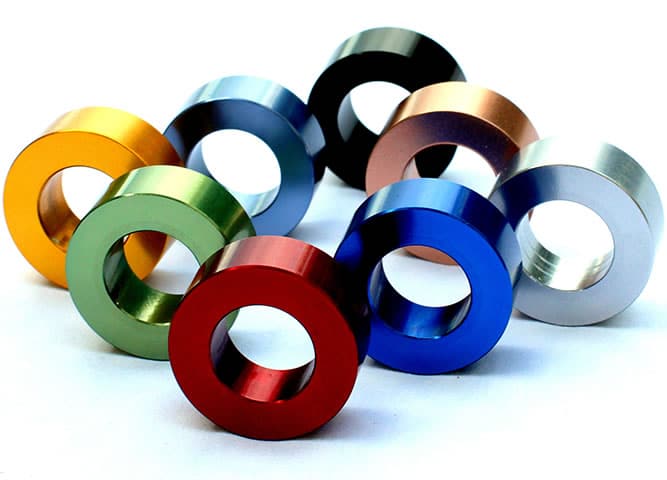
Anodizing is an electrochemical process by which a metal surface is given an anodic oxide finish made of aluminum oxide. Unlike other forms of protective coating, the process of anodizing means the protective layer is fully integrated with the aluminum substrate underneath so that it does not chip or peel. Anodizing is used across a wide variety of industries for things such as: implants in the medical industry, microwaves and refrigerators in the electronics industry, and helicopter rotor blades in the aerospace industry to name a few. Materials suitable for anodizing include: aluminum, magnesium, zinc, and titanium.
This article will discuss anodizing, how it works, its uses, material compatibility, and its advantages and disadvantages.
What Is Anodizing?
Anodizing is an electrochemical process used to create a protective oxide layer on a metal surface. This metal oxide creates a protective coating which is part of the metal rather than a separate coating. This creates a protective barrier that is durable and chip-resistant. Metals that can be oxidized include: magnesium, aluminum, zinc, titanium, niobium, and tantalum alloys.
How Does Anodizing Work?
Anodizing works by using an electrochemical process to treat a bare metal surface and create a corrosion-resistant and durable finish. In this process, the metal is bathed in an acid (electrolyte solution), and an electrical current is passed through a cathode rod in the bath to the anode (the metal being treated). In doing so, the oxygen atoms can be released from the electrolyte and attached to the surface of the metal, which forms a metal oxide.
What Is the Use of Anodizing?
One of the main reasons for anodization is to increase a metal’s corrosion resistance. By creating an oxide layer on the surface of the metal, the oxygen in the environment cannot get to the metal, which in turn prevents corrosion. The process of anodization is used for corrosion resistance because of its durability. The oxide layer that forms due to anodization is a part of the metal, rather than a coating that is applied to the metal. This makes the oxide layer much stronger and more durable than coatings. Finally, anodization can be used to protect a metal while keeping the metal dimensionally stable. This is because anodization does not significantly increase the thickness of a part when compared to coatings used to protect the metal. Such a thin proactive layer can be achieved with anodization because the oxide layer penetrates the metal as the treatment is part of the metal substrate and not a coating that is applied to the substrate.
What Is the Advantage of Anodizing?
There are several advantages to anodizing metal which can include heightened corrosion resistance. Anodizing the metal will create an oxide layer to increase the corrosion resistance of the metal. Since anodization uses an oxide layer, it is UV resistant which can result in a more durable finish. Additionally, anodization requires no maintenance which is ideal for hard-to-reach parts. Finally, anodization is chemically stable and non-toxic, which is great for the environment.
What Is the Process of Anodizing?
There are five mandatory steps and one optional step to anodizing metal parts. These steps are discussed in more detail below:
1. Cleaning
The first step in anodization is to clean the metal to be treated. The first stage of cleaning is to remove any dirt or debris from the metal. The second is to degrease the surface. This is important to ensure an oxide layer can form evenly across the surface. Additionally, the metal can be chemically etched to remove a very thin layer of material to give the oxygen a fresh surface to bond to. Etching will create a smooth and consistent surface finish, and remove any small damage to the surface. If this step is missed, then the oxygen from the electrolyte will not be able to form an oxide layer and will leave an area of metal exposed or poorly anodized.
2. Preparation
After cleaning, the equipment needs to be prepared to anodize the metal. An anodizing tank large enough to fit the part to be anodized needs to be ready with the chosen acid solution. The temperature and concentration of the acid solution is a key parameter that needs to be decided before starting the process, as these parameters will affect the final thickness and properties of the protective layer. If these conditions are not properly prepared and the process is delayed then the newly etched metal surface will start to corrode due to the oxygen in the atmosphere. Additionally, the final thickness of the anodized layer will be incorrect if the parameters are not controlled.
3. Anodizing
Anodizing is the main step of the process. The part is bathed in an acid electrolyte solution. The cathode in the acid bath is commonly sheet aluminum, and the part to be anodized becomes an anode. The length of time the part is anodized, the intensity of the current used, the acid temperature, and the acid concentration all affect the thickness of the oxide layer. By monitoring the parameters, the part can be removed at the right time ensuring the appropriate oxide layer is formed.
4. Optional Coloring
There will be pores left from the creation of the oxide layer, these pores can be filled with a dye to color the part. To do this, the part needs to be dipped in the dye for a period to allow the dye to seep into the pores. This step is optional and only adds an aesthetic to the part as the pores are sealed in the next step.
5. Sealing
The pores created during the anodization of the parts must be closed to prevent corrosion. To do this, the parts can be dipped in either boiling water or a cold nickel acid solution. This will close the pores, and if the part has been dyed it will prevent the dye from leaking out. This step is essential to prevent the oxide layer from being penetrated and to stop the dye from leaking.
6. Quality Control
The parts must be inspected to ensure the process has worked. In the quality control, factors such as the oxide-layer thickness and surface finish are checked. The part can also be visually inspected for any defects. Adhesion tests can be used to confirm the anodized layer is fully adhering to the substrate, and corrosion tests can be performed to ensure the part performs as expected. Without quality control, any breakdown in the process will not be spotted and the parts will not perform as expected.
What Organization Sets the Standards for Anodizing?
The Aluminium Anodizers Council (AAC) provides a variety of process controls that can monitor and control the correct anodized coat for the specific application. The AAC has quality criteria that include: anodized-film uniformity and density; abrasion, corrosion, and fade resistance; reflectivity and image clarity; adhesion and sealing. Applicable testing includes: weight tests, microscopic tests, and dielectric tests. In addition, anodizing companies can also obtain ISO accreditations (e.g., ISO 9001) to certify that their processes meet the required standard.
How Much Does Anodizing Cost?
The cost of anodization will vary depending on the specific job. The cost of anodization is likely to increase with the size of the part and the thickness of the anodized layer required. The price may also vary with the type of metal being used, the number of parts being anodized, and with the use of optional color dyes. The price of anodization could be in the range of $2–120 per part depending on these factors.
What Are the Different Materials Suitable for Anodizing?
Several different materials can be anodized. Anodization can be used to create corrosion resistance or to improve aesthetic . Below are six metals that are commonly anodized:
1. Magnesium
Magnesium is a soft silver/white earth metal which is the eighth most abundant metal on earth. Magnesium is one of the lightest structural metals at a density of 1.737 g/cm³, with a strength of up to 280 MPa and a modulus of 45 GPa. Pure magnesium has a melting point of 650 °C and magnesium alloys will have varying melting points based on the composition. The corrosion resistance of magnesium is poor and can be made worse by the inclusion of alloying metals which cause intermetallic corrosion. Magnesium’s biggest advantage is its light weight which gives it a high strength-to-weight ratio, however, it is let down by its poor resistance to degradation. Due to this reason magnesium and all of its alloys can be and are anodized to prevent corrosion. The cost of magnesium before anodizing is $25 per kg.
magnesium
Magnesium. Image Credit: Shutterstock.com/RHJPhtotos
2. Aluminum
Aluminum is one of the most abundant metals on earth. It has a light and silver appearance and is known for its low cost and light weight. Aluminum weighs 2.71 g/cm³, with a strength of up to 570 MPa, and a modulus of 70 GPa. The melting point of aluminum is 660 °C. The corrosion resistance of aluminum is moderate but is much improved with anodization. Aluminum and all of its alloys can be anodized, and commonly are, to protect from corrosion. The advantages of aluminum are its high strength-to-weight ratio, low cost ($4 per kg), and recyclability. The disadvantages are aluminum’s high thermal conductivity which makes it hard to weld and its low strength compared to other metals such as steel or titanium.
aluminum
Aluminum. Image Credit: Shutterstock.com/BigTunaOnline
3. Zinc
Zinc is a soft silver metal which is the 23rd most abundant metal on earth. Zinc has a density of 7.11 g/cm³, a strength of up to 200 MPa, and a modulus of 45 GPa. The melting point of zinc is 420 °C. Zinc is a very stable metal and therefore has good corrosion resistance properties. Zinc and its alloys can be anodized for aesthetic reasons and their corrosion resistance, however, this is not widely done as zinc already has high corrosion resistance and the cost of anodizing zinc is high. The advantages of using zinc are its high durability, corrosion resistance, and recyclability. However, the disadvantages of zinc are its brittleness, low melting point, and its limited availability compared to other metals. Zinc costs $3 per kg.
zinc
Zinc. Image Credit: Shutterstock.com/RHJPhtotos
4. Titanium
Titanium is a type of shiny, hard, strong metal found naturally in the earth, and is the ninth most abundant element found in the earth’s crust. Titanium has a density of 4.5 g/cm³, a minimum yield strength of c. 240 Mpa, and Young’s modulus of elasticity of 120 GPa. Titanium’s melting point sits at 1,670 °C, and its boiling point at 3,287 °C. Titanium has excellent corrosion resistance in seawater and is used there to protect ship hulls, submarines, and various other structures used in the maritime industry. Titanium is used widely as an alloying agent with other metals, for example, aluminum, iron, and molybdenum. Both pure titanium and titanium alloys can be anodized. The advantages of titanium are that it is highly resistant to chemicals, rust, and corrosion, has the highest strength-to-weight ratio amongst metals, and is incredibly durable. Key disadvantages include the difficulty of machining due to its strength and it is generally more expensive in comparison to other types of metal such as: iron, steel, and aluminum. The average cost of titanium per kg is ~$10.
titanium
Titanium. Image Credit: Shutterstock.com/RHJPhtotos
5. Niobium
Niobium is the 33rd most abundant metal on earth, making it more abundant than lead. It has a density of 8.60 g/cm³, a strength of 600 MPa, and a modulus of 103 GPa. The melting point of niobium is 2,468 °C, making it highly heat resistant. Niobium is one of the most corrosion-resistant metals available due to its naturally forming oxide layer, which is commonly artificially made with anodization. Niobium is artificially anodized to make different colors in a jewelry application. Niobium and all of its alloys can be anodized. The advantages of niobium are its high corrosion and temperature resistance. The disadvantage of niobium is its high cost. Niobium costs $57 per kg.
niobium
Niobium. Image Credit: Shutterstock.com/Bjoern Wylezich
6. Tantalum Alloys
Tantalum is one of the rarest metals, and therefore tantalum alloys are very uncommon. Tantalum is very heavy with a density of 16.65 g/cm³, strength of 172 MPa, and modulus of 27 GPa. The melting point of tantalum is very high at 2,996 °C. Tantalum is extremely corrosion resistant due to its naturally forming oxide layer. This oxide layer is usually artificially created by anodization to create corrosion resistance for tantalum and its alloys. The main advantages of tantalum are its high corrosion resistance and temperature resistance. However, its disadvantages are its high weight and cost. The cost of tantalum is $121 per kg, making it one of the most expensive metals.
tantalum
Ttantalum. Image Credit: Shutterstock.com/Bjoern Wylezich
There is also a range of materials that can not be anodized, which include all non-metals including: wood, composites, and plastics. Additionally, iron or any iron-based metals such as steel cannot be anodized.
What Industries Use Anodizing?
A number of industries use anodizing to protect the surface of a finished product against corrosion and scratching, providing one of the most durable types of surface finishes possible as well as enhancing the aesthetics. Architecture and construction industries use anodizing, for example in: escalators, door frames, window frames, awnings, and handrails. One example of a building sheathed in anodized aluminum is the Willis Tower in Chicago. The automotive industry uses anodizing for applications such as: frames, wheels, pistons, and bumpers. Examples from the aerospace industry include: helicopter rotor blades, avionic cases, instrument panels, satellite components, and airframe skins to name a few. In the electronics and consumer goods industries, anodizing is used on: refrigerators, washers, dryers, televisions, microwaves, cameras, and beauty products such as curling irons. Military and defense industries use anodizing for products such as gun scopes. Similarly, the sporting goods and recreation industries anodize aluminum for both protection and aesthetics on items such as: baseball bats, sailboat masts, tent poles, and golf carts. Finally, the medical and healthcare industries use anodizing on metals for medical devices such as: surgical instruments, implants, and prostheses.
How To Choose the Best Anodizing Manufacturer?
There are a variety of factors that should be taken into consideration when choosing the best anodizing manufacturer, including:
Level of Experience and Expertise: These are crucial and are directly proportional to the level of understanding of the equipment and process that is needed to produce high-quality outcomes.
Quality Assurance: The best manufacturers should have a comprehensive system in place to measure quality control that includes regular inspection and performance of testing on a final product. This will ensure the final product has the best possible treatment and meets client specifications.
Capabilities and Services: Both inform the decision on which manufacturer has the necessary skills and experience to meet client needs.
Customization and Flexibility Options: The balance should be considered between high-quality services that are adapted to individual requirements while maintaining competitive pricing. It is important to compare quotes from several anodizing companies before choosing to ensure the best value for money.
Communication and Support: Both should be considered, as the level of customer service (willingness to answer questions, responsiveness, communication quality, etc.) directly influences the experience of a client and the ease of the entire process.
Environmental Practices: An ethical manufacturer who is conscious about the environment upholds higher standards and can enjoy a more stable reputation that comes along with that. Making efficient and effective use of the materials available and recycling of metals helps with costing of projects and has a positive impact on the world around us.
Location of the Manufacturer and Logistics: The delivery of the final anodizing project is important to consider as this may have a bearing on the ability to meet any tight deadlines of a given project.
Reputation and Reference: are important in choosing the best anodizing manufacturer as their track record of performing quality work for clients gives the client comfort in trusting them with their finished product.
Potential for a Long-Term Partnership: Have a trusted manufacturer who understands the individual requirements to make each project more seamless.
What Are the Best Anodizing Suppliers?
There are plenty of anodizing suppliers in North America that can meet your anodizing needs, these suppliers can be found at XTJ using the discovery platform. Some of the best anodizing manufacturers include: Techmetals Inc., Sapphire Metal Finishing, Mills Metal Finishing, Certified Metal Finishing, and US Anodize.
What Is the Disadvantage of Anodizing?
Whilst there are a few drawbacks to anodizing, arguably the main disadvantage is that this process has higher up-front costs in comparison to other forms of protecting the surface of a given metal (e.g., powder coating). This is due to the specialized processes and equipment required, and the time-consuming pre-treatment. Before undergoing anodizing, the product must undergo pre-treatment to ensure a clean surface. Not only does this take time, but there may be additional costs involved in procuring extra equipment and chemicals. This can be a significant drawback if the manufacturer is not processing a high volume of finished product. Other disadvantages include variations in color and shading as it can be very difficult to achieve perfect consistency across a large batch of anodized metal parts.
Is Anodizing the Same As Coating?
No, anodizing is not the same as coating. While both provide protective layers to a metal product, the process is very different and each method has its pros and cons. Anodizing is an electrochemical process that creates a protective layer of oxide to protect a metal surface. Unlike a coated finish, anodizing creates a coat that is actually part of the metal product and therefore cannot flake or peel. This is achieved by immersing the product in an electrolyte solution and then applying electric current to form a layer of aluminum oxide on the surface. Powder coating on the other hand applies dry powder to the surface of the metal product and heats it until the powder is cured.
What Is the Difference Between Anodizing and Coating?
There are a few main differences between anodizing and coating. Firstly, anodizing has a slightly different finishing process. Coating a material creates a protective layer over the finished product, whereas an anodized finish is more ingrained and becomes part of the completed artifact. Secondly, an anodized surface is much harder than a coated one. Thirdly, since anodized finishes are part of the metal rather than a coating layer on top, it does not peel off in the way coating can. Finally, manufacturers can achieve a much deeper metallic color when using anodizing as opposed to coating. Another important thing to note is that anodizing is traditionally performed on aluminum, whereas coating can be performed on a wider range of metals.
XTJ is a leading OEM Manufacturer that is dedicated to providing one-stop manufacturing solutions of Machining 6061 Aluminum from prototype to production. We are proud to be an ISO 9001 certified system quality management company and we are determined to create value in every customer relationship. We do that through collaboration, innovation, process improvements, and exceptional workmanship.lication: Automotive industry, Bicycle and motorcycle, Door and windows and furniture, Household appliance, Gas meter, Power tool,LED lighting, Medical instrument parts, ect.