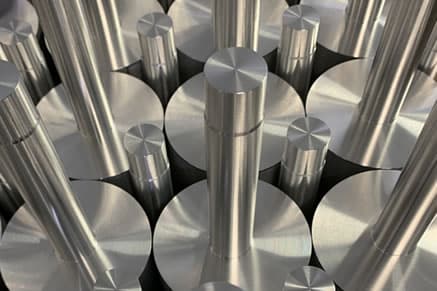
Table of Contents
What is a CNC Machine Shop?
1. What is a CNC Machine Shop?
A CNC machine shop is an environment where machining, a form of subtractive manufacturing, is performed. Machining involves the use of various tools to shape, cut, and modify raw materials like metal, plastic, or composites into precise parts and components. These facilities are equipped with an array of machine tools, such as lathes, milling machines, and drill presses, each serving a unique purpose in the manufacturing process
Exploring the Evolution of Machine Shops
The history of machine shops is a testament to human innovation and technological advancement. From manual operations in the early 19th century to the integration of computer numerical control (CNC) in the late 20th century, the journey of machine shops reflects the evolution of manufacturing practices.
19th Century: The advent of industrialization saw the rise of basic machine tools.
20th Century: The era of mass production and the introduction of CNC technology.
21st Century: Advanced automation, AI, and robotics redefine machining operations.
What Does a Machine Shop Do?
Machine shops are vital in producing intricate parts that form the backbone of various machines and structures. They offer a plethora of services, including milling, turning, drilling, and grinding. These processes are crucial in creating components with precise dimensions and tolerances, essential in industries like aerospace, automotive, and construction.
Milling: Involves removing material using rotary cutters.
Turning: The process of cutting a workpiece while it rotates.
Drilling: Creating cylindrical holes in a workpiece.
Grinding: Using an abrasive wheel to finish surfaces and achieve high accuracy.
The Structure of a Machine Shop
In the heart of manufacturing industries, the machine shop stands as a cornerstone, orchestrating the symphony of creation from raw materials to precision parts. Key components of a machine shop include a variety of machines, tools, and a well-planned layout, all integral to its efficient operation.
Machines: The primary instruments of production, ranging from lathes to milling machines.
Tools: An array of cutting tools, hand tools, and machining tools, each serving a unique purpose.
Layout: Strategically designed for optimal workflow, safety, and productivity.
Storage: Organized areas for storing raw materials, tools, and finished products.
Machines in a Machine Shop
A machine shop is akin to an artist’s studio, where each machine tool is like a different paintbrush, each contributing uniquely to the masterpiece.
Lathe: A cornerstone in machining, used for shaping materials by rotating them against cutting tools. It’s essential for tasks requiring precision, such as crafting cylindrical parts.
Milling Machine: Versatile and powerful, a milling machine removes material using a rotating cutter, ideal for creating complex shapes and surfaces.
Drill Press: Specialized for making precise holes, drill presses are pivotal in any machining operation.
Grinding Machine: Used for finishing operations, providing a high-quality surface finish and precise dimensions.
CNC Machines: Representing the pinnacle of modern machining, CNC machines automate operations, enhancing precision and reducing human error.
Different Tools Used in a Machine Shop
Here’s an expanded list of various tools used in a machine shop and their unique functions:
Cutting Tools: These include end mills, drills, and turning tools made of high-speed steel or carbides. They are used for cutting, shaping, and removing material from a workpiece.
Hand Tools: Comprising wrenches, hammers, and screwdrivers, hand tools are essential for manual adjustments and assembly tasks within the shop.
Measuring Instruments: Precision is key in machining, and tools like calipers, micrometers, and gauges are used to measure the dimensions and tolerances of machined parts accurately.
Power Tools: These are electrically or pneumatically driven tools like power drills and saws, used for a range of cutting and shaping tasks.
Workholding Devices: Including vises, chucks, and clamps, these tools are used to hold the workpiece securely in place during machining operations.
Deburring Tools: Essential for removing burrs and smoothing edges after machining, ensuring the safety and quality of the finished parts.
Coolant Systems: Used to keep cutting tools and workpieces cool during machining, thereby extending tool life and preventing material deformation.
Sawing Machines: For cutting raw materials into manageable sizes, band saws and circular saws are commonly used.
Specialized Tools: Depending on the specific requirements of a project, specialized tools like broaching machines, honing machines, and thread cutting machines may be utilized.
Understanding CNC Machines in a Machine Shop
The era of CNC (Computer Numerical Control) machining marks a revolutionary shift in the manufacturing process. CNC technology, governed by computer-aided design (CAD) and computer-aided manufacturing (CAM), brings unmatched precision and efficiency to machine shops.
CNC machines, ranging from mills to lathes, operate with minimal human intervention, translating digital designs into physical parts with intricate details and complex geometries. This technology is a game-changer in industries like aerospace and automotive, where precision and repeatability are paramount.
CNC machining has significantly reduced the margin for human error, bringing a new level of consistency and speed to production. The integration of CNC machines in modern machine shops not only streamlines the manufacturing process but also opens up new possibilities in terms of design complexity and material utilization.
As a result, a modern CNC machine shop is at the forefront of technological innovation, continually pushing the boundaries of what is possible in manufacturing.
Machine Shop as a Business
Operating a machine shop transcends the mere provision of machining services; it encapsulates a dynamic business enterprise, brimming with both challenges and opportunities. Business owners in this realm must navigate a landscape marked by technological advancements, evolving customer needs, and the constant pursuit of efficiency and quality.
Challenges in the Industry: The path of running a machine shop is not without its hurdles. Key challenges include the substantial investment in machining equipment and technology, the necessity for skilled machinists and ongoing training, and the relentless competition within the manufacturing industries. Furthermore, staying abreast of industry news and technological developments, like CNC machining and robotics, is crucial for staying competitive.
Opportunities for Growth: Amidst these challenges, however, lie significant opportunities. Machine shops, particularly those specializing in CNC machine shops or offering unique machining tasks, can carve a niche in sectors like the aircraft industry or automotive manufacturing. Embracing advanced technologies, such as computer numerical control and automation, can lead to increased efficiency, precision, and the ability to undertake complex machining operations, thereby attracting a broader clientele.
What are the different machining types and techniques offered by a machine shop?
Machining, the backbone of any machine shop, encompasses a diverse array of types and techniques, each tailored to specific needs and materials. Understanding these various methods is crucial for both machinists and customers, as it directly impacts the quality, precision, and applicability of the finished product.
Different Machining Types and Techniques:
Turning: Utilizing lathes, turning involves rotating the workpiece against a cutting tool. It’s commonly used for creating cylindrical parts and is a staple in many machining processes.
Milling: Milling machines, equipped with cutting tools like milling cutters, are used for removing material from a workpiece. Milling is versatile, allowing for the creation of a variety of shapes and sizes.
Drilling: Employing drill presses, drilling creates round holes in materials. This fundamental machining task is essential in almost every manufacturing project.
Grinding: Grinding machines, using a grinding wheel, provide a fine finish and precise dimensions. This process is often used for the final touch on metal parts, ensuring smooth surfaces and tight tolerances.
CNC Machining: Standing at the forefront of modern machining, CNC (Computer Numerical Control) technology automates the machining process, reducing human error and enhancing precision. This technique is integral in complex machining tasks and is pivotal in industries demanding high precision, such as aerospace and automotive.
Inspection and Quality Control in Machine Shops
Inspection and Quality Control in Machine Shops
Machine shops, whether dealing with bulk production or specialized custom jobs, must adhere to rigorous standards of quality and accuracy. This section delves into the critical aspects of inspection and the crucial practice of tool calibration and maintenance, which together form the backbone of quality assurance in machine shops.
The Role of Inspection
Inspection in machine shops is a multifaceted process, integral to ensuring that every part and component meets the specified dimensions, tolerances, and quality standards. This process is not only about detecting flaws or non-conformities but also about guaranteeing that the manufacturing process consistently produces parts that meet the clients’ exact requirements.
Key Aspects of Inspection:
Dimensional Accuracy: Utilizing tools like calipers, micrometers, and coordinate measuring machines (CMMs) to ensure that each part matches the specified dimensions and tolerances.
Surface Quality: Examining the finish and texture of machined parts to ensure they meet the required aesthetic and functional standards.
Material Integrity: Assessing the material composition and strength, especially critical in industries like aerospace and automotive, where material failure can have dire consequences.
Compliance with Standards: Ensuring that all parts conform to industry-specific standards, such as those set by the International Organization for Standardization (ISO).
Calibration and Maintenance of Tools
The precision of machining operations is heavily reliant on the condition and accuracy of the tools used. Regular calibration and maintenance of these tools are critical to the overall quality of the machining process.
Importance of Tool Calibration and Maintenance:
Accuracy: Regular calibration ensures that tools like milling machines, lathes, and drill presses operate with the highest possible accuracy, essential for producing parts that meet strict specifications.
Longevity of Tools: Proper maintenance prolongs the life of expensive machining tools, thereby protecting the investment of the machine shop.
Prevention of Errors: Routine checks and maintenance minimize the risk of tool failure, which can lead to costly mistakes and production delays.
Compliance with Quality Standards: Adherence to regular maintenance schedules is often a requirement of quality standards and certifications, reinforcing the credibility and reliability of the machine shop.
Safety Practices in Machine Shops
In the bustling environment of a machine shop, where machinery and manpower work in unison, the importance of safety cannot be overstated. Adhering to safety standards is not just a regulatory requirement but a fundamental responsibility to protect the well-being of machinists and ensure smooth operations. Here, we outline the key safety guidelines and protocols essential in a machine shop setting.
Key Safety Guidelines and Protocols:
Personal Protective Equipment (PPE): Mandatory use of safety glasses, ear protection, and steel-toed boots to safeguard against common hazards.
Proper Handling of Tools and Machinery: Training in the correct usage of machine tools, cutting tools, and power tools to prevent accidents and injuries.
Regular Maintenance of Equipment: Ensuring that all machinery, including milling machines, lathes, and drill presses, are in good working condition to avoid malfunctions.
Emergency Procedures: Established protocols for handling emergencies, including fire safety measures and first-aid procedures.
Workplace Cleanliness and Organization: Maintaining a clean and orderly environment to minimize the risk of slips, trips, and falls.
Importance of Adhering to Safety Standards:
Adhering to safety standards in a machine shop is crucial for several reasons:
Prevention of Accidents and Injuries: By following safety protocols, the risk of workplace accidents and injuries is significantly reduced.
Compliance with Legal Requirements: Adherence to safety standards ensures compliance with occupational safety regulations, avoiding legal complications and penalties.
Productivity and Efficiency: A safe workplace promotes a more efficient and uninterrupted workflow, enhancing overall productivity.
Creating a Culture of Safety: Emphasizing safety standards fosters a culture of safety within the workplace, where every individual is aware of and committed to maintaining a safe working environment.
The Role of Technology in Modern Machine Shops
The Role of Technology in Modern Machine Shops
Integration of Advanced Technologies
The integration of advanced technologies has transformed modern machine shops from traditional manufacturing hubs into sophisticated centers of innovation and precision. Key technologies such as Artificial Intelligence (AI), robotics, and Computer Numerical Control (CNC) have redefined the capabilities and efficiency of machine shops.
Impact of Advanced Technologies:
AI and Machine Learning: AI has enabled smarter manufacturing processes, optimizing machining operations, and predictive maintenance, thereby reducing downtime and enhancing quality.
Robotics: The use of robots in machine shops has improved precision and speed, particularly in repetitive and high-volume tasks, reducing human error and labor costs.
CNC Technology: CNC machining has revolutionized the manufacturing process, allowing for the creation of complex and precise parts with minimal human intervention.
Future Trends in Machine Shop Technologies:
The future of machine shop technology is poised for further innovation, with trends indicating a move towards more interconnected and automated systems. Advancements such as the Internet of Things (IoT) and continued development in AI and robotics are expected to further enhance efficiency, precision, and customization in machining processes. These technologies will not only streamline manufacturing but also open new avenues for complex designs and applications, ultimately shaping the future landscape of machine shops.
How to Select the Right Machine Shop?
Choosing the right machine shop is a critical decision for any business or individual requiring machining services. The selection process involves assessing various factors that impact the quality, reliability, and overall satisfaction with the services provided. In this section, we outline key factors to consider when selecting a machine shop, ensuring that your choice aligns with your project’s needs and standards.
Factors to Consider When Choosing a Machine Shop
Selecting a suitable machine shop involves a comprehensive evaluation of several aspects, ranging from technical capabilities to customer service. Here’s a bullet list highlighting the primary factors:
Quality of Work: Assess the shop’s ability to produce parts that meet your specifications. Check their past projects, certifications, and quality control processes.
Reliability and Reputation: Research the shop’s reputation in the industry. Look for reviews, testimonials, and feedback from previous clients to gauge their reliability.
Technical Capabilities and Equipment: Ensure the shop has the necessary machinery and technology, like CNC machines and precision tools, to handle your project’s requirements.
Experience and Expertise: Evaluate the experience and expertise of the machinists and engineers. Experienced professionals can offer insights and solutions to complex machining tasks.
Turnaround Time: Consider the shop’s efficiency and ability to deliver projects within your timeframe. A quick turnaround is often crucial in fast-paced industries.
Customer Service and Communication: Good communication and customer service are essential for a smooth working relationship. Ensure the shop is responsive and willing to collaborate closely with you.
Cost Effectiveness: While cost shouldn’t be the only factor, it’s important to ensure the services offered are competitively priced and provide value for your investment.
Safety Standards: Verify that the shop adheres to safety standards, especially if your project involves hazardous materials or complex processes.
Flexibility and Scalability: The ability to adapt to changes and scale up operations if needed is crucial, particularly for long-term or evolving projects.
Location and Logistics: Consider the shop’s location and its impact on logistics, especially if you require frequent visits or fast shipping of parts.
Additional Services: Look for additional services like finishing, assembly, or design assistance that can add value to your project.
Confidentiality and Intellectual Property Protection: Ensure the shop has measures in place to protect your intellectual property and sensitive information.
Advantages and Challenges of Operating a Machine Shop
Operating a machine shop comes with its unique set of advantages and challenges. These elements define the day-to-day operations and long-term sustainability of the business. Understanding these aspects is crucial for anyone involved in the machining industry, from business owners to customers, and even machinists themselves.
Benefits of Utilizing a Machine Shop
Machine shops offer a range of benefits that make them an indispensable part of the manufacturing and engineering sectors. Here are some of the key advantages:
Precision and Accuracy: Advanced tools and technology like CNC machines ensure parts are made with high precision, meeting stringent specifications.
Production Speed: Modern machining processes allow for rapid production, significantly reducing turnaround times for projects.
Cost-Effectiveness: Economies of scale and efficient use of materials can make machining a cost-effective solution, particularly for bulk orders.
Versatility in Manufacturing: Machine shops can handle a wide range of materials and specifications, making them versatile partners in various projects.
Expertise and Experience: Skilled machinists bring a wealth of knowledge, offering solutions and innovations for complex manufacturing challenges.
Customization: Ability to produce bespoke parts tailored to specific needs, offering flexibility in design and function.
Quality Control: Rigorous inspection and quality control measures ensure that every part meets the required standards.
Common Challenges Faced by Machine Shops
While the advantages are significant, machine shops also face several challenges that can impact their operations and profitability:
Investment Costs: The high cost of advanced machinery, technology, and tools, such as CNC machines and precision tools, represents a significant investment.
Skilled Labor Shortage: Finding and retaining skilled machinists, particularly those experienced in advanced machining techniques, can be challenging.
Maintenance Issues: Regular maintenance of complex machinery is necessary to avoid downtime, which can be costly and time-consuming.
Competition and Market Fluctuations: Staying competitive in a rapidly evolving market, with fluctuating demand and technological advancements, is a constant challenge.
Adapting to New Technologies: Keeping up with the latest advancements in machining technology requires ongoing training and investment.
Material Costs and Availability: Fluctuations in the cost and availability of raw materials can impact production timelines and costs.
Regulatory Compliance: Adhering to industry standards and regulations can be complex and requires constant vigilance.
Energy Costs: Operating heavy machinery can lead to significant energy consumption, impacting operational costs.
The Impact of Machine Shops on Various Industries
Machine shops play a pivotal role in various industries, from aerospace to automotive, from healthcare to construction. Their impact is profound and widespread, shaping the way industries operate and innovate. This section explores how machine shops contribute significantly to different sectors, highlighting their indispensable nature in the modern industrial landscape.
Aerospace Industry: Precision and accuracy are paramount in the aerospace industry. Machine shops provide specialized machining of aircraft components, adhering to strict tolerances and quality standards.
Automotive Sector: The automotive industry relies on machine shops for the production of engine components, gearboxes, and custom parts, driving innovation and efficiency.
Healthcare and Medical Devices: Machine shops contribute to the healthcare sector by manufacturing intricate components used in medical devices, surgical tools, and implants.
Construction and Infrastructure: In construction, machine shops play a role in fabricating metal structures, frameworks, and bespoke fittings essential for building and infrastructure projects.
Energy Sector: For the energy industry, including renewable energy, machine shops produce components for turbines, generators, and other critical machinery.
Electronics and Technology: The production of precision components for electronic devices and technological equipment is another key area where machine shops excel.
Defense and Military: Machine shops support the defense sector by providing robust and precise machining for military equipment and vehicles.
Consumer Goods: Even in the consumer goods sector, machine shops contribute to the manufacturing of various products, from appliances to sports equipment.