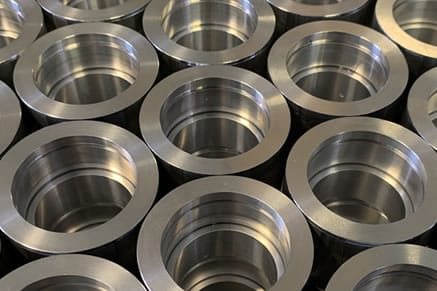
Table of Contents
What is Surface finish?
Surface finish and surface finishing might sound similar but refer to distinct aspects of CNC machining. Surface finish denotes the inherent texture and quality of a part’s surface after machining, characterized by metrics such as roughness average (Ra).
In contrast, surface finishing involves additional processes applied to the machined part to alter or improve its surface properties, including techniques like anodizing, powder coating, and bead blasting.
What Are the Pre-Surface Finish Processes for CNC Machining?
Before applying surface finishes, certain preparatory steps ensure the machined parts are ready for finishing.
One essential process is masking holes and surfaces to protect specific areas from finishing treatments, maintaining their original precision and functionality.
Other pre-surface finish processes include cleaning to remove any machining residues, smoothing edges to eliminate sharpness, and surface preparation techniques to ensure optimal adhesion and finishing results.
What are the Different Surface Roughness Levels Typically Used for CNC Machined Parts?
Surface roughness levels are pivotal in dictating the functionality and aesthetics of CNC machined parts. Here’s a breakdown of common roughness levels:
0.4 μm Ra: This ultra-smooth surface finish is often required for high-precision parts where minimal friction and maximum durability are critical. It’s more costly, adding a significant percentage to the production price due to the intensive machining and quality control efforts required.
0.8 μm Ra: Ideal for parts requiring a balance between cost-efficiency and performance, this level of smoothness is often sought after for consumer electronics and automotive components, moderately increasing the part’s production cost.
1.6 ÎĽm Ra: This roughness level is commonly used for general machinery components, offering a good trade-off between surface quality and manufacturing cost.
3.2 ÎĽm Ra: Suitable for less critical applications where surface smoothness is not the primary concern, this level keeps production costs lower while still providing adequate performance for many industrial components.
Surface roughness, often denoted by the term “Ra” (Roughness Average), is a quantitative measure of the surface texture or smoothness of machined parts. It plays a significant role in determining how a part will interact with its environment or other components.
Let’s delve into more details about the various Ra levels and their applications in CNC machining.
0.4 ÎĽm Ra
At a microscopic level, a 0.4 μm Ra surface finish is incredibly smooth, resembling almost a mirror finish. This level of smoothness is essential for components where minimal friction is crucial, such as in aerospace applications or high-precision bearings. Such a finish ensures that the parts can operate efficiently under high speeds or in environments where any surface imperfection could lead to failure. The precision required to achieve this finish means that it’s often the most costly, reserved for parts where performance cannot be compromised.
0.8 ÎĽm Ra
Stepping up to a 0.8 μm Ra, this surface roughness level finds its sweet spot in automotive and consumer electronics, where components need to be smooth enough to ensure reliability and longevity but not to the extent that it becomes prohibitively expensive. This finish strikes a balance, offering a surface that minimizes wear and tear while keeping manufacturing costs in check. It’s ideal for visible components that also require a degree of aesthetic appeal without needing the extreme smoothness of a 0.4 μm Ra finish.
1.6 ÎĽm Ra
A 1.6 μm Ra surface finish is widely considered the industry standard for a variety of general applications. This level of roughness is sufficiently smooth for many mechanical components in machinery where the surface finish impacts functionality less critically. It’s a cost-effective option for parts that do not come into constant human contact or where the slight roughness does not detract from the part’s performance, such as internal components of machinery.
3.2 ÎĽm Ra
When it comes to a 3.2 μm Ra, we’re looking at a surface finish that’s more about functionality than form. This level is common in parts where the surface finish is not a primary concern, such as in structural components or those hidden from view. It’s the most economical choice, suitable for parts that require basic functionality without the need for a high degree of smoothness. The increased roughness is tolerable in applications where the interaction with other parts or materials is minimal or where any potential for increased wear and tear is not a significant concern.
What Are the Different Methods of Surface Finish in CNC Machining?
The various surface finish methods sued in CNC machining can be categorized under three main categories:
mechanical finishing methods
chemical finishing methods
thermal finishing methods
Let’s explore each technology starting with the mechanical finishing methods.
Mechanical Finishing Methods
Mechanical finishing methods involve physical interactions with the part’s surface to achieve the desired finish.
These methods are versatile, capable of producing a range of finishes from rough to mirror-like. They’re suitable for a wide array of materials, including metals, plastics, and composites, making them indispensable in the CNC machining process.
Milling and Turning
Milling and turning stand as the foundational pillars of mechanical finishing in CNC machining. These processes not only shape the part but also determine its final surface texture.
Technical Characteristics: Both methods employ cutting tools that remove material from the workpiece in a controlled manner, with precision and speed being paramount. The choice between milling and turning is often dictated by the part’s geometry: milling is preferred for complex shapes and features, while turning is ideal for cylindrical parts.
Materials and Applications: Commonly used across metals like aluminum, steel, and brass, and plastics such as nylon and PEEK, milling and turning are versatile in their application. From aerospace components requiring tight tolerances to automotive parts needing durability and finish, these methods are pivotal.
Pros and Cons: The main advantage of milling and turning lies in their precision and versatility, allowing for a wide range of surface finishes and part geometries. However, limitations include tool wear, which can affect finish quality over time, and the need for multiple setups for complex parts, potentially increasing production time and cost.
Grinding
Grinding is a finishing process that uses an abrasive wheel to achieve extremely smooth surfaces or precise geometrical shapes on the workpiece.
Technical Characteristics: Grinding is characterized by its ability to achieve high precision and surface quality, often reaching finishes as smooth as 0.1 μm Ra. It’s the go-to method for parts requiring tight tolerances that milling and turning cannot achieve.
Materials and Applications: Ideal for hard materials like hardened steel, ceramics, and carbides, grinding is extensively used in tool manufacturing, automotive, and aerospace industries, where precision and surface integrity are non-negotiable.
Pros and Cons: Grinding offers unmatched precision and surface quality, making it essential for many high-precision applications. The downside is its relatively slow speed and the higher cost associated with the process due to the wear and maintenance of the abrasive wheels.
Sanding
Sanding uses abrasive materials to smooth surfaces, typically as a finishing step to remove minor imperfections left by prior machining processes.
Technical Characteristics: Sanding is versatile, allowing for adjustment in grit size to move from rough to fine finishes. It’s often used in combination with other finishing processes to prepare surfaces for painting or coating.
Materials and Applications: Sanding is suitable for a wide range of materials, including wood, metals, and plastics. It’s commonly used in the automotive and furniture industries to prepare surfaces for final finishing.
Pros and Cons: The primary advantage of sanding is its simplicity and effectiveness in achieving a smooth finish. However, it can be labor-intensive and time-consuming, especially for parts with complex geometries or requiring ultra-smooth finishes.
Bead Blasting
Bead blasting is a mechanical process that involves propelling a stream of abrasive glass beads at high speed against the surface of a part. This action effectively removes surface imperfections, resulting in a uniform, matte finish that can enhance the part’s aesthetic and functional properties.
Materials and Applications: Bead blasting is versatile, applicable to a wide range of materials including metals like aluminum, steel, and titanium, as well as plastics. It’s commonly used in the automotive, aerospace, and electronics industries to prepare surfaces for painting, anodizing, or simply to improve their appearance.
Pros and Cons: The main advantage of bead blasting is its ability to provide a consistent, aesthetically pleasing finish that can also obscure minor surface defects. However, it’s important to control the blasting process carefully to prevent material removal that could alter the part’s dimensions or introduce surface stresses
Polishing
Polishing is a finishing process that uses abrasives or chemical agents to achieve a high-gloss, mirror-like finish on the surface of a part. It’s a method that not only enhances the part’s visual appeal but can also reduce friction, improve cleanliness, and increase corrosion resistance.
Materials and Applications: This method is ideal for metals such as stainless steel, aluminum, and brass, and is widely used in the medical, food processing, and luxury goods industries, where a high degree of surface finish is essential for both aesthetic and functional reasons.
Pros and Cons: Polishing offers the benefit of a smooth, reflective surface that enhances the part’s visual appeal and performance characteristics. However, it can be labor-intensive and time-consuming, especially for parts with complex geometries or requiring extremely high finishes.
Brushing
Brushing uses fine bristles or abrasive media to create a uniform, directional texture on the surface of a part. This method is particularly effective for highlighting the natural luster of metal parts without achieving the high gloss of polishing.
Materials and Applications: Suitable for a variety of metals, including aluminum, stainless steel, and copper, brushing is often employed for architectural components, consumer electronics, and automotive parts, where a satin finish is desired.
Pros and Cons: Brushing is advantageous for its ability to provide a consistent, aesthetically pleasing finish that can conceal fingerprints and minor imperfections. However, it might not be suitable for applications requiring a non-directional finish or where surface smoothness is a critical factor.
Tumbling and Vibratory Finishing
Tumbling and vibratory finishing are batch processes that smooth and polish parts by placing them in a container filled with abrasive media and either rotating the container (tumbling) or vibrating it (vibratory finishing). These methods are excellent for processing large quantities of small parts.
Materials and Applications: These processes are applicable to a broad range of materials, including metals, plastics, and ceramics. They are particularly useful in the automotive, aerospace, and jewelry industries for deburring, smoothing, and polishing components.
Pros and Cons: The primary advantage of tumbling and vibratory finishing is their efficiency in finishing large batches of parts simultaneously, providing a uniform finish. The main drawback is the potential for part-on-part contact, which can lead to damage or deformation, especially for delicate parts.
Media Blasting
Media blasting is a versatile finishing process that involves propelling a stream of abrasive material against the surface of a part under high pressure. This method is highly effective for cleaning, deburring, and finishing surfaces.
Materials and Applications: Media blasting can be applied to a wide range of materials, including metals, plastics, and composites. It’s particularly useful in preparing surfaces for subsequent coatings, removing manufacturing residues, or creating a specific surface texture. Common applications include automotive parts, aerospace components, and industrial machinery.
Pros and Cons: The main advantage of media blasting lies in its ability to uniformly finish complex geometries and reach difficult-to-access areas. However, it requires careful selection of blasting media and parameters to avoid damaging the substrate or altering critical dimensions.
Vapor Polishing
Vapor polishing is a finishing technique that uses a chemical vapor to melt the surface of plastic parts, resulting in a smooth, glossy finish. This method is particularly suited for materials that are difficult to polish mechanically.
Materials and Applications: Vapor polishing is primarily used on thermoplastics such as polycarbonate, ABS, and acrylic. It’s ideal for applications requiring optical clarity or a high-gloss finish, such as medical devices, automotive lights, and display cases.
Pros and Cons: Vapor polishing offers the advantage of achieving a clear, smooth finish without introducing mechanical stress to the part. However, it involves the use of hazardous chemicals, requiring strict safety measures and environmental controls.
Knurling
Knurling is a process that creates a patterned texture on the surface of a part, usually for grip enhancement or aesthetic purposes. It involves pressing a patterned tool against the rotating workpiece to form a tightly controlled, uniform pattern.
Materials and Applications: Knurling is commonly performed on metal parts, including aluminum, steel, and brass. It’s widely used in tool handles, control knobs, and custom fasteners where an improved grip or decorative finish is desired.
Pros and Cons: The primary benefit of knurling is its ability to enhance the tactile properties of parts without significantly impacting their dimensional tolerances. However, it’s limited to accessible, rotationally symmetrical areas and may require additional finishing steps to remove any burrs or sharp edges created during the process.
Chemical Finishing Methods
Chemical finishing processes in CNC machining involve the application of chemical agents to alter the surface of machined parts. Unlike mechanical methods that physically remove or deform the surface layer, chemical techniques modify the surface through chemical reactions, offering a different set of advantages and applications.
Chemical Milling
Chemical milling, also known as chem-milling or chemical etching, is a process that removes material from the surface of a part using controlled chemical reactions.
Technical Characteristics: This process involves protecting certain areas of the part with a maskant while exposing others to a chemical reagent that dissolves the unprotected metal. The depth and rate of material removal can be precisely controlled, allowing for the creation of complex shapes and features that might be difficult or impossible to achieve with traditional machining methods.
Materials and Applications: Chemical milling is used on a variety of metals, including aluminum, steel, copper, and titanium. It’s particularly beneficial for aerospace components, such as airframe structures, where reducing weight without compromising structural integrity is crucial.
Pros and Cons: The primary advantage of chemical milling is its ability to produce complex, precise features without inducing stress or mechanical deformation. However, the process requires careful handling of hazardous chemicals and can generate waste that must be properly managed.
Passivation
Passivation is a chemical process used to enhance the corrosion resistance of metals, particularly stainless steel, by removing free iron from the surface and promoting the formation of a thin, inert oxide layer.
Technical Characteristics: The process typically involves immersing the part in a passivating acid bath, such as nitric or citric acid, which removes surface contaminants and facilitates the formation of the protective oxide layer.
Materials and Applications: Passivation is essential for medical devices, food processing equipment, and any stainless steel components exposed to corrosive environments. It ensures the longevity and reliability of the parts by significantly reducing their susceptibility to corrosion.
Pros and Cons: Passivation significantly increases corrosion resistance and enhances the natural oxide layer without changing the part’s appearance. However, it’s only effective on certain materials, like stainless steel, and requires precise control of the chemical process to avoid damaging the parts.
Chemical Conversion Coatings
Chemical conversion coatings are used to deposit a protective coating on metal parts through a chemical reaction, improving their corrosion resistance, enhancing paint adhesion, and providing electrical insulation.
Technical Characteristics: This method involves immersing the part in a solution containing chemicals that react with the metal surface to form a protective film. Common types of conversion coatings include chromate coatings on aluminum and phosphate coatings on steel.
Materials and Applications: Conversion coatings are widely used in the automotive, aerospace, and electronics industries for parts that require enhanced corrosion protection and paint adhesion. They are suitable for aluminum, zinc, cadmium, magnesium, and steel surfaces.
Pros and Cons: Chemical conversion coatings offer excellent corrosion resistance and surface preparation for subsequent finishing processes. The main drawbacks include the need for precise chemical control and environmental concerns associated with certain chemicals, such as hexavalent chromium in chromate coatings.
Powder Coating
Powder coating is a dry finishing process where a powder material is electrostatically applied to a surface and then cured under heat to form a hard, protective layer.
Technical Characteristics: This process stands out for its ability to produce a thick, uniform coating without runs or sags, offering excellent durability and resistance to chipping, scratching, and corrosion. The range of available colors and finishes, from matte to high gloss, allows for significant aesthetic versatility.
Materials and Applications: Powder coating is predominantly used on metal surfaces, including steel, aluminum, and brass, making it a popular choice for automotive parts, outdoor furniture, and industrial equipment. Its robust nature ensures components withstand harsh environments and heavy use.
Pros and Cons: The advantages of powder coating include its environmental friendliness, emitting fewer volatile organic compounds (VOCs) than liquid coatings, and its durability. However, its application requires specialized equipment and cannot be easily applied to non-conductive materials.
Zinc Coating / Galvanising
Zinc coating, often achieved through a process known as galvanizing, involves applying a protective zinc layer to steel or iron to prevent rusting.
Technical Characteristics: Galvanizing can be performed through hot-dip processes, where the part is submerged in molten zinc, or electro-galvanizing, which applies zinc through an electrochemical process. Both methods provide excellent corrosion protection and increased longevity of the part.
Materials and Applications: Primarily used for steel and iron components, zinc coatings are essential in construction, automotive, and marine industries, where parts are exposed to corrosive environments.
Pros and Cons: While offering significant protection against corrosion, zinc coatings can be susceptible to white rust if exposed to wet conditions without adequate passivation. Additionally, the thickness of the coating needs to be carefully controlled to avoid brittleness in the part.
Alodine
Alodine, a brand name often used synonymously with chromate conversion coating, is a chemical treatment for aluminum that enhances corrosion resistance and provides a good primer for paint adhesion.
Technical Characteristics: This process involves treating aluminum parts with a chromic acid-based chemical solution that leaves a protective chromate layer on the surface. It can also improve electrical conductivity, making it suitable for electronic applications.
Materials and Applications: Alodine treatments are used extensively in the aerospace and electronics industries for parts that require a lightweight yet durable finish. It’s particularly beneficial for aluminum alloys prone to corrosion.
Pros and Cons: Alodine treatments offer the advantage of improving corrosion resistance and paint adhesion without adding significant weight or altering the part’s dimensions. However, environmental and health concerns associated with chromic acid use necessitate strict handling and disposal measures.
Black Oxide
Black oxide is a conversion coating for ferrous metals, stainless steel, copper, and copper-based alloys that provides a matte black finish, offering mild corrosion resistance and minimal dimensional change.
Technical Characteristics: The process involves a chemical reaction between the iron on the metal surface and the oxidizing salts in the black oxide solution, creating a magnetite layer on the part.
Materials and Applications: Common applications include firearms, automotive parts, and tools, where a non-reflective, corrosion-resistant surface is desirable. It’s also used for aesthetic purposes in architectural and consumer products.
Pros and Cons: Black oxide provides a visually appealing, durable finish that can retain lubrication on the surface, enhancing wear resistance. However, its corrosion protection is limited compared to other coatings and often requires supplemental oil or wax treatments.
Electrical/Electrochemical Finishing Methods
Electrical and electrochemical finishing processes offer unique advantages, including the ability to deposit metals or alloys onto surfaces, polish to a high luster, and create protective or functional coatings that significantly extend the life of CNC machined parts.
Electroless Nickel Plating
Electroless nickel plating is a chemical process that deposits a nickel-phosphorus or nickel-boron alloy onto the surface of a part without the use of electrical current.
Technical Characteristics: This autocatalytic process results in a uniform coating, even on complex geometries, providing excellent wear and corrosion resistance. The phosphorus content in the coating can be adjusted to modify properties such as hardness and magnetic response.
Materials and Applications: Electroless nickel plating is suitable for a wide range of substrates, including metals, plastics, and ceramics, making it versatile for industries like aerospace, automotive, and electronics. It’s particularly beneficial for parts requiring dimensional precision, such as hydraulic components and molds.
Pros and Cons: The process offers the advantage of even coating distribution, excellent adhesion, and enhanced corrosion resistance. However, it requires rigorous pre-treatment and cleaning processes, and the chemical solutions used can be environmentally hazardous if not properly managed.
Electroplating
Electroplating involves the deposition of a metal coating on a part through the use of an electric current.
Technical Characteristics: This process provides excellent control over the thickness and composition of the deposited layer, allowing for the enhancement of electrical conductivity, corrosion resistance, and aesthetic appeal. Common plating metals include gold, silver, copper, and zinc.
Materials and Applications: Electroplating is widely used across various industries, from electronics for PCBs and connectors to automotive for decorative and protective components. It’s also employed in the jewelry industry for plating precious metals onto less expensive bases.
Pros and Cons: Electroplating can significantly improve a part’s appearance and durability. However, the process can be complex, requiring careful control of solution chemistry and electrical parameters. Environmental concerns and the disposal of toxic waste products also pose significant challenges.
Electropolishing
Electropolishing is an electrochemical process that smooths and streamlines the microscopic surface of a metal part.
Technical Characteristics: By dissolving the outer layer of material, electropolishing reduces surface irregularities, resulting in a brighter, smoother finish. This process can also improve the part’s corrosion resistance and cleanability.
Materials and Applications: Primarily used for stainless steel, electropolishing is also applicable to aluminum, copper, and other alloys. It finds extensive use in the medical, food and beverage, and pharmaceutical industries, where hygiene and cleanability are paramount.
Pros and Cons: Electropolishing offers the dual benefits of enhanced aesthetic appeal and increased resistance to corrosion and contamination. However, it can be costly, and like other electrochemical processes, requires careful waste management and environmental controls.
Anodizing
Anodizing is an electrochemical process that enhances the natural oxide layer on the surface of metal parts, primarily aluminum. This method increases corrosion resistance, surface hardness, and wear resistance, while also allowing for the addition of colored dyes for aesthetic purposes.
Technical Characteristics: Anodizing involves immersing the aluminum part in an acid electrolyte bath and passing an electric current through the medium. This process thickens the natural oxide layer, making it more durable and resistant to corrosion.
Materials and Applications: Primarily used for aluminum, anodizing is ideal for aerospace, automotive, consumer electronics, and architectural applications where durability and cosmetic appearance are crucial.
Pros and Cons: Anodizing offers excellent corrosion and wear resistance, improved adhesion for paint primers, and aesthetic enhancement. However, it is limited to aluminum and its alloys and requires strict control over the electrolytic process to ensure uniformity and quality of the finish.
Anodizing Type I
Type I anodizing, or chromic acid anodizing, is the least common form, offering thinner coatings that retain a part’s dimensions and tolerances. It’s preferred for parts requiring tight tolerances and fatigue resistance, often used in aerospace applications for its ability to prevent stress-corrosion cracking.
Anodizing Type II
Type II, or sulfuric acid anodizing, is the most common form, providing a good balance between surface hardness and wear resistance. Suitable for a wide range of applications, from automotive to consumer goods, it allows for color dyeing, enhancing the part’s aesthetic appeal.
Anodizing Type III
Type III, known as hardcoat anodizing, produces the thickest and most durable oxide layers, significantly increasing wear and corrosion resistance. Ideal for industrial and military applications where extreme durability is required, it, however, reduces the part’s fatigue strength slightly due to the thicker coating.
Thermal Finishing Methods
Thermal Finishing Methods
Thermal finishing methods involve the use of heat or thermal energy to alter the surface properties of machined parts, improving their mechanical and physical characteristics.
Laser Engraving
Laser engraving is a non-contact thermal process that uses a laser beam to remove material from the surface of a part, creating permanent marks without affecting the part’s structural integrity.
Technical Characteristics: This method provides high precision and repeatability, allowing for intricate designs and legible markings on a variety of materials.
Materials and Applications: Suitable for metals, plastics, ceramics, and even wood, laser engraving is widely used for serial numbers, logos, and custom designs in industries ranging from medical devices to automotive manufacturing.
Pros and Cons: Laser engraving offers unmatched detail and precision, with the ability to mark almost any design. However, it can be limited by the material’s ability to absorb the laser energy, and the depth of engraving is generally shallow.
Heat Treating
Heat treating encompasses various processes used to alter the microstructure of materials, enhancing their mechanical properties such as strength, hardness, and ductility.
Technical Characteristics: Common heat treating processes include annealing, tempering, case hardening, and through hardening, each tailored to specific material requirements and desired outcomes.
Materials and Applications: Widely applicable to steel and other alloys, heat treating is essential in automotive, aerospace, and tool manufacturing, where enhanced material properties are critical for performance and durability.
Pros and Cons: Heat treating can significantly improve a part’s mechanical properties, making it more suitable for demanding applications. However, it requires precise control over temperature, time, and atmosphere to achieve consistent results and can sometimes lead to distortion if not properly managed.
Annealing
Annealing involves heating and then slowly cooling a material to reduce hardness and improve ductility, making it easier to work with and enhancing its machinability.
Tempering
Tempering is performed after hardening to decrease brittleness and achieve a desired balance of hardness and toughness.
Case Hardening
Case hardening increases the surface hardness of a part while maintaining a tough and ductile interior, ideal for parts subjected to high levels of wear.
Through Hardening
Through hardening heats the material and quenches it to achieve uniform hardness throughout the part, suitable for components requiring high strength and wear resistance.
Can You Combine Multiple Surface Finishes for CNC Machined Parts?
The feasibility of combining different surface finishes in CNC machining is not only possible but often encouraged for several reasons.
This multidimensional approach allows for the optimization of parts for specific applications, enhancing attributes such as corrosion resistance, wear resistance, and surface roughness, or simply for achieving a unique aesthetic appearance.
What are the Reasons for Combining Finishes?
Enhanced Performance: Combining finishes can significantly improve a part’s resistance to environmental factors, mechanical wear, and corrosion.
Aesthetic Appeal: Sequential finishes can achieve unique textures, colors, and gloss levels that a single process might not accomplish.
Customization: Tailoring surface finishes to meet specific customer or industry requirements can differentiate a product in the market.
Examples of Combined Finishes
Anodizing followed by Bead Blasting: This combination is popular for creating a uniform, matte surface on aluminum parts that are also resistant to corrosion and wear. Anodizing adds a hard, protective outer layer, while bead blasting gives the part a consistent, aesthetic finish without the typical glossiness of anodized surfaces alone.
Powder Coating after Chemical Conversion Coating: Applying a powder coat on top of a chemically converted surface enhances the adhesion of the powder coating and provides additional corrosion resistance, making this combination ideal for outdoor or harsh environment applications.
How Is Surface Finish Measured in CNC Machining?
Understanding the degree of surface finish achieved is crucial for ensuring that parts meet the required specifications and performance criteria. Measurement of surface finish in CNC machining involves several methods, each offering insights into the surface’s texture, irregularities, and overall quality.
Common Measurement Methods
Visual Inspection: While subjective, visual inspections can quickly identify major surface flaws.
Surface Roughness Testers: These devices measure the micro-irregularities on the surface, providing a quantitative roughness value.
Profilometers: By tracing a stylus over the surface, profilometers generate a detailed profile that can be analyzed to assess surface characteristics.
Common Measurement Units and Symbols for Surface Finish in CNC Machining
The quantification of surface finishes involves specific units and symbols that represent the average or peak-to-valley roughness of a surface. Understanding these metrics is essential for specifying, achieving, and verifying the desired surface quality.
Ra (Roughness Average): Represents the average surface roughness, measured in microinches (µin) or micrometers (µm). It’s the most commonly used parameter for general surface finish.
Rz (Average Maximum Height): Measures the average peak-to-valley height of the surface irregularities over a specified length.
RMS (Root Mean Square): Similar to Ra but calculated differently, providing a slightly different perspective on surface roughness.
Are CNC Machining Surface Finishes expensive?
The cost of CNC machining surface finishes can vary widely, influenced by factors such as the type of finish, material complexity, and the required precision level.
For instance, simple finishes like bead blasting might range from $30 to $50 per part, while more complex processes like anodizing or electroless nickel plating could escalate to $100 to $200 per part, depending on size and complexity.
It’s important to consult with manufacturers for specific quotes, as these ranges can fluctuate based on order volume, material costs, and additional processing requirements.
How long does CNC Machining Surface Finishing typically take?
Simple finishes might take a few hours to a day, whereas more complex treatments like anodizing or electroplating could extend from 24 to 48 hours, excluding prep and curing times. Factors influencing these durations include the finish type, part complexity, and the efficiency of the machining facility.
Planning for potential delays and understanding the specifics of each process can help manage timelines effectively, ensuring project deadlines are met without compromising on the quality of the finish.
How to Prepare CNC Machined Parts Before Applying Surface Finishes?
Preparing CNC machined parts for surface finishing is a critical step in the manufacturing process. It ensures that the final product meets the desired quality and aesthetic standards. Here’s how you can prepare your CNC machined parts for surface finishes:
Cleaning: Begin with thoroughly cleaning the parts to remove any machining fluids, oils, and residues. Ultrasonic cleaning or solvent-based methods are commonly employed to ensure parts are free of contaminants that could interfere with the finishing process.
Smoothing Edges: Burrs and sharp edges can negatively impact the finishing process. Use deburring techniques such as manual sanding, tumbling, or edge rounding machines to smooth out edges, ensuring a uniform application of the finish.
Ensuring Compatibility: Verify the compatibility of the material with the chosen finishing process. For instance, certain metals may require specific pre-treatments before anodizing or plating to achieve optimal adhesion and finish quality.
What are some common problems and defects with CNC Machining Surface Finishes?
Several issues can arise during the surface finishing of CNC machined parts. Understanding these problems and knowing how to prevent or fix them is crucial:
Orange Peel: A textured appearance resembling the skin of an orange, often due to improper powder coating application. Ensuring a uniform application and controlling the curing temperature can prevent this issue.
Blistering: Caused by moisture or air entrapment under the finish. Pre-heating parts to remove moisture and ensuring a clean, dry surface can mitigate blistering.
Peeling or Flaking: This can occur if the surface was not properly prepared or if there was inadequate adhesion. Mechanical or chemical surface preparation can enhance adhesion.
Scratches or Abrasions: Resulting from handling or process equipment. Handling parts with care and using protective coverings can reduce the risk of these defects.
Inconsistent Coloration: Especially in anodizing, this can be due to uneven surface texture or material composition. Homogeneous material selection and precise control of the anodizing process are key to consistency.
XTJ is a leading OEM Manufacturer that is dedicated to providing one-stop manufacturing solutions  from prototype to production. We are proud to be an ISO 9001 certified system quality management company and we are determined to create value in every customer relationship. We do that through collaboration, innovation, process improvements, and exceptional workmanship.