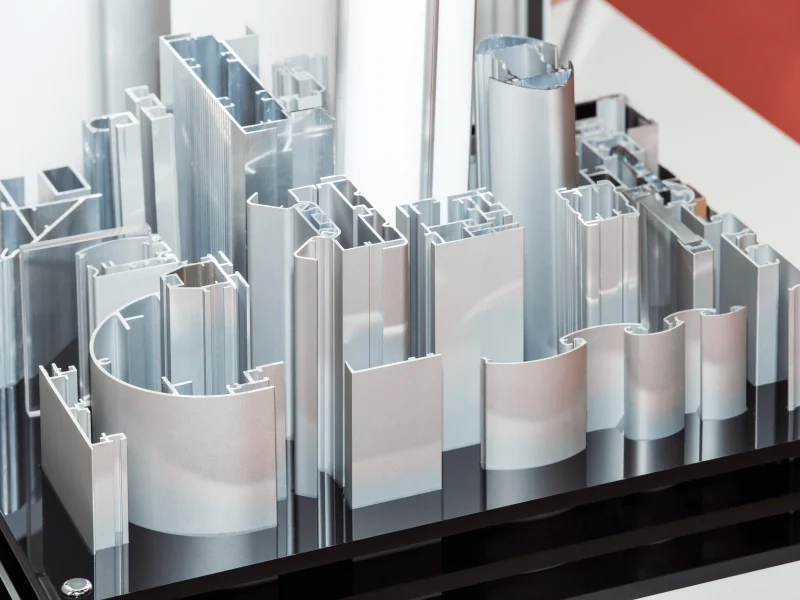
Anodizing is a metal finishing process, which creates a thin, hard, and corrosion-resistant layer on the surface of the metal. Anodized aluminum is widely used in aircraft construction because it is lightweight and resistant to corrosion. Although this process has mostly been applied to aluminum parts, it can now also work for a variety of materials such as zinc, titanium, magnesium, and zirconium. This process works mainly for non-ferrous metals, as they do not contain large quantities of iron. Iron exfoliates when anodized, forming a layer of iron oxides (rust), which deteriorates the material.
The main advantage of anodizing is adding an anodic oxide finish, which works as anti-corrosion protective later. To create an anodized coating, aluminum is first immersed in an acidic electrolyte solution that reacts with the surface of the metal. The aluminum then goes through one or more baths of electrically charged water where it is subjected to electrochemical reactions that cause it to form oxide layers on its surface.
For some metals, notably types of aluminum alloy, the regular anodizing process may not always provide as reliable as surface finish and protective film. For this, a specialized alumite treatment liquid is used, in a method known as precision anodizing.
Table of Contents
How It Works
Like most surface finish processes, the first step is surface preparation. This is in order to clean the surface from impurities that can hinder the final result. A solution is usually applied to the material for this process, referred to as a Desmut solution. Nitric acid had been commonly used for this process but is no longer applied due to environmental concerns.
After the cleaning process, the material is placed into a bath of an electrolytic solution. When a direct electrical current is applied, it creates a positive electric charge in the material (usually aluminum) and a negative charge in the solution’s electrolyte plates. The material functions as an anode with the aluminum plates of the electrolytic cell functioning as the cathode. This reaction releases oxygen into the surface of the material. This enables the substrate to bond with oxygen ions, creating aluminum oxide.
The acidic solution in which the substrate is dumped slowly dissolves the aluminum oxide, forming at the surface. This balance forms nano-pores on the surface. These pores allow the solution to reach the substrate, grow the protective layer to a greater thickness, and facilitate the absorption of the dye. In the latter case, the anodizing process is usually followed by a sealing stage to keep the dye layer intact.Â
Different Types of Anodizing
Anodized finishes usually have multiple applications, ranging from industrial to decorative uses. This required result is what determines the anodizing method. The anodizing process comes in three varieties. Type I Chromic acid anodize, Type II sulfuric acid anodize and Type III hard anodizing. The difference between each method depends on the type of acidic solution, and the results each one can yield.
Type I chromic acid anodizing uses chromic acid and is designated by the MIL-A-8625 standard. This method is most commonly used for airplane parts that can be exposed to propellants. This method often relies on higher voltage and produces thinner coatings. For metal parts requiring a dyeing process, anodizing is applied mostly as a pre-treatment.
Type II uses sulfuric acid and is the most widely applied method. It produces a thicker layer than chromic acid. Type II anodizing has high porosity and creates a wear-resistant layer. It’s often for decorative purposes and is compatible with dyeing.
Type III hard anodizing is a much more specialized process, often reserved for mechanical metal parts, and other items requiring excellent corrosion resistance and wear protection. It’s similar to Type I in that it also uses sulfuric acid, but results in a much thicker protective layer, and offers the best abrasion resistance. It’s also compatible with dyeing. The main difference between these methods is the coating thickness.
Color Options
Anodizing, especially for aluminum parts, is distinct in that it only offers a limited choice of colors. These include clear, bronze, black, gray, and champagne, but recent developments in this technique have enabled manufacturers a much more diverse palette. This method can also produce a white coating with 80 % reflectivity.Â
Organic acids, notably oxalic acid, have been used for quite some time to produce integral color anodizing. However, the last few decades have seen an increasing reliance on sulfonated aromatic compounds being applied for this process, mostly sulfosalicylic acid, which can achieve a much thicker coat.
Common Applications
Anodizing is both a high and affordable process, which makes it one of the most adopted in several industries and manufacturing operations. For example, structures and architectural beams of all types go through this process. Storefronts, roofing systems, and other building exteriors are often anodized. The anodizing process is also a standard application for many automobile parts and the aerospace industry, for components like trim parts and wheel covers, and exterior panels for planes. Transport vehicles, in general, contain many anodized components.Â
The anodizing process is also useful for other non-industrial applications. Television sets and microwaves, as well as other home appliances, are anodized. It’s safe to say that most aluminum parts, or ones made from non-ferrous metal, often go through this process. The surface finish of anodizing is both practical and aesthetically pleasing. This, coupled with the increased durability of anodized materials, makes this method one of the most effective and common across industries.
Advantages of Anodizing
Compared with other surface finishing methods, anodizing is more prone to sustainability and durability. Its prominent effect is the increased resistance of the material against corrosion and scratching. Since the anodizing process is electrochemical, the protective layer is embedded into the material. This is what gives anodized materials an insulating property. Another advantage of anodizing is the aesthetic appeal of anodized surfaces. By now, anodizing can offer a wide range of colors, with a uniform finish.
General Guidelines
The anodizing usually adds thickness to the part (some methods more than others). This should be closely monitored for products with tight tolerances. For such products, Type I and Type II are the most optimal.
For circular designs and angles, it should be noted that all the edges must have a radius of at least 0,5 mm. The electric current is prone to overheat, or even burn, the metal substrate if these parameters are not accounted for in the design.
To achieve a completely uniform surface finish, it’s preferable to apply another surface finish method before anodizing. The latter is an electrochemical process, which can often leave machine marks on the surface.
It’s quite difficult to exactly match the color of an anodized surface with another piece. Therefore, it’s preferable to work in small batches. When several small parts are anodized in the same batch, a greater degree of color uniformity is obtained.Â
The anodizing process usually creates a matte finish on the material’s surface. This is a sign that the process has been successful. The matte finish is a non-gloss and non-reflective layer, uniform in color. Usually, a simple scratch would suffice. Anodized materials are completely scratch-resistant. Successful anodizing would also produce even color distribution.Â
High voltage is very common in metal anodizing. As such, it’s vital to closely monitor burns and increased temperature. Anodizing burns are not uncommon and often occur as a result of high current density.
Most anodizing processes aim to obtain a protective layer above the substrate’s surface ranging between 3 and 25 µm. Although this method usually develops a solid protective layer and reliable corrosion resistance, it is not durable for some aluminum alloys. This is where advanced precision anodizing becomes necessary. This method is similar to regular anodizing process, but relies on alumite treatment liquid (a chemical solution added to the electrolytic cell) which achieves a precise coating (usually between 9 and 11 µm), stable even for thicker coatings.
Anodized Aluminum and the Environment
Anodizing has long been associated with aluminum, although it can apply to other non-ferrous metals as well. The durability effects that anodizing has on non-ferrous metal have also proven to be environment-friendly. Anodized metals, especially aluminum, are recyclable, which helps save the energy required to produce more aluminum. This quality is also accentuated with reinforcing properties of the anodizing process. Compared with other metal surface finish methods, anodizing is both cost-effective and can significantly enhance the life cycle of aluminum parts. Anodizing essentially accentuates the environmental benefits of aluminum.
As a water-based process, anodizing does not use any VOCs (Volatile Organic Compounds), toxic organics, and no solvents. The colors generated through anodizing use an insignificant amount of dye. In addition, anodizing produces no hazardous waste.
As more and more non-ferrous metals are becoming compatible with anodizing, this will increase the number of recyclable metals, and significantly decrease industrial demand for durable material. The environmental benefits of anodizing exceed the impact it has on a component’s life cycle, but constitute a reliable and environmentally safe industrial process that would fulfill demand in several industries.
Conclusion
By now, most appliances and equipment we come across in our everyday lives are anodized, or at least contain several components that have been through the process. There are multiple reasons why this method has become widely adopted in several industries. Other than the environmental benefits it has, and the aesthetic appeal it can add to appliances and materials in general, anodized metals are the optimal solutions to many industrial and consumer demands, in terms of reliability, durability, and corrosion protection.