essential information about the dimensions, features, and machining requirements of the part. By carefully studying the part diagrams, programmers can understand the machining process and select the most suitable tools, fixtures, and processing equipment.
2. Numerically Calculating Tool Paths
Next, CNC programmers numerically calculate the tool paths that the CNC machine will follow to create the desired part. They consider factors such as cutting speeds, tool diameters, and cutting depths to determine the most efficient tool paths that will produce high-quality results.
3. Writing Machining Programs
Based on the analyzed part diagrams and the calculated tool paths, CNC programmers then write the machining programs using the appropriate programming language, such as G-code. These programs contain a series of instructions that specify the machine movements, tool changes, feed rates, and other parameters necessary to produce the part accurately.
4. Inputting Programs into the CNC System
Once the machining programs are written, CNC programmers input them into the CNC system. This can be done manually by entering the program code directly into the machine’s control panel or through computer-aided manufacturing (CAM) software, which generates the CNC program file for transfer.
5. Conducting Inspections and Trial Cutting
Before running the CNC machine at full production, CNC programmers conduct inspections and trial cutting to ensure that the programs are functioning correctly and producing the desired results. They carefully monitor the machining process, make any necessary adjustments, and verify the accuracy of the machined parts through measurements and quality control procedures.
6. Ensuring Machining Quality
Throughout the machining process, CNC programmers continually analyze and control the quality of the parts being produced. They monitor factors such as surface finish, dimensional accuracy, and overall part quality, making adjustments as needed to maintain the highest standards of precision and consistency.
By following this comprehensive process, CNC programmers ensure that the CNC machine operates effectively and produces parts that meet the required specifications. Their expertise in programming, tool selection, and quality control is essential for achieving optimal results in CNC machining.
CNC Programming Software
When it comes to CNC programming, having the right software can significantly enhance efficiency and precision. There are several popular CAD/CAM software programs that are widely used by CNC programmers for CNC programming. These software programs offer advanced features such as 3D parametric design, analysis, and manufacturing capabilities, making them ideal for creating complex CNC machining programs.
Some of the most commonly used CNC programming software programs include:
UG (Unigraphics): UG is a powerful CAD/CAM software that offers a comprehensive range of tools for designing and manufacturing parts. It provides advanced modeling, simulation, and machining capabilities, allowing CNC programmers to create accurate and efficient machining programs.
CATIA: CATIA is a versatile CAD/CAM software widely used in various industries, including aerospace, automotive, and industrial design. It offers a wide range of features for modeling, simulation, and machining, making it a popular choice among CNC programmers.
Pro/E (Pro/Engineer): Pro/E is another widely used CAD/CAM software that provides advanced tools for 3D parametric design and manufacturing. It offers features such as surface modeling, assembly design, and NC machining, making it an excellent choice for CNC programming.
Application:
Metal Machining: CNC machining centers have a wide range of applications in the field of metal processing. It can mill, drill, boring and other processing of various metal materials. Whether it is aluminum alloy, steel or copper, CNC machining centers can complete machining tasks with high speed and precision.
Plastic machining: CNC machining centers are also suitable for the field of plastic processing. It can be used for injection molding, extrusion processing, etc. of plastic parts. Whether it is ordinary plastic products or engineering plastic products, CNC machining centers are able to provide high-quality and high-precision machining services.
Wood processing: For the precision machining of wood, CNC machining centers are also a very suitable choice. It can be used for wood cutting, carving, slotting and other processing operations, and can be widely used in furniture manufacturing, wood carving art and other fields.
Precision parts machining: CNC machining centers are especially suitable for precision parts machining that requires high precision. For example, optical devices, molds, hardware, etc. CNC machining centers have high-precision positioning and repeatability, which can meet the strict requirements for precision and stability in these fields.
Rapid Prototyping: CNC machining centers play an important role in rapid prototyping. By using CAD software for design and programming, design drawings can be quickly transformed into physical products, thus speeding up the product development cycle.
In conclusion, CNC machining centers are suitable for a wide range of metal processing, plastic processing, wood processing, precision parts processing, and rapid prototyping. It provides reliable solutions for various industries through high-precision and high-efficiency processing, and promotes the technological progress and development of the manufacturing industry.