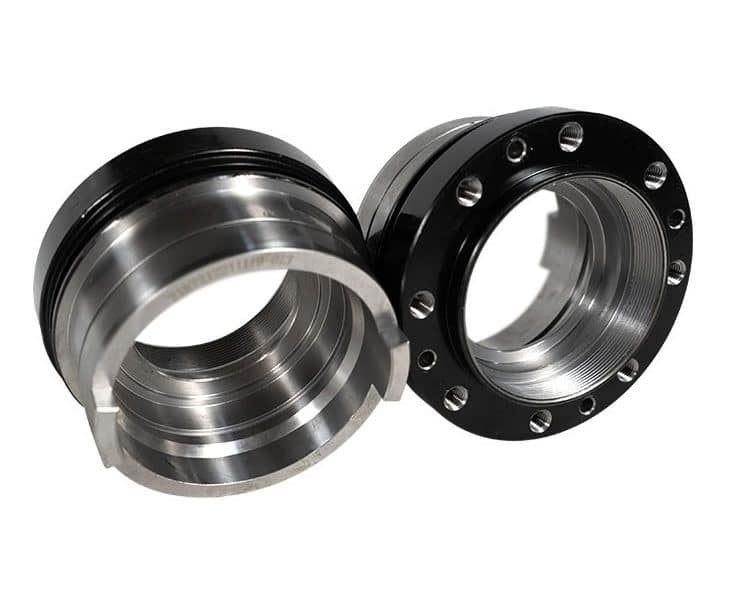
Table of Contents
What Is the Historical Evolution of Materials used in Machining?
The saga of machining materials is as old as civilization itself, evolving from the simple metals used in ancient tools to the sophisticated alloys of today. Initially, materials like bronze and iron marked significant advancements in machining, enabling the creation of more complex and durable tools.
The industrial revolution ushered in an era of experimentation, leading to the discovery of steel alloys and their varied applications. The 20th century saw a surge in technological advancements, introducing materials with unprecedented properties, tailored for specific industrial applications.
As technology advanced, so did the complexity of machining requirements. The need for materials that could withstand extreme conditions—such as high temperatures and corrosion—led to the development of superalloys and advanced polymers.
Innovations in aerospace, automotive, and medical industries further diversified the spectrum of materials, emphasizing the importance of properties like strength-to-weight ratio, corrosion resistance, and biocompatibility.
How are materials used for conventional machining different than the materials used for CNC machining?
Conventional machining and CNC machining differ not just in their process automation but also in the materials that best suit each method.
While machining is forgiving with a wide range of materials, CNC machining often requires materials with consistent mechanical properties to exploit its precision and repeatability. The latter’s capabilities to work with harder, more complex materials at tighter tolerances have expanded the material palette significantly.
For instance, alloy steel and titanium offer the strength and durability needed for aerospace components, while plastics like ABS and polycarbonate provide the versatility for consumer goods with complex geometries.
What are materials suitable for CNC machining but not suitable for conventional manual machining?
The precision and control offered by CNC machines allow them to handle materials with characteristics that are difficult, if not impossible, to machine manually.
Below we provide some common CNC machining materials that are difficulty to machine manually.
Hard-to-Machine Metals and Alloys
Titanium: Renowned for its strength-to-weight ratio and corrosion resistance, titanium is often used in aerospace and medical industries. Its machining difficulty arises from its hardness and the risk of it binding to cutting tools, a challenge adeptly managed by CNC’s precise speed and feed rate control.
Inconel: This superalloy is known for its ability to withstand extreme temperatures and corrosive environments, making it indispensable in the aerospace and chemical processing sectors. Its toughness makes it nearly impossible to shape and form through manual machining methods.
Stainless Steel 304 and 303: While these grades of stainless steel are popular in a variety of applications due to their corrosion resistance and strength, they can be particularly tricky to machine manually because of their hardness and work hardening properties. CNC machines, with their precise control, can effectively handle these materials.
Engineered Plastics
PEEK (Polyether Ether Ketone): A high-performance engineering plastic known for its excellent mechanical and chemical resistance properties. Manual machining of PEEK can be challenging due to its toughness and the need for precise temperature control during machining, which CNC machines can manage efficiently.
Polycarbonate: Used in bulletproof glass and other impact-resistant applications, polycarbonate requires precision machining to maintain its structural integrity, something that CNC machining can achieve but is challenging to replicate with manual methods.
Advanced Composites
Carbon Fiber Reinforced Plastics (CFRP): The directional strength of carbon fiber composites can make manual machining problematic, as it can lead to delamination or fraying. CNC machining can be programmed to cut along the fiber direction, minimizing these issues.
What Are the Most Common Materials Used in Machining?
Machining encompasses a wide range of materials, each selected based on the desired properties of the final product, such as strength, weight, corrosion resistance, and appearance.
Metals
Metals are the most commonly machined materials, prized for their strength, durability, and conductivity. Here’s a closer look at some of the most machined metals:
Stainless Steel: This alloy is durable, resistant to rust and high temperatures, making it a choice material for medical devices, cookware, and any application requiring a clean, corrosion-resistant surface.
Aluminum: Aluminum and its alloys are highly favored in manual machining for their lightweight and corrosion-resistant properties. This metal is ideal for aerospace, automotive, and consumer goods applications, where its ease of machining and excellent strength-to-weight ratio are highly valued. Aluminum grades such as 6061 are particularly sought after for manual machining projects due to their balance of machinability, weldability, and corrosion resistance.
Brass: Known for its golden appearance and excellent machinability, brass is often used for decorative items, gears, valves, and fittings. Its low friction coefficient and ability to resist tarnishing make it a preferred choice for applications requiring aesthetic appeal and moderate strength. Brass alloys, like C36000, are especially easy to machine, offering high-speed operations and fine finishes without the need for extensive tool wear.
Low Carbon Steel: Carbon steel, particularly low carbon varieties like 1018, is widely used in manual machining. Its popularity stems from its balance of ductility, strength, and machinability. Low carbon steel is often chosen for parts requiring good surface finish, dimensional accuracy, and weldability, making it suitable for a wide range of applications, from construction to machinery components.
Lead: Though used less frequently due to health and environmental concerns, lead’s low melting point and softness make it relatively easy to machine manually. It is typically used in applications requiring its high density, such as radiation shielding and battery manufacturing, where machining precision isn’t as critical.
Copper: Renowned for its exceptional electrical conductivity, copper is also valued in manual machining for its malleability and ductility. This metal is extensively used in electrical components, plumbing, and decorative arts. Copper’s thermal conductivity also makes it ideal for heat exchangers and radiator components, facilitating efficient machining without significant tool wear.
Bronze: An alloy of copper and tin, bronze stands out for its strength and corrosion resistance, alongside excellent machinability. Its historical use in bearings, bushings, and gears continues today, particularly in marine environments where its resistance to seawater corrosion is invaluable. Bronze alloys, like C93200 (SAE 660), are particularly favored for manual machining due to their ease of cutting and ability to achieve a fine finish.
Magnesium: Magnesium alloys are the lightest structural metals, offering a superb strength-to-weight ratio alongside good machinability. They are commonly used in automotive and aerospace industries for components where weight reduction is critical. Despite its flammability during machining, with proper precautions, magnesium can be safely machined manually to produce lightweight, strong parts.
Nickel Silver (German Silver): Despite its name, nickel silver contains no silver but is an alloy of nickel, copper, and zinc. It offers excellent corrosion resistance, a decorative silver-like appearance, and good machinability. This material is often used for musical instruments, architectural hardware, and decorative items, where it can be easily shaped and polished in manual machining processes.
Tool Steel: Tool steels are carbon and alloy steels known for their hardness, resistance to abrasion and deformation, and ability to hold a cutting edge at high temperatures. They are widely used in the manufacture of tools, molds, and dies. With a variety of grades available, tool steels like W1 (Water-hardening) and O1 (Oil-hardening) are particularly suitable for manual machining, offering a balance of wear resistance and machinability for detailed work requiring precise tolerances and finishes.
Plastics
Here are ten plastics that are widely recognized for their suitability in machining operations:
ABS (Acrylonitrile Butadiene Styrene): Known for its toughness and impact resistance, ABS is a common choice for automotive parts, consumer goods, and prototypes. Its ease of machining and excellent surface finish capabilities make it ideal for manual machining.
Nylon: Renowned for its wear resistance and strength, nylon is used in gears, bearings, and other mechanical components. Its ability to absorb moisture can affect dimensional stability, thus requiring consideration during the machining process.
Polycarbonate: This plastic is prized for its impact resistance and transparency, making it suitable for protective gear, windows, and lenses. Polycarbonate can be machined manually to produce intricate parts with precision.
POM (Polyoxymethylene), also known as Delrin: Offers high stiffness, low friction, and excellent dimensional stability, making it a favorite for precision parts that require a high degree of accuracy and smooth operation.
PTFE (Polytetrafluoroethylene), commonly known as Teflon: Noted for its high heat resistance and non-stick properties, PTFE is often used in seals, gaskets, and bearings. It requires careful machining due to its softness and propensity to deform under load.
PMMA (Polymethyl Methacrylate), also known as acrylic: Acrylic is chosen for its clarity and resistance to UV light, ideal for lenses, windows, and signs. It can be machined to a high-quality finish with sharp tools and proper techniques.
PEEK (Polyether Ether Ketone): This high-performance plastic offers exceptional heat resistance, mechanical strength, and chemical resistance. It is used in demanding applications such as aerospace, medical implants, and automotive components. Despite its toughness, it can be manually machined with specialized tooling.
PVC (Polyvinyl Chloride): PVC is used for a wide range of industrial and construction applications due to its chemical resistance and strength. It machines well, producing smooth surfaces and precise dimensions with the right tooling.
UHMWPE (Ultra High Molecular Weight Polyethylene): Known for its high abrasion resistance and impact strength, UHMWPE is used in wear-resistant applications like liners, gears, and bearings. It is also favored for its ease of machining.
HDPE (High-Density Polyethylene): HDPE is used in a variety of products, from piping systems to storage containers, due to its high strength-to-density ratio. It machines well, allowing for the production of components with tight tolerances and smooth finishes.
Other Materials
Beyond the realm of metals and plastics, several materials can be efficiently machined with conventional techniques, providing alternatives that meet the unique requirements of certain projects.
Here is a list of the most popular ones
Wood: Wood is one of the oldest materials used in machining for creating furniture, musical instruments, and decorative items. Its ease of machining, availability, and aesthetic appeal make it a popular choice.
Graphite: Used in the production of electrodes for electrical discharge machining (EDM) and for high-temperature crucibles, graphite is favored for its conductivity and heat resistance. It requires careful handling during machining due to its brittleness.
Ceramics: Advanced ceramics offer high hardness, heat resistance, and chemical stability, making them suitable for aerospace components, cutting tools, and medical devices. Manual machining of ceramics requires specialized tools and techniques due to their brittleness.
Rubber: For gaskets, seals, and flexible couplings, rubber can be manually machined into various shapes. Its elasticity and compressibility pose unique challenges that necessitate specific machining practices.
Silicone: Used in medical devices, kitchen utensils, and seals due to its biocompatibility and heat resistance. Silicone’s flexibility requires precise control during manual machining.
Fiberglass: Reinforced plastic material used in automotive body panels, boat hulls, and construction. It offers strength and durability, although machining releases fine particles that necessitate proper ventilation.
Carbon Fiber: Known for its lightweight and high strength, carbon fiber is used in racing cars, aerospace, and sporting goods. Manual machining must be carefully managed to avoid delamination.
Epoxy Resins: Often used in composite materials for aerospace, automotive, and marine applications, epoxy resins can be manually machined into precise shapes for molds or prototypes.
Foam: Lightweight foams are used for molds, prototypes, and packaging. They are easily machined manually for custom shapes but require tools that minimize tearing.
Phenolic: A hard, dense material made from phenol-formaldehyde resin, used for electrical insulators and industrial laminates. Its wear resistance and insulation properties make it suitable for precise manual machining.
Gypsum: Used in prototyping and mold making, gypsum can be finely machined to detailed specifications for casting applications in art and industry.
Stone: Including marble and granite, stone is machined for countertops, architectural elements, and artistic sculptures. While harder to machine, it offers unmatched durability and natural beauty.
What is the most used machining material?
Aluminum stands as the most utilized material in conventional machining. Its popularity is attributed to its exceptional machinability, lightweight, and corrosion resistance.
What material is easiest to machine?
Brass is recognized as the easiest material to machine. Known for its softness and ductility compared to other metals, brass allows for smooth machining operations, producing clean cuts and excellent surface finishes with minimal tool wear.
Which material is difficult to machine?
Titanium is known to be one of the most challenging materials to machine manually due to its high strength and low thermal conductivity. These characteristics cause it to generate excessive heat during machining, leading to tool wear and potential difficulties in maintaining precise tolerances.
How Do Material Properties Influence Machining Techniques?
The properties of materials, such as hardness, malleability, thermal conductivity, and toughness, play a pivotal role in determining the appropriate machining techniques.
Materials with high hardness levels, like tool steel, demand specific cutting tools and slower machining speeds to minimize tool wear and achieve desired finishes.
Conversely, malleable materials like aluminum allow for faster speeds and more aggressive cutting techniques, optimizing production efficiency.
Thermal conductivity affects how quickly heat is dissipated from the cutting zone, influencing tool choice and cooling needs.
Materials that retain heat, such as titanium, require techniques that minimize heat buildup to prevent damage to both the workpiece and the tool.
Additionally, the toughness of a material can affect chip formation processes, necessitating adjustments in tool geometry, feed rates, and speeds to ensure clean cuts and prevent material deformation.
How Do You Choose the Right Material for Machining?
Selecting the appropriate material for a machining project is a crucial decision that significantly impacts the outcome of the manufacturing process.
Here are 10 factors 3erp thinks are most important when choosing a material for machining, especially in the context of manual conventional machining.
Material Properties: Strength and Hardness
The material’s strength and hardness determine its ability to withstand forces and wear. Softer materials may be easier to machine but may not offer the durability needed for the application.
Corrosion Resistance
For components exposed to harsh environments, materials with high corrosion resistance are essential to ensure longevity and reliability.
Thermal and Electrical Conductivity
Certain applications may require materials with specific thermal or electrical properties. For instance, copper’s high electrical conductivity makes it ideal for electrical components.
Machinability
Machinability refers to how easily a material can be cut into the desired shape. Materials with good machinability result in smoother finishes and longer tool life.
Thermal Expansion
Understanding the material’s coefficient of thermal expansion is crucial for parts that will experience temperature variations, ensuring dimensional stability across different conditions.
Cost
The raw material cost can significantly impact the overall project budget. Balancing material performance with cost efficiency is vital for economic viability.
Weight Requirements
In industries like aerospace and automotive, lightweight materials are preferred to improve fuel efficiency and performance.
Availability
Material availability can affect lead times and project schedules. Choosing readily available materials can expedite the manufacturing process.
Environmental Impact
Sustainability concerns may influence material selection, favoring materials with a lower environmental footprint or those that are recyclable.
Specific Application Needs
The intended use of the part may dictate specific material properties, such as biocompatibility for medical devices or wear resistance for mechanical components.
How to Address Common Issues in Machining Different Materials?
Machining various materials can present a set of unique challenges. Understanding these challenges and how to address them is crucial for maintaining efficiency, achieving precision, and ensuring the longevity of both the tools and the machined parts.
Here are solutions and preventive measures for some common problems encountered in conventional machining.
Tool Wear
Regular inspection and maintenance of cutting tools to catch signs of wear early.
Use of appropriate tool materials and coatings to extend tool life.
Material Deformation
Properly securing the workpiece to minimize vibrations and potential deformation.
Adjusting cutting speed and feed rate to reduce forces on the material.
Heat Generation
Implementing cooling or lubrication systems to dissipate heat efficiently.
Adjusting machining parameters to prevent excessive heat buildup.
Surface Finish Quality
Using sharp, properly maintained tools to ensure clean cuts.
Fine-tuning machining parameters like speed, feed rate, and depth of cut for optimal surface finish.
Dimensional Accuracy
Regular calibration of machines to ensure accurate movements and dimensions.
Taking material thermal expansion into account when setting dimensions.
Chatter and Vibrations
Ensuring all machine components and workpiece setups are rigid and securely clamped.
Adjusting cutting conditions or using dampening devices to reduce vibrations.
Burrs Formation
Employing sharp tools and appropriate cutting conditions to minimize burr formation.
Implementing deburring processes as part of the post-machining workflow.
Material Waste
Planning machining paths efficiently to maximize material usage.
Recycling or reusing scrap material whenever possible.
Difficulty in Machining Hard Materials
Preparing the material surface through annealing or other softening processes before machining.
Utilizing carbide or other hard cutting tools designed for tough materials.
Maintaining Tool and Workpiece Temperature
Using coolant fluids or air blasts to keep both tool and workpiece at manageable temperatures.
Adjusting machining pace to allow intermittent cooling periods.
What Are the Cost Implications of Different Machining Materials?
The choice of materials for machining projects significantly affects both the initial costs and the overall value of the manufacturing process.
The cost associated with machining materials is not solely based on the raw material price but is influenced by a variety of factors, including:
Material Availability: Scarce materials often come with higher prices due to limited supply.
Machinability: Materials that are difficult to machine may require more time, specialized tools, and advanced techniques, increasing production costs.
Tool Wear: Hard materials may accelerate tool wear, necessitating more frequent replacements and thereby elevating costs.
Finish and Precision Requirements: Achieving high precision and surface finishes can increase machining time and costs, especially with materials that require slower feed rates or additional finishing processes.
Waste Management: Materials that produce significant waste or require special disposal methods can introduce additional costs.
To optimize the balance between material performance and cost, consider the following tips:
Assess the Entire Lifecycle Costs: Include considerations for durability, maintenance, and lifespan of the material in cost evaluations.
Explore Alternative Materials: Sometimes, less expensive materials can meet the project requirements when treated or processed appropriately.
Leverage Material Machinability: Opt for materials known for their ease of machining to reduce labor and tooling costs.
Minimize Waste: Select materials and machining strategies that maximize yield and minimize waste.
Bulk Purchasing: For large projects, bulk purchasing of materials can offer cost savings.
Consider Recycled Materials: When applicable, recycled materials can provide a cost-effective and environmentally friendly option.
Tooling Investment: Invest in high-quality tools that can withstand the machining of harder materials to reduce frequent replacements.
Efficient Design: Design parts with manufacturing in mind to minimize complex machining operations.
Supplier Relationships: Build strong relationships with suppliers to negotiate better prices or discover cost-saving opportunities.
Stay Informed: Keep abreast of market trends and new materials that may offer cost advantages without compromising quality.
XTJ is a leading OEM Manufacturer that is dedicated to providing one-stop manufacturing solutions  from prototype to production. We are proud to be an ISO 9001 certified system quality management company and we are determined to create value in every customer relationship. We do that through collaboration, innovation, process improvements, and exceptional workmanship.