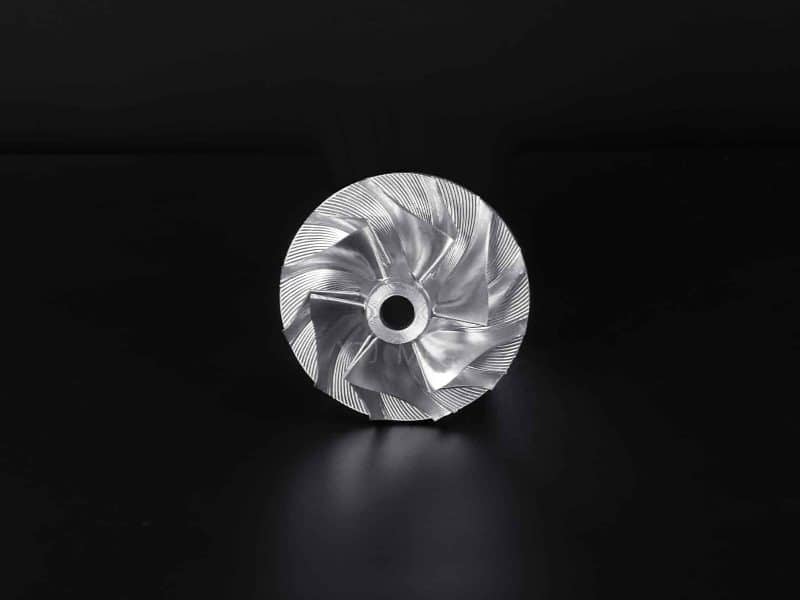
What is Injection Molding?
Injection molding is a manufacturing process for producing parts by injecting molten material into a mold. It allows for high-volume production of parts with complex shapes and sizes, utilizing various materials including plastics, metals, and ceramics. The process involves a machine that melts the material before injecting it into a cavity within a mold. Once cooled, the part is ejected, ready for use or further processing. This method is renowned for its precision, repeatability, and capability to produce parts with intricate designs and tight tolerances.
What Are the Different Types of Injection Molding Processes?
From automotive to medical devices, the versatility of different injection molding processes caters to the specific needs of each application, offering a spectrum of methods, each with its unique advantages, challenges, and material compatibilities.
Let’s get into more detail on each one, including applications, and technical characteristics
Gas-Assisted Injection Molding
Gas-assisted injection molding revolutionizes the production of plastic parts by introducing a pressurized gas into the molten plastic within the mold cavity. This innovative technique not only enhances the structural integrity of the product but also allows for the creation of complex geometries that would be difficult or impossible to achieve with conventional injection molding methods.
Applications: This process is particularly beneficial for manufacturing large, hollow parts such as handles, automotive body panels, and furniture components. Its ability to create strong, lightweight parts makes it a favored choice in sectors prioritizing these attributes.
Materials Used: Suitable for a wide range of thermoplastics, gas-assisted injection molding is commonly applied to materials such as nylon (polyamide), polyethylene, and acrylonitrile butadiene styrene (ABS), each offering distinct advantages in terms of strength, flexibility, and aesthetic finish.
Benefits and Challenges:
Enhanced strength and reduced weight of the final product, leading to cost savings in both material use and shipping.
The ability to mold complex shapes and structures not feasible with traditional injection molding.
Challenges include the need for specialized equipment and the precise control of gas injection to avoid defects.
Transitioning from gas-assisted to cube molding reveals the breadth of innovation in the injection molding industry, catering to the evolving demands for efficiency and complexity in part design.
Cube Moulding
Cube molding stands out for its unique mold design, which rotates along two axes, allowing for simultaneous molding of several parts or layers. This process significantly enhances production efficiency and is especially suited for complex, multi-component products.
Applications: Cube molding finds its niche in the production of small, intricate parts like gears, components with multiple materials or colors, and packaging items. Its ability to integrate different materials in a single cycle makes it invaluable for manufacturing sophisticated products.
Materials Used: The versatility of cube molding extends to its compatibility with a broad spectrum of materials, from standard thermoplastics to engineering polymers, enabling the production of parts that meet specific strength, durability, and aesthetic requirements.
Benefits and Challenges:
Remarkable increase in production efficiency by molding multiple parts in a single cycle.
The capability to produce complex, multi-material components.
The initial cost and complexity of the cube mold design pose challenges, requiring significant upfront investment and expertise.
The journey from cube to thin-wall injection molding underscores the industry’s drive towards maximizing efficiency and minimizing material usage, reflecting broader trends in sustainability and technological advancement.
Thin-Wall Injection Molding
Thin-wall injection molding caters to the demand for lightweight, high-strength parts with minimal material usage. This process specializes in producing extremely thin yet robust components, a critical requirement in today’s fast-paced electronic and consumer goods markets.
Applications: Ideal for manufacturing packaging materials, mobile phone cases, and containers, thin-wall molding is pivotal in industries where the strength-to-weight ratio and precision are paramount.
Materials Used: High-flow materials, such as polypropylene and polyethylene, are commonly used in thin-wall injection molding to ensure the molten plastic can fill and solidify in the mold quickly and uniformly, producing parts with consistent quality.
Benefits and Challenges:
Reduction in material consumption and production time, leading to significant cost savings and environmental benefits.
The ability to produce parts with high precision and excellent surface finishes.
However, the process demands advanced machinery with high injection pressure and speed capabilities, alongside meticulous mold design to achieve the desired wall thickness and avoid defects.
Liquid Silicone Injection Molding (LSR)
Liquid Silicone Injection Molding (LSR) stands out for its exceptional ability to produce parts that require flexibility, durability, and a high level of detail. This process utilizes liquid silicone rubber, a material known for its thermal stability, chemical resistance, and biocompatibility, making it an ideal choice for a wide range of applications.
Applications:
Medical devices and components that are in direct contact with human skin.
Automotive parts that must withstand extreme temperatures.
Consumer goods such as kitchenware and waterproof enclosures for electronics.
Materials Used: The primary material used in LSR molding is liquid silicone rubber, chosen for its consistency and properties that allow for high-precision molding.
Benefits and Challenges:
Benefits:
Exceptional durability and resistance to temperature variations.
High level of precision in molding intricate details.
Compatibility with medical and food-grade applications.
Challenges:
The initial setup and material costs can be higher compared to traditional plastic injection molding.
Requires specialized machinery and expertise to manage the curing and molding process effectively.
Transitioning from LSR to Metal Injection Molding (MIM), we shift our focus from the flexibility of silicones to the strength and precision of metal parts, illustrating the breadth of possibilities within injection molding technologies.
Metal Injection Molding (MIM) combines the design flexibility of plastic injection molding with the strength and integrity of metal. By mixing metal powders with a polymer binder, MIM allows for the production of metal parts with complex shapes and fine details, which are difficult to achieve through traditional metalworking processes.
Applications:
Precision components for watches and electronics.
Industrial tools and components requiring high strength and durability.
Medical and dental instruments.
Materials Used: A wide variety of metals can be used in MIM, including stainless steel, titanium, and alloys tailored to specific property requirements.
Benefits and Challenges:
Benefits:
Ability to produce dense, strong parts with complex geometries.
Cost-effective for high-volume production runs.
Reduces or eliminates secondary operations such as machining.
Challenges:
Higher initial costs for tooling and setup compared to some other injection molding processes.
The debinding and sintering processes require careful control and can extend production times.
As we move from MIM to Reaction Injection Molding (RIM), the versatility of injection molding processes in accommodating a range of materials—from silicone to metal to reactive polymers—becomes increasingly evident, showcasing the adaptability of this manufacturing technique to diverse industry needs.
Reaction Injection Molding (RIM) is a process where two reactive chemical components are mixed and injected into a mold where they then react and cure, forming a lightweight, strong, and intricate part. This process is particularly noted for its ability to produce large parts with variable wall thickness and excellent impact resistance.
Applications:
Automotive bumpers and dashboards that require durability and lightweight.
Enclosures for medical equipment and electronics that need a high-quality finish.
Custom panels and housings for industrial machinery.
Materials Used: Polyurethanes are the most commonly used materials in RIM, selected for their versatility, impact resistance, and strength-to-weight ratio.
Benefits and Challenges:
Benefits:
Produces large parts with complex shapes and superior surface finishes.
High impact resistance and lightweight properties.
Offers significant design flexibility and material options.
Challenges:
Process control is critical to prevent issues with curing and material properties.
The cost of raw materials and the need for precise metering and mixing equipment can be higher than other methods.
Thermoplastic Injection Molding
Thermoplastic Injection Molding
Thermoplastic injection molding is renowned for its efficiency and flexibility. This process involves melting thermoplastic polymers and injecting them into a mold cavity, where they cool and solidify into the final part. One of the most appealing aspects of thermoplastic molding is the material’s ability to be remelted and reused, making it a popular choice for a wide range of applications.
Applications:
Consumer electronics enclosures, such as smartphones and computers.
Automotive components like dashboards and bumpers.
Medical devices that require sterilization.
Materials Used: Common materials include ABS (Acrylonitrile Butadiene Styrene), Polycarbonate (PC), Polypropylene (PP), and Nylon (Polyamide), each offering unique properties such as durability, flexibility, and resistance to impact and heat.
Benefits and Challenges:
Benefits: Cost-effectiveness for large production runs, recyclability of materials, and a broad selection of materials to meet specific property requirements.
Challenges: Material degradation with repeated processing and the initial cost of mold design and production setup.
Transitioning from thermoplastics to thermosets, we encounter materials that, once cured, offer different benefits and challenges, underscoring the need to choose the right process based on the end-use requirements.
Thermoset Injection Molding
Thermoset injection molding caters to applications requiring materials that can withstand high temperatures without losing their structural integrity. Unlike thermoplastics, thermoset materials undergo a chemical change when heated and molded, resulting in a product that cannot be remelted or reshaped.
Applications:
Electrical components and insulators due to their high heat resistance.
Automotive parts that must endure extreme conditions.
Appliance housings for their durability and finish.
Materials Used: Epoxy, Phenolic, Polyester, and Silicone are common thermoset materials, chosen for their strength, chemical resistance, and thermal stability.
Benefits and Challenges:
Benefits: Superior heat and chemical resistance, high dimensional stability, and durability in harsh environments.
Challenges: Irreversibility of the curing process limits recyclability, and precise control of the molding process is critical to prevent defects.
Exploring further into the domain of specialized molding processes, structural foam injection molding presents a unique set of characteristics, blending aspects of both thermoplastic and thermoset processes to achieve parts with exceptional strength and lightweight properties.
Structural Foam Injection Molding
Structural foam injection molding is distinguished by its use of a foaming agent mixed with the polymer, creating a cellular core surrounded by a solid skin. This technique results in components that are lighter and more rigid than solid plastics, offering enhanced structural strength for a variety of applications.
Applications:
Large parts such as outdoor furniture, automotive panels, and enclosures for large machinery.
Components requiring high strength-to-weight ratios.
Products that benefit from thermal insulation properties.
Materials Used: High-density polymers such as Polyethylene (PE), Polystyrene (PS), and Polypropylene (PP) are commonly used, with the addition of a physical or chemical blowing agent to create the foam structure.
Benefits and Challenges:
Benefits: Reduction in material usage without compromising strength, improved thermal and acoustic insulation, and lower production costs for large parts.
Challenges: Managing the foaming process to achieve consistent cellular structure throughout the part and ensuring the mold is designed to accommodate the expansion of the material.
Overmolding
Overmolding is a two-step process that involves molding a second layer of material over a previously molded part. This technique is used to add soft touch surfaces on hard plastics, create multi-colored or multi-material components, and improve the product’s aesthetic and functional attributes.
Applications:
Tool handles with a comfortable grip.
Medical devices with a soft-touch surface for better handling.
Automotive interior parts that require a combination of textures or materials.
Materials Used: Typically involves thermoplastics like ABS for the rigid substrate and TPE (Thermoplastic Elastomers) for the soft outer layer.
Benefits and Challenges:
Benefits: Enhances the aesthetic appeal and functionality of the product, improves grip and comfort, and can seal parts against moisture and dust.
Challenges: Requires precise control of molding conditions to ensure proper adhesion between layers and may involve higher production costs due to multiple processing steps.
The transition from overmolding to insert molding showcases the versatility of injection molding processes in integrating various components and materials to meet specific design requirements.
Insert Molding
Insert molding involves the insertion of a pre-made part (often metal) into a mold, where it is then encased by plastic. This process is ideal for integrating metal parts with plastic, creating a single, robust component.
Applications:
Electrical connectors with metal pins encased in plastic.
Knobs or components with metal threads for screws.
Surgical instruments with metal tips or components.
Materials Used: A wide range of plastics can be used, including ABS, Polycarbonate, and Nylon, which are molded around metal parts such as brass, stainless steel, or aluminum inserts.
Benefits and Challenges:
Benefits: Provides enhanced structural strength, enables the integration of different materials, and reduces assembly and labor costs.
Challenges: The process requires precise insert placement and mold design to prevent shifting during molding, and there’s a risk of thermal damage to inserts.
Exploring further into the precision capabilities of injection molding, micro injection molding offers solutions for producing extremely small and detailed components.
Micro Injection Molding
Micro injection molding is tailored for manufacturing micro-sized parts and components with intricate details. This process demands specialized machines and molds to handle very small volumes of material with extreme precision.
Applications:
Medical components like micro needles or small implants.
Micro gears and components for electronics.
Connectors and optical parts requiring high precision.
Materials Used: High-performance materials such as PEEK, LCP (Liquid Crystal Polymer), and specialized thermoplastics suitable for fine detail and strength at a micro-scale.
Benefits and Challenges:
Benefits: Allows for the production of highly detailed and precise components, suitable for advanced applications in the medical and electronics industries.
Challenges: High costs of tooling and machinery due to the precision required, along with challenges in handling and inspecting such small parts.
High-Pressure Injection Molding
Key Characteristics: High-pressure injection molding is characterized by the injection of molten material into a mold at high pressure. This process allows for the creation of parts with intricate designs and excellent surface finish, making it suitable for a wide range of applications.
Applications:
Automotive components such as dashboards and exterior panels that require high strength and a flawless finish.
Consumer electronics casings, where precision and aesthetic appeal are paramount.
Medical devices that demand high precision and reliability.
Materials Used: Wide variety of thermoplastics, including ABS, Polycarbonate, and Polyamide, known for their strength, flexibility, and ability to withstand high pressure without deforming.
Benefits and Challenges:
Benefits: Produces parts with high precision and excellent surface quality; suitable for complex shapes and designs.
Challenges: Higher operational costs due to the need for robust machinery and higher energy consumption; increased risk of warping or internal stresses in finished parts.
Transitioning from the high intensity of high-pressure injection molding, low-pressure injection molding offers an alternative that prioritizes the integrity and functionality of electronic components and delicate inserts.
Low-Pressure Injection Molding
Low-pressure injection molding operates at lower pressures, making it ideal for encapsulating delicate components without causing damage. This method is particularly favored for its ability to provide superior protection for electronic components against environmental factors.
Applications:
Encapsulation of electronic components to protect against moisture, dust, and mechanical shock.
Manufacturing of large and complex parts where minimizing stress and warping is critical.
Overmolding on sensitive components such as cables and connectors.
Materials Used: Low-pressure molds often use thermoplastic and thermosetting polymers like Polyethylene and Epoxy resins, which flow easily at lower pressures, ensuring delicate components are not damaged.
Benefits and Challenges:
Benefits: Lower risk of damaging inserts, improved part strength and stress distribution, and enhanced sealing properties.
Challenges: Limited to materials that can flow under low pressure; may not be suitable for products requiring high-density materials.
As we move from the realm of structural component fabrication to the intricacies of product branding and aesthetics, in-mold decoration (IMD) and in-mold labeling (IML) offer innovative solutions for integrating design directly into the molding process.
In-Mold Decoration (IMD) and In-Mold Labeling (IML)
IMD and IML processes involve integrating graphics, textures, and labels directly into the surface of molded parts during the injection molding process. This technique ensures that decorations are durable, wear-resistant, and seamlessly integrated with the part.
Applications:
Consumer products packaging, where brand identity and instructions need to withstand wear and tear.
Automotive interiors for seamless integration of designs and icons on components.
Electronic device housings with detailed graphics and branding.
Materials Used: Uses films and labels made from compatible materials such as Polypropylene for IML and various engineered polymers for IMD, ensuring compatibility with the substrate for a strong bond.
Benefits and Challenges:
Benefits: Enhanced durability of printed graphics; opportunities for creativity in product design; reduction in post-processing and labeling steps.
Challenges: Complexity in mold and film design; initial cost and setup time; limitations in label or film adjustments once production starts.
Multi-Material Injection Molding (also known as Multi-Component or 2-Shot Molding)
Multi-material injection molding, also recognized as multi-component or 2-shot molding, is a sophisticated process that molds two or more different materials into a single part in one machine cycle. This technique allows for the combination of varied colors, textures, and material properties in a single component, enhancing functionality and aesthetic appeal.
Applications:
Automotive parts such as dashboards with soft-touch surfaces and rigid substrates.
Medical devices that require a rigid body with soft, flexible seals.
Consumer products like toothbrushes with a comfortable grip and durable bristles.
Materials Used: A wide range of thermoplastics can be used, including combinations of hard plastics such as Polycarbonate (PC) and Acrylonitrile Butadiene Styrene (ABS) with soft materials like Thermoplastic Elastomers (TPE) or Silicones.
Benefits and Challenges:
Benefits: Enhanced product design and functionality through the integration of multiple materials; reduction in assembly time and costs.
Challenges: Requires specialized injection molding machines and molds, leading to higher initial investments; material compatibility and bonding issues may arise.
The evolution from multi-material to co-injection molding reflects the industry’s push towards more efficient and innovative manufacturing techniques, capable of producing complex parts with enhanced properties.
Co-Injection Molding
Co-injection molding is a process where two dissimilar materials are injected into the same mold cavity, one after the other, creating a part with a skin and core structure. This method is often used to combine materials with different characteristics, such as rigidity and flexibility, or to encapsulate a lower-cost material with a high-quality outer layer.
Applications:
Packaging for food and beverages that require a barrier layer to extend shelf life.
Automotive panels that need a high-quality surface with a cost-effective core.
Structural components that benefit from the combination of high strength and reduced weight.
Materials Used: Typically involves a combination of a base material like Polypropylene (PP) with a barrier material such as Ethylene-Vinyl Alcohol (EVOH) for barrier properties or a rigid plastic with a soft-touch thermoplastic overlay.
Benefits and Challenges:
Benefits: Allows for the creation of parts with enhanced physical properties; cost savings through the use of less expensive core material.
Challenges: Complex process control and machine settings; potential issues with the bond between the two materials.
Shifting focus to a technique that bridges the gap between design complexity and manufacturability, fusible (lost, soluble) core injection molding offers a unique solution for creating parts with intricate internal geometries.
Fusible (Lost, Soluble) Core Injection Molding
Fusible core injection molding, also known as lost core molding, utilizes a core material that can be melted or dissolved away after the molding process, leaving behind a detailed internal cavity or undercuts that would be difficult to achieve with traditional molding methods.
Applications:
Automotive intake manifolds, coolant passages, and other complex internal structures.
Hollow components in aerospace, medical, and consumer products that require internal channels.
Materials Used: The process typically employs a fusible alloy or soluble material for the core, surrounded by engineering thermoplastics such as Nylon or Polypropylene for the part.
Benefits and Challenges:
Benefits: Enables the production of complex internal geometries without the need for post-molding assembly; reduces weight and material usage.
Challenges: High cost and complexity of producing fusible cores; additional process steps for core removal.
Water-Assisted Injection Molding
Water-assisted injection molding is an innovative process that introduces water into the molten plastic inside the mold cavity to create hollow or partially hollow parts. This technique enhances cooling times and allows for more uniform wall thickness, leading to stronger and lighter components.
Applications:
Automotive components such as coolant lines, air ducts, and handles.
Hollow consumer product handles and parts requiring lightweight and strength.
Fluid flow applications where internal channels are necessary.
Materials Used: Compatible with a wide range of thermoplastics, including Polypropylene (PP), Polyethylene (PE), and Nylon, that accommodate the water-assisted process without compromising the material’s integrity.
Benefits and Challenges:
Benefits: Reduced cycle times, material savings, and enhanced part strength due to more uniform wall thickness.
Challenges: The complexity of mold design and the need for specialized equipment can increase initial costs.
Transitioning from the efficiency and enhanced structural integrity offered by water-assisted molding, silicone injection molding caters to applications demanding flexibility, durability, and high performance in extreme conditions.
Silicone Injection Molding
Silicone injection molding specializes in producing parts from silicone rubber, a material known for its flexibility, thermal stability, and chemical resistance. This process is ideal for creating components that need to withstand harsh environments while maintaining their shape and functionality.
Applications:
Medical devices and implants that require biocompatibility and sterilizability.
Automotive seals, gaskets, and hoses exposed to extreme temperatures.
Consumer goods such as kitchenware, bakeware, and protective covers that demand durability and flexibility.
Materials Used: Liquid silicone rubber (LSR) is predominantly used due to its excellent flow properties, allowing for the molding of intricate details and complex shapes.
Benefits and Challenges:
Benefits: High levels of precision and repeatability, ability to produce parts that withstand extreme conditions, and excellent material properties such as biocompatibility and thermal resistance.
Challenges: The high cost of silicone materials and the requirement for precise temperature control during the molding process.
As we explore the nuances of injection molding processes further, cold runner molding emerges as a method focused on efficiency and material conservation, offering distinct advantages in the production of thermoplastic parts.
Cold Runner Molding
Cold runner molding utilizes a system where the molten plastic is conveyed into the mold cavity through channels (runners) that cool and solidify along with the part. This method is widely used due to its simplicity and effectiveness in producing multiple parts per cycle.
Applications:
General plastic components including consumer products, automotive parts, and medical devices.
Products requiring multi-cavity molds for high-volume production.
Materials Used: Versatile across a broad spectrum of thermoplastics such as ABS, Polyethylene, and Polycarbonate, allowing for a wide range of part properties.
Benefits and Challenges:
Benefits: Flexibility in the use of materials, ability to produce multiple parts per cycle, and relative ease of changing material colors.
Challenges: Increased cycle times due to the need for runners to cool and the potential for material waste, although the latter can be mitigated through regrinding and recycling.
Hot Runner Molding
Hot runner molding is a system where heated channels guide molten plastic into the mold cavity, ensuring efficient material usage by eliminating the runner. This process is ideal for high-volume production where material conservation and cycle time are critical.
Applications:
Automotive components that require precise dimensional tolerances.
Consumer electronics with intricate details.
Medical devices needing high-quality surface finishes.
Materials Used: Compatible with a wide range of thermoplastics, from commodity plastics like Polyethylene (PE) and Polypropylene (PP) to engineering plastics such as Polycarbonate (PC) and Polyamide (nylon).
Benefits and Challenges:
Benefits: Reduction in waste, consistent quality due to maintained temperature, and shorter cycle times.
Challenges: Higher initial setup and maintenance costs, complexity in mold design, and the necessity for advanced temperature control systems.
Transitioning from the streamlined efficiency of hot runner systems, rotational molding offers a contrasting approach suited for hollow, large, and one-piece items.
Rotational Molding
Rotational molding involves a heated mold that is rotated on two axes, distributing the plastic material evenly along the mold’s inner surface to form hollow parts. This method is celebrated for its ability to produce large, durable items with uniform wall thickness.
Applications:
Large storage tanks and containers.
Durable outdoor furniture.
Hollow toys and recreational equipment.
Materials Used: Mainly Polyethylene (PE) due to its low melting point, flexibility, and durability. Other materials include PVC, Nylon, and Polycarbonate for specific applications requiring different material properties.
Benefits and Challenges:
Benefits: Cost-effective for small to medium production runs, ability to create large and complex hollow shapes, and minimal material waste.
Challenges: Relatively slow production cycle, limitations in achieving intricate details, and dependency on mold quality for the final product’s consistency.
Exploring further into the realm of specialized molding processes, Ceramic Injection Molding (CIM) presents a sophisticated technique for manufacturing components requiring the exceptional properties of ceramics.
Ceramic Injection Molding (CIM)
Ceramic Injection Molding combines the versatility of plastic injection molding with the advanced material properties of ceramics, offering high precision, excellent wear resistance, and the ability to withstand extreme conditions.
Applications:
Aerospace and automotive components for high temperature and wear resistance.
Medical and dental tools due to biocompatibility and strength.
Electronic device components for their insulating and heat resistance properties.
Materials Used: A variety of ceramic powders, including alumina, zirconia, and silicon carbide, mixed with a polymeric binder to facilitate the injection process.
Benefits and Challenges:
Benefits: Enables the production of complex shapes with high precision and excellent material properties such as hardness, wear resistance, and temperature tolerance.
Challenges: Requires significant post-processing to remove the binder and sinter the ceramic, high initial tooling costs, and the need for specialized knowledge to handle ceramic materials.
High-Gloss Injection Molding
High-gloss injection molding is distinguished by its ability to produce parts with a shiny, high-quality surface finish without the need for post-molding operations. This process is achieved through the use of high temperatures and pressures, along with specialized molds and materials.
Applications:
Automotive interior and exterior components that require a premium aesthetic.
Consumer electronics casings, such as smartphones and laptops.
High-end cosmetic packaging.
Materials Used: Thermoplastics compatible with high-gloss finishes, including ABS, Polycarbonate, and PMMA (Acrylic).
Benefits and Challenges:
Benefits: Eliminates the need for painting or plating, reducing production costs and environmental impact.
Challenges: Requires precision in mold design and process control to prevent defects and ensure uniformity of the gloss finish.
Transitioning from the aesthetics-driven high-gloss molding, the classification of injection molds introduces another layer of complexity and specificity to the injection molding process, tailored to enhance efficiency, product quality, and manufacturability.
How Are Injection Molds Classified?
How Are Injection Molds Classified?
Injection molds can be categorized based on various criteria, each addressing different aspects of the molding process, from material selection to the intricacies of mold design. This classification system helps in precisely identifying the most suitable mold type for a given application, ensuring optimal performance and cost-efficiency.
Based on the Mold Material
Metal Molds: Preferred for high-volume production due to their durability and ability to withstand high pressures and temperatures.
Silicone and Rubber Molds: Used for producing flexible parts, these molds are ideal for items requiring elasticity.
3D Printed Molds: Offer a cost-effective solution for prototyping and low-volume production, with a faster turnaround time but limited durability.
The material of the mold directly influences the production capabilities, affecting everything from cycle times to the final part quality.
Based on the Type of Feeding System
Hot Runner Molds: Incorporate a heated channel system that keeps the plastic molten, enabling continuous flow into the mold cavity, significantly reducing waste.
Cold Runner Molds: Utilize a system where the runner cools and solidifies with the part, requiring subsequent removal and recycling.
Insulated Runner Molds: Designed to partially insulate the runner path, slowing the cooling process and reducing material waste without the complexity of hot runners.
The type of feeding system a mold employs has profound implications on material efficiency, cycle times, and the overall sustainability of the production process.
Based on the Number of Cavities
Single Cavity Molds: Designed to produce one part per cycle, these molds are ideal for low-volume production or large components. They offer simplicity and ease of maintenance but may not be cost-effective for high-volume manufacturing due to slower production rates.
Multi-Cavity Molds: Contain multiple cavities of the same part, significantly increasing production efficiency. They are suited for high-volume manufacturing, reducing costs per part. However, they require precise design and higher initial investment to ensure uniform quality across all cavities.
Family Molds: These molds produce different parts within the same cycle, useful for components that go together in the final product assembly. While they can reduce production time and costs by eliminating the need for multiple molds, careful design is crucial to balance the filling, cooling, and ejection phases across differently sized parts.
Based on the Mold Opening and Ejection System
Two-Plate Molds: The most common type, consisting of two plates that open in one direction. Simplicity and lower manufacturing costs make them a popular choice, though they may be limited in complexity.
Three-Plate Molds: Allow for more complex part designs with automatic ejection. They contain two parting lines and can incorporate multiple gates. The added complexity increases the cost but offers greater flexibility in gate placement and part design.
Stack Molds: Essentially several two-plate molds stacked together, allowing for double or even quadruple the output without increasing the machine size or clamp requirements. They maximize production efficiency but come with higher costs and complexity.
Based on the Type of Gating System
Edge Gate: The most common and simplest type, suitable for a wide range of parts. It directly injects the molten material into the part cavity at its edge.
Pin Gate: Small and easily removable, pin gates are ideal for small or cosmetic parts, minimizing marks and allowing for closer gate placement to the part.
Submarine Gate: Hidden beneath the parting line, this gate type allows for automatic part ejection and is typically used for medium and thick sections.
Fan Gate: Spreads the material more evenly with its fan-shaped design, reducing stress and warpage, ideal for large parts needing uniform filling.
Sprue Gate: Directly connected to the machine’s nozzle, it’s used for single cavity molds or large parts, providing a straightforward path for the molten material.
Based on the Mold’s Design
Standard Molds: The backbone of injection molding, standard molds are versatile and straightforward, designed for a wide range of applications. They are the go-to choice for many projects due to their reliability and cost-effectiveness.
Slide Molds: Equipped with movable sections or “slides” that allow for the creation of parts with undercuts or protrusions. These molds are essential for producing complex shapes that are impossible to mold with a simple open-and-shut mold.
Lifter Molds: Similar to slide molds, lifter molds include components that move perpendicular to the mold opening direction. They are used to create recesses or undercuts on the sides of parts, enhancing the mold’s ability to produce intricate details.
Rotating Molds: These molds rotate on a second axis within the molding machine, allowing for parts with more complex geometries. This type of mold is particularly useful in creating parts that need to be molded from two different directions.
Three Plate Molds: Consist of three sections that separate during ejection, offering more flexibility in gate placement. This design is ideal for parts requiring multiple injection points.
Split Cavity Molds: Designed to split into two or more parts to release the molded part. They are particularly useful for molding parts with intricate designs and deep cavities.
Mold With Screw Device: Incorporates a screw mechanism to demold parts with threads or helical features. This allows for the production of threaded components without damaging the threads during ejection.
Stripper Ejector Mold: Uses a plate to strip the part off the core during ejection. It’s especially effective for ejecting parts with a large diameter or those that would stick to the core.
Based on Special Features
Unscrewing Molds: Utilize rotating cores powered by hydraulic or electric motors to produce threaded parts. This type of mold is essential for manufacturing components with precise internal or external threads.
Overmolding Molds: Designed for overmolding, a process that molds additional layers of material over an existing part. This technique is used to add soft-touch surfaces, seals, or aesthetic features.
Insert Molding Molds: These molds allow for the incorporation of inserts into the molded part. Inserts can be made of metal, another plastic, or different materials, providing enhanced strength, functionality, or conductivity.
Gas-Assisted Injection Molds: Employ gas (usually nitrogen) to create hollow sections within the molded part. This reduces weight, material usage, and cycle times, while improving structural integrity.
Based on the Cooling System
Conventional Cooling Molds: Utilize drilled channels through which cooling fluid circulates to control the mold temperature. While effective for many applications, the cooling can be uneven.
Conformal Cooling Molds: Feature cooling channels that follow the shape of the part or mold cavity more closely. This advanced cooling method allows for faster and more uniform cooling, reducing warpage and sink marks.
What Factors Influence the Choice of Injection Molding Process?
When you’re delving into the world of injection molding, the process you select can significantly impact the efficiency, cost, and quality of your project. Various factors must be meticulously considered to ensure the optimal method is chosen. Here are key elements that influence this critical decision, accompanied by practical tips to guide you:
Material Selection: The type of plastic material you plan to use plays a pivotal role. Different materials have varying flow rates, cooling times, and temperature requirements. For instance, thermoplastics like polyethylene and polypropylene might be suited for high-volume production due to their low cost and fast processing time.
Part Complexity and Design: Complex parts with intricate geometries might require advanced molding techniques like 3D printing or gas-assisted injection molding to achieve the desired precision and detail without compromising structural integrity.
Volume of Production: For high-volume production, multi-cavity molds or family molds can be more cost-effective. Conversely, for low-volume or prototype production, single-cavity molds or additive manufacturing (3D printing) could be more suitable.
Tolerance and Quality Requirements: High-precision parts necessitate molds with tight tolerances and may benefit from technologies like hot runner systems to maintain consistent quality.
Lead Time: Projects with tight deadlines might opt for rapid prototyping methods such as 3D printing before committing to more time-intensive traditional molding processes.
Cost Considerations: Budget constraints can significantly influence the choice of molding process. For example, silicone and rubber molds are less expensive than metal molds but might not offer the same durability or precision.
XTJ is a leading OEM Manufacturer that is dedicated to providing one-stop manufacturing solutions  from prototype to production. We are proud to be an ISO 9001 certified system quality management company and we are determined to create value in every customer relationship. We do that through collaboration, innovation, process improvements, and exceptional workmanship.