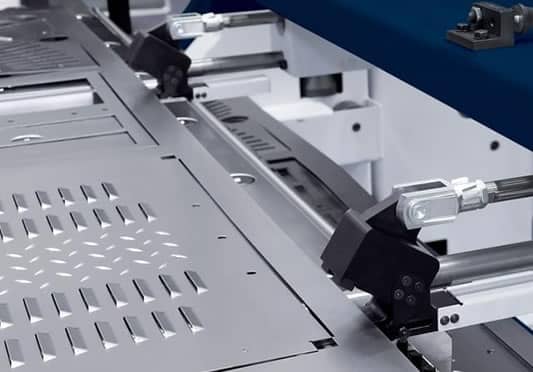
Sheet metal punching and sheet metal stamping are two common sheet metal fabrication techniques used in numerous industries. Sheet metal punching uses a punch press to cut holes or basic shapes into metal sheets while sheet metal stamping uses a die and press to form metal sheets into desired shapes. Both techniques have their advantages and disadvantages. Sheet metal punching is a simpler process compared to stamping which makes it more cost-effective for simple designs and small-volume production runs but has limitations when it comes to complex features. Sheet metal stamping is better for complex-geometry parts or large-volume production runs but is more costly. This article will review the key differences between sheet metal punching vs. sheet metal stamping to help you make an informed decision on which process is more suitable for your project.
Table of Contents
What Is Sheet Metal Punching?
Sheet metal punching is a cutting process that uses a die and a punch press to cut holes into metal sheets or to obtain desired shapes from sheet metal workpieces. When using a punch to obtain a sheet metal part with a particular profile, the process is called blanking. Both punching and blanking are effective methods for quickly processing sheet metal parts.
What Does Sheet Metal Punching Look Like?
In sheet metal punching, a flat metal sheet is fed into the punching press in which a die lowers and cuts the desired profile into the workpiece. Figure 2 below shows a sheet metal punch press:
Sheet metal punch press.
How Does Sheet Metal Punching Work?
Sheet metal punching works similarly to sheet metal stamping in that the die and punch press lower and exert force into the metal workpiece to remove material. If the stress induced by the punch is higher than the shear strength of the workpiece, then the material will be removed. The primary difference between sheet metal punching and sheet metal stamping is the die used for sheet metal punching. A sheet metal punching die is simpler compared to a stamping die as a punching die’s purpose is to only cut a hole into the sheet metal workpiece.
Why Use Sheet Metal Punching?
Sheet metal punching is perhaps the cheapest manufacturing technique for creating holes and other profiles in small or large volumes of sheet metal parts. Multiple holes or profiles can be cut into or from a sheet metal workpiece in a single process which makes it an economical sheet metal fabrication technique. Additionally, the simplicity of the punching tooling compared to stamping tooling makes it a viable technique for prototyping, in addition to small and large production volumes.
What Are the Different Applications of Sheet Metal Punching?
Sheet metal punching is used in many industries—from electronics and automotive to architecture and furniture. Applications of sheet metal punching include: hole creation in electronic panelings and connections, automotive chassis and brackets, furniture, and architectural trim pieces.
What Machine Is Used for Sheet Metal Punching?
A punch press equipped with a punch and die set is the primary machine used for sheet metal punching.
What Are the Materials That Work Best With Sheet Metal Punching and Sheet Metal Stamping?
Both sheet metal stamping and punching work well with metal materials like: mild steel, stainless steel, aluminum, brass, and copper.
What Are the Advantages of Sheet Metal Punching?
Sheet metal punching has many advantages which are listed below:
Cost-effective: Because of the simplicity of punch dies compared to stamping dies, punching is generally more economical for simpler designs and smaller production runs.
High-speed Production: Multiple holes or profiles can be cut in a single process which enables efficient, high-speed production of sheet metal products.
Minimal Material Waste: As with metal stamping, material utilization rates are high with sheet metal punching. Therefore, manufacturers can maximize the number of products they can generate from a single piece of sheet metal stock.
Consistency: Sheet metal punching is an easily repeatable process and ensures consistency in the shapes created by the process.
XTJ is a leading OEM Manufacturer that is dedicated to providing one-stop manufacturing solutions  from prototype to production. We are proud to be an ISO 9001 certified system quality management company and we are determined to create value in every customer relationship. We do that through collaboration, innovation, process improvements, and exceptional workmanship.
What Are the Disadvantages of Sheet Metal Punching?
Sheet metal punching is not without its disadvantages which are listed below:
Unsuitable for Complex Shapes: Achieving complex shapes poses a significant challenge in sheet metal punching. This is because punching is intended to perforate sheet metal to create basic shapes or cut holes. More complex shapes can be a limitation for sheet metal punching and may necessitate other sheet metal fabrication techniques, like laser cutting, to obtain desired results.
Potential for Material Distortion: Sheet metal punching has the potential to distort workpieces, especially when dealing with thin or delicate sheets. The force applied during the punching process may cause unintended deformations which affects the tolerance and precision of punched parts.
Less Flexibility: Sheet metal punching is noticeably less flexible than sheet metal stamping. This is because sheet metal punching is limited to cutting or perforating sheet metal workpieces while sheet metal stamping can both cut and form sheet metal workpieces through bending, embossing, and more.
What Is Sheet Metal Stamping?
Sheet metal stamping is a versatile manufacturing process that involves forming flat sheets of metal into desired shapes using a die and a press. Like imprinting a stamp onto paper, sheet metal stamping incorporates other sheet metal forming processes such as: bending, blanking, punching, and more into a single process. Therefore, sheet metal stamping is often used for the production of complex sheet metal parts and for producing large quantities of parts with consistent shapes and dimensions.
What Does Sheet Metal Stamping Look Like?
During sheet metal stamping, a flat metal sheet is fed into the stamping press, in which a die lowers and forms the metal into the desired shape. Figure 1 below shows the toolset in a sheet metal stamping press:
Sheet metal stamping set.
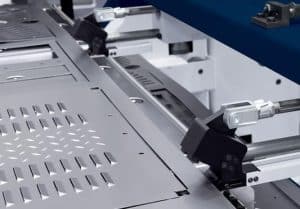
How Does Sheet Metal Stamping Work?
Sheet metal stamping works by a die and press that exerts force onto a metal sheet to form it into the shape of the die as a final product. The die may bend, coin, emboss, or blank the sheet metal workpiece in a single process. Sheet metal stamping can be used to make a single large part or multiple smaller parts in a single process. The stamped part is then ejected, and the cycle repeats for mass production.
Why Use Sheet Metal Stamping?
Sheet metal stamping is a widely employed manufacturing process due to its ability to repeatedly and efficiently produce complex sheet metal parts. Additionally, sheet metal stamping’s versatility to produce different features in a single process makes the process valued for use in high-volume production. Different industries such as: automotive, aerospace, electronics, construction, and machinery use sheet metal stamping to produce parts.
What Are the Different Applications of Sheet Metal Stamping?
There are numerous applications of sheet metal stamping in various industries, including: automotive, aerospace, and electronics. Common stamped components include: mounting brackets for automotive or aerospace components, electronic housing panels, and intricate metal parts for machinery.
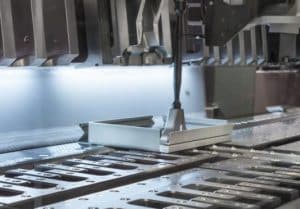
What Machine Is Used for Sheet Metal Stamping?
A stamping press, equipped with a die and (often) automated feeding systems, is the primary machine used for sheet metal stamping.
What Are the Advantages of Sheet Metal Stamping?
Sheet metal stamping has many advantages that make it suitable for a variety of applications in different industries. The advantages of sheet metal stamping are listed below:
High Precision: Stamping excels in producing intricate and precisely shaped components. Dies used in stamping are precisely designed tools to satisfy tight tolerances. The sheet metal parts produced by these dies reflect those same tolerances.
Efficient for Large Volumes: Stamping is cost-effective for large production runs due to its ability to produce complex sheet metal parts quickly.
High Material-Utilization Efficiency: Sheet metal stamping has high material-utilization efficiency since the design of the die ensures parts are formed with minimal scrap generated. This helps manufacturers maximize the number of parts they can create with a single piece of sheet metal stock.
Complex Shapes: Stamping is ideal for sheet metal parts that have complex or detailed shapes. Stamping dies can carry out sheet metal fabrication techniques like: punching, bending, and embossing all in a single process.
Consistency: Stamping ensures consistency in shape and dimensions across mass-produced parts.
What Are the Disadvantages of Sheet Metal Stamping?
Sheet metal stamping is not without its drawbacks. The disadvantages of sheet metal stamping are listed below:
High Initial Tooling Costs: The setup costs for stamping, particularly die design and creation, can be relatively high compared to sheet metal punching.
Less Economical for Small Runs: Stamping may not be cost-effective for small production quantities due to the costs associated with die engineering and fabrication. This is because up-front costs for small runs are distributed over fewer units, making each unit more expensive.
Setup Time: Complex die designs may increase setup time to ensure parts are made correctly. This may impact manufacturing efficiency and is undesirable for projects that require quick turnaround time.
What Factors Determine Whether Sheet Metal Punching or Stamping Is Better for a Manufacturing Project?
Several factors come into play when determining whether sheet metal punching or stamping is better suited for a manufacturing project. The project and product requirements must be considered. Factors like the complexity of the part’s features and the required tolerances must be vetted. Additionally, production volumes should be considered. Careful consideration of these factors will help determine whether sheet metal punching vs. sheet metal stamping is the better manufacturing process for the project.
To learn more, see our full guide on Stamping Services.
How Do Sheet Metal Stamping and Sheet Metal Punching Differ in Applications?
Sheet metal stamping and sheet metal punching differ in their applications due to their distinct capabilities and characteristics. Sheet metal stamping is capable of achieving both sheet metal forming and sheet metal punching in a single process. Bending, embossing, blanking, punching, and more can be achieved with sheet metal stamping, while only punching or blanking can be achieved with sheet metal punching. Despite these differences, both sheet metal fabrication techniques are commonly used in: the automotive, aerospace, electronics, construction, and medical industries.
How Does Sheet Metal Punching Compare to Stamping in Cost and Efficiency?
Punching is generally more cost-effective for simpler designs and smaller production runs but is capable of large production volumes. On the other hand, stamping is the better process when it comes to large volumes of complex parts.
What Situations Favor Sheet Metal Punching Over Sheet Metal Stamping and Vice Versa?
Sheet metal punching is preferable for projects with simple shapes, small quantities, and tight budgets. Sheet metal stamping is the choice for high-volume production requiring complex shapes and precise details.
XTJ is a leading OEM Manufacturer that is dedicated to providing one-stop manufacturing solutions  from prototype to production. We are proud to be an ISO 9001 certified system quality management company and we are determined to create value in every customer relationship. We do that through collaboration, innovation, process improvements, and exceptional workmanship.