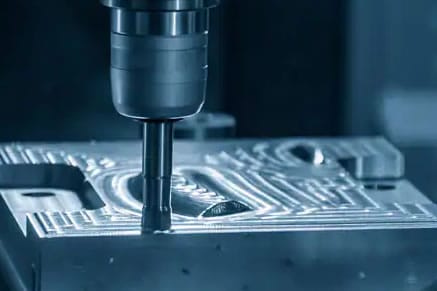
Table of Contents
What is CNC Routing?Type,Application,Materials Process and Benefits ?
CNC( Computer Numerical Control)process or tool to shape wood, plastics, and soft metals. The computer control of CNC routing can precisely cut, drill,
and engrave these materials into intended parts. Moreover, its rapid material removal and detail-shaping capabilities are indispensable in specific material-focused applications.
his technology uses CNC machines that follow computer-generated machine instructions to move high-speed tools to different coordinates and machine-preferred designs. Understanding everything about this machining approach is essential to derive peak benefits.
This explores the basics of CNC routing, how it works, and the essential components of a CNC router. You will also learn more about the various CNC router types and the benefits and limitations of the process by reading to the end!
To involves shaping compatible materials into specific shapes or geometry with a specialized rotary tool called a router. However, the tooling and capabilities of this machining process differ from other standard CNC machining methods. Besides, CNC routing allows a more extensive range of motion along the Z-axis than a CNC milling machine.
A routing machine utilizes a specialized tool known as a router with a rotating bit. This CNC router rotates across the workpiece based on the programmed instruction (G-code) and predetermined paths to execute the machining operations. A typical CNC router has a gantry-style configuration where the spindle moves left and right along the X-axis and back and forth on the Y-axis. However, note that a CNC mill differs from a CNC mill because they are not designed to handle high-speed cutting of intricate features and geometries in harder metals.
How Does a CNC Router Work?
Computer-controlled routing is an indispensable process in different industries. The CNC (Computer Numerical Control) router works following a series of meticulous steps or stages, which help to ensure the final product matches the customer’s specifications. Here is a breakdown of how the CNC router carries out its operation:
Design Creation: The CNC routing process starts with design creation, the final product’s conceptual blueprint. Product designers use CAD software to draft detailed models, including all specifications, tolerances, and features.
CNC Language Conversion: After the design modeling, the next thing is to convert the CAD model into a CNC machine language (Geometric-code). The CAM software programs are reliable tools for converting design intricacies into machine instructions.
Machine Setup: You must use the right machine tools and CNC router bits to set the machine up for routing operation to achieve the desired outcomes. Likewise, ensure the workpiece is firmly secured in the machine bed.
Zero Positioning: The CNC router bit is programmed at the starting point (0, 0, 0, referencing)
Machining: The CNC routing task begins after the machine has been correctly set up and calibrated. Following the G-code directives, the CNC router bit rotates at high RPM to remove material across the predetermined toolpaths.
Surface Finishing: You may have to apply additional finishing operations like deburring, sandblasting, and brushing if the as-machined finish doesn’t match the intended aesthetics or functionality.
Quality Control: This is the final checkpoint where you must ensure that the finished part meets all specifications and quality standards. It includes inspecting the workpiece for dimensions and surface finish accuracy, guaranteeing the CNC routing process fulfills the highest standards.
Types Of CNC Routers?
There are various machines in the world of CNC routing, each specially engineered to fulfill the specific needs of your project. This section discusses the different CNC routers available based on their characteristics, capabilities, and applications:
ATC (Automatic Tool Changer) CNC Routers
Automatic tool changer routers are intricate machinery with an automated tool-changing mechanism allowing them to swap out tools without machinists’ intervention. Moreover, this attribute improves productivity and efficiency significantly, most notably in tasks requiring multiple cutting tool types.
ATC routers are mainly applicable in production environments where time is a primary factor, and precision is of the essence. Their extraordinary capability to mitigate downtime and human error makes them valuable assets for large-scale, complex projects.
3-Axis CNC Routers
3-axis CNC routers are the standard and most widely used CNC routers with the ability to move in their directions. These include X-axis (left to right), Y-axis (front to back), and Z-axis (up and down). The versatility of 3-axis CNC routers makes them applicable for extensive cutting, milling, and drilling applications across flat surfaces.
Since they are efficient and straightforward, beginners and experts widely use 3-axis CNC routers in machining signs, furniture, and other intricate designs on flat surfaces.
4-Axis Routers
The 4-axis CNC routers expand the 3-axis machines by introducing an extra axis of rotation, allowing the workpiece to rotate along the X-axis. This additional flexibility allows the creation of highly complex shapes and designs like sculptures or parts that must be machined on several sides.
These particular CNC routers are applicable in industries with high demand for precision and multidimensional cutting because they can create more complex geometries without manually repositioning the workpiece.
5-Axis Routers
5 axis cnc machining diagram
5 Axis CNC Machining Diagram
5-axis CNC routers are highly versatile CNC routing machines able to move along five axes simultaneously. As a result, these machines can make undercuts and cut complex shapes, providing smoother surface finishes.
5-axis CNC routers are best suited for advanced manufacturing applications that require intricate design tasks, such as high-precision parts, architectural elements, and aerospace components. They offer endless possibilities for innovation and design versatility due to their unique capability to cut the workpiece from virtually any angle or direction.
Desktop CNC Routers
As implied by the name, they are compact CNC machines built to fit in a small workshop space or on a desk. These CNC routers are best suited for handling smaller projects and prototyping because they offer a cost-effective solution for those new to the CNC routing world or with limited space.
Desktop CNC routers provide outstanding precision and versatility, perfect for machining plastic, wood, and soft metals regardless of size. Their ease of maintenance makes them the most widely used CNC routers among hobbyists, designers, and small businesses.
Hobby CNC Routers
This CNC routing machine is engineered especially for DIYers and enthusiasts who practice CNC routing for personal projects or low-volume production. These machines balance low cost and performance, providing a gateway into CNC machining without requiring industrial-grade equipment investment.
Hobby CNC routers are sophisticated enough to handle different materials like plastics, wood, and foam. Hence, they are ideal for making unique items like home décor and prototypes.
Industrial CNC Routers
Industrial CNC routers are designed to handle heavy-duty machining jobs. These powerhouses of CNC technology are engineered with robustness and durability. Hence, they can handle large volumes of work faster and with high precision.
These routers feature innovative automation capabilities like ATC (Automatic Tool Changer) systems and high-end software interfaces for handling complex tasks efficiently. Industrial CNC routing applications include engraving, cutting, and shaping different manufacturing materials for automotive, aerospace, and furniture. Moreover, they are perfect for high-volume operations because of their precision and high production capacity.
Nested-Based CNC Routers
These CNC routers are specially engineered to arrange patterns to be cut to reduce waste, optimizing material usage and efficiency. Nested-based CNC routers are used in sheet metal fabrication, cabinetry, and furniture production industries.
This type of CNC router offers economic and environmental benefits due to its ability to combine precision cutting with software-driven optimization, minimizing waste and maintaining superior quality standards.
Application:
Aerospace Industry: Waterjet cutters are used to shape and cut aerospace components, including composite materials used in aircraft.
Architectural Cutting: They are employed in architectural design for precision cutting of materials like stone and glass for decorative elements.
Artistic Creations: Waterjet cutting is embraced by artists for crafting intricate sculptures and mosaics.
Precision Engineering: Industries requiring high-precision components, such as medical device manufacturing, benefit from the accuracy of waterjet cutting.
CNC routing technology encompasses a diverse range of machines, each tailored to specific materials and applications. Router machines are versatile workhorses,
while plasma cutters and waterjet cutters excel in metal and precision cutting, respectively. The choice of CNC routing machine depends on the material to be processed and the intricacy of the desired design.