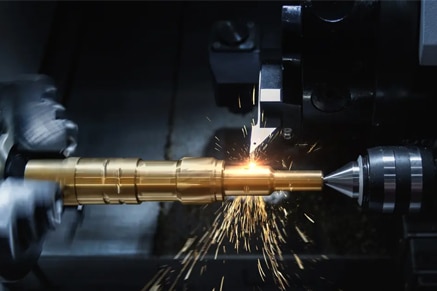
CNC machining technologies are now a staple in many manufacturing and production environments. These computer-controlled machines can be used to create intricate parts or products. Programming and using a CNC machine can be complex, but with the right guidance, it is a breeze. In this article, we will first unveil the ins and outs of turn-milling and proceed to show you how to optimize your turn-milling CNC machine use for optimal performance.
Table of Contents
Turn-Milling: Milling a Rotating Workpiece
CNC milling machines are the workhorses of the modern manufacturing world. These versatile machines can be used to create a wide variety of parts and products, from small components to large ones. One of the most popular milling methods is known as turn-milling.
Turn-milling is one of the most versatile machining operations out there. In turn-milling, the workpiece is held in a chuck and rotated while a milling cutter is fed into the workpiece. The milling cutter then removes material from the latter. The rotation during the turn-milling process creates a helical path. Which makes the shape of the cutting edge of the cutting tool best suited to the respective milling operation.
This machining operation is used to create a variety of odd shapes and features on a workpiece that cannot be created using a traditional mill. These include threads, grooves, and other internal features on a workpiece. Since turn-milling is a two-step operation, the two separate steps can be repeated multiple times on the same workpiece, while different cutting tools are used in each step. The first step being to turn the workpiece on a lathe which creates the cylindrical shape, and the second is the milling of the piece and creating the desired product.
Choosing between turn-milling processes
Face turn-milling on a 4 or a 5-axis machine is a great way to quickly and accurately remove material from the outside of a workpiece. This type of machining is often used for creating complex shapes or for machining parts with very tight tolerances.
It is a better-suited option when it comes to machining external and slender components. This is because it allows for a smaller tool diameter which results in a smaller contact area with the workpiece, and therefore less torque is required to achieve the same cutting action. In addition, shorter tool extensions will also reduce the risk of tool breakage, especially when machining on a not a natural cylindrical surface.
Meanwhile, periphery turn-milling is the type of machining recommended for creating internal features on a workpiece. This process is well suited for creating threads in narrow slots or with rounded corners.
The CNC Turn-Mill Machine
A CNC turn-mill machine is a milling tool programmed to mill and turn parts to precise specifications. It is typically used for production work and is able to produce large quantities of highly intricate parts for various applications and industries (automotive, aerospace, medical…etc).
The CNC turn-milling machine has several components, including:
- The spindle: the part of the machine that holds the cutting tool and rotates it at high speeds.
- The chuck: a device that holds the workpiece in place while it is being machined.
- The tool turret: a rotating platform that holds the various cutting tools that are used by the machine.
- The X-axis: the horizontal axis on which the milling machine operates. The X-axis is typically placed on the back of the machine and is connected to the spindle, which holds the milling cutter.
- The Y-axis: the vertical axis of the machine. The Y-axis is typically placed on the front of the machine and is connected to the tool turret, which houses the cutting tool.
- The Z-axis: the virtual axis that moves horizontally. The Z-axis is typically placed between the spindle and tool turret and connects the X-axis to the Y-axis.
About Programming a CNC Turn-Milling Machine
With the ability to create turned parts with diameters ranging from a few inches to several feet, CNC mill turning machines are a must-have for any serious machinist. While there are many different ways to program a CNC mill-turn machine, the best way will vary depending on the specific machine and the desired outcome. Let’s start with the basics of CNC programming.
CNC programming is the process of creating a program that creates instructions and tells a CNC machine what to do. The program is written in a special language called G-code which is a numerical control (NC) programming language. It is used mainly in computer-aided manufacturing (CAM) and computer-aided design (CAD) to control automated machine tools such as CNC machines, and 3D printers.
When it comes to turn-milling, the process can be programmed using a variety of different software packages. his can help you get the most precise results possible.
If you don’t have access to a turn-milling specific program, it’s still possible to program your CNC machine manually. The best way to do this is to look at a turn-milling diagram and identify the different operations required.
Tips for Optimizing CNC Turn-Milling Machines’ Performance for greater accuracy
In order to get the most out of turn-milling machines, it is important to optimize their performance. Here are some tips to help you do just that.
Tool life and tool wear
In order to ensure maximum productivity of the machine, it is necessary to regularly maintain and repair the tools and cutters and replace the worn parts. To do so, make sure to:
- Use high-quality tooling. All the cutting tools used on CNC machines are made of special materials. The right tool should be purchased and maintained in order to maximize the life of the tooling.
- Inspect your tools regularly and replace them as needed. 3. Use the correct cutting tool for the material.
- Do not exceed the maximum speed or load of the machine as higher speed rates decrease the tool life.
Roundness
The roundness of the machined part is impacted by the workpiece diameter, the workpiece rotational speed, the number of teeth, and the spindle cutting speed.
There are a few ways to optimize the roundness of a part while using a turning mill. First of all, make sure to use a shorter tool. This will allow for a more constant cutting pressure, which will result in a more circular part. Additionally, use a higher cutting speed which will minimize the amount of material that is removed from the workpiece.
Surface roughness
The surface finish of a product is usually what determines its quality. There are certain technical requirements that must be met for certain products. Achieving the desired surface finish quality is essential for the proper functioning of a part. For best results, ensure to follow these tips:
- Make sure that the tool is sharp and in good condition.
- Use a coolant or lubricant to help reduce friction and heat.
- Use a lower feed rate and speed to avoid chatter and vibration.
- Experiment with different tool geometries and coatings to find the best combination for the material being machined.
Conclusion
Turn-milling is one of the most versatile machining operations out there. This machining operation is used to create a variety of highly intricate shapes and features on a workpiece that can not be created using a traditional mill. In this article, we went over the details of turn-milling and everything you need to know as a machinist on how to optimize your turn-milling CNC machine use and get the highest performance out of it. To do so, we mentioned that it is necessary to regularly maintain and repair the tools and cutters and replace the worn parts.
About Xin Tian Jian
Xin Tian Jian is a surface finishing and CNC machining company that delivers quality services. We have been ISO 90001-2015 certified and we offer customized manufacturing with free consultation services.
We provide a comprehensive range of surface finishing and CNC machining solutions, including cutting, grinding, polishing, anodizing, powder coating, plating, and more. We also offer online quotations for any inquiries. It’s quick, easy, and confidential so you know exactly how much it’ll cost before we start your project.
If you have any questions about custom manufacturing or would like to speak to one of our experts, please feel free to contact us without any obligations or pressure.