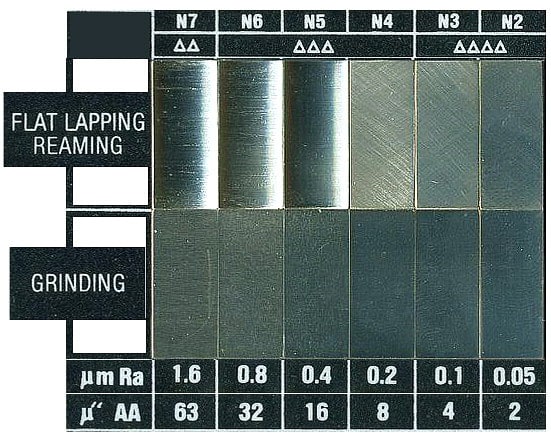
When discussing CNC machining, one of the most important variables is what finish will be applied to the product. There are a variety of surface finishes charts that can be used to help machining operations. The most common type is the roughness chart which shows a graphical representation of the roughness of a surface. This can be used to help determine the best machining process for a given surface.
Another common type is the surface finishes chart, which shows the actual surface finish measurements for a given surface. This can be used to help determine if a surface is within the desired tolerances.
As a best practice, using this chart along with the roughness chart can help operators to understand exactly what parameters they need to stay within.
Table of Contents
The Importance of Surface Finish in CNC Machining
CNC machining is one of the many manufacturing processes that can produce a surface texture. By optimizing the process, the resulting texture can be usable without the need for further modification.
There are many factors that go into creating a quality part through CNC machining, and surface finish is one of the most important. A good surface finish will ensure that the part functions as intended and looks aesthetically pleasing. There are a number of factors that affect surface finish, including the type of material being machined, the tooling used, and the machining parameters.
The following image showcases a surface finishes chart of popular finishes that are often created by various manufacturing methods:
This is especially true for parts where the finish plays a critical role, such as on components for wear resistance. The most important aspect is to use a surface finish that provides a consistent surface quality throughout the part.
Understanding Surface Finish and How to Measure it
Surface finish is an important consideration when manufacturing parts. It affects the appearance, wear, and lubricity of the part. There are three parameters that distinguish a surface finish lay, roughness, and waviness. Each of these parameters can be classified in terms of the geometrical shape of the surface. Which is created when a tooling form and/or material, such as abrasive grains, impacts the surface of a workpiece. The geometric shape that results from a tooling form and material combination creates a unique surface profile.
Measuring surface finish is also referred to as surface metrology. It is an important part of many fields and is mostly known for the CNC machining of precision parts and assemblages.
There are two ways to measure the surface finish: contact and non-contact methods. The contact method is more common and involves the use of a stylus. This involves using a stylus with a mirror at its tip. A technician will place the stylus on a workpiece and move it along the surface. The stylus will reflect light back to a screen where the surface finish can be viewed.
The non-contact method, though less common, is not only more accurate but also more convenient in that it is automated. This is because the surface finish is measured through laser reflection. Also, the non-contact method can be used to measure both hard and soft materials.
Another surface finish measurement method is the comparison method. This method involves taking two steps. First, a sample is measured using a particular surface finish measurement method. Second, the same sample is measured again by a different surface finish measurement method. The result of the first measurement can be used to compute an accuracy factor for the second measurement. This allows surface finish measurements to be compared to other surface finish measurements without making any assumptions about the repeatability of the different methods used.
Factors that Affect Surface Finish
The surface finish of a product is affected by a variety of factors, including the material from which it is made, the manufacturing process used, and the environment in which it is used.
Some factors, such as the composition of the material, are largely beyond the control of the manufacturer. Others, such as the manufacturing process, can be controlled to some extent, and the manufacturer must take these factors into account when designing a product.
The type of material being machined:
The type of material being machined affects the surface finish that can be achieved. Hard materials, such as metals, produce a smooth surface finish, while softer materials, such as plastics, produce a rougher surface finish.
The sharpness of the cutting tool
The sharper the cutting tool, the better the surface finish will be.
The type of cutting fluid
The type of cutting fluid used can affect the surface finish of the workpiece. For example, a cutting fluid that is high in oil content can leave a film of oil on the workpiece that can lead to a poor surface finish.
The feed rate
The feed rate affects surface finish because the faster the feed rate, the more passes the tool will make over the material, which leads to a rougher surface finish.
The depth of cut
The depth of cut affects the surface finish of the workpiece. A shallow depth of cut produces a smooth surface finish, while a deep depth of cut produces a rough surface finish.
Surface Finishes Chart Symbols and Units
There are many surface finishes chart symbols that you may come across while reading or creating technical drawings. These symbols indicate the appearance of a surface after it has been machined. Each of these symbols has a specific meaning and can be used to describe different aspects of a surface finish:
Ra – Average Roughness
Ra is a measure of the average roughness of a surface. It is a unitless quantity that expresses the average height of the surface irregularities, or peaks and valleys, over a given length.
Rz – Average Maximum Height of the Profile
Rz calculates the average difference between the five largest peaks and valleys. This measurement is done using five different sampling lengths, in order to eliminate any errors. Ra is quite insensitive to some extremes, so this calculation is very helpful.
Rmax – Vertical Distance from Peak to Valley
Rmax is more sensitive to anomalies such as burrs and scratches that cannot be seen only by Ra.
RMS- Roughness average magnitude surface
The RMS- roughness average magnitude surface is a surface that is used to measure the average roughness of a surface. This surface is created by taking the absolute value of the surface’s RMS roughness magnitude.
PE- Profile roughness
The profile roughness of a material is a measure of the size and distribution of the surface irregularities. It is usually expressed in terms of the height of the largest peak or the depth of the deepest valley on the surface.
PS- Profile smoothness
Profile smoothness is the average area of flat surfaces in a profile of a surface. It is usually expressed in terms of the breadth of the flattest section of the surface or the thickness of the thinnest portion of the surface.
PT- Profile tolerances
Profile tolerances are the allowable deviations from a nominal profile. They are important to ensure that parts fit together correctly and perform as intended. Profile tolerances are specified in terms of the maximum allowable deviation from the nominal profile at any point along the part’s length.
Surface Finishes Chart Cheat Sheet
FAQ – Surface Finishes Chart
What is the steel surface finish chart?
The steel surface finish chart is a guide to help identify the most common surface finishes on steel. It describes the surface finish’s associated visual appearance and typographical appearance and is not meant to be prescriptive. For example, the chart does not include every possible combination of finish color and typographical appearance.
What is the plastic surface finish chart?
The plastic surface finish chart is a guide to the various finishes that can be applied to plastic parts. The chart lists the name of the finish, the roughness (in microns), and the applications for which it is best suited.
What does a 32 surface finish mean?
A surface finish of 32 means that the surface has an average roughness of 32 microinches. A roughness of 32 microns is the equivalent of 1/32 inch. The closest surface finish to a 32 finish would be a 6 surface finish and smoother.
How do I choose a surface finish?
The surface finish you choose for your project will be based on the look you are trying to achieve, as well as the function of the surface. Some common surface finishes include matte, satin, semi-gloss, and gloss.