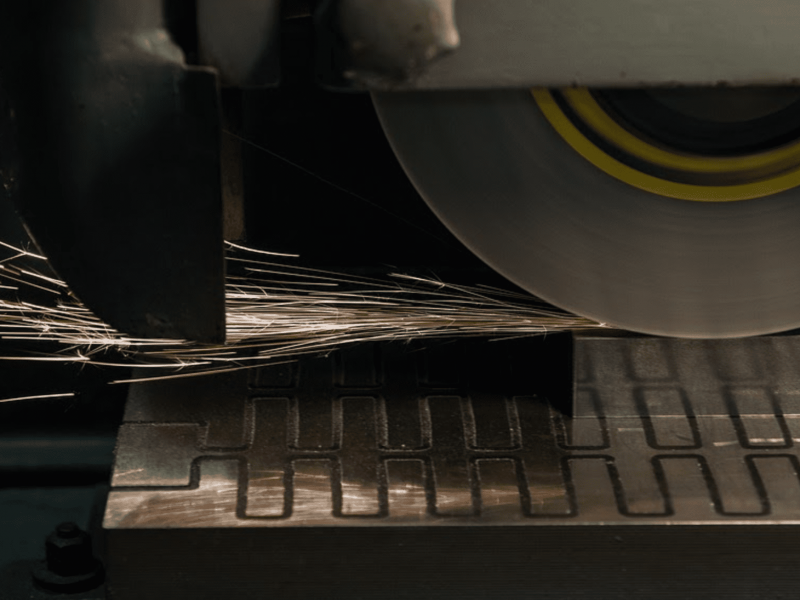
Machining lapping and grinding are two of several machining techniques used in surface finishes. This process usually applies to different materials, but most commonly hard ones like metal and glass. Although there is a difference between the two processes, these terms have often been used interchangeably. The two processes both involve friction, at normally low speed, to smoothen the surface, or high points, of a workpiece, where the greatest material removal occurs.
Machining lapping is optimal for products requiring precise flatness, parallelism, with measured requirements in terms of consistency and finish. One of the defining characteristics of this material removal process is the ability to obtain precise surface roughness levels. An age-old method that technology has come to render more precise.
Table of Contents
What is Machining Lapping?
The lapping process is a form of fine polishing and surface finish. Many industries rely on this method and use it for several types of material. It usually involves the removal of surface defects through friction.
Machining lapping is usually done with the help of a flat lapping machine. The surface of the workpiece rubs against the lap of the machine (usually a surface of iron), using abrasive material like emery, silicon carbide, or diamond.
The high precision of the machine achieves a very fine and consistent surface, free of even microscopic imperfections. Although machining lapping usually produces a uniformly smooth and flat surface, it can also produce concave and convex surfaces.
How Does Lapping Work?
Lapping is a loose abrasive process (LAP). It mainly relies on the use of an abrasive mixture, a Slurry, or a liquid cutting tool. The Slurry is a mixture of abrasive and a water-based or oil-based solution. In a batch process, the several parts are held in place using the retaining rings, and the abrasive mixture is then placed on the flat lap plate. The parts are then dragged across the lapping plate surface in a circular motion.
Surface accuracy (or surface flatness) and roughness are the common objectives of the lapping process. These parameters are both closely monitored during the process. Roughness is measured usually in microns, or by quantifying the averaging the variances of peaks and valleys (Ra value). while accuracy, or flatness, is measured in Helium Light Bands (HLB). Light interference is now an increasingly precise measuring technique, employing lights with the smallest wavelength.
The required levels of surface roughness determine the choice of the abrasive. Abrasive particles of smaller grain size (less than .025 micron) like aluminum oxide are more conducive to very fine, almost undetectable micro scratches, and produce a fine finish.
Common Applications of Machining Lapping
As in many surface finish processes, grinding and lapping have several industrial applications. This method is mostly common for parts and components requiring specific surface finishes with tight tolerances. For example, in the automotive industry, several components go through this process, such as brake cylinders and pistons, spline and gear shafts. As many of these parts need to fit between several components, the surface finish produced by lapping and grinding gives these bearings the perfect fit they need. Grinding and lapping also have specialized applications in the medical industry, mostly to produce surgical drills, and some parts of joint implants.Â
Most of the parts used in the aerospace industry require high strength, as they often operate near the severe environment of jet engines and turbines. These components are difficult to process using conventional manufacturing tools, and often go through the grinding process. These attributes are what makes the grinding process a perfect fit for most machine tools / parts manufacturers.
General Guidelines
There are several guidelines and specific parameters requiring special attention during the process. The speed of the plate is by far the most important factor to consider in machining lapping. Higher speeds are inductive to smoother surfaces but are also more likely to cause certain objects to vibrate. An optimal speed would keep the workpiece firm in place.
The desired effect and surface texture determine the choice of abrasive particles. Besides the crystal size of abrasive compounds, the different friability can also affect the final result. The crystal size decreases during the process as cutting edges break. Harder compounds like Silicon Carbide have low friability and can generate greater surface roughness before their cutting edges begin to break.Â
Pressure can also affect abrasive compounds. Higher pressures (3 PSI and above) can affect the thickness of the abrasive mixture. Most applications require a pressure no greater than 2-3 PSI. Although machining lapping is a cost-effective technique, it has limitations. This process can remove only a limited amount of material from the workpiece.
Common Abrasive Compounds
As the required surface finish determines the choice of abrasive, grinding and lapping are compatible with a wide range of abrasive compounds. Each delivers specific levels of roughness. There are generally two categories of abrasives; natural and synthetic. For example, industrial diamond, corundum and emery are considered natural abrasives, with higher grain size. They are often used for cutting glass or grinding metals.Â
Flint, quartz and pumice are also natural abrasives but are more brittle than emery and are used mainly for smoothing surfaces and finer finishes. Synthetic abrasives are almost entirely high grain size compounds. Examples include silicon carbide and boron nitride.
Difference Between Lapping and Grinding
Although these processes are fairly similar and have the same objective, they differ in some key aspects. Machining lapping involves the use of an abrasive mixture to create friction between the lap plate and the workpiece.
Grinding on the other hand is a machining process that uses an abrasive wheel to smoothen a surface. The abrasive wheels (or grinding wheels) used in the grinding process are usually composed of the same abrasive material used to make the Slurry mixture, and conform to the same parameters of abrasive grain size and friability.
The two processes can also differ in terms of material. Grinding is mostly compatible with harder materials like metal and glass. However, machining lapping is more compatible with brittle materials like pitch, ceramic, and stone.
Different Types of Grinding
There are different variations of the grinding process, depending on the requirement of the final product. These variations usually involve spindle orientation. Peripheral Surface Grinding is one of the most common methods. This technique can smoothen flat surfaces in edges, angled or recessed surfaces. The outer edge of the grinding wheel (the periphery) is usually in contact with the workpiece
Vertical-Spindle Grinding, also referred to as snow grinding, consists of a vertical spindle rotating the grinding wheel, in an indexed rotation. A reciprocating table holds the workpiece in place and facilitates the indexed rotation. This motion allows the operation to continue in one station while unloading the other. Surface grinding involves a greater area of contact between the workpiece and the grinding wheel.
Other variations can differ in terms of the size of contact area and wheel orientation, as well as the number of discs. A double-disc grinder per example can work on two sides of the workpiece simultaneously (double-sided lapping).
Pros And Cons
The grinding operation is optimal for many industrial uses. This is largely due to its capacity to process hard materials like iron, steel and some types of ceramic and pitch. This process is very reliant on detail, which makes it perfect for uses requiring high quality and accurate surface finish. It can obtain precise dimensions, and specific levels of roughness. Nonetheless, grinding and lapping are limited in some regards.Â
This process usually relies on specialized equipment (grinding wheels, specific abrasive compounds of different grain sizes, and flat lapping machines), which can often make the process costly. In addition, grinding and lapping usually require skilled workers, as the process is detail-reliant. Any small misstep or imperfect contact can damage the workpiece. This process is also unable to remove large amounts of material from the workpiece
Conclusion
When it comes to surface finishes, there are many techniques, depending on the desired effect. For a tight tolerance machining process, grinding and lapping are industry standards in terms of dimensional accuracy and precision. The cost-effectiveness and accuracy of this method make it the optimal choice for mass production and quality.
As of now, most materials can be lapped, each with specific requirements in terms of pressure, abrasives, and cutting precision. As manufacturing technology develops, it will bring about further improvements to these techniques.