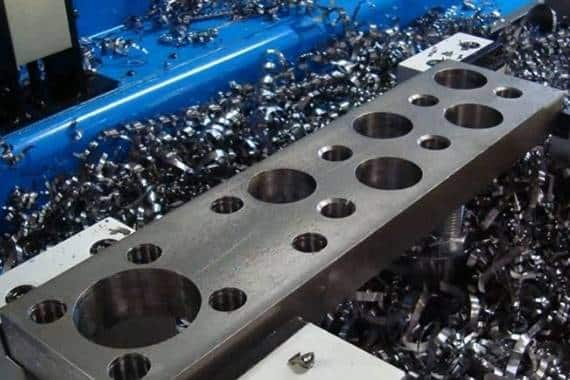
Fine blanking is a precision metal stamping process used to produce highly accurate and complex parts. This technique uses three forces to achieve the desired shape: a holding force, a counter pressure, and a blanking force. This is different from conventional blanking in which only a single downward force is applied. The result is parts that are burr-free with clean and smooth edges. This process is also capable of adhering to tight tolerances.
This article will discuss what fine blanking is, how it works, the materials used, types, and its importance.
Table of Contents
What Is Fine Blanking?
Fine blanking is a precision metal forming process, or more specifically a metal stamping process, used to produce complex and high-accuracy parts from various types of metal sheets. Unlike conventional blanking, which is a shearing process that separates a piece of metal sheet by applying a force that exceeds the material’s tensile strength, fine blanking involves three forces: a holding force, a counter pressure, and a blanking force. This combination of forces applied simultaneously through a specially designed press and tooling, ensures smooth, straight edges and superior flatness of the part, with minimal burring.
What Is the Process of Fine Blanking?
The process of fine blanking starts with a piece of metal being fed into a specialized blanking press. The system incorporates a die and a stripper, which work in tandem to shape the part. The stripper functions to securely hold the metal in place, while the press and die apply a clamping force to form the part, ensuring it retains precise dimensions. Once the part is formed, the stripper releases it, revealing a component with a smooth, burr-free finish.
What Are the Different Tools in Fine Blanking?
Fine blanking involves several specialized tools and components designed to work together to produce high-precision parts with smooth edges and complex features including:
Press: A high-precision mechanical or hydraulic press specifically designed for fine blanking.
Die: The die has a specially designed cutting edge that shapes the blanked part. It is custom-made for each part design and is critical for achieving the desired accuracy and detail in the finished part.
Punch: The punch is the component that presses the metal sheet into the die to cut out the part. It is typically made of high-strength materials to withstand the high pressures involved in fine blanking.
Stripper Plate: This tool holds the workpiece in place during the blanking process and then strips the finished part from the punch as it retracts. The stripper plate ensures the material does not lift or deform, contributing to the precision of the process.
V-Ring (or Stinger): The V-ring is a critical component used in fine blanking to prevent material from moving outward and to reduce rollover at the cut edge. It impales the metal just before the punch contacts the part, trapping the metal and pushing it inward toward the punch.
Counter Pressure Plate: This plate applies a force opposite to the direction of the punch. The counter pressure helps to stabilize the material during cutting and contributes to the smooth, burr-free edges typical of fine blanking parts.
Guide Plates: These plates ensure the precise alignment of the punch and die during the blanking process, which is crucial for achieving tight tolerances and detailed features in the finished part.
Holding Plates and Pads: These components apply the necessary holding force to keep the metal sheet flat and prevent it from deforming plastically during the cutting process. This helps in maintaining the critical flatness characteristic of fine blanked parts.
Feeder: This component is used to feed and hold the metal in place for fine blanking.
Lubrication System: A lubrication system is needed to prevent friction and wear on the tools.
What Is the Importance of Fine Blanking in Manufacturing?
Fine blanking is crucial in manufacturing due to its ability to produce high-precision parts with clean, straight edges and minimal burring directly from the press. This process enables the mass production of complex parts with tight tolerances that might otherwise require additional machining or finishing processes, significantly reducing production time and costs.
What Are the Different Materials That Can Be Used in Fine Blanking?
Fine blanking is a versatile manufacturing process that can be applied to a wide range of materials, such as:
1. Aluminum
Known for its light weight and excellent corrosion resistance, aluminum is widely used in fine blanking for automotive and aerospace applications. Its malleability allows for the creation of intricate parts without sacrificing strength or durability.
2. Titanium
Esteemed for its exceptional strength-to-weight ratio and corrosion resistance, titanium is often used in fine blanking for aerospace, medical, and high-performance automotive components. Despite its toughness, it can be finely blanked into precise, durable parts.
3. Copper
Copper’s excellent electrical conductivity makes it a popular choice for electrical components produced through fine blanking. Its ductility allows for the production of complex shapes with high precision, ideal for electrical connectors and components.
4. Brass
Brass is well-suited for fine blanking, with its low tool wear, excellent electrical conductivity, corrosion resistance, and aesthetic appeal — properties that make brass parts ideal for various applications. It is frequently used in fine blanking for decorative hardware, musical instruments, and electrical fittings, offering both aesthetic appeal and functionality.
5. Stainless Steel
Stainless steel is prized for its strength and resistance to corrosion and staining. Its versatility makes it suitable for fine blanking applications across various industries, including: medical devices, automotive parts, and kitchen utensils, producing parts that are both durable and aesthetically pleasing.
6. Precious Metals
While common materials for fine blanking include various grades of steel and aluminum, precious metals such as: gold, silver, platinum, and palladium might be used for specific applications. These applications often involve the electronics, medical, or aerospace industries in which the unique properties of precious metals—such as their electrical conductivity, resistance to oxidation and corrosion, or biocompatibility—are necessary. However, due to the high cost of precious metals, their use in fine blanking is typically reserved for small, high-value parts for which these specific properties are essential.
7. Carbon Steels
These materials are frequently used in fine blanking due to their clean-cutting properties when paired with adequate tooling and minimal hardness. They are known for their strength and versatility. They’re ideal for a wide range of applications across industries, from automotive and machinery parts to tools and hardware.
8. Inconel®
Exotic alloys like Inconel®, Monel®, and Hastelloy® are used in fine blanking for aerospace and defense industries, in which extreme properties such as heat resistance and high strength are crucial. These materials demand exceptional quality tooling and can significantly affect tool life. Inconel® alloys specifically are known for their ability to withstand extreme temperatures and corrosive environments.
9. Alloy Steel
Alloy steel is steel mixed with various elements to enhance its mechanical properties, such as: strength, hardness, and wear resistance. In fine blanking, alloy steel is used to produce parts that require higher strength and durability, such as: gears, fasteners, and automotive components.
10. Tool Steel
Tool steel is characterized by its hardness, abrasion resistance, and ability to retain shape at high temperatures. Fine blanking of tool steel is used for making durable, precise tools and dies that require maintaining sharp edges and tolerances under repeated use.
11. Beryllium Copper
Beryllium copper combines high strength with non-sparking and non-magnetic properties. In fine blanking, beryllium copper is used for creating electrical connectors, undersea communication equipment, and aerospace components, in which a combination of electrical conductivity and durability is required.
12. Nickel Alloys
These materials require specific treatment such as normalization or annealing before blanking due to their tendency to pose issues. Selected for their heat, corrosion, and wear resistance, nickel alloys are used for demanding applications, including jet engine components.
Materials unsuitable for fine blanking include very hard metals, which can damage tooling, and brittle materials like cast iron and certain ceramics that may crack under pressure. Non-metallic materials and certain high-strength alloys with limited ductility are also challenging to fine blank due to their inability to undergo the necessary plastic deformation without fracturing. Essentially, the process demands materials that can be cleanly sheared, possess ductility, and maintain integrity under high pressure.
What Are the Different Types of Fine Blanking?
Listed below are the different types of fine blanking operations, each with their unique applications:
1. Conventional Fine Blanking
This is the most basic form of fine blanking, in which a single part is produced with each stroke of the press. It involves three main forces: holding force, counter pressure, and the blanking force itself. This method is known for producing parts with very clean edges and minimal burring, ideal for high-precision components.
2. Compound Fine Blanking
This process combines fine blanking with other stamping operations, such as forming or embossing, in a single press stroke. This allows for the production of more complex components within tighter tolerances, reducing the need for additional processing steps and thereby saving time and costs.
3. Progressive Fine Blanking
In progressive fine blanking, the metal strip moves through a series of stations within the same tool, with each station performing different operations. This sequential approach enables the production of parts with multiple features or components from a single strip, enhancing efficiency and throughput for high-volume production.
4. Hybrid Fine Blanking
Hybrid fine blanking combines the principles of fine blanking with other metal forming processes, such as traditional stamping or cold forging, to create parts that benefit from the advantages of each technique. This method can offer improved material utilization, enhanced part strength, and the ability to produce complex shapes that would be difficult to achieve with fine blanking alone.
5. Fine Piercing
While technically not a type of fine blanking, fine piercing is a related process that uses similar principles to create precision holes or cutouts in a material. Like fine blanking, it involves the use of high pressures and tight clearances to achieve clean, burr-free edges. Fine piercing can be integrated into fine blanking operations to produce parts with both solid forms and precise openings.
Are There Other Types of Blanking Aside From Fine Blanking?
Yes. Aside from fine blanking, there are additional types of blanking processes utilized in the industry. Ordinary blanking is a more basic form of stamping that is used to cut simple shapes out of sheet material. It is best suited for manufacturing parts that require moderate precision, such as washers. This method is characterized by its cost-effectiveness in producing consistent shapes and is widely employed across various sectors for the mass production of simpler components. On the other hand, micro-blanking represents an advanced precision metal stamping process designed specifically for the production of small and intricate parts. It achieves micron-level tolerances and precision, catering to the needs of industries like: electronics, medical devices, and microtechnology. Micro-blanking is essential for manufacturing components such as: microelectromechanical systems (MEMS), micro-connectors, and other parts that demand high precision and miniaturization.
What Is the Advantage of Fine Blanking?
Fine blanking offers several advantages including:
Can achieve tight tolerances and produce parts with complex geometries and minimal dimensional variation.
The process results in smooth, clean edges on the parts, reducing or eliminating the need for secondary finishing operations such as grinding or machining.
Reduces labor, tooling, and processing costs associated with additional machining and finishing steps.
Utilizes material efficiently, minimizing waste and scrap. The precise-cutting process allows for closer nesting of parts, optimizing material use.
Can process a wide range of materials, including: various types of steel, aluminum, copper, and brass, among others. It is adaptable to different sizes and thicknesses, up to 0.625 inches.
The ability to combine multiple operations into a single process streamlines the production timeline, enabling faster turnaround times for high-quality parts.
Given its precision, efficiency, and material flexibility, fine blanking is suited for a broad spectrum of industries, including: automotive, electronics, aerospace, and medical devices, for manufacturing a variety of critical components.
Is There Any Risk in Fine Blanking?
Yes, there are risks associated with fine blanking. These risks include tool wear and damage due to the high pressures and tight tolerances involved, potentially leading to increased maintenance costs and downtime. Proper material selection is crucial, as using inappropriate materials can result in product defects or further damage to the tooling. Ensuring operator safety is also critical, given the high pressures and mechanical operations involved. Proper training and adherence to safety protocols are essential to mitigate the risks of accidents.
What Are the Different Real-Life Applications of Fine Blanking?
Fine blanking is used to produce parts for the following industries:
Automotive: Utilizes fine blanking to manufacture a wide array of components, including: electrical parts, parts for brakes and steering systems, suspension elements, seat-belt mechanisms, and engine and transmission components.
Aerospace: Relies on fine blanking for the production of specialized parts critical to aircraft functionality and safety.
Construction: Employs fine blanking to create durable, precise parts for a range of tools and machinery essential in construction projects.
Medical: Benefits from fine blanking in the fabrication of essential devices, such as stethoscopes, and various specialized medical instruments, ensuring precision and reliability.
What Are the Different Fine Blanking Examples?
Fine blanking is used to produce a variety of high-precision parts, including:
Automotive Components: Gear shifters, seat-recliner mechanisms, brake-system parts.
Electronic Parts: Connectors, mobile-phone components, circuit-board components.
Consumer Goods: Keys, knife blades, complex watch components.
Industrial Equipment: Precision gears, fasteners, and various machinery components.
What Are the Best Fine Blanking Manufacturers?
The “best” fine blanking manufacturers can vary depending on specific needs. However, here’s a list of some leaders in the field:
How To Choose Fine Blanking Manufacturers
When selecting fine blanking manufacturers, it’s crucial to consider their expertise, quality standards, equipment capabilities, and experience with your specific material and industry requirements. Look for manufacturers with a proven track record of producing high-quality parts similar to what you need. Assess their certifications (such as ISO 9001) to ensure they adhere to international quality management standards. Evaluate their technical capabilities, including the types of materials they can process and the complexity of parts they can produce. Consider their capacity to meet your production volumes within the required timelines. Additionally, examine their willingness to collaborate on design and engineering to optimize part manufacturability. Finally, review their customer service and support, ensuring they provide clear communication and are responsive to your needs. Selecting a manufacturer that aligns with these criteria will help ensure a successful partnership and high-quality outcomes for your fine blanking projects.
Is Fine Blanking a Metal-Forming Method?
Yes, fine blanking is a metal-forming method. It’s a precision machining process specifically designed for producing parts with very tight tolerances and smooth edges directly from metal sheets. Fine blanking combines the actions of a conventional stamping press with a precision tooling setup that includes specially designed punch, die, and counter-pressure mechanisms. This process is capable of producing complex and high-accuracy metal parts with clean, straight edges and minimal burr, making it distinct from standard blanking operations.
What Is the Difference Between Fine Blanking and Conventional Blanking?
Fine blanking differs from conventional blanking in several key aspects:
Fine blanking produces parts with higher precision and tighter tolerances than conventional blanking.
Fine blanking results in smoother, burr-free edges, eliminating the need for secondary finishing operations, whereas conventional blanking often leaves rough or burred edges.
Fine blanking uses specialized, more complex tooling, including precision dies and punches, and often employs a counter-pressure mechanism, unlike the simpler tools used in conventional blanking.
Conventional blanking applies a single downward force, while fine blanking applies forces from three directions simultaneously to minimize material deformation and achieve cleaner cuts.
Fine blanking is typically used for materials up to about 0.625 inches thick and can create parts with complex features in a single operation, a contrast to conventional blanking’s limitations in thickness and complexity.
What Is the Difference Between Fine Blanking and Stamping?
Fine blanking is a specialized version of stamping that offers superior precision, producing parts with smooth, clean edges and tight tolerances. This method utilizes a unique process that applies pressure from three directions simultaneously to the workpiece, minimizing the clearance between the punch and die and effectively eliminating unwanted material deformation and burring. Stamping, in contrast, is a broader category of metal forming that includes a variety of processes like: punching, bending, and cutting, typically with simpler tooling and less precision. Stamping is more suited for producing larger volumes of parts with lower precision requirements.
XTJ is a leading OEM Manufacturer that is dedicated to providing one-stop manufacturing solutions of Machining 6061 Aluminum from prototype to production. We are proud to be an ISO 9001 certified system quality management company and we are determined to create value in every customer relationship. We do that through collaboration, innovation, process improvements, and exceptional workmanship.lication: Automotive industry, Bicycle and motorcycle, Door and windows and furniture, Household appliance, Gas meter, Power tool,LED lighting, Medical instrument parts, ect.