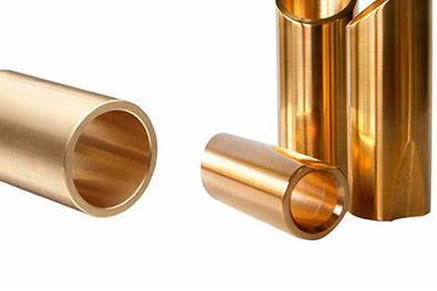
alloy not only retains some properties of each element, but it can have new properties not seen in either, which has revolutionized our modern material selection. The two alloys that started this shift are bronze and brass, which are ancient metallic alloys that have been used for thousands of years by the Greeks and other bygone empires. These metals provided the starting place for all other alloys, and this article will explore bronze and brass and how they differ. The physical, chemical, and mechanical properties of bronze and brass will be detailed, as well as how they are still used today. This article aims to show how these metals, while being more archaic than most other engineering materials, are still necessary components to our success in the modern era.
Table of Contents
What is Bronze
Bronze is the result of adding tin to copper, though there are often many additional side elements because bronze was discovered in about 3500 BC, before exact chemistry methods were developed. In the modern age, bronze is considered a class of copper alloys which have been defined based on their working properties and specific alloying elements. Metals such as lead, manganese, antimony, nickel, zinc, silicon, and more have been found to improve bronze and so designers now have a wide array of bronze grades to choose from. To learn more about the different types of bronze available, feel free to read our article on the types of bronze.
The typical bronze is a reddish-brown/gold color and is brittle, but less so than cast iron. It has a relative density of around 8.8 g/cm3 and exhibits low friction when in contact with other metals. It readily conducts heat and electricity and has a melting point range of 950 – 1050 °C, depending upon the amount of tin present. It oxidizes in the air due to its high copper content, which gives bronze a distinct mottled patina. This oxidation prevents bronze from corroding, especially in saltwater environments; however, if chlorine compounds can react with the bronze, a process that is known as “bronze disease” starts where corrosion breeds more corrosion, slowly destroying the alloy over time. It’s saltwater resistance has made bronze useful for boat fittings and submerged marine parts, as well as sculptures which must resist degrading in the outside environment. It portrays excellent casting properties and can be readily cast as bearings, clips, electrical connections, springs, and much more.
If you are interested in purchasing bronze for your project, feel free to browse our buying platform for bronze suppliers.
What is Brass
Brass was discovered around 500 BC and is an alloy of copper and zinc, though it too contains other elements just as with bronze. Since there is much overlap between brass and bronze, brass is usually denoted by its large percentage of zinc and the relative absence of tin (though, confusingly. tinned brass alloys also exist, further blurring the lines). Lead is a common additive in brass which increases its machinability, as well as other unique elements that have built the class of brass alloys.
Brass is a bright gold, copper, or even silver color, depending upon the ratio of zinc to copper. It is more ductile than bronze and exhibits similarly low friction when in contact with other metals. It has a density of around 8.73 g/cm3 and has a low melting point of 900 – 1000 °C, depending on the alloy. Brass is a great conductor of heat and is corrosion-resistant, especially to galvanic seawater corrosion. It casts well, is reasonably durable and attractive, and even possesses some antimicrobial qualities thanks to its high copper content. The most common uses for brass are in musical instruments, decorative trims, screws, radiators, bullet casings, and more.
If you are interested in purchasing brass for your project, feel free to browse our buying platform for brass suppliers.
Comparing Bronze & Brass
Even though these metals are related in both composition, appearance, and even applications, brass and bronze are often reserved for different purposes. It will be useful to explore what makes these two copper alloys distinct from each other by examining some common mechanical properties.
Comparison of material properties between bronze and brass.
Material properties |
Bronze |
Brass |
|||
Units |
Metric |
English |
Metric |
English |
|
Thermal Conductivity (20 °C) |
24 W/m-K |
15 Btu/(hr ft °F) |
120 W/m-K |
64.1 Btu/(hr ft °F) |
|
Fatigue Strength |
90.0-352 MPa |
13100-51100 psi |
22-360 MPa |
3190-52200 psi |
|
Melting Point (average) |
1010 °C |
917 °C |
|||
Hardness (Brinell) |
40 – 420 |
55-73 |
|||
Machinability (average) |
33.0% |
46.8% |
Thermal conductivity is a good measure to know if a metal will be used in thermal applications, because it shows how much energy can transfer through the material, and at what rate. The thermal conductivity of brass is much higher than that of bronze, making it an ideal choice for radiators. Bronze can also be used in thermal applications, but brass will always take precedence if there is a choice between the two.
Fatigue stress is stress caused by a high cycling of small stresses, which can introduce micro and even macro fractures into a material over a long period of time. This value is vital to understand if the material will be under consistent stress such as frequent changes in temperature or loads, which can chip away at the integrity of the alloy given enough cycles. The fatigue strengths of bronze and brass are given as ranges in Table 1, as there are many alloys of each metal. Bronze generally has a higher fatigue resistance than brass, which can be seen by comparing the lower bound of their fatigue strength ranges. This quality makes bronze more useful for marine parts and springs which undergo constant stresses when in use.
Brass has a lower average melting point than bronze , but they are both easily cast. If using either of these metals to cast shapes, consider the desired mechanical properties; a more resilient project will most likely benefit from bronze, while a more decorative one can use brass to great effect.
Hardness is a measure of a material’s response to local surface stresses and how it reacts to scratching, denting, etc. The Brinell hardness scale is one of the numerous hardness scales available and uses its own hardness indenter machine to grade a material’s response to a standardized force. For reference, typical glass scores 1500 on the Brinell hardness scale and lead scores 5; using these as benchmarks, Table 1 clearly shows that bronze is on average harder than brass. A harder material is usually more brittle, and bronze follows this rule by being much more prone to fracture than brass. If workability is a necessity, brass is by far the better choice than bronze. However, if strength and resistance to wear are of concern, bronze may be the better option.
Machinability is a comparative score given to metals to show how they react to machining stresses such as turning, milling, stamping, and other procedures. It is important to understand the machinability score of a metal, as it dictates what types of machining can be done, if any. A metal’s machinability percentage is in comparison to a reference metal, where this metal is given a 100% rating (being easily machined). A metal that is more difficult to machine is given a rating below 100%, which is the case with both bronze and brass. There are some alloys developed specifically for machining (e.g. brass alloy C360), but most copper alloys are too ductile to machine. Both metals have excellent casting characteristics, so consider a casting procedure before machining these metals. If it must be machined, make sure the alloy you choose is made for machining, or risk gumming up your mill.
Both bronze and brass come in many shapes, sizes, and compositions. As always, ask your supplier for the most up to date information on what is available and which type of bronze or brass will fit your application best.
XTJ is a leading OEM Manufacturer that is dedicated to providing one-stop manufacturing solutions from prototype to production. We are proud to be an ISO 9001 certified system quality management company and we are determined to create value in every customer relationship. We do that through collaboration, innovation, process improvements, and exceptional workmanship.