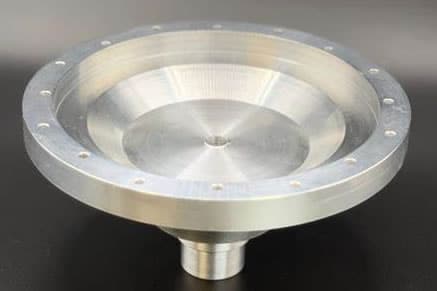
Table of Contents
What is Cast Iron?
Cast iron is made from pig iron, which is the product of melting iron ore in a blast furnace. Cast iron can be made directly from the molten pig iron or by re-melting pig iron, often along with substantial quantities of iron, steel, limestone, and carbon (coke), and taking various steps to remove undesirable contaminants.
Phosphorus and sulfur may be burnt out of the molten iron, but this also burns out the carbon, which must be replaced. Depending on the application, carbon, and silicon content are adjusted to the desired levels, which may be anywhere from 2–3.5% and 1–3%, respectively.
If desired, other elements are then added to the melt before the final form is produced by casting.
Cast iron is sometimes melted in a special type of blast furnace known as a cupola, but in modern applications, it is more often melted in electric induction furnaces or electric arc furnaces. After melting is complete, the molten cast iron is poured into a holding furnace or ladle.
Cast iron is a group of iron-carbon alloys with a carbon content of more than 2% to 4%. In addition, varying amounts of silicon from 1 to 3% by weight and manganese as well as traces of impurities such as sulfur and phosphorus. Cast iron is made by reducing Iron Ore in a Blast Furnace.
The liquid iron is poured or cast and hardened into crude ingots called pigs, and the pigs are then remelted along with scrap and alloying elements in cupola furnaces and recast into molds to produce a variety of products.
The alloying ingredients affect its color when breaks: white cast iron has carbide impurities that allow cracks to pass easily, gray cast iron has graphite flakes that deflect a passing crack and initiate countless new cracks as the material breaks and ductile cast iron has spheroidal graphite “nodules” that stop the crack prevent further progress.
With the exception of malleable iron, cast iron tends to be brittle. With its relatively low melting point, good fluidity, castability, excellent machinability, deformation resistance, and wear resistance, cast iron has become an engineering material with a wide range of applications.
What is Steel?
Steel is made of an alloy of iron and carbon in which the carbon content ranges up to 2 % (with higher carbon content, the material is defined as cast iron).
Iron, the major elemental component of steel, is one of the most plentiful elements in the earth’s crust. All steel alloys are primarily iron and 0.002–2.1 % carbon by weight. In this range, carbon bonds with iron create a strong molecular structure.
The resulting lattice microstructure helps achieve certain material properties, like tensile strength and hardness, that we rely on in steel.
Although all steel is made of iron and carbon, different types of steel contain different percentages of each element. Steel can also include other elements like nickel, molybdenum, manganese, titanium, boron, cobalt, or vanadium.
Adding different elements to the “recipe” for a steel alloy affects its material properties. The method of manufacture and treatment of the steel further enhances those abilities.
One notable group of steel alloys contains chromium. All such alloys are known commonly as stainless steel.
Steel is an alloy made up of iron with typically a few tenths of a percent of carbon to improve its strength and fracture resistance compared to other forms of iron. Many other elements may be present or added. Stainless steels that are corrosion– and oxidation-resistant need typically an additional 11% chromium.
Because of its high tensile strength and low cost, steel is used in buildings, infrastructure, tools, ships, trains, cars, machines, electrical appliances, and weapons. Iron is the base metal of steel.
Depending on the temperature, it can take two crystalline forms (allotropic forms): body center cubic and face center cubic. The interaction of the allotropes of iron with the alloying elements, primary carbon, gives steel and cast iron their range of unique properties.
In pure iron, the crystal structure has relatively little resistance to the iron atoms slipping past one another, and so pure iron is quite ductile, or soft and easily formed. In steel, small amounts of carbon, other elements, and inclusions within the iron act as hardening agents that prevent the movement of dislocations.
What are the Properties of Cast iron?
Properties of Cast iron
1. Hardness. Cast iron is hard and it can be hardened by heating and sudden cooling.
2. Toughness. Material’s ability to absorb energy.
3. Ductility. Material’s ability to deform without fracture.
4. Elasticity.
5. Malleability.
6. Tensile strength.
7. Fatigue strength.
8. Melting Point.
What Are The Uses Of Cast Iron?
Applications of cast iron
1. It is used in making pipes, to carry suitable fluids.
2. It is used in making different machines.
3. It is used in making automotive parts.
4. It is used in making pots pans and utensils.
5 It is used in making anchors for ships.
What Is The Difference Between Cast Iron & Steel?
The main difference between the two elements is that steel is produced from iron ore and scrap metals, and is called an alloy of iron, with controlled carbon. Whereas around 4% of carbon in iron makes it cast iron, and less than 2% of carbon makes it steel.
Cast iron is cheaper than most steel. Also, the cast iron melting temperature is lower than that of steel, but it has high compressive strength, high hardness, and high wear resistance. Therefore, the important difference between steel and cast iron is that steel is ductile and malleable, whereas cast iron is hardened and has high compressive strength.
As another important difference between steel and cast iron, we can say that carbon in steel is in the form of iron carbide while cast iron has carbon as graphite or iron carbide or both. In addition, cast iron has excellent fluidity, with no steel.