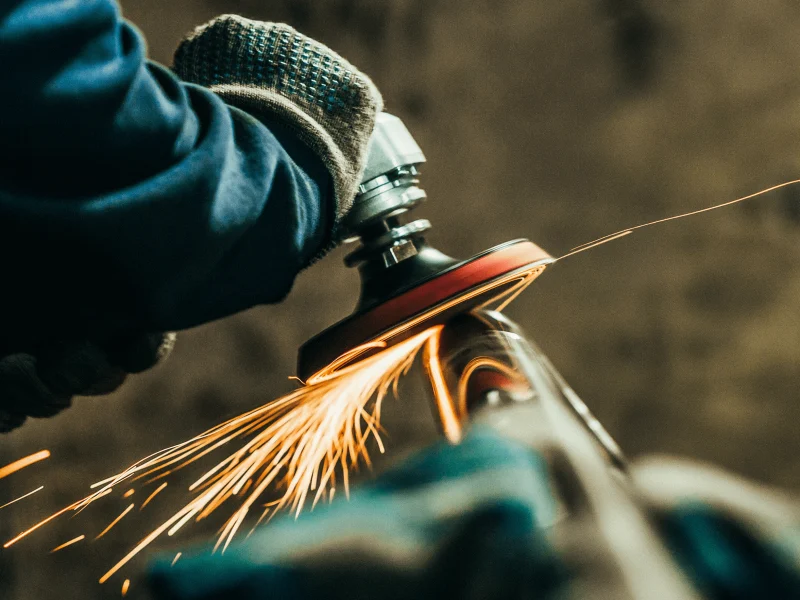
Metals are some of the most resistant and reliable materials available to us. As such, they’re versatile in their industrial and mechanical applications due to their strength. This makes them often in contact with degrading elements or conditions, like air, heat, high electrical current density. Metal parts require an impermeable surface finish that would enhance their resistance and prevent them from decay.
Because it significantly contributes to the corrosion resistance of metal parts, as well as their aesthetic appeal, functionality, and tight tolerances, a polish finish is one of the standards of manufacture in multiple industries. Polishing can also prevent contamination of metal parts and remove oxidation, making the process optimal for other uses requiring solid components. Though surface polish has been in application for many centuries, on a variety of materials, ranging from copper and metals to glass and wood, most of the industrial applications of this process now focus on metals.
The process consists of applying friction to the substrate to make its surface more uniformly flat, smooth and consistent. It applies the same principle as grinding or lapping but is still different in many regards. Depending on the specific metal used, polishing finishes come in several varieties, and to differing effects. Polishing can often keep a surface in excellent conditions, yet requires specific measurements and design guidelines to harness its full potential.
Table of Contents
How Does It Work
The surface polishing process is sometimes also referred to as buffing, although there is a slight difference between the two. Buffing refers to the final stages of the process, where small imperfections in the surface, not visible to the naked eye, are smoothened. The general process, or principle, of polishing, is different from the newer methods like electrolytic polishing, or chemical polishing.
This method usually begins with a rough abrasive of higher grain size. This is largely dependent on the initial state of the workpiece. The aim here is to remove the major imperfections; convexities, scratches, lines, or pits. This method involves the use of an abrasive, in an oil-based mixture, polishing pads and buffing wheels. Afterward, the process employs finer and finer abrasive grains, to refine the more minute valleys and peaks. Manufacturers often use this technique to obtain a reflective surface, or mirror finish, using high-speed polishing machines.Â
As of now, surface polishing can apply to more materials. Metal is by far the most common, and now it includes soft metals like copper and brass, silver and gold, as well as plastic. Although the substrate’s material and the desired finish largely determine the choice of buffing compound (abrasive), the process is organized into three main stages. Rough, Initial buff, and final buff, each using finer and finer abrasive grain size, significantly impacting the polish finish.
The wafers, or buffing wheels, are various. Each type has uses, for specific types of materials, and steps of the process. The common ones include Canton flannel, string, and sisal fiber. Similarly, the buffing compound is also specified for distinct usages and is categorized by color.
Different Types Of Polishing
The regular surface polishing process, also referred to as mechanical polishing, is by far the most used. This method is largely effective, customizable through the use of precision or high-speed polishing machines. It also produces of different types of polish finish. However, modern developments in technology and manufacturing have facilitated the use of other methods.Â
Besides mechanical, polishing methods also branch into electrolytic polishing; the use of anodic reactions to level-up the peaks and valleys of the surface and increase corrosion resistance; and mechanical polishing; a method combining regular mechanical polishing with the use of chemical solutions to dissolve the protruding area of the surface.
In chemical polishing , the dissolution of the surface, or passivation, helps form a protective layer. This method is compatible with workpieces with complex shapes, and is more often reserved for metals. Chemical polishing is quite efficient in that it achieves high precision on a micro-roughness level, although it can often release hazardous waste, and is difficult to reverse or adjust.Â
Electrolytic polishing, or electro-polishing, is more similar to anodizing in its use of electrolytic in its use of an anodic reaction. Compared to chemical polishing, this method is much more effective in color consistency and corrosion resistance. Yet, electrolytic polishing becomes complex as it relies on extensive pre-polishing and design measurements. This method is most commonly used for pipes, valves, and some medical equipment like scalpels and bone/joint implants. Â
Difference Between Grinding and Polishing
Although both grinding and polishing processes use the same mechanics, there is a slight difference between the two. This shows up mainly in the level of roughness and detail, with regards to the substrate’s surface. In a manufacturing process, the polishing phase usually comes post-grinding. In this sense, grinding/lapping prepare the surface, by removing the major surface imperfections, scratches, and differences between peaks and the valleys and light imperfections. Polishing on the other hand levels up the surface on a micro level.
Some types of surface finishes require only grinding/lapping, as this method can now obtain a wider range of surface finishes. Polish finish remains however a standard in most high-precision industrial demand.Â
Pros and Cons of Polishing
Although polishing is widely applied, for multiple usages and in various industries, it has its shortcomings, which make it incompatible with certain applications. This also applies to the different types of polishing processes.Â
For example, regular mechanical polishing can often produce a high gloss finish on the surface, which doesn’t usually last for a long time, but this method consistently gives a cleaner surface and the best quality surface finish. Nonetheless, this method relies on skilled laborers. It isn’t always optimal for complex shapes and workpieces, and the surface finish it produces isn’t resistant to corrosion.Â
Chemical and electrolytic polishing often offset the shortcomings of the mechanical method. Despite their higher efficiency, improved surface protection, and low cost, these processes are vulnerable to other factors. Chemical polishing per example doesn’t always produce a consistent brightness, coupled with environmental hazards, while electrolytic polishing relies on high current densities, which is quite volatile, requiring constant monitoring and complex additional equipment.Â
General Guidelines
Polishing is a detail-reliant task. Not only does the required finish determine many of the decisions throughout the process –choice of abrasive type and buffing wheel-, the surface finish is vulnerable to many subtleties of polishing. As far as buffing wheels go, the variety of materials ensures the production of several types of surface finish, but abrasive discs with polyester fillings are preferred as they can achieve a more uniform and consistent finish.Â
Each abrasive compound is specific to a distinct material of the buffing wheel. However, it is possible to avoid this by cleaning the compound residue, thoroughly, from the buffing wheel before usage.
Like most surface finishing processes, polishing too requires pre-treatment. The surface should be cleaned, and have any lacquer removed to ensure better contact between the substrate and the buffing wheel.Â
Applications And Different Materials
The polishing technique is applied to a wide range of appliances ranging from household items like kitchenware, sinks, and electronic equipment, to architectural metal, medical equipment as well industrial parts like turbine blades, wheels, and safety equipment.Â
There are generally six types of abrasive; black (emery compound), white (aluminum oxide), red (Jeweller’s rouge), brown (rottenstone), green compounds (chromium III oxide), and blue (drier red compound, used on its own wheel). Each is specific to a stage, or a type of material. Blue buffing compound for example is mostly used for plastic and the final buff of some metals. Green compounds are compatible with stainless steel. Black buffing compound on the other hand is reserved for rough buffing harder metals.Â
Similarly, there are six types of buff type (material of buffing wheel), each with specific usage guidelines. For example, stainless steel, iron, chrome plating, and some soft metals like copper and brass rely on sisal fiber during the rough buffing phase, whereas a material like string is used only with plastic, for all stages. Â
Many metal parts are polished in order to obtain a reflective surface, or mirror finish, using high speed polishing machine. This is mostly compatible with iron and steel and it significantly improves their appearance.
Conclusion
The polishing process is key to a consistent, protective, and functional surface finish. Besides the aesthetic appeal, which is the most prominent feature of this process, polishing is also cost-effective and multipurpose. As it manages to cover more materials, and develop newer methods, the potential of this method expands to produce multiple types of surface finishing. The quasi-reflective surface and uniformly smooth texture, coupled with a consistent color dispersal and corrosion resistance are hallmarks of the polishing process, making it a standard of several industries.