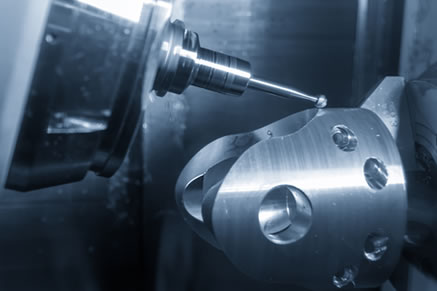
CNC machines have revolutionized precision manufacturing with their speed, accuracy, and ability to create complex geometries. From automotive parts to intricate designs, CNC cutting has become an integral part of the manufacturing industry. In this ultimate guide, we will explore the process, tools, materials, and technology behind CNC cutting, providing you with expert tips and techniques for successful implementation.
Understand the CNC machining process and its history.
The history of CNC machining dates back to the 1940s when it was initially developed for military applications. Over the years, advancements in computer technology and automation have led to the widespread adoption of CNC machining in various industries.
CNC machining relies on Computer-Aided Manufacturing (CAM) software, which generates the machine instructions necessary for cutting, drilling, and shaping materials. These instructions, known as G-code, are based on a 3D model of the desired part or component.
The CNC Machining Process
The CNC machining process involves several steps, starting with the creation of a 3D model using Computer-Aided Design (CAD) software. Once the model is complete, it is exported to CAM software, which generates the G-code instructions.
Next, the chosen material for CNC machining is securely clamped to the machine’s worktable. The cutting tools, such as drills, end mills, or lathe tools, are selected based on the material and design requirements. The G-code instructions guide the machine’s movements, directing the cutting tools to remove excess material and shape the workpiece.
CNC machining offers remarkable versatility, as it can be used with various materials, including:
Aluminum
Steel
Brass
ABS
Delrin
Nylon
The ability to work with such a wide range of materials makes CNC machining suitable for numerous applications across industries like automotive, aerospace, electronics, and more.
Overall, CNC machining offers unparalleled precision, speed, and repeatability, making it an invaluable technique in modern manufacturing. With CAM software and G-code driving the process, CNC machining continues to push the boundaries of what is possible in terms of design complexity and production efficiency.
Types of CNC Machines for Cutting
When it comes to CNC cutting, there are various types of CNC machines designed for specific purposes. Each machine brings its own set of capabilities and advantages to the table. Let’s explore the different types of CNC machines commonly used in the industry:
CNC Routers
CNC routers are incredibly versatile machines that can produce a wide range of shapes and designs. They are commonly used in woodworking, sign making, and fabrication industries. CNC routers utilize rotating cutting tools to remove material from the workpiece, resulting in precise and intricate cuts.
Read What kinds of milling cutters are there?
CNC Lathes
CNC lathes are specifically designed for turning operations, which involve creating cylindrical shapes from wood, metal, or plastic workpieces. These machines rotate the workpiece while a cutting tool shapes it into the desired form. CNC lathes are commonly used in the production of furniture components, sports equipment, and artistic objects.
CNC Plasma Cutters
CNC plasma cutters are known for their ability to engrave and etch designs into various materials, including wood. These machines use a high-velocity jet of ionized gas, known as plasma, to cut through the workpiece. CNC plasma cutters are widely used in metal fabrication, automotive, and artistic industries.
CNC Mills
CNC mills excel at creating highly detailed designs and manufacturing molds and intricate parts. These machines use rotating cutting tools to remove material from the workpiece, resulting in precise and accurate cuts. CNC mills are extensively used in the aerospace, automotive, and medical industries.
CNC Laser Cutters
CNC laser cutters are renowned for their exceptional accuracy and ability to produce intricate designs. They employ a high-powered laser beam to cut or engrave materials with precision. CNC laser cutters are commonly used in industries that require fine detailing, such as jewelry making, prototyping, and signage.
Each type of CNC machine offers unique capabilities, allowing manufacturers to choose the most suitable one for their specific cutting needs. By leveraging these advanced machines, businesses can achieve faster production, superior accuracy, and increased efficiency in their cutting processes.
CNC Machine Main Use
CNC Router Woodworking, Sign Making, Fabrication
CNC Lathe Turning Wood, Metal, or Plastic
CNC Plasma Cutter Engraving, Etching, Metal Fabrication
CNC Mill Detailed Designs, Mold Making, Precision Parts
CNC Laser Cutter Intricate Designs, Fine Detailing
Basics of CNC Machining Wood
CNC machining wood is a precise and efficient process that utilizes computer-controlled machines to shape and cut wood into desired designs. This method, also known as computer numerical control, offers numerous advantages over traditional woodworking techniques. Understanding the basics of CNC machining wood is essential for achieving accurate and high-quality results.
The process of CNC machining wood begins with designing the product using CAD (Computer-Aided Design) software. CAD software allows users to create detailed and intricate 2D or 3D models of their desired design. Once the design is finalized, it is exported to CAM (Computer-Aided Manufacturing) software.
The CAM software takes the CAD model and generates the necessary instructions, known as G-code, for the CNC machine. This code includes information about the tool paths, cutting speeds, and other parameters required for the machining process. The G-code is then loaded onto the CNC machine.
Before the wood can be machined, proper preparation and setup are necessary. The wood material should be selected based on the desired outcome and characteristics such as hardness, grain pattern, and durability. Additionally, the wood must be securely clamped onto the machine’s worktable to ensure stability during the machining process.
Once the wood is prepared and secured, the CNC machine is ready for machining. The cutting tool, such as a router bit or drill bit, is carefully positioned and programmed to follow the path defined by the CAM software. The CNC machine then executes the programmed instructions, cutting and shaping the wood into the desired design.
After the machining process is complete, additional finishing may be required to achieve a smooth and polished final product. Finishing techniques such as sanding, staining, and varnishing can enhance the appearance and durability of the wood.
Overall, CNC machining wood offers unparalleled precision, efficiency, and consistency in woodworking. It allows craftsmen and manufacturers to create intricate designs and achieve consistent results. By harnessing the power of CAD and CAM software, woodworkers can unlock the full potential of CNC machining and elevate their woodworking projects to new heights.
Advantages of CNC Machining Wood Wood Selection for CNC Machining Cutting Tool Selection
Precision
Efficiency
Consistency
Waste Reduction
Hardwoods
Softwoods
Engineered woods
Cutting Tool Material
Shape and Diameter
Flutes
Spindle Speed
Feed Rate
Benefits and Tools of CNC Machining Wood
CNC machining wood offers a multitude of benefits that surpass traditional woodworking methods. One of its main advantages is the unmatched precision it offers. The computer-controlled machines ensure accuracy down to the smallest details, resulting in flawless and consistent cuts every time. This precision allows for intricate and complex designs that were once difficult to achieve.
Not only does CNC machining wood provide precision, but it also increases efficiency. The automated process significantly reduces production time compared to manual labor. With the ability to perform multiple operations simultaneously, CNC machines streamline the manufacturing process, allowing for faster turnaround times and increased productivity.
In addition to precision and efficiency, CNC machining wood brings consistency to the table. The computer-controlled machines ensure that each piece is cut and shaped exactly according to the programmed design. This consistency is essential for large-scale production or when creating identical parts, ensuring uniformity and quality across the board.
Another notable benefit is the reduction of wasted materials. CNC machines optimize cuts, minimizing material waste and maximizing the utilization of wood. This not only reduces costs but also contributes to a more sustainable manufacturing process by minimizing environmental impact.
When it comes to CNC machining wood, selecting the right tools is crucial for optimal results. Factors such as cutting tool material, shape, diameter, flutes, spindle speed, and feed rate should be considered. Each wood type requires different considerations, and understanding the characteristics of different types of wood is essential for successful CNC machining.
Whether you’re working with hardwoods, softwoods, or engineered woods, CNC machining provides the precision, efficiency, consistency, and waste reduction necessary for high-quality woodworking. By properly selecting the cutting tools and considering the unique properties of each wood type, you can unlock the full potential of CNC machining wood.
XTJ is a leading OEM Manufacturer that is dedicated to providing one-stop manufacturing solutions of Machining 6061 Aluminum from prototype to production. We are proud to be an ISO 9001 certified system quality management company and we are determined to create value in every customer relationship. We do that through collaboration, innovation, process improvements, and exceptional workmanship.lication: Automotive industry, Bicycle and motorcycle, Door and windows and furniture, Household appliance, Gas meter, Power tool,LED lighting, Medical instrument parts, ect.