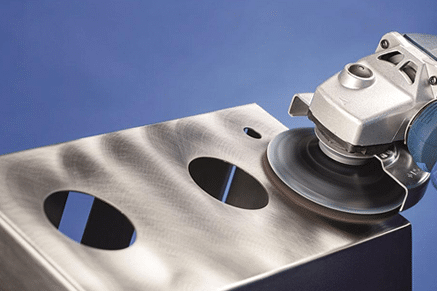
Table of Contents
Why Should we make a Good Surface Finish for CNC Parts?
When it comes to machining, a good surface finish is essential. The benefits of having a good Surface Roughness are many and varied. In general, a smooth Surface finish will result in better performance in terms of wear resistance, corrosion resistance, fatigue strength, and overall strength. A good surface finish can help to reduce friction and wear, improve corrosion resistance, and increase the overall lifespan of the component.
Surface roughness is a measure of the irregularities in the surface of a material. It is often quantified by the average surface roughness, which is the arithmetic mean of the absolute values of the deviations of profile points from their means. Surface roughness is a relevant factor in many engineering applications because it affects tribological properties such as friction and wear, and it can also affect fluid flow and heat transfer. In machining, surface roughness can be an important factor in both the quality of the final product and the efficiency of the manufacturing process.
Additionally, a good Surface Roughness will often times improve aesthetics and/or function. For example, a smooth Surface finish on a cutting tool will result in cleaner, more precise cuts; whereas a rougher Surface finish may cause the tool to “grab” or “catch” on the workpiece, resulting in poor quality cuts. In the case of medical implants, a smooth Surface finish is often times critical to preventing infection and/or rejection. Aesthetically, a good Surface Roughness can be the difference between a product that looks “cheap” and one that looks “high-end”. Functionally, a good Surface Roughness can improve the performance of mechanical components by reducing friction and/or providing a better seal.
In short, the benefits of having a good Surface Roughness are many and varied, not only does it improve the aesthetics of the piece, but it also provides a smoother surface for further machining, sealing, or painting. So if you’re looking to improve the performance of your product, or make it look more high-end, then paying attention to Surface roughness is a good place to start.
How to Improve Surface Roughness
Surface roughness is a very important factor when it comes to creating a good surface finish. Surface roughness is the measure of the bumps and valleys on the surface of a material. There are many ways to improve surface roughness, but the most common and effective method is by using a machining process called lapping.
Lapping
Lapping is a process where a rotating abrasive wheel is used to remove small amounts of material from the surface of a workpiece. This process can be used to create very smooth and precise surfaces.
Lapping is a process of polishing a surface by hand with an abrasive. The abrasive particles are held between the laps, which are two flat surfaces that are rubbed together. Lapping can be used to create a smooth, glossy finish on a variety of surfaces, including metals, glass and plastics.
Lapping is an effective way to improve surface roughness. By using progressively finer abrasives, lapping can remove imperfections and create a smooth surface finish. In addition, lapping can also help to create a more consistent surface roughness across the entire surface of a material.
Electroplating
Surface roughness can also be improved by using chemical or physical treatments. These treatments work by filling in the small imperfections on the surface of the workpiece. For example, electroplating.
Surface roughness can be improved through electroplating. Electroplating is a process where a thin layer of metal is deposited onto the surface of the workpiece. This process can be used to fill in voids and irregularities on the surface of a material, resulting in a smoother finish. Electroplating can also be used to add a protective layer to the surface of a material, which can help to reduce wear and tear. This process can fill in any small imperfections on the surface of the workpiece and create a smoother finish.
Heat treatment
Surface roughness can also be improved by using a process called heat treatment. Heat treatment is a process where the surface of the workpiece is heated to a high temperature and then cooled rapidly. Heat treatment alters the microstructure of the material surface, making it more smooth and even. This process can be used on both metals and plastics.
Conclusion
Surface roughness is an important consideration in many engineering applications as it can affect the performance, durability, and aesthetics of a product. In many cases, it is necessary to control surface roughness in order to meet the requirements of the application. Surface roughness can be controlled through a variety of methods, such as careful selection of materials and manufacturing processes, use of operating conditions that are favorable to surface finish, and by using surface finishing methods.